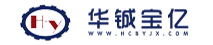
1 前言
通常从地下刚采出的原油乳状液稳定性较低,易实现破乳脱水。但在曝氧条件下,原油乳状液由于受空气、温度和阳光等环境因素的作用发生化学反应,以及各种乳化剂、沙尘的混入,经过一段时间乳化剂聚结在油水界面膜上使原油乳状液的稳定性增强,形成了所谓的“老化油”。老化油在形成过程中,由于化学反应及固体颗粒杂质、高分子化合物、污水处理药剂、增产增注化学剂等乳化剂的混入,使其界面活性物质增加,并随时间延长在油水界面不断富集,使界面膜的强度和厚度增加形成稳定性很高的原油乳状液。与从地下刚采出的原油乳状液相比,其特点是轻质成分含量较少,沥青质、胶质含量高,固相渣质含量高,电导率高,原油乳状液稳定性高,难以破乳脱水。室内实验通过对老化油性质进行研究,从宏观和微观上揭示老化油乳状液形成及稳定机理,并对影响稳定性的因素进行分析研究。寻找到经济有效的老化油脱水方式:热化学-离心脱水技术。
2 加热工艺研究
无论对老化原油采取何种脱水方式,都离不开温度的作用,结合油田实际情况开展掺蒸汽和掺热水两种方式对乳状液性质的影响。
2.1 加热方式对老化原油脱水影响
原油脱水工艺中一般采用换热器对原油进行升温加热,为热化学脱水作准备,由于含水原油各种杂质含量很大,换热器容易产生腐蚀与结垢现象,所以根据油水乳化的实际特点在新疆油田的一些区块采用了掺蒸汽的方式来加热原油,在缩短工艺流程、降低成本、提高热效率上均取得了比较好的效果。因此能否在老化原油离心脱水过程中采用掺蒸汽的加热方式来加热老化原油对于简化工艺、提高热效率、降低成本具有重要的意义。
通过显微照相分析掺蒸汽加热、掺热水加热、水浴加热前后老化原油水珠粒径分布对比,结果表明掺热水加热的方式能够明显提高一厂红浅老化原油中水珠粒径中值,根据斯托克斯沉降公式结论,这种加热方式能够提高原油的脱水速度,降低原油脱水难度。与之相反,掺蒸汽加热方式降低了一厂红浅老化原油中水珠粒径中值,提高了老化原油的脱水难度。
2.2 掺热水及活性水对老化油的洗涤作用研究
老化油中含有大量的杂质是影响老化油脱水的主要因素之一,研究热水及活性水对老化油的洗涤作用,是老化油加热脱水工艺研究的主要因素之一。
通过将不同量热水(占原油总量的20%、30%、40%、50%)掺入原油中,经不同混合强度下,在水浴中恒温静置30min,观察试管下部分出的水量及机杂数量。
通过试验可以看出:用热水常规洗涤老化原油,对原油中杂质的去除能力较弱;掺活性水对老化原油的洗涤作用比直接掺热水的洗涤能力大,但洗涤效果仍然不理想;两种洗涤方式只能洗出较大杂质颗粒,而对细小的杂质洗涤效果较差。
2.3 老化油加热工艺的选择
根据以上研究,原油必须在一定温度下脱水才能取得较好的脱水效果;如果只考虑原油脱水采用换热和掺热水加热是理想的加热方式,而采用掺蒸汽加热方式时,必须保证原油中有较高的含水量(大于10%),避免分散相水珠较小和水珠间距较大的情况发生;掺热水及掺含活性剂的热水对老化油中的杂质有一定的洗涤作用,但存在热水掺入量较大的问题。结合红浅处理站现场具有高压蒸汽的条件,现场在实际流程中采用先掺蒸汽后再经过活性热水层洗涤的流程。
3 老化油现场脱水设备的选择及工艺流程的确定
老化油中固体颗粒吸附在油水界面形成一定厚度和强度的界面膜,起到空间稳定作用,是老化原油稳定性高的主要原因。因此,去除固体颗粒渣质将有助于界面膜的破坏,提高老化原油的脱水效率。离心技术多用于渣质分离,因此,离心法脱水特别适用于含机渣较多的老化油的脱水。
