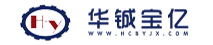
唐山首钢京唐西山焦化有限责任公司一期工程酚氰废水处理项目4×7.63m焦炉配套建设,处理煤气净化过程中产生的含酚氰废水及煤气管道冷凝水,由预处理、生化处理、后混凝沉淀过滤处理及污泥处理等工序组成,废水生物处理采用缺氧-好氧-好氧(A-O-O)的内循环工艺流程。目前,该公司按年产380万t焦炭进行生产组织,酚氰废水处理原水水量为130~140m³/h,无稀释水,其中蒸氨废水水量为100~110m³/h。
根据设计资料,酚氰废水处理作业区剩余污泥(平均排泥量15.4m³/h,含水率为99.2%,连续排泥)和凝聚沉淀池排出的污泥(排泥量45m³/h,含水率为99.2%,每天排泥8h),由污泥泵送入污泥浓缩装置进行处理,浓缩后的污泥由污泥泵送污泥脱水机进一步脱水。污泥浓缩池上清液流回污水处理系统进行处理,泥饼(22t/d,污泥含水率为80%)送煤场掺入焦煤中焚烧。因此,酚氰区域产生污泥量约为22÷(1-80%)=110m³/d。实际污泥量为90~100m³/d,化验剩余污泥实际含水率为99.1%。
1 设备使用现状
酚氰废水处理作业区污泥浓缩装置原采用带式压滤机,单台污水处理能力仅为4~5m³/h,每天24h连续运转。排泥含水率为84.5%,泥中带水较多导致泥稀,不能很好地形成泥饼,污泥在运输过程中洒落严重,设备运行环境较差。由于带式压滤机泥处理量较小,随设备的老化,频繁停用检修。检修时,生物处理系统中污泥不能及时排出,系统内污泥指数增高,随污泥基数逐步增大,污泥量迅速膨胀,形成恶性循环。2台带式压滤机24h超负荷运转,系统泥量仍持续上涨,造成生物处理系统污泥指数严重超标,影响出水指标。并且,备件更换频繁,检修强度和难度较大,导致维修成本较高。压滤机运行过程中需用清水随时冲洗滤带,每天耗用清水约180m³。压滤机驱动电机为1.5kW。
目前,焦化废水污泥脱水生产中采用的脱水设备类型主要分为3种,即板框压滤机、带式压滤机和离心机。这3种类型脱水设备的比较见下表:
比较项目 | 离心机 | 带式压滤机 | 板框压滤机 |
絮凝剂投加量 | 中 | 大 | 小 |
脱水后泥饼含水率 | 低 | 较高 | 高 |
自动化程度 | 连续操作,可无人自动控制 | 可连续操作,需人工管理 | 间隙程序操作,需人工管理 |
环境条件 | 好(密闭管道式) | 差(敞开式),二次污染大 | 差(敞开式),二次污染大 |
日常维护措施 | 更换轴承和皮带 | 更换托辊和滤带 | 更换滤布和框板 |
分离效果稳定性 | 好(参数设定后机器自动控制) | 差(受进泥及人为因素影响大) | 差(受人为因素影响大) |
消耗功率 | 大 | 小 | 小 |
由上表可知,离心机具有自动化程度高、运行环境条件好、分离效果人为因素影响小、操作维护方便、日常运行费用小等诸多优点。结合其他单位使用情况,该厂决定将带式压滤机改为卧式螺旋卸料沉降离心机,并配套自动配投药装置和控制系统。
2 离心机工作原理
卧式螺旋卸料沉降离心机(以下简称离心机)是依靠固液两相的密度差,在离心力场的作用下,加快固相颗粒的沉降速度来实现固液分离。
当污泥进入离心机转鼓腔后,高速旋转的转鼓产生强大的离心力,污泥颗粒由于密度大,离心力也大,因此污泥被甩贴在转鼓内壁上,形成固环层;而水的密度较小,离心力也小,只能在固环层内侧形成液环层。由于螺旋和转鼓的转速不同,二者存在相对运动(差速),把沉积在转鼓内壁的污泥推向转鼓锥体端出口处排出,分离出的水从转鼓的另一端排出。差速器的作用是使转鼓和螺旋之间形成一定的差速。污泥中投加絮凝剂,以产生絮凝作用,使分散的污泥颗粒聚集产生较大的絮凝体,加速泥水分离。
