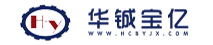
在离子膜法生产烧碱工艺中,其核心部件主要是全氟阳离子交换膜,其生产及技术全部掌握在日本旭化成与旭硝子、美国杜邦这三家公司手里。在国产化离子膜还未得到推广应用的这段时间,我国的离子膜法生产烧碱所用的离子膜全部依赖进口。所以离子膜在生产中使用寿命的长短,是衡量一个氯碱生产企业管理水平的标准。在整个离子膜生产工艺中,盐水中金属离子的含量高低,是影响离子膜电流效率的主要因素。现在离子膜生产烧碱工艺由强制循环逐步被高电流密度、自然循环取代,而大部分新建或扩建的氯碱企业采用的工艺,都是电流效率更为突出的离子膜膜极距生产工艺。对于盐水中的各种金属离子的要求也更为严格,而使用陶瓷膜处理一次盐水的优势也逐步体现出来。
1 陶瓷膜工艺介绍
来自界区外的淡盐水、回收盐水、工业水及滤液进入配水罐混合后,由化盐给料泵经汽水混合器加热升温后,送入化盐池化盐,饱和粗盐水自流进入反应池,在反应池内加入精制剂次氯酸钠、碳酸钠和氢氧化物。加药后粗盐水在反应池中,次氯酸钠分解粗盐水中的有机物,碳酸钠与粗盐水中的钙离子完全反应生成碳酸钙结晶沉淀。氢氧化钠与粗盐水中的镁离子反应生成氢氧化镁胶体沉淀。完成精制反应的粗盐水自流进入中间池,经陶瓷膜过滤供料泵送往粗盐水过滤器,滤除大于1.0mm的机械杂物后送往陶瓷膜过滤单元。
陶瓷膜过滤单元采用三级串联“错流”过滤方式,由粗盐水过滤器来的 粗盐水料液,经循环泵先送入陶瓷膜过滤器一级过滤组件过滤,一级组件出来的浓缩液进入二级过滤组件过滤;二级过滤组件出来的浓缩液进入三级过滤组件过滤。自陶瓷膜过滤器三级过滤组件浓缩液出口流出的浓缩盐水按比例和浓度排出一小部分进入原有系统的盐泥池。其余的回到盐水循环罐,与供料泵送来的粗盐水混合,用于调整进料液的固液比,进入过滤循环泵进口,实现控制浓缩液含固量和保证膜面流速的目的,然后经过滤循环泵回到陶瓷膜过滤器内循环过滤。各级过滤组件过滤出的精制过滤盐水通过陶瓷膜过滤器各级渗透清液出口排出。在混合器中加入亚硫酸钠消除过滤盐水中的游离氯后,进入系统中的精制盐水槽,经由一次盐水泵送螯合树脂塔二次精制。
陶瓷膜过滤器在长时间的运行后,因膜表面的污染可能会导致通量变化,过滤能力下降。需对膜表面进行再生,使膜通量得到恢复,过滤能力达到起始状态。再生的方式有物理反冲和化学清洗。物理反冲是采用过滤后的精制盐水在反冲罐由压缩空气加压后对膜表面进行反向冲洗;化学清洗是采用10%~15%的盐酸对膜进行化学清洗,使陶瓷膜面彻底清洁,完全恢复过滤通量。
根据以上工艺可以看出陶瓷膜的生产工艺流程短,控制点少,过程控制和操作简单,并在一次盐水的处理上实现了DCS自动控制,也是盐水精制的一大突破,大大降低了操作员工的劳动强度。对稳定盐水质量提供了保证。
由于陶瓷膜是一种无机膜,平均过滤孔径仅为40nm,并且孔径分布窄,保证了一次盐水中的SS总是在0.5mg/l以下。陶瓷膜的强度高,不受酸、碱、氧化剂等的影响,可在1MPa的工作压力下工作过滤。与有机膜不同,不会存在膜表面剥离、撕裂、腐蚀、孔径拉伸等现象。
2 应用情况