3.1 脱水设备的选择
离心机分离技术在船舶、冶金、医疗、食品等行业应用较为广泛,由于原油处理量大且磨砺性工质含量高等工况,以前没有人把离心机用于原油脱水。随着机械工业的发展,实力较强的离心机制造商把离心机用于原油脱水,首先应用成功的是加拿大HACA油田。本次实验选用该型离心机为碟式分离机。
碟式分离机工作原理是被分离的物料进入分离机的转鼓内部,在强大的离心力场作用下,轻相流体经过一组碟片束的分离间隔中从碟片的大端沿表面流向碟片的小端,比重较大流体及固体沿碟片壁向大端运动,固相积聚在沉渣区,定期自动排出机外。比重较小的液体沿碟片壁向碟片小端运动,汇聚至转鼓顶部的向心泵处,由向心泵输出至下道工序。本机属自动排渣型,其工作过程中,可根据物料成分的不同来调节分离和排渣周期的各个参数(如排渣时间、操作水压力等)。
3.2 完善配套工艺
采用了全密闭流程,防止油气水泄漏。在离心机原油进、出口管线安装了在线原油含水检测仪、流量计,实现在线连续检测计量。离心机内部增加了油水比重环控制出油含水、污水含油的自动控制。设置了排渣过程中清水置换流程,每次排渣时,离心机 清水置换出腔中原油,减少了排渣原油损失,降低渣中原油含量,便于渣的处理。
3.3 自动检测
建立了完善的自动检测控制系统,系统运行后实现计算机在线检测进、出油线原油含水、流量、温度;自动控制出油含水、排渣及排渣过程中清水置换。基本实现系统的自动检测和运行。
4 水洗、沉降、缓冲罐的设计
设计了500方水洗、沉降、缓冲罐,在一个罐内实现了原油水洗、重力沉降分离、缓冲的作用。
5 生产工艺的确定
老化油脱水生产的基本流程是来油卸入缓冲方罐,由转油泵转入掺汽装置进行提温,转输过程中均匀加入破乳剂,同时均匀加入盐水,原油加温后进入500方水洗沉降缓冲罐,利用罐内底部3米水层进行水洗除渣及除去水溶性药剂,油罐的中上部起缓冲作用,脱出游离水的原油从罐上部出油,再由转油泵转入离心机脱水,脱出原油进入净化油罐,脱出水进入水系统。
6 现场运行效果评价
工业化老化油处理工艺从2007年7月下旬开始试运行,并整改了试运行中存在的问题。9月转入正常工业生产。通过离心机处理的原油来源为红浅大坝收油和采油一厂稀有处理站罐底乳化油。
老化油处理系统自投产以来,运行稳定。处理后的原油含水基本在0~2%之间,并且能够有效地分离原油中混合的杂质、悬浮物等。原油在进入离心机前必须掺热到80℃以上,并且温度越高离心机的脱水效果越好。离心机在处理杂质较多的大坝收油时处理量一般在4.5m³/h左右,在处理稀、稠油站的净化油罐底压油时处理量可以到6~7m³/h。离心机的排渣间隔、原油品质的好坏也可以影响离心机的脱水效果。
7 结论
(1)采用离心分离的方法处理老化油能够使杂质分离出来,同时与采用热化学沉降方法相比,脱水效率明显提高;离心机用于处理老化油技术是可行的,同一种油品温度越高处理量越大;不同油品黏度越大处理量越小。
(2)掺蒸汽加热对低含水老化原油造成二次乳化,使离心脱水效果受到明显影响,原油含水率越高,掺蒸汽造成的乳化现象越小,对含水率大于转相点的老化原油的脱水难度基本没有影响。老化油采用热水洗涤和活性水洗涤,可以有效去除部分机渣及水溶性化学剂,便于后续流程脱水;加热方式可采用蒸汽加热和掺热水(水洗)相结合的方式。