分离因数是衡量离心分离机性能的主要指标,离心机的转鼓转速和直径决定其分离因数。对于同一台设备而言,其转鼓直径是一定的,可以通过调节转鼓转速来调整分离因数。一般来讲,转鼓转速越高,分离因数越大,离心机排出的泥饼中的含水率也就越低。另外,离心机的差速也可以通过控制污泥在转鼓中的停留时间而直接影响排出到转鼓外的泥饼的含水率。
3 改造效果及经济效益
3.1 改造效果
离心机主电机和螺旋电机均采用变频控制,可实现对转鼓和螺旋转速的方便调节。同时,螺旋推料扭矩可以在规定范围内进行设定,因此可以实现在不同工况下对运行参数进行调节,以保证离心机处理效果和设备运行稳定。
离心机有差速控制和扭矩控制2种运行模式,由于主电机转速不变,在扭矩控制模式下,通过改变螺旋电机转速,进而改变差速来调节扭矩,使扭矩保持在设定值上下波动,以保证设备稳定运行。在手动运行过程中可以采用差速控制模式,一般只有在调试和冲洗时使用,正常自动运行过程中不使用。在扭矩控制模式下,当过扭矩时系统自动将进料打回流,以保证不发生过负荷运行而损坏设备。自动配投药装置可以根据来料含水率预先设定配药浓度,并根据处理量随时自动调节加药量。这样能够有效避免因加药量不足导致污泥不能完全絮凝,进而致使分离效果变差;同时,可以避免因过量加药而导致过渡絮凝,致使污泥堵塞转鼓和螺旋,损坏设备,并且造成药品浪费。
改造后,离心机处理量达到18m³/h,24h连续运转,生物处理系统污泥指数持续下降。投用40天后,污泥指数达到正常水平,由于污泥处理及时,酚氰废水处理作业区域控制污泥指数在较低水平,系统达到良性循环。目前,离心机采用扭矩控制,在运行数据设定为扭矩40N·m、转鼓转速2500rpm、加药配比为3‰(质量分数)的情况下,处理量即可达到10~18m³/h,排泥含水率为71.2%,泥饼成形良好,基本呈固态可堆积,运输方便,完全满足生产需求。现离心机每天开机10h左右,且操作简单,停机冲洗时使用清水约10m³/d。离心机主电机为30kW,螺旋电机为7.5kW。
3.2 效益计算
在不考虑人工成本的情况下,根据实际,工业水新水按7元/t计算,380V工业用电按0.4元/kWh计算。
带式压滤机年消耗水费用为7×180×365=459900元;年电耗费用为0.4×1.5×24×365=5265元。统计近3年备件材料情况,每年平均更换滤带4条,每条滤带9720元,消耗滤带费用为9720×4=38880元。
离心机年消耗水费用为7×10×365=25500元;年电耗费用为0.4×(30+7.5)×10×365=54750元。
因此,由带式压滤机改为离心机进行污泥浓缩每年可节约费用为(459900+5256+38880)-(25550+54750)=423736元。
4 结论
(1)处理能力大大提高。单机处理能力由原4~5m³/h提高到14~18m³/h,有效避免了系统中污泥不能及时脱除而产生堆积的情况,提升了系统稳定性。
(2)实现自动控制。压滤机的调节主要靠人工完成,包括进料量、加药量调节以及冲洗操作等。离心机工作时的进料、分离、卸料等是在高速运转下连续自动进行的,实现了离心机主转速、差速和扭矩可调节,还能自动调节絮凝剂配制浓度及进料量。并且,采用可编程程序控制器实现离心分离与离心冲洗过程的自动控制,节约了人力。
(3)维护保养方便。使用压滤机时,除轴承润滑保养外,检修托辊、滤带频繁,耗费检修人力、物力。离心机投用后,日常仅需润滑保养,定期进行点检紧固,平时检修也只是更换轴承和皮带即可。同时,离心机设有扭矩保护、功率控制及检测、测温等多重保护,能有效地减少突发故障对机器造成的损害。
(4)现场作业和检修环境极大改观。改造前现场污泥、污水遍地,车间内异味弥漫。而离心机对物料的分离是在完全封闭条件下进行,保证操作现场整洁污染,并保持生产环境的整洁卫生,实现文明生产。