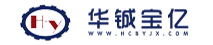
我国油脂企业面临的环保问题主要集中在“三废”治理上,即废水、废气、固体废弃物的处理。废水作为主要污染源之一,处理难度较大,投入成本也相对较高。按照废水排放标准的要求,废水的处理主要针对CODcr、氨氮、总磷和总氮等指标,常规的处理方法有物化处理方法(如隔油破乳、混凝沉淀、气浮法等)和生化处理方法(如活性污泥法、生物接触氧化法、水解酸化法等)。排放要求较高的有深度处理工艺,如强化除磷、膜过滤和离子交换等工艺。在上述废水处理的每一个工艺环节中均或多或少产生固体废弃物——污泥。随着环保要求越来越严格,固体废弃物的管控力度逐渐加大,其处理成本逐渐升高,目前油脂工厂废水处理产生的污泥处理费用多在300~800元/t,有的甚至更高。污泥处理费用占整个废水处理成本的比例越来越高,这无疑增加了企业环保的投入。
现阶段大多油脂企业聚焦于废水处理工艺的研究和改善,对废水处理过程中污泥产率的研究较少,现有的污泥处理工艺主要集中在末端的压滤,同时对处理成本的关注较少,但随着固废相关管理条例的出台,对企业的管理要求相对提高。因此,如何降低废水处理过程中污泥产率的问题显得尤为重要。本文主要论述植物油厂废水处理过程中污泥产生来源和如何降低其产率,以期为植物油厂废水处理提供参考。
1 植物油厂废水处理过程中污泥产生来源
1.1 废水处理工艺
植物油厂废水主要分为含油废水和其他废水,其中:含油废水主要是油脂精炼过程中产生的,其磷浓度高,含油、含皂,处理难度大,产生污泥量多。其他废水主要是油料压榨、浸出过程中产生的,相对处理难度较小。油脂压榨废水主要特征为高温、高氨氮、量大;油脂精炼废水主要特征为高含油、含皂、含磷,同时还具有一定温度,废水量相比压榨的稍少。
不同的废水处理工段需添加不同种类的药剂,会产生不同形态的固废。与压榨废水处理工艺相比,精炼废水处理工艺增加了隔油破乳工段,对于废水排放标准要求较严格的则要进行强化除磷。根据植物油厂废水处理工艺,可分析废水处理过程中污泥产生的来源。
1.2 污泥产生来源
1.2.1 隔油破乳系统产泥
油脂精炼废水含有较多油、皂,通常采用硫酸破乳,浮油长时间积聚变硬,较早的做法为人工打捞浮油,有的则是反溶后进入下一步工序,这将导致后续处理负荷增大,需要更多的药剂和能耗;隔油破乳系统长时间运行后设备内部也将产生污泥,通常由破乳系统增加的污泥量较少,且污泥无机质含量较高,较易压滤,但如果破乳、隔油不彻底会导致过多的乳化油进入下一道工序,经混凝沉淀后的污泥含油量增加,难以压滤,泥饼含水率增高,将导致大量的污泥产生。
1.2.2 混凝沉淀和气浮产泥
油脂精炼废水通常含磷较高,以前较多的废水处理工艺没有破乳系统,而是直接在精炼废水中添加混凝剂PAC、絮凝剂PAM和协同除磷剂Ca(OH)2除磷,药剂之间的相互作用使得磷和药剂之间形成絮体。药剂使用量较大时,废水中的油脂在药剂的作用下形成密度较大的胶体转变成污泥,在初沉池中进行泥水分离、沉淀压缩,然后通过排泥系统进入污泥浓缩池进行污泥浓缩,整个过程伴随着药剂与磷的反应,其反应效率影响药剂的添加量和磷的去除率;而密度较小的胶体则随水流进入下一步气浮,通过溶气系统溶解在水中气泡的减压释放,携带至设备表面,通过刮渣设备收集至污泥池中。在气浮过程中,同样添加少量的混凝剂PAC和絮凝剂PAM,密度较大的颗粒、胶体则沉淀至气浮池底部,气浮池底部的污泥有机质含量较低,无机质含量较高,容易压滤,压滤后的污泥含水率较低。刮渣过程产生的污泥较多,含油率较高,不易压滤脱水,含水率较高,是油厂废水处理过程中污泥产生的主要来源。
1.2.3 生化反应产泥
在植物油厂废水处理工艺中生活反应工艺通常较多采用生物接触氧化法或活性污泥法,实际根据废水排放要求选用,通常对出水含磷有较高要求的采用活性污泥法,对出水没有含磷要求或含磷要求不高的则通常采用生物接触氧化法。
