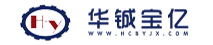
1 卧式螺旋沉降离心机介绍
1.1 卧式螺旋沉降离心机的工作原理
煤焦油混合物经进料管进入转鼓。在主机高速旋转产生的离心力作用下,比重较大的固相颗粒沉积在转鼓内壁上,与转鼓作相对运动的螺旋叶片连续将沉积在转鼓内壁上的固相颗粒刮下并推出排渣口,分离后的清液经堰板开口流出转鼓。螺旋与转鼓之间的相对运动由差速器来实现。差速器的外壳与转鼓联接,输出轴与螺旋联接,输入轴与副电机联接。主电机带动转鼓旋转的同时,也带动了差速器外壳的旋转,由于输入轴与副电机相联,副电机产生制动力矩,从而驱动行星轮按所设计的传动关系运转,并按一定的比例关系将扭矩传递给螺旋,实现了卧式螺旋沉降离心机对物料的连续分离。
1.2 分离原理
利用混合液中具有不同密度且互不相溶的轻、重液相和固相,在离心力场或重力场中获得不同的沉降速度的原理,达到分离分层或使液体中固体颗粒沉降的目的。
混合液在重力场或离心力场中,具有不同密度且互不相溶的轻、重液相和固相,分别获得不同的沉降速度,从而分离分层。在重力场中称为重力分离,在离心力场中称为离心分离。
由于混合液的密度不同,容器中的混合液经过一段时间后逐渐分为3层,混合液的重相颗粒下沉到容器底部,而且轻相则浮于上表面,重液相在轻液相和固相中间。分离的速度受到组成混合液的轻重相密度差的影响,密度差越大,分离的速度就越快。
当装有混合液的容器围绕自己的轴线作高速旋转时,由于组成混合液的两相密度不同,所以它们所受的离心力也不一样,混合液中的重相受到较大的离心力的作用,迅速沉降到转鼓的内壁,而轻相则较慢地贴附到重相表面,容器旋转的速度越快,组成混合液的轻重相所受的离心力差越大,分离的速度也就越快,当容器中设置有进料、推料、出液等装置后,此容器也就成了离心机,它与重力分离相比具有高效、快速、连续等优点。
卧螺机由电动机驱动。电动机轴带有一驱动皮带轮,运动的力通过V形皮带带动转鼓皮带轮,从而驱动转鼓。
背驱动的目的是使差速器的中心齿轮轴速度得到控制并且得以调整转鼓和输送器之间的差速。背驱动有2种形式,一是辅电机轴通过联轴器带动差速器,从而控制差速;二是电动机通过V形皮带带动差速器皮带轮,从而控制差速。
1.3 工作参数的选择
可根据悬浮液的物料性能,分离后液相与固相的要求,以及处理能力等因素,合理选择离心机的有关参数,如处理量Q、转鼓转速n、转鼓与螺旋的差转速△n、溢流板直径D等,以获得较满意的分离效果。
1.3.1 转鼓转速
随着转鼓转速的上升,分离因数上升,分离效果提高(在差速带轮确定后),螺旋与转鼓之间的差转速随之增大,处理能力加大,但离心机的振动、噪声也随之增加,使用寿命会有所下降,一般在能满足分离要求的前提下,选用合适的转速十分重要,因此本机转鼓的转速为3200r/min,工作转速建议选用在2000~3000r/min的范围内。
1.3.2 进料流量(处理量)
进料流量小,料液在转鼓内的轴向流速也小,物料在机器内停留时间则长,分离效果提高;进料流量增大,轴向流速也增大,物料在机器内停留的时间减少,分离效果随之下降。此外,进料流量还受到螺旋排渣能力的限制。当物料含固量较高,进料量过大,会造成分离后的沉渣因不能及时排出而引起转鼓堵料,影响分离,极端状态甚至不能分离,造成机器堵料的故障。因此在使用本机器时,应按物料的固相含量和分离要求选择适当的进料流量(即处理量Q),一般可在各种流量下进行分离效果比较后,确定较佳的进料流量,在△n=10r/min下的固相排渣量需小于1m³/h。
1.3.3 溢流板直径
