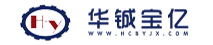
1 概述
离心机是利用离心力作为推动力来实现液相非均一系混合物的分离或浓缩的机械。基本原理就是采用机械的方法,将混合物置于一定的力场之中,利用混合物的各个相在力场中受到不同的力从而得到较大的相重差使其分离。在工业生产过程中,离心机属于后处理设备,主要用于脱水、浓缩、澄清、净化及固体颗粒分级等工艺过程。离心机以体积小、结构紧凑、分离效率高、生产能力大、附属设备少等优点广泛应用于化工、石油、食品、制药、纺织、冶金、煤炭、水处理和船舶等部门。
2 离心机的分类
离心机根据不同的分类原则派生出很多种类及名称,归纳以下几种分类原则,对后续设备的选型或可起到引领作用。
2.1 按照分离机理分类
2.1.1 过滤离心机
过滤离心机的转鼓壁上开小孔,转鼓内壁设有滤网(布),转鼓旋转时,液相由于离心力的作用,透过有孔鼓壁排出,固相截留在转鼓壁内,形成滤饼,实现液固分离。主要用来分离含固量高,固体颗粒大于10μm的悬浮液。代表机型有三足式离心机、上悬式离心机、卧式刮刀离心机、卧式活塞推料离心机、离心力卸料离心机、螺旋卸料过滤离心机等。
2.1.2 沉降离心机
沉降离心机的转鼓壁上无孔,也无滤网,悬浮液随转鼓高速旋转,物料中各相由于位置、密度不同,受到不同的离心力而分层沉淀,质量较大、颗粒较粗的物料分布在靠近转鼓壁,质量较小、颗粒较细的聚集其上,澄清液则从机上溢出,达到分离的目的。沉降离心机一般转速较高,n=7000~8000r/min,适用于固体含量较少,固体颗粒小于10μm的悬浮液。沉降离心机的常见机型有螺旋卸料沉降离心机。
2.1.3 分离机
分离机用于分离乳浊液,严格讲也属于沉降式,习惯上叫做分离机。转鼓壁上不开孔,依据液-液两相的密度差,在高速离心力场作用下,液-液分层,重相在外层,轻相在内层,固相沉于鼓壁通过一定的装置分别排出,实现分离。适用于含微量固体颗粒的乳浊液,固体颗粒小于5μm。常见机型有管式分离机、室式分离机、碟式分离机。
2.2 按照运转方式分类
2.2.1 间歇式离心机
间歇式离心机的加料、分离、卸渣过程是不同转速下间歇进行的。间歇式离心机主要用于固-液悬浮液的分离,其典型机型有三足式离心机、上悬式离心机等。
2.2.2 连续式离心机
连续式离心机的操作过程一直在全速运转条件下连续进行,生产能力较大,用于固-液悬浮液和液-液乳浊液的分离。连续式离心机的典型机型有卧式刮刀卸料离心机、卧式活塞卸料离心机、离心惯性力卸料式离心机等。
2.3 按照分离因数大小分类
按照分离因数大小,离心机可分为:
(1)常速离心机,Fr<3500,一般为过滤式,主要用于分离颗粒不大的悬浮液和物料的脱水。
(2)高速离心机,3500≤Fr<50000,一般为沉降式,主要用于分离乳浊液和细粒悬浮液。
(3)超高速离心机,Fr≥50000,一般为分离机,主要用于分离超微细粒悬浮液和高分子的胶体悬浮液。
2.4 按照卸料方式分类
按照卸料方式,离心机可分为:人工卸料、重力卸料、刮刀卸料、活塞推料、螺旋卸料、振动卸料、离心力卸料、进动卸料等。
2.5 按照转鼓主轴的空间位置分类
按照转鼓主轴的空间位置,离心机可分为卧式离心机和立式离心机。
3 离心机的选型依据
离心机的选型实质上就是根据物料的物性参数和工艺要求,在各种离心机机型中寻找一种能符合工艺要求的特定机器,这就要求对物料分离流程系统有比较全面的了解,注重离心机的各种技术参数。
3.1 明确分离的目的