生物接触氧化法主要依靠向安装在设备设施内部的填料接种驯化微生物,微生物附着在填料的表面,随着时间的推移形成越来越厚的生物膜,生物膜的微生物种类也从生物膜的内表面至外表面形成厌氧菌、兼氧菌和好氧菌,形成较为稳定的菌落环境,对营养物质进行分解。附着在填料上的生物膜,微生物成分复杂,污泥龄相对较长,依靠曝气和水流的冲刷力使生物膜脱落、更新,随出水流入沉淀系统分离。与活性污泥法不同之处在于同样的好氧系统中,生物接触氧化法存在着较为复杂的3种菌群协同处理废水中的污染物。生物接触氧化法尤其适合低负荷水质,污染物浓度较低时,活性污泥法难以形成大量的悬浮污泥,从而影响处理效果,而采用生物接触氧化法,则可通过增加设备设施内部填料,快速形成较多的生物膜,从而缩短生化反应启动时间,改善出水水质,使出水指标更好。生物接触氧化法由于污泥龄相对较长,产生的活性污泥老化程度较高,因此产生的剩余污泥量较少,且污泥无机质含量相对较高,更容易压滤,压滤后的泥饼含水率较低,因此污泥产量也较低。
活性污泥法在废水生物处理方法中是普遍使用的方法,具有处理效率高、脱氮除磷能力强、运行维护方便等优点。活性污泥法通常选用的工艺有AAO工艺、奥贝尔氧化沟工艺和SBR工艺等。其中:AAO工艺具有较高的脱氮除磷效率,对进水水质的适应能力较强,适合低中高负荷水质,调控灵活方便,易管控;奥贝尔氧化沟工艺要求较长的停留时间和较低的BOD负荷,出水指标较低,另外该工艺具有完全混合活性污泥法的优点,有较强的抗冲击能力等特点;SBR工艺处理流程较短,控制灵活,适合工业废水的间断运行,系统整体构筑物较简单,布置紧凑,节省投资,可适应中高负荷水质。
活性污泥法工艺需要污泥回流和循环液回流,具有较高的CODcr去除率,同时兼具脱氮除磷功能,总磷以剩余污泥的形式排出。活性污泥法较为适合高负荷生化反应,污泥龄较短,剩余污泥的老化程度较低,因此产生的剩余污泥量比生物接触氧化法稍多,污泥有机质含量较高,同样压滤后的泥饼含水率液较高。生物接触氧化法污泥较易脱水、产量少。
下表是活性污泥法(脱氮、除磷)和生物接触氧化法在污泥量、污泥龄等方面的对比。
工艺类型 | 污泥量 | 污泥龄(d) | 有机质含量 |
活性污泥法-脱氮 | 一般 | 10~23 | 一般 |
活性污泥法-除磷 | 较多 | 5~10 | 较高 |
生物接触氧化法 | 较少 | 较长 | 较低 |
由上表可见,在不同工艺下,生化反应产泥率不同。
1.2.4 强化除磷和深度处理产泥
当出水总磷要求较高时,依靠前端物理化学处理和生化反应除磷较难达标排放,后续需辅助强化除磷设施,通常采用混凝沉淀化学法除磷,与前端混凝沉淀一样会产泥。当要求出水回用时,则需增加深度处理工艺,该深度处理工艺废水悬浮物含量较小,产生的污泥量极少,同时污泥脱水性能较好,几乎不影响整个系统的产泥率。
综上,植物油厂废水处理过程中污泥来源主要有混凝沉淀+气浮和生化反应,其中在混凝沉淀过程中需要去除大量的污染物磷,因此需投加大量的药剂,产生的污泥量大且不易脱水。因此,提出出水水质的不同要求,有针对性地选择合适的废水处理物化和生化工艺,优化每个工段的设备设施,对降低整个系统污泥的产率尤为重要。
2 降低植物油厂废水处理过程中污泥产率的措施
2.1 优选破乳剂,回收废水中的油和皂类物质
油脂精炼废水含有较多的油、皂,回收废水中的有机皂类对降低后续污泥产率至关重要,同时回收的皂类物质还可以变废为宝再利用。工业上通常选用硫酸进行破乳除皂,硫酸破乳除皂具有以下缺点:
(1)硫酸属于危化品,在经济较为发达地区采购较为困难,同样在添加时有一定的安全隐患,加大了企业安全生产管理的难度。
(2)引入了硫酸根,会消耗后续添加的除磷用钙离子,药剂之间相互作用,相互消耗,降低了药剂的处理效率,增加了药剂投加量和污泥产量。
