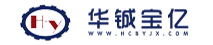
在众多的干燥器中,转筒干燥机是一类广泛应用于冶金、建材、化工等领域的大型回转干燥设备。转筒干燥机主要结构是一个可旋转筒体,湿物料被加入其中,筒体受高温将物料干燥,并向一端输送。转筒干燥机对物料的适应性较强,可用于干燥各种散状农产品物料。除此之外,转筒干燥机还有设备机械化程度高、生产能力较大、运行费用较低、操作稳定方便等优点。
但由于转筒干燥机存在热效率低(除蒸汽管式转筒干燥机外)、热容量系数小、安装困难等缺点,导致干燥系统不能以 状态操作,因此对转筒干燥机还有很大优化空间:提高干燥效率、减少能源浪费。因此,本文以高效节能为目标,论述国内外研究现状并进行分析。
1 转筒效率
选择干燥装置应以总成本低为目标。成本主要包括设备费和操作费,片面追求干燥的高热效率以节省操作费而使设备费大增,或单纯强调操作强化以减少设备费而增加能耗的做法都不可取。因此,要兼顾这两个因素,实现高效、节能的目标。高效就是用较小干燥容器实现较大蒸发水分,即干燥强度大;节能,就是以较小能耗获得较大蒸发水量,即热效率高。
1.1 效率指标的介绍
干燥强度用于衡量转筒干燥机生产能力,指单位时间和容积水分蒸发的能力,即单位时间内1m³加热容积可蒸发的水量。转筒干燥机的干燥强度为10~50kg/(m³·h),随热风温度的提高而提高,还随物料的水分、性质而变化,受转筒干燥机的进料口、进风口大小和出料系统密封程度的影响。
热效率用于评价转筒干燥机的热利用率,是指水分蒸发所需要的热量与热源提供给干燥机的热量之比,热源提供给干燥机的热量主要包括水分蒸发需要的热量、物料升温所需热量、热损失。转筒干燥机的热效率为30%~70%,随热风温度的提高,热效率也提高,并受进口、出口风的温度与系统密封情况的影响。
1.2 效率指标的计算
1.2.1 干燥强度
干燥强度DR定义如下式所示:
DR=水分蒸发量/(干燥时间×干燥器容积)
其中,水分蒸发量W=L(H1-H2)=G2(X1-X2)
以上各式中:
L:干空气用量,kg/h;
H1、H2:进入、排出转筒干燥机空气湿度,kg/kg绝干空气;
T1、T2:物料进入、排出转筒干燥机温度,℃;
W1、W2:进入、排出转筒干燥机的水量,kg/h;
G1、G2:进入、排出转筒干燥机的物料量,kg/h;
X1、X2:进入、排出转筒干燥机物料的含水量,kg/kg。
1.2.2 热效率
热效率η定义如下式所示:
Η=水分蒸发所需的热量Qw/热源提供的热量Q×100%
计算的总能量用耗电量来表示,以设备的总开关处安装电度表计,水分蒸发所需要的热量通过被干燥物料从入口状态加热到出口状态所吸收的热量计算,如下式:
Qw=W(2490+1.88T2)-4.187T1×W
2 转筒优化研究现状
目前国内外在转筒干燥机的研究与使用上大致相同。
物料和载热体的接触方式有两种,即物料与载热体直接接触加热,以对流传热方式进行干燥;载热体不直接与物料接触,间接加热,干燥所需的全部热量都是经过传热壁传给物料。
按照接触方式,可将转筒干燥机分为三种类型,即直接加热式、间接加热式、复合加热式。在此介绍就直接和间接加热方式的研究进行讨论。
2.1 直接加热式
2.1.1 传统形式
直接加热式主要包括常规式、叶片式穿流以及通气管式转筒干燥机。
常规转筒干燥机,被干燥的物料与热风直接接触,物料借助于圆筒的缓慢转动,在重力作用下从较高一段向较低一段移动,筒体内部装有抄板,不断将物料抄起又洒下,促使物料向前移动,按照热风与物料的流动方向,分为并流式和逆流式。
叶片式穿流转筒干燥机,按照热风的吹入方式分为端面吹入型、侧面吹入型。端面吹入型:筒体水平,沿筒体内壁圆周方向等距离装有侧倾斜的叶片,热风仅从下部有料层的部分叶片间隙吹入筒内。侧面吹入型:筒体略倾斜,热风从开有小孔的筒体外吹入筒内,方向与筒内物料的移动方向成直角,再穿过三角形叶片的百叶窗孔进入料层。
