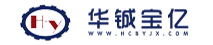
目前,涂装行业多采用湿式喷涂工艺,其靠循环水对漆雾进行捕集,处理后的漆渣含水率高,直接导致处理费用增加,在汽车行业内如何降低漆渣的含水率已成为涂装车间降低成本的一项重要课题。
1 漆渣产量及处理费用
目前,某公司各涂装车间采用湿式喷涂工艺,在喷漆过程中会产生大量漆渣,且主要存在以下两方面的问题。
(1)漆渣产量大:目前该公司涂装车间产生的漆渣总产量约为5.4t/d,漆渣产量大,且各车间产生的漆渣不能随时处理,需要集中存放,占用车间空间,另外放置的漆渣会产生异味,影响车间整体环境。
(2)处理费用高:目前该公司处理漆渣的费用大约为0.3万元/t,而漆渣中含有大量水分,漆渣处理费用相对偏高,全基团漆渣处理费用约为1.6万元/t。
2 漆渣处理方式
该公司目前存在3种漆渣处理形式。
(1)人工打捞漆渣并将漆渣放入编织袋进行沥水。此种方法存在的问题为:人工打捞漆渣作业效率低,并且需要将漆渣装入编织袋,浪费劳动力并且占用空间,漆渣搬运不方便,污染现场环境。
(2)刮渣机直接将漆渣刮入漆渣桶内进行处理。此种方法存在的问题为:刮渣机直接将漆渣刮入渣桶内,水分无法沥出,增加漆渣处理成本。
(3)刮渣机将漆渣刮入带有滤网的小车内。此种方法存在的问题为:刮渣机先将漆渣刮入带有滤网的小车内,再由人工操作转移至漆渣桶内,不能一步到位,存在作业浪费,且由于漆渣的特殊结构存在沥水不净的问题。
3 漆渣含水率测定
3.1 漆渣含水率测定方法
目前该公司没有明确的漆渣含水率测定方法,故参考污泥含水率测定方法进行漆渣含水率测量,将刚打捞出来的漆渣样品放入铝箔内(漆渣不宜选取太多,一般在20g左右,便于漆渣内部的水分蒸发),用天平测量漆渣总质量,之后减去铝箔质量,算出漆渣烘干前的总质量;随后将盛放有漆渣的铝箔放入烘干炉内,150℃烘干1.5h,再测量烘干后的漆渣质量并减去铝箔质量,得出漆渣含水率。
3.2 漆渣含水率现状
目前各车间盛放漆渣的方式不尽相同,部分采用编织袋、部分采用漆渣桶、部分采用漆渣小车,而公司内部并没有 的盛放标准及放置时间,对于处理前的漆渣的含水率也没有明确的要求,这就导致部分车间漆渣处理时含水率偏高,通过测量,含水率高达83%,这将会造成漆渣处理费用的严重浪费。
4 实施方案确定
4.1 项目调研
为了解决漆渣含水率高的问题,进行多方调研,了解漆渣烘干脱水设备、离心式脱水设备、真空负压脱水设备以及物理压榨式脱水设备等,确定采用叠螺式污泥脱水设备,利用物理压榨方式进行脱水,其具有结构简单、脱水率高、运行能耗低的优点。
4.2 设备原理
叠螺式挤水机的主体由多重固定环和游动环构成,螺旋轴贯穿其中形成过滤装置。前段为浓缩部,后段为脱水部,将污泥的脱水和压榨工作在一桶内完成,以独特的滤体模式取代了传统的滤布和离心过滤方式。此设备设计的动静环滤缝结构使得工作过程中不易发生堵塞,无需为防止滤缝堵塞而进行大量的清洗。设备可实现24h自动连续运行,无需专人进行看管,人工费用大幅降低。螺旋轴的转速在10r/min以内,无振动,低噪音。其叠片具有自清洁功能,不会发生堵塞,只需少量的水冲洗,无二次污染。再加上污泥在很慢的工作状态下运行,臭气不扩散,不影响整体环境。
4.3 项目实施
根据项目调研结果,采购了一台叠螺式漆渣脱水设备,并将其与循环水池进行集成,两套设备组合成一个整体,即现有的刮渣机直接将絮凝完成的漆渣刮入漆渣处理设备中进行压榨处理,处理完成的漆渣直接落入渣桶或回收小车中,设备的启停是由人工进行手动控制,根据项目需求,脱水设备也可以实现自动检测并开关机,整个处理过程无需人员参与。
4.4 问题暴露及改进
4.4.1 设备存在问题
目前该公司早期建设的涂装车间全部采用溶剂型涂料,生产过程中产生的漆渣特性与水性涂料存在差异,溶剂型涂料产生的漆渣比水性涂料产生的漆渣黏度大,而设备入料口较小,导致漆渣黏连在入料斗侧壁上无法自动入料,必须由人工辅助作业才能实现漆渣脱水功能。
