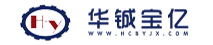
变压器油溶解气分析是大型充油电力设备健康监测的重要手段,通过对变压器绝缘油中的特征故障气体进行定量分析,可以及时掌握变压器的运行状态,进而进行必要的维护,鉴于目前并没有一种方法可以直接对溶解在油中的气体进行检测,因此把溶解在变压器油中的故障气体高效地分离出来是实现变压器实时在线监测的关键环节。
早期应用的油水分离方法主要有多普勒脱气法和部分脱气法,它们基本能实现完全脱气,但是需要活塞做真空处理,操作繁琐,不适于在线监测使用,近年来研究比较广泛的是高分子膜溶解-渗透油气分离方法,这种方法结构简单、性能稳定,目前使用较多的高分子膜有聚全氟乙丙烯膜(FEP)、聚四氟乙烯毛细管膜(GP100)、中空纤维复合膜以及带微孔的聚四氟乙烯膜等,但是这些有机高分子膜也普遍存在气体渗透率低、在线监测响应时间长的问题,油气平衡时间往往长达十几个小时甚至是数天,不能很好地满足在线监测的要求。
相比于有机高分子膜,无机膜具有耐高温、耐微生物、化学稳定性好、机械强度高、易清洗再生和孔径分布集中等优点,已在食品、药物等液体分离领域得到应用,其中比较有代表性的就是陶瓷膜。而且随着陶瓷膜制备工艺的改善,其过滤孔径可以达到30nm以下,成为有机高分子膜的有力竞争对手,国内外也已出现了将其与有机高分子膜结合应用于变压器油气分离领域的相关研究,但是未见单独用陶瓷膜进行油气分离的研究工作,本文提出单独采用陶瓷膜进行油气分离的设想,设计基于陶瓷膜的油气分离膜组件,测试该组件对于变压器典型故障气体C2H2的脱气性能,并与传统有机膜进行比较。
1 膜分离机制
传统的有机膜油气分离机制可以用溶解扩散模型进行描述,膜的一侧直接与变压器油接触,另一侧是一个隔离出的小型气室,两侧的气体分子因热运动而逐渐趋于平衡。平衡后气相中气体的体积分数与油中溶解气体的体积分数存在一定的换算关系,因此,通过测定气室中气体的体积分数便可以计算得到油中溶解气体的浓度。
这种结构相对简单,在线监测上只要将膜固定好,在长期运行中很容易达到稳定可靠的性能,比其他油气分离方法简单,但是传统有机膜普遍存在一个致命的缺点——平衡时间比较长。
区别于传统的有机膜,本文采用的微孔陶瓷膜是一种“错流过滤”形式的流体分离过程:变压器油在膜管内高速流动,膜管外是隔离出的小型气室,陶瓷膜为多通道管状结构,管壁密布微孔。
陶瓷膜的油气分离过程主要是依靠气体分子的热运动而使得油液内外气体浓度逐渐趋于平衡,不同的是变压器油在膜管内流动过程中会产生内压,在压力的驱动下沿垂直方向向外渗透,渗透过程中油液压力逐渐减小,导致溶解于其中的故障气体溶解度降低,从而使得气体分子更容易逸出,缩短平衡所需时间,此外,这种形式的过滤相比于传统有机膜的终端过滤形式,大大增加了过滤的面积,也使之更容易达到较短的平衡时间,结果是含大分子组分的变压器油液被膜分离层截留,而小分子气体通过陶瓷膜管壁分离出去,从而达到油气分离的目的。
2 油气分离实验
2.1 陶瓷膜油气分离膜组件
陶瓷膜油气分离膜组件包括陶瓷膜管、金属外壳以及油、器导管接头几部分,陶瓷膜油气分离膜组件外壳为管式结构,材质为304不锈钢,两端采用法兰盘进行连接,法兰盘上接有Swagelok6.0接口作为油的进出通路,陶瓷膜组件外壳壁开设2个气体循环通路。
外壳内装有过滤孔径50nm的内压式陶瓷膜管,陶瓷膜管与外壳之间形成小型气室,变压器绝缘油通过2个油路接口在陶瓷膜管内循环流动,溶解在绝缘油中的故障气体沿陶瓷膜管外壁分离出去,再通过2个气路接口与气体检测单元连接,该组件中,油路和气路之间的隔离密封采用的是硅胶圈。