通气管式转筒干燥机,内没有抄板,物料始终处于转筒底部。中心管不随筒体转动,分支管沿着圆周集中在中心管下部均匀分布。热空气从端部进入中心管后,高速地从埋在料层内的分支管小孔中喷出,与物料强烈接触,强化传热传质过程。与叶片式相比,气体在干燥机长度上分布更均匀。
2.1.2 提高干燥强度的研究
目前针对转筒干燥机干燥强度提高的研究,主要包括多层滚筒干燥、并流干燥。
2.1.2.1 多层滚筒干燥
主要由两个以上直径不等的圆筒(通常设为3个)组成,按直径大小,将多个圆筒同轴套装在一起,并通过轴心连接成一个整体,内、中、外滚筒内壁均装有抄板。多层滚筒物料走向是:热风带着湿物料从内筒进入,从末端返回进入中层滚筒走到首端,再转入外层滚筒,由外筒末端排出。
与传统形式相比的优点:
因物料在圆筒内部的物料行程长,延长了物料与热风接触的时间,物料与热风的接触面积增大,强化了传热传质过程,干燥效果大大提高。
2.1.2.2 并流
在筒体圆周壁开设至少三个通孔,将通孔与接管连通,每个接管的自由端弯向转筒体较低端口,在该筒体外部至少有一个由密封装置组成的载热气体出入口与这些接管沟通。使热空气从圆筒的两端进入、中间排出,采用顺流逆流并用的方式,实现干燥流向分段变化。
解决了干燥流向单一的问题,物料表面蒸发的水汽扩散加快,热效率和干燥速率提高,克服了目前干燥设备或与物料并流或逆流所存在的干燥效率低的缺点,可广泛应用。
2.1.3 提高热效率的研究
主要包括充分利用热面空间:改进抄板形式、模型优化、穿流干燥、废气循环、破碎装置。
2.1.3.1 改进抄板形式
改进结构形式:如在抄板上设置凹槽、设计活动式抄板、采用带挠性件弧形抄板、抄板末端安装弯曲齿等等。
改进分布形式:沿转筒纵向将转筒分为几个区间,在每个区间内设置不同的形式的抄板,如大倾角式、倾斜式、带清扫装置圆弧型抄板等等。起到导料、撒料、破碎、清扫等作用,共同完成整个干燥过程。
改进抄板形式主要是延长物料的下落时间,搅动物料均匀干燥,充分利用热面空间,从而提高热量利用的程度,提高热效率。
2.1.3.2 模型优化
建立抄板模型,模拟抄板持料量,使得持料量增加,撒料也更均匀,增大物料与热风的接触面积,提高热效率。抄板模型可以适用于具有复杂截面的抄板结构,以及在不同安装角时抄板的持料与撒料量计算。
2.1.3.3 穿流干燥
使热风与物料成直角方向进行加热干燥。热风从开有许多小孔的筒体外吹入筒内,其方向与筒体内物料运动方向成直角,物料在每次升举下落中与垂直吹进的热风充分接触。
这种方法水分扩散距离短,有效地提高了热量利用程度,无大颗粒出现,产品收率高。
2.1.3.4 废气循环
将出口气体进行回收利用,与新鲜空气按一定比例混合吹入干燥器,适合的比例可以使能量传递小,研究循环对被干燥物料水分含量的影响。
这种形式利用了废热,减少电耗,热效率得到有效提高。
2.1.3.5 破碎
转筒内设置烘干格栅、破碎器、打散装置等破碎装置,将被抄板抄起的散状物料进一步破碎,增加干燥机内冷、热介质换热面积,使物料抛洒均匀,干燥更充分,节能效果好。
除此之外,还有其它方法如:在筒体与热气进管处连接密封圈减少热量损失、利用导料装置延长物料下落时间、设置分隔板以形成多个接触空间增大加热面积等改进方法。
2.2 间接加热式
2.2.1 传统间接加热式
间接加热转筒干燥机根据热载体的不同,分为常规式和蒸汽管式两种。
常规式的转筒砌在炉内,用烟道气加热外壳。在转筒内设置一个同心圆筒,烟道气进入外壳和炉壁之间的环状空间后,穿过连接管进入干燥筒内的中心管;烟道气的另一种走向是 入中心管,然后折返到外壳和炉壁的环状空间。物料在外壳和中心管的环状空间通过,这样物料有足够的停留时间。