分离的目的主要有:
(1)取得水含率低的固相。
(2)取得澄清度高的液相。
(3)对固-液二相均有要求,或对一相要求高,对另一相可适当放宽要求。
分离的目的不同,对选择的分离机的机型也就不同。
①用于液-液分离及液相澄清,乳浊液分离难度较大,可选用沉降离心机,选用高速分离机,依靠高速旋转把不同密度的液体分离开来。
②用于固相脱水可考虑选用过滤离心机及沉降离心机。
③浓缩过程首先考虑使用分离机,也常常选用螺旋卸料沉降离心机。
④固相分级常可选用螺旋卸料沉降离心机,如果处理量很小,也可选用三足式沉降离心机。
3.2 与选型有关的参数
3.2.1 物料的物性参数
物料的腐蚀性、磨蚀性、挥发性、毒性、密度、pH值、燃爆性等;悬浮液的固相浓度,固相颗粒尺寸、形状、分布,固-液二相密度差,表面张力和液相黏度等;乳浊液的液-液二相的浓度、液珠大小、布朗运动系数和黏度。
3.2.2 物料分离的工艺参数
物料分离的工艺参数主要有:物料的处理量、温度、压力,分离液的澄清度,分离固体的含水率、破损率,洗涤程度、分级和原液的浓缩度等。
离心机种类繁多,能满足同一分离要求的机型可能不止一种,在这种情况下,需要对比设备的价格及可靠性,选择结构简单、附属装置少、易于维修、运行费用低的设备。另外也要考虑行业习惯,分离工艺和设备在某行业中已非常成熟,在选型时调研现有运行情况,可以参考、借鉴。
4 离心机在某项目中的选用实例
4.1 项目背景
医药中间体为医药的主要活性成分,大致等同于半成品,属于多段工艺中间体,经过一定工艺处理的粗产物,是用于药品合成工艺过程中的化工原料或化工产品。某医药中间体项目以甲醇、硫磺、亚硝酸钠、氯化钾和氢氧化钙等原料,生产硫酸二甲酯、硝基甲烷、盐酸羟胺、硫酸钾、氯甲烷、硫酸、氯化钙等一系列产品。以该项目中离心机应用相对集中的80kt/a硝基甲烷装置结晶工段的工艺流程为例,来阐述离心机的选型和应用。
循环泵从盐液中间罐将盐液抽出送到离心机12-M301,经分离后得到的肟胺盐固体进入肟胺盐罐,然后装桶包装;分离液流入母液罐,然后由进料泵增压,经换热器升温后进入结晶器。母液在结晶器内蒸发结晶,浆液经泵送入离心机12-M302,硫酸钠固体送入产品库,分离液流入母液罐。母液经再次蒸发结晶后送入离心机12-M303进行固液分离,制得亚硝酸钠送至产品库。
3台离心机在结晶单元起到固液分离的作用,分别分离出肟胺盐、硫酸钠、亚硝酸钠等产品。
该项目涉及的物料品种多样,根据工艺要求,其分离要求也不尽相同,因此用于不同物料分离的离心机类型也不相同。
考虑兼顾不同设备形式选型的需要,除了选取硝基甲烷装置中的离心机12-M301和离心机12-M602为例外,还选取了200kt/a硫酸二甲酯装置中的离心机11-M501和50kt/a盐酸羟胺装置中离心机13-M201加以介绍。各装置的具体流程在这里不再赘述了。
4.2 离心机的选用情况
4.2.1 离心机11-M501
(1)选型原因
在上述项目中,离心机11-M501的作用是用于硫酸钠溶液的脱水,此处硫酸钠溶液的额定流量为3062kg/h,溶液密度为1300kg/m³、固含量=20%~25%,工艺要求脱水后硫酸钠产品中的w(H2O)≤5%。
用于固相脱水的离心机可以考虑过滤离心机和沉降离心机,综合考虑硫酸钠溶液中的固体颗粒含量较高、但颗粒度不祥以及流程中允许间断工况等条件,该项目的离心机11-M501初选立式刮刀型离心机。综合考虑各种因素,离心机11-M501选用了平板式自动刮刀下卸料离心机。