(3)硫酸的酸性较强,破乳后的浮油流动性较差、黏度较高,不易收集和输送。考虑上述缺点,选用硫酸破乳不易降低污泥产率,同时存在安全生产隐患,因此选择新型破乳剂势在必行。
结合生产实际情况,新型破乳剂需具备以下特点:
(1)具有较高的酸度,同时可规避危化品管理的要求,即pH不能小于2。
(2)具有除磷功能,同时不与后续添加的除磷剂钙盐相互反应,具有混凝沉淀的功能。
(3)不影响破乳后皂类物质的经济性能,能够使其具有较好的流动性,便于输送、储存。
(4)不含有磷酸根和其他有机酸,因为硫酸根与后续添加的除磷剂钙盐相互反应,而磷酸根和有机酸则增加后续生化处理的难度。因此,该新型破乳剂只能是经盐酸调配而成,同时引入在中心条件下具有混凝沉淀功能的三价铁离子,结合市场情况新型破乳剂选用酸性聚合氯化铁较为合适。
酸性聚合氯化铁中的盐酸和乳化的皂类物质发生化学反应,以强酸置换弱酸的原理,能够较容易地置换出皂类物质中的脂肪酸类物质,该脂肪酸类物质不溶于水,密度比水小,因此浮于废水表面。酸性聚合氯化铁中的铁盐则溶于废水中,经后续加碱和石灰调节pH至中性后,可发生水解反应形成胶体,同时与废水中的磷酸根反应生成难溶物质,在胶体的作用下产生混凝沉淀,通过初沉池进行泥水分离,达到除磷的目的。
下表为新型破乳剂酸性聚合氯化铁与硫酸进行破乳时的优缺点比较。
破乳剂 | 破乳效果 | 除磷效果 | 皂类产量 |
酸性聚合氯化铁 | 接近100% | 约60% | 约2.75kg/m³(以废水计) |
硫酸 | 约95% | 无 | 忽略不计 |
由上表可见:新型破乳剂酸性聚合氯化铁破乳彻底,使得水化磷脂变成非水化磷脂被分离出系统(形成了废油皂),减少了沉淀的污泥量,产生的废油皂量大,较易集中收集;非水化磷脂含有大量的磷,起到除磷的作用,同时药剂中的铁离子具有混凝除磷功能,减少了后续除磷剂的添加量,进而降低了产生的污泥量;回收的油皂类物质则能变废为宝进行销售,能够产生较好的经济效益。
2.2 优化药剂添加种类和配比
隔油破乳后精炼废水中不溶性有机悬浮物的含量降低,但仍含有较高的磷,少量的有机悬浮物将影响后续处理工艺,增加生化工段处理的难度,降低生化处理效率。较高含量的磷增加了生化除磷及后续除磷的难度,受生化除磷能力的限制,较高含磷废水进入生化工段后,污染物中碳、氮、磷含量不成比例,导致污泥生长受到影响,常见的现象有污泥沉降缓慢、生长过快等;生化工段出水含磷将超过控制标准,需在后续工段中强化除磷,如:需增加混凝沉淀工序,增加了药剂的使用量,即使如此仍然存在水质超标的风险。因此,在隔油破乳后仍需添加混凝剂PAC、絮凝剂PAM和除磷剂Ca(OH)2,预先将过多的悬浮物和总磷去除。此时添加的药剂受溶解性悬浮物的影响较小,主要作用是除磷。常规的除磷剂通常是使用生石灰,而生石灰的主要成分是CaO,使用生石灰时有两个作用:
(1)生石灰与水反应生成碱性熟石灰,提供钙离子结合磷酸盐生成难溶物质,此过程主要作用是除磷。
(2)生石灰与水反应生成碱性熟石灰,提供碱性基团氢氧根用于中和隔油破乳后废水的酸性,使得pH为7.5左右,为混凝剂PAC、絮凝剂PAM的反应提供较为适合的中性环境,此过程主要作用是调节pH。
在废水磷含量一定的条件下,使用足够量的生石灰除磷时,除磷效果取决于废水中的pH,因此在使用生石灰除磷时,通过实验确定用以满足除磷的反应所需要的生石灰添加量之后,用强碱代替生石灰调节pH,则效果更好、调节速度更快,同时能够降低生石灰的使用量,减少因投加生石灰而产生的污泥量。考虑经济性,代替生石灰调节pH较适合的强碱为片碱或液碱,所以选用一部分液碱代替生石灰调节pH。因此,优化药剂添加种类和配比能够显著提高药剂的利用率,有效减少污泥的产生量。
2.3 选用合适的生化处理工艺
废水处理工艺对于污泥产生量有重要影响。在前面生化反应的两种工艺即活性污泥法和生物接触氧化法对比时,发现两种工艺产生的污泥量是不同的。因此,针对不同的进水水质和排放标准选用合适生化处理工艺,对降低污泥的产率有较大的帮助。