4.4.2 问题改进
设备改善前漆渣入料口为方形小口,由于漆渣黏度大,无法实现漆渣自动入料。改善后将漆渣入料口长度增加3倍,增加了螺旋轴与漆渣的接触面积,提升了入料效率。设计研发漆渣自动入料搅拌辅助轮,辅助轮齿数需要根据螺旋轴螺旋间距确定,使其能够完全啮合,另外在搅拌轮中间部位增加了搅拌叶片,可以使漆渣搅拌效果得到明显提升,同时搅拌叶片在转动过程中不能与螺旋轴发生干涉。漆渣搅拌辅助轮需要安装在设备入料口处,另外在入料口的螺旋轴上部需要安装一块压板,防止漆渣被搅拌轮带走。
5 改进效果
漆渣搅拌辅助轮安装完成后可以对锥斗内部的漆渣进行搅动,同时配以入料压板,成功地实现了漆渣自动入料,漆渣搅拌辅助轮装配在一起后,可以利用主机螺旋轴的转动作为驱动管理,无需额外提供动力,此改善措施解决了叠螺式污泥脱水机自动入料的瓶颈问题,开创了漆渣脱水的新思路。
通过改善前后效果对比发现,传统技术仅仅是通过沥水的方法降低含水率,由于漆渣内部结构类似蜂窝状态,故此部分水分无法沥出,导致漆渣在经过沥水后仍含有大量水分;而通过叠螺式漆渣脱水机进行压榨脱水效果明显,可以脱出约30%的水分。以该公司某车间涂装漆渣压榨前后的含水率为例,通过测量确定含水率由59.78%降至29.69%,降低了30.09%,按脱水率30%计算,全集团可节省的漆渣处理费用约为1.6万元/d×30%×25d=12万元/月。
6 风险识别
由于叠螺式漆渣脱水机采用物理压榨方式进行脱水处理,且脱水主机的固定环和游动环之间存在一定间隙,在进行漆渣脱水时会有部分漆渣被挤出,这属于正常现象。对于正常絮凝的漆雾,其漆渣状态为絮状基团,在挤压过程中漆渣不易被挤出,但是未完全絮凝的漆渣类似粥状或膏状,在压榨脱水时会通过脱水主机环片的缝隙被挤出,造成漆渣无法脱水或脱水率低下,故在确定选用叠螺式漆渣脱水机之前需要先确定漆渣的絮凝状态。
7 经验分享
该公司在进行漆渣脱水项目改进过程中发生过多次设备故障,主要有以下几个方面:
(1)电机过载报警:现场在进行漆渣脱水过程中发生了多次电机高温停机现象,分析原因主要是因为清漆漆渣黏度大,导致电机超负荷运行,从而产生高温停机问题。问题解决对策为增加电机功率。
(2)减速机高温:脱水机运行过程中发现减速机异常高温,并在润滑油观察窗处发现油液中混有大量金属碎屑,经分析确定脱水主机运行阻力超标,无级变速器异常磨损发热。问题解决对策是将无级变速器改为定速减速机。
(3)主机设备卡死:该公司在进行双组分清漆漆渣脱水验证过程中发生了设备卡死停机故障,经过设备拆解分析,发现凝固的清漆块卡在了螺旋轴中间,而清漆块则是在进行喷漆室保洁时从轨道及格栅上清理下来的。问题解决对策是在漆渣脱水机入料口处增加粗滤网,过滤大块的凝固清漆块等杂物。另外对漆渣脱水机增加正反转功能,当设备异常卡死时可以通过反转来自动清理内部异物。
(4)喷淋头堵塞:设备在运行时需要对脱水主机定时进行喷水清洁,为了节省水资源,同时减少自来水安装管路,该公司从循环水泵出口引出管路连接至脱水设备进行喷水清洁,但在运行一段时间后发现喷嘴堵死,无法进行喷水作业,经拆解喷嘴发现是循环水中的漆渣堵住了喷嘴。问题解决对策是在设备喷水系统主管路之前增加过滤网,消除堵塞问题。
8 结语
采用叠螺式漆渣脱水机进行漆渣脱水具有设备结构简单、投资成本低、占地面积小、运行成本低、便于维护且脱水效果良好的优点,但叠螺机本身主要是用于污泥脱水处理,想要将其应用于漆渣脱水必须针对漆渣特性进行设备改进,改进后的设备可以取消絮凝部分,但必须保证循环水池的漆渣为正常絮凝的漆渣。另外需要确定单个循环水池的漆渣产量,以便匹配合适的设备型号。由于脱水设备需要根据不同的工厂进行特殊定制,故此项目的关键点在于充分与设备厂家沟通,做好前期技术方案探讨,以确保项目的顺利实施。