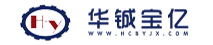
市政污水处理处置中,污泥减量化一直是关心的焦点。活性污泥法是应用非常广泛且比较成熟的工艺,而由此产生剩余活性污泥性质也决定了后期污泥处理工艺和设备的选择。参考欧洲较为普遍的浓缩加消化加脱水的工艺,处理流程中需要配备卧螺沉降离心浓缩机以结合消化工艺。本文针对卧螺离心机在团岛污水处理厂的实际应用,总结出部分经验,并提出需要改进的内容。
1 卧螺离心机的基本构造及主要参数
1.1 基本构造
卧螺离心机主要由转鼓(柱段加锥段),驱动电机,机架,螺旋推料器和齿轮箱器构成。通过主驱电机带动转鼓旋转,达到2000~4000rpm产生几千倍重力加速度的离心力,使污泥颗粒沉降;齿轮箱产生额外的差速,使同轴旋转的螺旋体与转鼓有0~30rpm的速度差,螺旋体与转鼓之间产生了相对位移,污泥被螺旋叶片输送至固相出口。上清液则沿着柱段通过另一侧的出水堰板溢流排出。
1.2 主要参数
(1)分离因数(G-force),分离因数等于离心力与重力加速度(g)的比值,是个无纲量。G-force=F离心力/F重力=m·w2r/(m·g),近似公式为0.011×r×n2/g。其中,0.011是(2π/60)2的近似值,n为离心机的转速,单位rpm,r为离心机转鼓半径。从分离因数可以得出结论,为了获得更高的分离因数,可以通过增大转鼓直径或提高转速来实现。对于同一规格即转鼓直径不变,提高转速也可以获得更高的分离因数,但对机械本身(轴承、密封圈、润滑等)损耗也就更厉害,额外产生的高分贝噪音也进一步影响现场的操作环境。
(2)转鼓,由圆柱及圆锥部分组成,柱段为澄清区,锥段为推料区,柱段与锥段夹角的补交称作锥角(半锥角)。根据经验,离心机做浓缩机使用时一般配备小锥角(6~10°)。转鼓直径大小与分离因数成正比,转鼓的容积大小同离心机处理能力也成正比。
(3)齿轮箱,也称为差速器。齿轮箱与推料螺旋连接,通过调节差速值的大小,达到调节扭矩,扭矩值可以相当于螺旋推料的作用力,差速越小,扭矩越高。齿轮箱有行星齿轮箱,摆线齿轮箱等,输出速比值决定了差速器的形式,目前能输出大速比的行星齿轮箱更为主流。
(4)驱动电机,以行星齿轮箱为例,驱动电机为主驱和背驱,均为变频电机。主驱电机驱动转鼓和螺旋体,产生高转速;背驱电机驱动齿轮箱,产生0~30rpm的差速。
(5)防磨损保护,包括进料区,推料区,排泥口都是物料与离心机接触的位置,同样也是磨损较为严重的部位,因此需要考虑防磨损保护措施,在进料区,排泥口增加可更换的碳化物衬套,在螺旋叶片上喷涂碳化物保护涂层或者硬质合金烧结块。
2 团岛污水处理厂离心浓缩机参数
根据团岛污水《青岛市团岛污水处理厂升级改造工程项目初步设计说明》:污水处理厂原初沉污泥采用重力浓缩、剩余污泥采用机械浓缩,两者混合后进行中温消化、机械脱水。
而项目采购了3套德国福乐伟公司的C5E-4/454 OSE卧螺离心浓缩机。转鼓直径0.57m,转速3100rpm,理论处理量90m³/h,装机容量75+5.5(kW),齿轮箱型号SP 3.10,输出扭矩2750N·m。
结合设备72h进料调试验收报告以及具体运行指标要求,将从多个方面来验证该项目的离心机的选型是否合理。
2.1 分离因数计算
离心浓缩机的分离因数计算如下:
G-forece=0.011×(0.57/2)×(3100)2/9.81=3070
通过试管离心机测试,在未投加絮凝剂(一般为阳离子的聚丙烯酰胺)情况下,剩余活性污泥能够离心分离的较小分离因数约1500。实际工况,离心机正常转速在2344rpm,此时分离因数为1756。另外,在投加絮凝剂情况下,污泥颗粒絮凝后粒径变大,更有利于沉降。因此离心机的分离因数满足工艺要求。
2.2 转速,差速
结合分离因数条件,转速达到2344rpm,较之转速3100rpm来评价,该转速工况下,离心机处于比较稳定状态,主机功率实际消耗低于装机容量的60%;现场离心机1m范围内测定的噪声值低于80dB。
