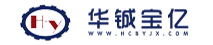
1 污泥干化设备工艺类型及工作原理
1.1 热对流干燥系统
早期的直接热干燥系统是将外部热介质(热空气、燃气或蒸汽等)加热后通入干燥器与污泥直接接触,蒸发污泥中的水分并运送污泥。热介质离开干燥器后与干污泥颗粒分离,经除尘、热氧化除臭后排放。由于系统所需热风量很大,故尾气处理成本较高。目前该工艺采用了气体循环回用的设计,使尾气处理成本高这一缺陷得到明显改善。在其干燥工艺中,热介质经除尘、冷凝、水洗后,只需对15%的热介质进行热氧化除臭并排放,其余的85%可直接返回干燥器。这不仅减小了尾气处理的负担,更重要的是大大降低了外部热介质的引入量,将干燥器内的氧气含量维持在较低水平,从而大幅提高了系统的安全性能。直接加热转鼓式干燥机是较常用的热对流干燥设备。热对流干燥系统具有如下优、缺点:
(1)热对流工艺对污泥进行全干化时传热传质效率较高,对污泥进行半干化时能耗较高,因此该干燥系统更适于全干化工艺。
(2)热对流干燥系统的强扰动和机械作用对污泥颗粒的坚硬外壳具有较强的破坏能力,可使内部的潮湿污泥外露,提高热传输效率及蒸发速率。
(3)后续冷凝洗涤废水量大,处理费用较高。
(4)系统的额外能耗增加。这是由于热对流干燥系统采用的是气体循环回用设计实际上是对循环载气进行反复的加热、冷凝和洗涤,致使热损失很大。
(5)该系统内部的气体流动量大,粉尘浓度高,因此安全性较低。
(6)整个系统庞大、复杂,给操作和管理带来一定的麻烦。
1.2 热传导干燥系统
热传导干燥系统不存在大量工艺载气的循环,系统仅抽取相当于蒸发量的部分进行冷凝,通常采用抽取微负压方式,也有部分工艺采用少量载气的方式,因此尾气处理的负担较轻,且载气热损失也较低。目前国内外常用的热传导干燥机主要有多层台阶式干燥机、转盘式干燥机等。
热传导干燥系统具有如下优、缺点:
(1)热传导工艺系统进行全干化时能耗高、效率低,更适于半干化工艺。
(2)无需载气或所需载气量较小,因此气体产量少,后续尾气处理费用较低。
(3)系统内部气体流动性小,因此粉尘浓度低,系统安全性较高。
(4)干燥器内部的运动部件较多,维修费用较高。
目前欧美等 常用的干化系统主要以直接干燥转鼓式工艺、多层台阶式干化工艺、转盘式干化工艺、流化床干化工艺等为主。此外还有碟片式、带式、日光式等干化工艺,但在大型工程中的应用很少。
1.3 干料返混工艺
为避免全干化过程中的污泥粘结、干燥效率低等问题,目前多采用干料返混工艺手段,该工艺具有如下特点:
(1)由于城市污泥干燥过程存在“胶粘相”阶段(含水率为60%左右),在此过渡段内污泥极易结块,具有表面坚硬、难以粉碎而里面却仍是稀泥的特点,这给污泥的进一步干燥和灭菌带来较大困难。而干料返混方式可以使污泥的含水率降至50%左右,使其直接越过“胶粘相”,大大减轻了污泥在干燥器内的粘结,从而提高了热传输效率及蒸发速率。
(2)干料返混工艺还可改善初始进料湿污泥含水率变化的敏感性。一般干燥系统在运行过程中,供热量及其相关的工艺气体量已经确定,当进料含水率变化而进料量不变时,系统内部的湿度平衡被破坏,从而引发如下问题:
①湿度增加可能导致干化不均。
②湿度减少则意味着粉尘量的增加和颗粒温度的上升,使系统安全性大大降低。
而采用干料返混工艺则能够扩大可允许的湿泥波动范围。干料返混实际上就是用5~10倍的绝干物质来混合初始污泥,例如用5倍含固率为90%的干泥颗粒混合湿泥,则当湿泥的含固率为10%~20%时,混合物你的含固率为50%~55%,可见干料返混可扩大湿泥波动范围,提高系统的安全性和稳定性。