(2)结构
平板式自动刮刀下卸料离心机由机盖与机体、刮料装置、料位探测器、转鼓、轴承座、汇集料斗等构成。
(3)技术参数
平板式自动刮刀下卸料离心机的主要技术参数如下:
转鼓直径:1250mm
转鼓容积:400L
装料限量:520kg
转速:1000r/min
分离因数:698
主电动机功率:18.5kW
(4)特点及用途
该类刮刀离心机是过滤离心机中应用广泛适应性强的设备,分离因数可达到600,甚至1000以上,分离效果较好,具有结构简单、操作方便、适应性强、过滤时间可根据物料特性及分离要求灵活掌握、滤渣洗涤充分、固体颗粒不易破碎等优点,并可实现自动控制。因此,具有其他分离设备不可替代的优点,是制药工业中主要的处理设备之一。
4.2.2 离心机12-M301
(1)选型原因
离心机12-M301的作用也是用于硫酸钠溶液的脱水,此处硫酸钠溶液的额定流量为39000kg/h,密度为1300kg/m³、固含量=29.84%,工艺要求脱水后硫酸钠产品中的w(H2O)≤5%。
与离心机11-M501相比,此处硫酸钠溶液的固含量明显增大,且额定流量要大得多,故此处硫酸钠溶液的脱水选择了卧式螺旋沉降离心机。
(2)结构
卧式螺旋沉降离心机的结构由柱-锥转鼓、螺旋卸料器、差速器、机壳、进料管、固/液排出口等构成。
(3)技术参数
卧式螺旋卸料沉降离心机的主要技术参数如下:
转鼓直径:520mm
转鼓长度:2187mm
转速:2800r/min
转鼓与螺旋的转速差:5~25r/min
分离因数:2280
主电动机功率:55kW
(4)优点
卧式螺旋沉降离心机的主要优点有:
①该机单机生产能力大,结构紧凑。
②对物料适应性较大,在不能提供固相颗粒大小及分布的相关参数时也能完成分离。
③能根据工艺流程要求自动、连续、长期运转,实现封闭操作。
4.2.3 离心机12-M602
(1)选型原因
离心机12-M602用于盐浆液的脱水,其额定流量为33.7m³/h,密度为1350kg/m³、固含量=50%~60%,粒度主要分布在0.15~1.00mm,工艺要求脱水后产品中的w(H2O)≤3%。
由于盐浆液中的固含量高、固体颗粒物较粗,且要求脱水后固相的水含率低,因此盐浆液脱水选用双级活塞推料离心机比较适合。
(2)结构
双级活塞推料离心机的结构主要由回转体、推料机构、机壳、油路、机座、护罩、控制部分等组成。
(3)技术参数
双级活塞推料离心机的主要技术参数如下:
转鼓内径:720/800mm
过滤区长度:300mm
转鼓转速:700~1600r/min
分离因数:220~1147
推料次数(可调):30~80次/分
推料行程:50mm
主电动机功率:75kW
(4)优点
双级活塞推料离心机具有全自动操作、连续排渣、生产能力大、晶粒不易破碎等优点。
4.2.4 离心机13-M201
(1)选型原因
盐酸羟胺溶液的额定流量为3.5m³/h,密度为1326kg/m³、固含量=30%,粒度分布不祥,工艺要求脱水后固相中的w(H2O)≤5%。
盐酸羟胺固体物料是该项目的产品之一,对固相质量要求较高,固相需要清洗且含水率低,故离心机13-M201的作用不仅是对盐酸羟胺溶液进行脱水,还需对脱水后的固相进行洗涤。故离心机13-M201选择卧式螺旋卸料过滤离心机。
(2)结构
卧式螺旋卸料过滤离心机的结构主要由机壳、机座、外转鼓、内螺旋、差速器、进料管、洗涤管、出料/液口、传动主轴等部分组成。
(3)技术参数
该离心机的主要技术参数如下:
