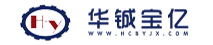
1 概述
石油炼制企业污水处理厂产生的油泥和浮渣,处理难度大、成本高。随着《 危险废物名录》(2021年版)颁布,石油炼制过程中含油废水隔油、气浮、沉淀等处理过程中产生的浮油、浮渣和污泥(不包括废水生化处理污泥)被归类为HW08废矿物油类危险废物,代码251-003-08。废水生化处理污泥未纳入危险废物,污水处理场产生的含油污泥与生化污泥分开处理将成为未来发展趋势。
对脱水后的含油污泥进行减量化、资源化、无害化处理,降低企业危险废物处理成本是非常必要的。本文介绍了某炼油企业污水处理场油泥减量化处理技术。
2 含油污泥特点及现有处理技术
2.1 含油污泥特点
(1)成分复杂。
含油污泥一般都含有大量老化原油、蜡质、沥青质、胶体、固体悬浮物、细菌、盐类、酸性气体、腐蚀产物等。
(2)脱水难度大。
含油污泥是性质十分稳定的悬浮乳化物,属于多相体系且充分乳化,黏度大,不易脱水。
(3)臭味大。
含油污泥中含有硫化物、氨、硫醇、硫醚等恶臭污染物,在处理过程中易散发,产生二次污染。
(4)含有易燃易爆物质。
含油污泥中的大量挥发性烃类物质易与空气混合形成爆炸性气体,因此在选择处理工艺时需考虑防爆问题。
2.2 现有处理技术
含油污泥的无害化处理技术与资源化利用技术众多,含油污泥无害化处理技术包括焚烧法、固化处理技术、超临界水氧化处理技术、地耕法及堆肥法等。资源化利用技术包括溶剂萃取技术、热分解技术、超声波处理技术、调质机械分离技术、化学清洗技术等。
每种处理方法都有其自身的优缺点,如焚烧法、固化法、超临界氧化法、溶剂萃取法、热分解技术、调质-机械分离法,这些技术具有快速、高效等优点,但能耗高、成本高、处理不彻底;生物法(地耕法与生物堆肥法)具有节能、投资少、运行费低等优点,但处理时间长、受环境影响较大。
目前,含油污泥产量高,性质复杂,如果不及时处理,不仅会对环境造成不同程度的污染,也会造成巨大的经济损失。含油污泥无害化与资源化处理迫在眉睫。
3 工程实例
3.1 项目背景
某炼油企业原油加工能力达到3500kt/a,拥有16套主要生产装置及相应配套设施,具有渣油催化、渣油催化、氧化沥青、气体分馏、聚丙烯、MTBE、延迟焦化、重整加氢等深度加工装置,可以加工任何性质的陆上原油和进口原油。主要产品有汽油、柴油、铝箔轧制系列油、变压器干燥油、润滑油、聚丙烯、聚酯、车用液化气、油漆,石化助剂、除锈剂、防凝剂、纯净水、矿泉水等。
污水处理采用“隔油+浮选+气浮+生化处理+深度处理组合工艺”,污水处理场运行过程中产生的污泥主要包括隔油罐罐底油泥、隔油池底油泥、浮选浮渣、剩余活性污泥。现有“三泥”处理设施不完善,隔油池、浮选池排出的油泥、浮渣入污泥池送至油泥沉降浓缩罐,将其含水率由约98%脱水至约85%。
3.2 设计指标
污泥处理系统的设计指标如下:
污泥处理规模:1.5t/h
浓缩后原料含固率:≤2%
浓缩后原料含油率:≤10%
污泥干化后含水率:25%~40%
污泥干化后温度:≤50℃
3.3 工艺流程