山东大地盐化集团氯碱厂在15万吨/年离子膜烧碱扩建中,生产采用离子膜膜极距工艺。盐水工序使用陶瓷膜技术处理一次盐水,首套陶瓷膜自2011年9月份投入使用至今,一次盐水的质量稳定,用滴定法监测一次盐水中的钙、镁等金属离子,均未检出。对于SS的检测,数据一般在0.12mg/l左右。整个陶瓷膜运行采用DCS自动控制;每台陶瓷膜的组件采用5-4-3排列,共计3台;一共装有膜管的筒体为36个;每个筒体装有37只膜管,每只膜管的过滤面积大约0.23㎡/只,陶瓷膜管总面积大约306.36㎡;每平方米陶瓷膜管能够处理合格的一次盐水不低于0.65m³;而3台陶瓷膜设备的占地面积仅为130㎡。
2012年11月扩建30万吨离子膜烧碱/年配套陶瓷膜工艺试运行,每台陶瓷膜的组件采用6-5-4排列,共计3台;一共装有膜管的筒体为45个;每个筒体装有61只膜管,每只膜管的过滤面积大约0.23㎡/只,陶瓷膜管总面积大约630㎡;可以过滤合格的一次盐水不低于410㎡;至今运行正常。
3 与凯膜或颇尔膜处理盐水技术的比较
3.1 节省占地面积
由于陶瓷膜技术的工艺流程大大缩短,设备相比较而言(没有预处理器这样的大型设备)也大幅度减少,从而使该技术项目的占地和建筑面积大大减少。特别是在一些扩产项目上,无需新增装置用地,利用现有盐水装置的闲置场地及厂房、建筑,就能够新增一倍以上的一次盐水能力。
3.2 节省资金投入
由于陶瓷膜工艺取消了粗盐水浮上桶预处理系统,整个盐水工序的投资可比其他膜法处理一次盐水系统减少投资大约35%左右。初步测算三十万吨离子膜烧碱装置节省投资可超过1000万元。
3.3 节省运行费用
该技术不同于有机聚合物膜(凯膜或颇尔膜过滤),由于有机聚合物膜(凯膜或颇尔膜过滤)抗氢氧化镁及有机物污染的性能差,需要对过滤盐水采用浮上澄清桶进行预处理。而陶瓷膜过滤技术减少了加压溶气、浮上澄清的工艺及设备,也不需要加入三氯化铁等腐蚀性化学药剂,从而减少了对设备和管道的腐蚀危害。30万吨离子膜烧碱/年的项目可降低运行费用大约150万元/年左右。
3.4 过滤盐水质量高
从投入运行的陶瓷膜工艺来看,单从SS的化验数据(0.12mg/l)就可以看出该工艺的优势,并且盐水的质量相当稳定;远远超过盐水进离子膜电解的要求,能有效地提高离子膜的电流效率、延长了离子膜的使用寿命。
3.5 工艺操作简单
由于陶瓷膜处理盐水的工艺流程短,操作简单,采用了DCS自动控制,更能稳定盐水质量及降低操作员工的劳动强度。
3.6 使用寿命长
高强度的无机陶瓷管式膜不受酸、碱、氧化剂等的影响,可在1MPa的工作压力下长期工作过滤,不存在有机聚合膜的膜表面剥离、撕裂、腐蚀、孔径拉伸等现象,高效且长寿,使用寿命可达5年以上。
4 结语
总体来说,陶瓷膜工艺处理的一次盐水适用于不断发展变化离子膜烧碱工艺,特别是近几年陆续投产的膜极距工艺。对于盐水中的钙、镁等金属离子要求更为严格。钙、镁离子主要影响离子膜的电流效率;在生产中一旦进入电解槽,就会与从阴极室反渗透至阳极室的氢氧根离子,生成氢氧化物沉淀在离子交换膜里面,不仅导致电槽槽压上升,电流效率下降,而且形成微孔导致离子膜的物理损伤、折裂,引起离子膜结构不可修复性的损伤。所以在提高盐水质量、延长离子膜的使用寿命、有效降低氯碱生产企业产品成本等方面,使用陶瓷膜处理一次盐水工艺占很大优势。