根据浓缩段工艺要求,浓缩机出泥进入消化池的湿污泥干度仅需满足5%的要求,离心机可以轻松胜任,因此处理量成为相对重要的参数。差速值23.7rpm始终处于较高阈值(0~30rpm)内,差速越高,螺旋的推料速度越快,扭矩越小,污泥通过螺旋叶片输送,途径锥端再从固相出口排出离心机的时间缩短。相当于缩短污泥的停留时间,达到处理量大的效果,此时由于污泥停留时间短了,澄清时间也减少,因此会降低出泥的含固率,同时液相出口的上清液的回收率会提高。
2.3 理论处理量和实际处理量
卧螺离心机内部构造分为:推料区(锥段),进料部位及螺旋部位,以及澄清区。
其中澄清区就是所定义的离心机的有效容积,其有效容积计算如下:
V=(π·D2转鼓/4-π·d2堰板/4)×L柱段=(3.14×0.572/4-3.14×0.3122/4)×1.76=0.3145m³
一般物料在离心机停留时间为15~20s,因此理论处理量如下:
Q=V×3600/t=56.6~75.5(m³/h),与调试结果比较吻合,与理论处理能力存在一定差距。为了达到处理量90m³/h,可以从设备机械本身做以下调整:
(1)提高差速,加快浓缩后污泥的排出,减少了污泥的停留时间,从处理量公示中可以验证,分母变小,分数值变大。差速提升也是局限的,不能超过30rpm,一般程序上设置了高差速值的报警和停机功能。
(2)减少排液堰板直径。堰板直径变小,澄清区有效水深增加,有效容积值变大,处理量值变大。
(3)上述方法在提高处理量的同时,都是以牺牲出料干度为代价,对于污泥浓缩而言,这点完全是可以接受的。处理量介于79~83.3m³/h,出泥干度在6.4% ~7.0%之间,虽然能满足工艺5%的干度要求,但从严格意义上来说,当处理量需达到理论设计处理量90m³/h时,存在两个疑问:
①是否真的能够达到90m³/h,是否超出了机械当量设计的上限。
②如果达到理论处理量,需要确定一系列参数:
a. 进料的固体负荷具体数值。
b. 差速输出值。
c. 出泥干度值。
d. 主驱,背驱功率消耗值。
e. 离心机整机振动值,1m范围内噪声值等参数。
上述问题还需事实证明,从调试验收来看,处理能力约在84m³/h,能否达到90m³/h值,还有待事实证明,这也是该项目中剩余的一大遗憾。
2.4 絮凝剂消耗值(药耗)
配比浓度0.3%,投加量520dm³,此时处理量82.9m³/h,干粉投加量计算值=520×0.3%=1.56kg,每立方米消耗干粉量=1.56/82.9=18.8g,此时进料浓度1.3%,吨绝干污泥药耗=18.8/1.3%/1000=1.45kg-TDS。药耗量也满足1~2kg-TDS的工艺要求。
2.5 扭矩
该离心机配备了SP 3.10差速器,输出扭矩2750N·m,实际运行扭矩稳定在16%~16.7%,即实际输出扭矩440~460N·m,由于浓缩后污泥具有较好的流动性,干度要求仅需5%,所以该扭矩数值也很合理。离心机配备的差速器满足实际工况需求。
3 结论
(1)具有高分离因数的卧螺离心浓缩机完全适合浓缩段的工艺需求,也能更好地配合后续低温消化工艺。
(2)在性能指标上,出泥含固率达到5%,符合工艺段需求;处理量在80m³/h左右,基本满足要求,但处理量能否达到90m³/h,还有待论证。
(3)实际电耗仅为装机容量的60%,也起到了节能减排的作用。
(4)絮凝剂消耗低,满足工艺要求的同时,也为节约日后的药剂消耗量,实现了经济意义上的回报。
4 存在的问题及需要改进的问题
(1)团岛污水厂现场配备了三台离心浓缩机,对应三套进料泵,进料泵为潜水离心泵,非变频电机。进料流量通过电动刀闸阀PID调节阀体开启度以实现控制流量,在开启度过小的工况下,存在管道憋压的状态,长时间极有可能会损坏泵的电机。建议在进料泵出水管处设置1路DN50支管,各安装1套机械式减压阀,以实现在管道压力过高情况下自动排水减压的功能。
(2)对应三套离心浓缩机配备了三套管路,由于场地局限性,该三根管路管位非常紧张,当时的安装单位采用了泵出口三根DN150支管合并一根DN300总管的敷设方式,至浓缩机房前再分为三根DN150支管。这种方式不仅增大了水头损失,而且在浓缩机单台,双台,三台开启的不同工况下也存在配流不均的问题,建议直接采用三根支管的进料方式。