来自污水处理站的罐底油泥和浮渣经浓缩后,送入管道混合器,和破乳剂充分混合进入破乳罐进行破乳;油泥中的油在破乳剂的作用下从乳化液及污泥中分离出来,浮油定期排至油水储罐,破乳后的泥水混合物由提升泵输送至离心脱水机,脱水后的污泥送至污泥暂存罐。离心脱水机排出的液相被送至油水储罐,经提升泵送至高效分离器,高效分离器分离出的污油至污油罐回收利用,污水至污水处理系统,废渣排至污泥暂存罐。污泥暂存罐中的污泥由污泥泵送入油泥干化机中进行干化处理,干化后的干泥含水率控制在25%~40%,落至干泥仓内。干泥仓直管段外壁设置了夹套,通入冷却水将干泥冷却至50℃以下,同时干泥仓侧壁安装2个振捣电动机,底部采用旋转锁气阀排料,将冷却后的干泥排至吨包袋。干化机排出的尾气抽吸至洗气塔中,采用回用污水对其进行洗气和冷凝预处理,预处理后送至业主废气处理系统。
3.4 主要设备
该油泥、浮渣减量化工程污泥处理系统的主要设备及其技术参数见下表:
名称 | 单位 | 数量 | 规格及技术参数 |
油泥提升泵 | 台 | 2 | 螺杆泵,1用1备,Qmax=5t/h,H=30m,变频控制 |
破乳剂投加装置 | 套 | 1 | 储罐有效容积3m³;隔膜计量泵,Qmax=20L/h,H=40m,配备变频电动机,1用1备 |
破乳罐 | 台 | 1 | φ3000mm×9000mm,有效容积52.3m³;罐材质为碳钢,内刷防腐涂料 |
离心脱水机 | 台 | 1 | 处理能力1.5m³/h;转鼓内径300mm,转鼓速度4500r/min;主机功率15kW,辅机功率2kW |
油水储罐 | 台 | 1 | 4300mm×2000mm×2500mm,有效容积15m³;停留时间4h,常压操作;碳钢防腐 |
高效分离器 | 台 | 1 | 1870mm×12360mm×1800mm;处理能力5m³/h,功率18.5kW;与物料接触部分的材质为316L不锈钢 |
油泥干化机 | 台 | 1 | 处理能力200kg/h(极值240kg/h);换热面积60㎡;操作温度160℃,操作压力-0.5kPa;变频电动机37kW |
洗气塔 | 台 | 1 | φ1200mm×5120mm;双级独立液体循环,梯度冷凝和水洗,下层散装填料1寸鲍尔环,上层规整填料250Y |
3.5 工程设计特点
该油泥、浮渣减量化工程设计特点如下:
(1)对油泥进行破乳预处理,离心脱水机采用进口脱水机,具有强化破乳功能,离心后污泥含水率约85%;高效分离器能分离油泥中的大部分油类,对油泥中的油进行回收;油泥干化机可改善油泥的脱水和干化性能。
(2)为保证安全及防止臭气外逸,干化装置采用负压(-0.5kPa)方式运行,同时设氮气保护。
(3)为防止干化系统内污泥自燃和氧含量达到危险水平,设置氧气在线监测仪2台,并与氮气阀门联锁,保持系统的氧含量<1%,干化机内氧含量超标时进行报警。
(4)为确保干化单元安全运行,油泥干化机采用0.5~0.7MPa(G)的低压饱和蒸汽作为热源,控制干化热源温度不高于170℃,控制干化温度在不高于100℃的安全范围内进行操作。
(5)破乳罐采用蒸汽外盘管伴热,设有远传液位计,液位控制高度7400±150mm。油泥在破乳罐停留34.8h,在破乳剂的作用下进行破乳分离。
4 结束语
本工程采用“浓缩+破乳+离心脱水+干化”工艺处理污水处理装置油泥及浮渣,将生化污泥和含油污泥分别处理。本工程于2019年4月15日投入运行,并于2019年8月20日至8月22日进行标定,累计进料172.10m³,进料含水率平均值为94.47%,产生干化油泥3.78t,含水率均值为2.92%。油泥减量化明显,达到97.80%。
本油泥减量化装置投资1300万元,占地面积264㎡,直接运行成本82.26元/吨,该装置建设投产后,不仅解决了油泥直接干化可能产生的危险性,还为企业节约危险废物处理费940万元/年,具有较好的经济效益和环境效益。