转鼓大端溢流板直径的调节,能改变转鼓沉降区和干燥区的有效长度,溢流板直径小,则沉降区增大,干燥区减少,转鼓的液池深度增加,分离后液相中含固量可降低,但固相沉渣的含湿量增加,反之溢流板直径增大,沉降区长度减少,干燥区长度增加,分离后液相中含固量将增加,分离效果变差,而固相沉渣含湿量会减少。
1.3.4 转鼓与螺旋的差转速
差转速小,螺旋对流体扰动小,分离效果变好,固相沉渣在干燥区的停留时间长,固相含湿量减少,但固相排渣能力下降,易产生堵料;反之差转速大,螺旋对流体的扰动加大,分离效果变差,固相沉降在转鼓中的停留时间减少,固相沉渣的含湿量会增大,但固相排渣能力增加。差转速的确定一般是根据物料含固量大小来定,含固量较大应选用较大的差速,含固量较少则可选用较小的差转速,初始差转速的确定是根据试验,由分离要求、处理能力等因素来确定。初始差转速的调整可在运行状态下,通过调节液压变频器频率来实现,初始差转速的使用范围一般在5~15r/min内。
1.3.5 悬浮液的特性
物料中固相粒子越大,则越易分离;固相颗粒大小不一,则能被分离极限粒子决定了分离效果,部分小于极限粒子的小颗粒,将会随分离清液夹带出去。液固两相的重度差愈大,则分离越容易,悬浮液的粘度越小,则越易分离,反之则难分离。为此可适当提高物料进料温度或通过絮凝方法,加快自由沉降速度的预先处理,以降低粘度来改善分离条件。
2 炼铁厂煤化工序焦油系统使用卧式螺旋沉降离心机
2.1 基本参数
转鼓直径(mm) | 转鼓工作长度(mm) | 外形尺寸(mm) | 差速器类型 | 重量(kg) |
500 | 2120 | 4190*1300*1450 | 摆线差速器 | 5500 |
卧螺机主要技术规格参数:
转鼓直径Φ500mm;转鼓工作长度2120mm;转鼓转速3000r/min(转速);进料密度1800kg/m³;螺旋差转速5~30r/min(配双变频电控箱时,不配时按需要装机);分离因数2550;通水量25m³/h(处理量据物料不同而不同);螺旋推料器单头/左旋/超前;主电机Y200L-4B3,辅电机Y160M1-2B3。
转鼓与螺旋的差转速可通过下列公式改变差速器及副电机皮带轮大小来调节,其计算公式如下:
n=(nd×id-nx)/i
式中:n:转鼓螺旋差转速r/min;
id:主电机与转鼓皮带轮的比值;
nx:辅电机的转速;
nd:主电机的转速;
i=44。
2.2 设备的主要部件及材料的组成说明
主要部件有转鼓、螺旋推料器、机座、不锈钢外盖、减振器、电机、电气控制柜。
(1)机器的整体设计采用近几年国际上 机型的结构设计,电机旁置、外盖平放于机座的结构,使机器的维修更方便,噪音低、振动小、安装方便。
(2)不锈钢的外盖,采用密闭设计,机器在工作中的臭气不外泄,使机器的工作场所更符合环保要求。
(3)转鼓采用304不锈钢材质。
(4)机座采用方钢焊管,而非拼装焊接,使外观更美观,机座内部的焊接应力更低。
(5)机器减振装置采用鼓形高弹性模量的吸振阻尼装置,使机器的振动更小,对基础的振动冲击较以往的机型大为降低。
(6)电气控制装置。电气控制采用双变频控制系统,变频器采用台达品牌产品,其它主要的元器件采用合资、独资或国内 产品。
(7)控制柜的制造标准。所有用于低压交流系统的控制柜和开关设备按照IEC439中有关电力系统保护回路安装的技术要求进行安装和试验,380V电源直接供给电柜,进线方式为电缆下进线,控制柜的防腐处理为热镀锌后喷塑。
2.3 卧式螺旋沉降离心机的主要优点
(1)适应性好。在设计上充分考虑焦油分离处理工艺对卧式螺旋沉降离心机提出的各种特殊要求,对主要功能部件实行专用性、可调性等优化设计。
(2)生产能力强。连续24h工作、处理能力大、分离效果好。
(3)人工成本低。完全自动化操作,运行可靠,无需人工干预。每班仅需1人即可,对工人操作技术要求低,降低人工成本。
