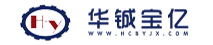
1 前言
随着辽河油田开发进入中后期,采出液含水不断上升,油品不断变稠,增加中的增产措施使采出液性质越来越复杂,使辽河油田的稠油老化油数量急剧增加。据不完全统计,全油田老化油总量接近10万吨/年(折合纯油)。由于稠油老化油在80℃时的粘度为400mPa·s左右,密度在0.92g/mL以上,用常规的破乳脱水手段难于处理,致使大量的老化油常年积存在在联合站内,严重影响着辽河油田的安全生产。大量的老化油不能处理达标后外输,既严重影响油田的经济效益,也严重影响油田的商品量。
该技术解决了稠油老化油无法处理这一难题,可对储油罐中位于油水界面上的中间过渡层的老化油、污水处理站回收水池内的污油、污水处理废弃物排放点内的污染物进行回收处理。具有分离时间短,不污染周边环境,不造成二次污染的特点。有着很好的经济效益和社会效益。
2 室内研究
2.1 工作原理
先降老化油通过加热模块加热到90℃左右,利用自动加药装置加入老化油破乳剂沉降2小时后,进入三相离心分离机,通过离心作用,使老化油中密度大的固体颗粒沉降到转鼓壁上,油水两相形成同心圆柱并分别排出。
破乳剂结合离心方法处理老化油技术的原理是利用老化油破乳剂的破乳功能使油水界面膜破坏,老化油进入离心机后,利用老化油中的油、水、固相颗粒相互间的比重差,并依靠离心力场使之扩大几千倍,固相在离心力的作用下被沉降,二种液相被分离开来形成二个液层,从而实现渣/水/油三相分离,并在特殊机构的作用下分别排出机体。整个进料和分离过程均是连续、封闭、自动地完成。
处理流程制作了一套自动化控制软件,通过此软件可对处理量、温度、处理前后老化油含水率等运行参数进行实时监测,并通过无线远传将数据传到控制室及各相关部门。另外,进料量采用变频器控制,出油缓冲罐、出水缓冲罐采用高低液位自动控制,使得出料泵能够自动控制启停,并加装高位报警装置,以便能够使设备安全、自动的条件下运行。
2.2 高效稠油老化油破乳剂的研制
老化油破乳剂的研制是针对冷一联、曙四联老化油开展起来的。辽河油田老化油是稠油老化油,粘度高,油水密度差小,老化油破乳及离心分离难度大。
因为直径小于10微米的水滴是用任何方法都无法分离的,所以必须加入破乳剂,其目的是让老化油中被乳化的水聚集成相对较大的水滴,然后才能借助离心力场的作用使油水迅速分离。在稠油老化油用破乳剂研发过程中,自行研制了药剂的分子结构及合成工艺,克服原有破乳剂对老化油破乳无效的缺点。针对辽河油田的稠油老化油,合成出三大类60余种破乳剂,并使用冷一联合站的老化油进行筛选评价,优选出适合冷一联合站老化油脱水的破乳剂系列配方。
2.2.1 加药温度的确定
实验采用冷一联老化油,随着处理温度的升高,脱水量也在增加。当加药温度超过90℃时,脱水量无明显变化,因此加药温度90℃较佳。
2.2.2 加药量的确定
实验采用冷一联老化油,加入不同的破乳剂,考察加药量对脱水量的影响。随着加药量的增加,脱水量也在增加,但加药量超过600ppm后,脱水量变化不大。针对冷一联老化油,破乳剂A2的破乳效果较好,加药浓度确定为600ppm。
2.2.3 稠油老化油破乳剂筛选
实验90℃下进行,加药量600ppm,对冷一联老化油,A2的脱水效果较好。
2.3 稠油老化油专用卧螺离心机的研制
针对稠油老化油成分复杂、粘度高、含渣多造成的脱水难题,研制出处理稠油老化油的专用三相卧螺离心机,通过对通用卧螺离心机的结构、材质、螺旋叶片的角度和螺距、油水腔位置及液池深度等多项改进,解决了排渣不畅、磨损严重、油水混流等问题,实现了油水渣高效分离,使分离后的油中含水2.92%、水中含油1623.68mg/L、纯净油品回收率达95%,并且单机处理能力到达100m³/d,满足了目前平均单站处理量的需求。
3 结果与讨论
目前,稠油老化油处理技术已在辽河油田各联合站全面推广。累计处理稠油老化油8.4×104m³,回收纯净油品4.3×104m³,纯净油品回收率为95%,处理后老化油含水平均值为2.92%。老化油处理系统运行平稳,满足了辽河油田各联合站的正常生产要求。
通过连续运行并跟踪记录数据,可以明显看出老化油处理后平均含水从48%左右降到3%以下,满足了正常生产要求。
在处理量为4m³/h、处理温度90℃左右,加药量600ppm情况下,老化油处理后纯净油品回收率平均值为95%。
4 结论
室内评价及现场试验表明,采用破乳剂结合离心的方法处理老化油,解决了辽河油田稠油老化油破乳脱水的难题,满足了现场生产的需要。
采用该方法处理稠油老化油,处理后原油含水平均值为2.92%,纯净油品回收率平均值为95%,能够达到工业化生产的要求。
该技术提高了联合站的有效库容,对保障联合站的安全平稳运行具有重要意义。
采用该技术处理后的老化油可以直接进入原油集输系统,提高了合格商品油量,经济效益和社会效益显著,具有广阔的应用前景。