(3)干料返混工艺的热损失能耗高。这是由于湿泥的含固率一般较低,致使返混比例较高,从而形成对大量干污泥载体的反复加热、冷却造成的。干料返混工艺的热损失由两个因素决定:
①返混的目标含固率。含固率越高则所需返混干泥的比例越高,形成热损失的物质总量越高。
②干燥器进口混合料和出口产品的温差。该值决定了单位质量物质的热损失幅度,由此可以计算干料返混工艺的热损失。
2 干燥工艺的技术要点
2.1 能耗
污泥干燥是一个能量净支出的过程,耗能费用在一个标准干化系统运行成本中的比例>80%,因此对热能损耗的研究是干化系统研究及改进的重点。
干化的热损失主要来自热源和干燥工艺两方面。不同类型热源的热利用效率不同,传输距离、保温状况均对热源的热利用效率产生较大影响,减少这部分热损失的原则是:优化热源,优化选择和组合换热器,缩短传输距离,强化保温效果。
不同的工艺类型对热损失的影响很大,含水率较高时热传导通过传热面发生固液传热,传热效率高于热对流的气液传热,干燥后期污泥进入“胶粘相”阶段,此时热对流的传热效率较高;全干化工艺干燥载气的反复冷凝、洗涤、加热过程具有较大的热损失;此外干料返混工艺的特点也决定了其热损失较大。减少这部分热损失的原则是:合理降低产品含固率,使之优化并适应污泥的处置要求;选择适合产品含固率的工艺类型;改善冷凝条件如减少载气量、分步冷凝等,减少工艺步骤、缩短工艺路线,优化运行参数以提高干燥效率。
2.2 安全性
老式干燥器存在起火或爆炸频繁的缺点,使污泥干燥设备的安全性能倍受质疑。对工艺安全性具有重要影响的要素包括:粉尘浓度,一般要求粉尘浓度<60g/m³;工艺允许的含氧量(燃烧气氛的惰性化),一般要求氧气含量<12%;颗粒温度(点燃能量);湿度(气体的湿度和物料的湿度对提高或降低粉尘爆炸下限具有重要影响)。
由于污泥的粉尘爆炸浓度下限值较低,当含氧量条件具备时,污泥颗粒的点燃温度较低。因此,降低污泥颗粒温度并不是排除粉尘爆炸的根本性条件。此外,提高干燥器内的湿度,易使水蒸气的平衡分压增大,导致湿污泥中水分的干燥速率降低,同样也不是提高干燥器安全性的主要手段。这表明保障系统的安全性应从降低粉尘浓度和降低含氧量两方面考虑,对干燥器内的粉尘浓度和含氧量进行实时监测,并采取针对性措施来完善设计和加强管理。
3 结语
(1)降低污泥含水率是解决目前污泥处理所面临困难的关键。污泥干化处理是污泥处理、处置重要的“ 步”,为后续的污泥处理处置及资源化提供了多种选择。
(2)目前国内外污泥干燥工艺主要分为热对流工艺和热传导工艺两种类型。热对流工艺更适合污泥的全干化,热传导则更适合污泥的半干化。与热传导相比,热对流具有对尾气、洗涤水等二次污染处理费用高、系统安全性低、循环载气导致的热损失大等缺点。但热传导干燥器内部较多的运动部件将导致系统的维修费用很高。
(3)干料返混工艺是目前许多干燥工艺常用的操作单元,可以避免干化过程污泥粘壁、干燥效率低等问题,同时可改善初始进料湿污泥含水率变化的敏感性,但干料返混单元导致的系统热损失能耗较大。
(4)污泥干燥是一个能量净支出的过程,干燥工艺的能量消耗高低是衡量一种干燥工艺优劣的关键因素,而整个干燥系统的安全性则是干燥工艺的首要控制条件。
(5)目前干燥工艺技术均引自化工行业的热干燥技术,而污泥与晶体物质的干燥特性有较大的差异,因此需对污泥的热干燥特性、污泥干燥过程的形态变化、干燥过程的有机物反应机理等加以深入研究,以期为适合污泥干燥的设备开发和研究提供必要的理论基础。