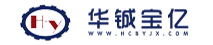
1 前言
卧式螺旋卸料沉降离心机是一种连续操作的、利用离心沉降原理分离悬浮液的离心机,可在全速运转时连续进行进料、沉降、分离、卸料操作。具有自动化程度高、生产能力大、运行稳定、清洁无污染、应用范围广等优点。广泛应用于化工、制药、食品、轻工、造纸、矿山及环保等工业部门。盐钙联产装置采用独有的MVR热泵盐钙联产工艺,该装置安装了一台沉降离心机,在使用过程中出现一些问题,值得大家总结与借鉴。
2 沉降离心机工作原理及适用分离范围
2.1 沉降离心机工作原理
沉降离心机结构主要由差速器、螺旋、转鼓、罩壳、机座、润滑系统、主电机以及气路系统组成。其工作原理是:悬浮液由中部的进料管进入全速运转的转鼓内,由于高速旋转产生的离心力场的作用,使悬浮液中密度较大的沉渣(重相)沉积在转鼓的内壁上,与转鼓作相对运动的螺旋叶片不断地将沉积在转鼓内壁上的固相颗粒刮下并推出排渣口。而密度较小的清液(轻相)则处于沉积层的内侧,通过螺旋的叶片所形成的螺旋型通道流向转鼓的柱段由溢流口溢出。从而实现密度相差的液-固两相的分离。
螺旋与转鼓之间的相对运动是由差速器实现的,差速器的外壳与转鼓相接,输出轴与螺旋相接,输入轴与电机相联。电机带动转鼓旋转的同时也带动了差速器输入轴的旋转,其输出轴按一定的速比将扭矩传递给螺旋,实现了离心机对物料的连续分离过程。
2.2 沉降离心机适用分离范围
(1)当液相粘度较小,固相颗粒度较大时,要求固、液比重差≥0.05g/cm³(固重、液轻)。
(2)当液相粘度较小,固、液比重差较大时(比重差≥1g/cm³)时,要求固相颗粒≥5μm。
(3)当液相粘度较大或固液比重较小并且固相颗粒很细小时,将影响分离效果,甚至不适用。
(4)当固相颗粒易破损时,也将影响分离效果。
3 沉降离心机在盐钙联产中的作用
3.1 盐钙联产工艺简介
盐钙联产装置是以高钙卤水为原料,生产氯化钠与氯化钙两种产品,其生产工艺可分为四个主要工序:四效强制预热、两级MVR蒸发制盐、三效钙液浓缩及两效高温制钙工序。其原理是利用氯化钠与氯化钙在溶液中的溶解度随温度升高时的变化趋势不同,卤水经四效强制预热工序和MVR蒸发浓缩后,NaCl蒸发结晶析出,经过离心分离后作为散湿盐产品。MVR排出的含CaCl2母液经三效钙液浓缩工序及两效高温制钙工序后,排出高浓度钙液经冷却结片后,进入干燥、包装得到二水氯化钙产品。
3.2 料液特性
随着钙液不断浓缩,氯化钙浓度越来越高,当浓缩到42%浓度设计参数如下:温度110℃,固液比7%,CaCl2含量619g/L,NaCl含30g/L,CaSO4含量3.1~4.3g/L,混合料液密度1.52t/m³,固体盐密度2.1t/m³,清液密度1.46t/m³,粘度12cP。该装置的原料为钙型卤水,其主要成分为:NaCl 250~260g/L,CaCl2 60~70g/L,CaSO4 0.6~1g/L。因此在氯化钙的生产中,其主要杂质是固体盐和硫酸钙颗粒,而随着钙液浓度越来越高,盐与硫酸钙结晶颗粒也会越来越细。42%钙液有如下特点:
3.2.1 温度高、腐蚀性大
氯化钙的腐蚀性比较强,随着其浓度与温度的升高,腐蚀性进一步增加。
3.2.2 固、液相密度差小
据以上参数测算,此处料液固、液密度差0.7t/m³,低于矿山、冶金,以及其他化工行业,查相关资料,如制盐行业卤水净化中盐泥脱水工序,混合料液的固液密度差为0.9t/m³,纯碱行业水平带滤机进料料液的固液密度差为0.9t/m³。