转鼓内径:350mm
转鼓长度:300mm
转鼓转速:3000r/min
分离因数:1762
处理能力:1~15m³/h
过滤精度:0.104mm(150目)
主电动机功率:15kW
(4)优点
该机型可连续操作,性能稳定,能耗低,密闭性好,分离效果好,能较好地适应产品要求,且转鼓10°的锥角可保证良好的洗涤效果。
4.3 其他考虑因素
离心机的选用不仅要满足分离目的要求,满足处理量、进出料特性、压力、温度等工艺参数的要求,还要考虑以下方面。
(1)运行环境的安全性
在爆炸危险区域的离心机,安全运行过程成为选型的首要要求。电动机的防爆等级应该符合爆炸性危险环境的区域等级,另外在选型时还需考虑配置其他防爆措施,比如:现场防爆按钮、防静电皮带、变频器控制、防爆电磁阀、防爆接近开关、防爆隔离栅、静电接地、能耗制动、氮气保护、氧气含量在线检测等。上述防爆措施并不是所有有防爆要求的场合都要配置,应综合考虑实际工艺和生产环境的需求科学选配。
(2)过流介质的腐蚀性
根据离心机过流的介质,应选用合适的材料来制造,以满足物料的腐蚀性、磨蚀性、pH值等参数要求。在医药中间体项目中,设备材料选用要求与盐酸羟胺直接接触的设备表面不和其发生化学变化或析出铁离子,不仅仅是转鼓等金属材料,所有接触物料的零部件材料都应达到这一要求,包括密封件、紧固件等。采用选用关系防腐性能、洁净度要求。按所分离物料的腐蚀数据(化学性质、温度、浓度等),要求选用合适防腐材料,如316L不锈钢或TA2钛合金;对一些特殊的物料,可采用哈氏合金或涂层处理。
(3)行业的特殊性
针对某些行业的特殊要求,以医药中间体项目所选用离心机为例,在保持离心机分离特性的前提下,根据 质监总局和 标准化管委会联合发布的GB 28670-2012《制药机械(设备)实施药品生产质量管理规范的通则》,对离心机这类原料药机械和设备提出了具体的要求:易于清洗、消毒或灭菌,便于生产操作和维修、保养,并能防止差错或减少污染。与药品直接接触的设备表面应光洁、平整、无死角、耐腐蚀,不与药品发生化学变化或吸附药品。设备所用的润滑剂、冷却剂等不得对药品或容器造成污染。管道的设计和安装应避免死角、盲管。针对以上要求,在选型时就必须充分考虑离心机结构型式,要求离心机应有紧急停车、自锁功能和振动保护或过振报警装置。
5 结束语
离心机选型是一项简单而又复杂的工作,随着分离技术的不断创新发展,分离机械的选型显得尤为重要。综上所述,认为离心机选型主要考虑的因素如下:
(1)首先根据所需分离的混合液的处理量及固含量、固体颗粒的粒径分布,是晶体状还是粉末状等来选择合适的离心机,确定滤布型号。
(2)依据所需分离物料的腐蚀性,确定与物料接触部分需用不锈钢(SUS304、316、316L)或钛材、衬塑(改性聚乙烯)、哈氏合金及特殊双相不锈钢等。
(3)依据物料中是否含有机溶剂及强腐蚀化学品选择合适的密封材料。
(4)根据所在区域的防爆等级,物料情况在设备制造及电器控制部分制作中充分考虑,使离心机的密封结构,密封材料及防静电措施满足现场要求,如需要可以增加惰性气体保护装置等。
(5)依据用户对设备自动化要求程度,选择自动化/手动操作的分离设备。
(6)对同时满足工况要求的不同形式离心机做经济对比,选择运行稳定、结构简单、附属装置少、易于维修、运行费用低的设备。
(7)考虑行业习惯,选用在某行业中已非常成熟,运行情况良好的设备。
技术经验丰富的制造厂多年来积累设计制造现场经验,也可与设备制造厂家的专家们沟通商定选择合适的机型。