2.2 实验平台
实验平台在油箱内采用高压击穿放电的形式模拟产生变压器油中溶解的微量故障特征气体(主要是C2H2),放电电压约为15kV,放电电流在1.5mA左右,测试中陶瓷膜组件直接与油箱连接,油箱内装有约2L标准变压器绝缘油,放电一定时间后,在蠕动泵驱动下,变压器绝缘油在陶瓷膜脱气组件中循环。
分离出的气体在气泵循环下进入光声池内进行定量检测,采用近红外光声光谱气体检测仪进行气体检测,该系统为基于可调谐掺铒光纤环形激光器(TEDFL)和掺铒光纤放大器(EDFA)的高灵敏度光声光谱气体检测仪,所测得的C2H2气体的浓度值和光声信号的峰值信号呈线性关系,因此,实验中直接以测得光声信号峰值的幅度表示C2H2气体的浓度。
3 实验结果及分析
3.1 脱气性能测试
在实验室室温条件下,测试陶瓷膜油气分离膜组件对变压器典型故障特征气体C2H2的脱气性能。测量前首先用N2对所有的气路进行持续20min的清洗,以排除干扰。
在2L变压器绝缘油中放电大约1min后开启蠕动泵,驱动变压器绝缘油在陶瓷膜管中不断循环,期间每30min测量一次光声池信号峰值的大小,即C2H2气体浓度的大小,测得C2H2气体光声信号峰值大小随绝缘油循环时间的关系,即气相C2H2浓度和绝缘油在陶瓷膜油气分离组件内循环时间的关系。
测试结果显示:C2H2气体浓度在6h左右趋于平衡,这一结果远远优于传统有机物高分子膜十几个小时乃至数天的平衡时间。
3.2 油中溶解C2H2气体含量与放电时间关系的测试
实验测试油中溶解C2H2气体的含量与放电时间的关系,实验条件与脱气性能测试中条件保持一致(实验室室温,2L绝缘油,每轮实验前用N2对所有气路进行20min的清洗),通过改变绝缘油中高压放电的时间,测得放电时间1~4min的光声信号的变化。由脱气性能测试所得结果可知,放电后,溶解有微量C2H2气体的变压器绝缘油在脱气装置内循环6h即可实现C2H2气体脱气平衡,因此,该节测量点就定在放电后脱气6h时,以保证气体含量测定的可靠性。
理论上,放电时间不长的情况下,在绝缘油中放电后,溶解于油中的故障气体含量与放电时间成正比。经过该组件进行油气分离而测得油中溶解的C2H2气体含量随放电时间的增加而增加,两者几乎成线性关系,这一结果与实验预期吻合得很好,从而说明该陶瓷膜组件对于变压器油中溶解气体C2H2的分离具有很好的重复性,进而证实该陶瓷膜组件进行油气分离的可靠性。
3.3 问题与讨论
在该次对陶瓷膜油气分离方法的研究中,也发现陶瓷膜油气分离存在陶瓷膜对油分子的截留率不高的问题,在长时间使用过程中会有少量的油透过陶瓷膜外壁渗透出来,虽然不至于影响实验的进行,但是考虑到将来真正应用于变压器在线监测油气分离时的稳定性和后期维护量,这也是必须解决的问题。
对此,本文考虑换用过滤孔径更小的陶瓷膜进行实验,同时也考虑通过改善陶瓷膜组件的结构,增加一个回流装置来解决长期使用过程中渗油的影响。
4 结论
陶瓷膜应用于变压器绝缘油故障气体的油气分离,可以在6h内实现C2H2的脱气平衡,远远快于传统的有机高分子膜,可以满足在线监测的要求,因此,陶瓷膜油气分离膜组件用于变压器油气分离可以提高变压器在线监测的可靠性和实时性。而且,陶瓷膜相比于传统的有机高分子膜还具有化学稳定性好、机械强度高、使用寿命长等优点,再加上如今陶瓷膜技术发展十分迅速,而且过滤效果稳定,是变压器油气分离膜领域一个很好的选择。