蒸汽式的转筒内以同心圆方式排列1~3圈加热管,物料在筒内受到加热管的升举和搅拌作用而被干燥。它的单位容积干燥能力是常规直接加热式转筒干燥器的3倍左右。
2.2.2 提高干燥强度的研究
真空干燥:包括干燥滚筒、刮刀装置和供料器,并设置于密闭真空罩内。真空罩通过抽空管道连向真空泵,当干燥机工作时,真空泵将真空罩内的气压抽至一定的真空度,从而使物料在真空状态下进行干燥。
既具有常压转筒干燥机热效率高的优势,还具有干燥物料品质优的特点。
真空冷冻:通过转筒使物料随着转筒而转动,通过与干燥筒热内壁的不断接触而获得升华所需的热量,实现对物料的干燥;同时,由于滚动过程中物料被搅拌均匀,因此有利于物料吸热及吸热后的升华,物料干燥程度均匀一致,大大提高了干燥质量。
干燥速度快、干燥均匀并且干燥成本低廉。
真空脉动干燥:将物料放入转筒以设定温度进行加热抽真空。真空与常压交替进行,不断循环直至物料降至所需含水率为止。在干燥过程中真空泵一直处于工作状态,这样就能及时将物料蒸发出的水分带走。
与传统干燥方法相比大大缩短了干燥时间。
2.2.3 提高热效率的研究
主要包括改进管束换热、循环热风。
2.2.3.1 改进管束换热
在转筒中空腔内的若干根换热管,所述换热管通过转筒内壁相固接的至少两块横置的支承管板安装在转筒内腔中,再从该内腔进入与管板相连通的换热管内,通过管束的换热及转筒的旋转对管束外物料进行加热、翻转、搅拌,从而使物料达到均匀干燥的目的。
与传统形式相比,降低制造成本和加工难度,并有效解决了换热管旋转时受力不均现象,以及换热管与管板之间的泄露问题。减少旋转所需的功率,一定程度上提高了热效率。
2.2.3.2 循环热风
转筒内部轴线方向上设置直径大且贯穿整个筒体的中心火管,主要作用是通过循环热风的热能来烘干物料干燥区的物料。通过循环热风提供了足够的热能。
除此之外,其他改进方法如:版式加热、利用导热油炉的烟气预热转筒内的空气以减少能耗等改进方式。
纵观以上几种转筒干燥机,主要是改善物料在转筒横截面上的分布。而物料的运动分为截面上的运动和轴向的运动。针对物料的轴向运动研究,国内外建立了物料运动轨迹、物料停留时间数学模型,模拟分析转筒内传热过程,分析进料量、热风流量、抄板参数、转筒转速等参数的关系。通过模拟分析,得出物料温度和气体温度,含水率和湿含量沿转筒长度的变化关系。优化出较佳干燥工艺参数,用于指导生产实践。
3 结论与建议
3.1 提高干燥强度和热效率的方法
从干燥强度方面来看,单位时间内传送的热量愈大,干燥强度就愈大。影响干燥强度的因素有:热风温度、原料水分、引风机风量等。目前的方法集中于强化物料水分汽化的过程,加快汽化速度:如延长物料和热风接触行程、真空干燥、并流干燥等。
从热效率方面来看,在干燥蒸发水量恒定的情况下,提供的总热量越小,干燥系统的热利用率越高,节能效果越好。目前的方法主要集中于强化传热传质过程:延长物料的下落时间,搅动物料均匀干燥,增大换热面积以充分利用热面空间,利用废热。
从加热方式来看,目前以常规型直接加热式转筒干燥机为主要研究对象,没有针对叶片式和通气管式转筒干燥机的优化:针对间接加热式转筒干燥机,本身蒸汽管式干燥机的效率较高,而现有的研究也是以蒸汽管式为主,对于常规式几乎没有相关研究。两种加热方式相比,间接加热式干燥机优化的研究较少。
从效率指标来看,目前主要研究热效率的提高。
综合来看,常规式转筒干燥机热效率提高方法较多,而间接加热式的干燥强度研究比较缺乏。综合优化转筒的主要方法就是建立干燥过程的运动停留时间模型等来优化操作参数,达到整体提高干燥强度和热效率的目的。
3.2 建议
今后应多考虑间接加热干燥机的优化,尤其是多对提高干燥强度展开研究,多方面系统地提高干燥机结构的合理性和可靠性,达到更好的高效节能的效果。