2.4 提高污泥压滤设备的压力,降低含水率
污泥压滤关乎着压滤后泥饼的含水率,而含水率决定着产出的污泥量。压滤设备的压力较低时,不能有效挤压出污泥中的水分,则会导致泥饼含水率较高,污泥产量较大;反之,压滤设备的压力较高时,能够有效挤压出污泥中的水分,使得泥饼含水率较低,从而有效降低污泥的产率。因此,选用合适的污泥压滤设备能够有效降低污泥含水率,直接降低污泥的产率。目前污泥压滤设备使用较多的有叠螺机、带式压滤机和隔膜板框式压滤机,在不同的运行工况下各有优点:污泥有机质含量较低时可优先考虑采用程控式隔膜压滤机(板框式压滤机的一种),其具有二次加压功能,再根据不同工况条件选用不同透气量和不同型号的滤布,能够使泥饼含水率降低至60%左右,远低于叠螺机和带式压滤机泥饼含水率,可大大减少污泥的产生量。下表是叠螺机、带式压滤机、隔膜板框式压滤机在泥饼含水率、脱水形式、压力大小方面的对比。
设备类型 | 泥饼含水率(%) | 脱水形式 | 压力大小 |
叠螺机 | 85~90 | 离心脱水 | 较小 |
带式压滤机 | 80~90 | 挤压脱水 | 一般 |
隔膜板框式压滤机 | 60~80 | 油压+水压/气压 | 较高 |
通过上述分析可知,废水处理系统污泥的产生来源于整个废水处理环节,充分发挥每一个处理环节的作用、提高药剂的利用率、选择合适的生化处理工艺和污泥压滤设备,可以有效降低废水处理系统污泥产生量。
3 应用实例
以某粮油工业废水项目为例,其废水站设计处理能力1500m³/d,油脂精炼废水含皂量超过3000mg/L,选用酸性聚合氯化铁为破乳剂,添加常规药剂如混凝剂PAC、絮凝剂PAM和除磷剂,用部分液碱代替除磷剂Ca(OH)2调节pH,污泥压滤设备选用程控式隔膜压滤机。优化工艺前(破乳剂为硫酸,未用液碱调节pH,选用带式压滤机或叠螺机等压滤污泥),由于产生的能够回收的皂类物质较少,并未进行统计。
下表为该废水项目与行业平均水平的进、出水效果与执行标准指标,混凝剂PAC、絮凝剂PAM和除磷剂用量,污泥含水率、污泥产率等的对比。
项目 | 项目指标 | 行业指标 |
进水CODcr(mg/L) | ≈14500 | 10000~15000 |
进水总磷(mg/L) | ≈145 | 80~150 |
出水CODcr(mg/L) | 30 | 50 |
出水总磷(mg/L) | 0.3 | 0.5 |
PAC单耗(mg/L) | 109 | 200 |
PAM单耗(mg/L) | 8.5 | 15 |
除磷剂单耗(mg/L) | 465 | 550 |
污泥产率(kg/m³) | 2.95 | 5.5 |
污泥含水率(%) | 60 | 75 |
由上表可见:该废水站进水水质与行业平均进水水质相似,排放标准高于行业排放标准,出水水质由于排放标准;该项目使用的常规药剂量明显低于行业平均水平,污泥含水率和污泥产率明显低于行业平均水平,说明采取上述降低污泥量的措施可以有效降低植物油加工行业废水处理过程中的污泥产率。
下表是选用新型破乳剂后2017~2019年度回收皂类物质的量和污泥产率统计。
年份 | 皂类物质回收量(t) | 污泥产率(kg/m³) |
2017 | 220 | 2.75 |
2018 | 550 | 2.65 |
2019 | 850 | 2.62 |
注:污泥产率以废水量计。
由上表可见,采用优化措施,回收了皂类物质,这有助于增加企业经济效益。
4 结语
植物油厂废水处理过程中会产生大量的污泥。随着我国环保要求越来越严格,固体废弃物的管控力度加大,植物油厂污泥处理成本也逐渐增高。根据植物油废水水质和排放标准,优化废水处理过程中每隔产泥工段来降低污泥产率至关重要。实践表明,通过优选破乳剂,降低加药量,选择合适的生化处理工艺和污泥压滤设备等措施,可有效降低植物油厂污泥产率。