(4)使用寿命长。正常操作条件下,卧式螺旋沉降离心机的无故障运行不小于8000h;且使用寿命不低于8年。
(5)结构紧凑。占地面积小,易于操作,维护方便且维护费用低。
(6)安全保护装置齐全可靠。设有扭矩保护、功率控制、电器联锁、声光报警等多重保护,能有效排除或减少突发故障对机器造成的损害。
(7)自动化程度高。进料、分离、卸料等工序在全速运转下连续自动进行。设备控制可与微机进行通讯,实现工艺自动化控制。
(8)操作环境好。对悬浮液的分离是在完全封闭的条件下进行,对操作现场无任何污染,能保持生产环境的整洁卫生。
(9)耐腐蚀和锈蚀性能强。转鼓、螺旋、机壳等与物料接触的部件均采用优质不锈钢制造,具备了充分的耐腐蚀和锈蚀能力。
(10)能耗低。该机型采用 的变频调速技术,对供电网络冲击小,能耗为同类产品的1/3~1/2。
(11)运转平稳。实施了旋转零件精密动平衡和整机工作转速加载动平衡,卧式螺旋沉降离心机振动烈度按公司标准为5mm/s以下,远远低于JB/T 502-2004《卧式螺旋沉降离心机》规定的7.1mm/s。
(12)噪音低。噪声声压级低于85dB(A),低于JB/T 502-2004《卧式螺旋沉降离心机》规定的90dB(A)。
2.4 故障及处理
因卧螺机是高速旋转设备,故在日常维护中发现有异常情况,应立即采取应急措施(停机检查),采取相应对策:
电流不稳或偏大 | 差速器注入的油不好 差速器齿轮轴承或主轴承损坏 转鼓被遗留在机壳上的沉渣粘结 其它与转鼓相连的旋转件有问题 | 检查油的质量 修理或更换,同与我厂联系 清理机盖上的沉渣 立即停机用手盘动转鼓,查明出问题的零件,修理或更换 |
主转速低 启动时间太长 | 电机有故障 转鼓被遗留在机壳上的沉渣粘结 其它与转鼓相连的旋转件有问题 | 更换或修理电机 清理机盖中的沉渣 立即停机用手盘动转鼓,查明出问题的零件,修理或更换 |
主转速太低 | 传动比不当 输入电压太低 轴承损坏 电机连线有误 | 立即停机更换皮带轮,使速比正确 检查输入电压 更换轴承 检查接线线路 |
主转速较高 | 传动比不当 电机速度选择有误 输入电压偏高 电机励磁绕组有问题 | 立即停机更换皮带轮,使速比正确 检查接线线路,改变接线 更换或修理 检查输入电压 |
液相不清 | 处理量太大 溢流半径太大 差转速太大 分离温度不适宜 | 减小进料量 更换液位调节片使溢流半径增大 增大差速器输入轴的速度(增大辅电机变频器的输出频率)得到适宜的差转速 使分离液处于适宜的温度 |
固相不出料或太干 | 转鼓内物料层没形成 转速太高 溢流半径太大,选择的调节板不对 差转速太小 | 正常现象,进料一段时间后,转鼓内物料层形成后会出料 调整主电机变频率、降低转鼓转速 更换液位调节片使溢流半径减小 减小差速器输入轴的速度(减小变频器的输出频率)得到适宜的差转速 |
辅电机电流大,差速器保护装置脱开 | 转鼓中固相沉渣太多 前次运行后未清理干净 进料浓度变高 处理量太大 不规则进料 固相沉渣物理性质不好 | 增大差转速 停机,把转鼓中的沉渣清理干净 增大差速器输入轴的速度(增大变频器的输出频率)得到适宜的差转速 减小处理量 使进料均匀 进料前料液先经过滤 |
机器振动增大 | 机器升到一定阶段或降到一定阶段有适度的振动 旋转部分不平衡,污料未清理干净,装配不当,其它的装配件互换 螺旋推料器损坏 减振失去作用 地基太薄弱 轴承损坏 | 正常现象 立即停机查明原因,将旋转部分清洗干净;恢复原来的装配情况,如还不行,送厂家修理 修复螺旋推料器 更换减振器(一般两年更换一次) 重建符合要求的地基 查明和更换损坏的轴承 |