3.2.3 料液粘度相对较大、固体颗粒粒径区别
此处料液粘度高达12cP,固相硫酸钙的粒径细(小于10μm)占比80~85%。固相氯化钠粒径相对较大,根据过滤试验数据,粒径发布如下:粒径大于147μm占60~87%,在30~147μm区间占8~30%,30μm以下占5~10%。
3.3 沉降离心机在此工艺中的作用
沉降离心机设置在氯化钙含量达42%的工艺点后面,其目的是分离掉料液中含有的固体盐和固体硫酸钙以保证清液的质量,然后再对固体盐进行回收。
4 沉降离心机在盐钙联产中的使用状况
4.1 分离盐的效果远远优于分离硫酸钙的效果
沉降离心机运行一段时间后,对进料前后料液取样分析,结果如下:
(1)沉降离心机分离后的硫酸钙含量远远高于设计值,按设计值沉降离心机将分离掉79%硫酸钙,结果只分离了40%。
(2)沉降离心机分离后的氯化钠含量超过设计值,说明沉降离心机已将料液中绝大部分固形氯化钠分离掉。
4.1.1 调整沉降式离心机堰板高度和沉降式离心机运行频率,提高分离效果
沉降式离心机的分离效果,主要就是调整频率及液相堰板高度。对沉降式离心机频率在35Hz到48Hz范围内分频段运行;堰板高度从围堰距离60mm逐步调整至28mm,每调整5mm运行一段时间,检测分析分离效果,当调整到28mm时,分离母液量较小满足不了生产需求。堰板调整到45mm运行,频率调整至48Hz,沉降式离心机的分离后清液中硫酸钙含量能够达到3~4g/L。
4.1.2 调整后,分离硫酸钙效果有了提高,但是存在缺点
增加堰板高度和提高沉降离心机运行频率,虽然提高了沉降离心机分离效果,但堰板高度增加导致了沉降离心机清液量减少,固相中含液量增加。清液量减少必然导致钙产量降低;而固相中含液量增加按工艺流程又会将高浓度钙液随盐浆回收系统返回流程前端,形成物料循环往复,一定程度上增加了系统动力消耗,同时也造成部分热量前移,系统效率下降。适当减小堰板高度和降低沉降离心机频率,并不影响沉降离心机分离盐的效率,因此可按经济的方式调整运行沉降离心机。
4.2 解决硫酸钙超标的方法
后期通过攻关,采用其他沉降分离工艺,解决了硫酸钙偏高的问题。
4.3 沉降离心机运行可靠性
沉降离心机在盐钙联产运行中,总体稳定,但由于该处料液高温、高浓度,腐蚀性特别强,出现几次较严重故障,影响生产正常稳定运行。其问题主要表现如下:
(1)转鼓加强筋腐蚀。
(2)机头空心轴腐蚀变形。
(3)螺旋输送器进料空心轴腐蚀变形。
(4)螺旋输送器叶片腐蚀磨损。
(5)机壳内积块盐,导致固相斗堵,机件磨损,机体振动,同时导致机器负荷增加,差速器卡死。
上述现象大部分与该料液的特性有关,鉴于沉降离心机在盐钙联产中的重要作用,联合沉降离心机厂家吸取上述教训,作如下改进:
(1)所有与物料接触的零部件由原来用的TA2升级为TA10。
(2)与物料接触的承载件材质由原来用的TA2升级为TC4。
(3)机壳增加冲洗水,刷车冲洗。
沉降离心机改造升级后,运行稳定,投运一年未发生任何影响生产的故障,停机检查与钙液接触的部件以及与钙液接触的承载件,腐蚀磨损情况良好;机壳内也未发现积块盐现象。
5 结束语
沉降离心机在盐钙联产工艺中是不可或缺的核心设备,虽然不能高效分离料液中极细硫酸钙晶体,但更便于后续工序中盐浆再回收利用,因此总体使用是很成功的。它在回收系统盐浆,保证后道系统可靠运行,提高系统产能,降低系统消耗水平等方面起着非常重要作用。