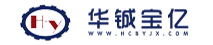
石油化工企业在生产过程中产生的污泥主要包括隔油池底泥、浮选浮渣、剩余活性污泥,通常简称为“三泥”。这些污泥是由水、油及固体物质组成,并含有蒽、芘、酚类、苯系物、重金属等有毒并有恶臭味的物质,混合在一起形成稳定的乳化体系。由于其特殊的性质,处理成本较高而且技术难度较大,一直是国内外炼油行业的环保难题。早在1989年 有关规定就将含油污泥列为危险废物,2016版《 危险废物名录》明确将炼油企业污水处理场产生的油泥列为HW08类危险废物,虽然活性污泥未再被列入危险废物名录,但是在实际处置过程中,环保部门大多要求进行危险危废鉴定,鉴定过程耗时耗力,大多企业为确保依法合规,还是将活性污泥按危险废物处置。近年来,随着我国环保法规的日趋严格和企业技术进步的强烈要求,相关法律如《 清洁生产促进法》和《固体废物环境污染防治法》也要求必须对油泥进行无害化处理,三泥的减量化、无害化、稳定化、资源化处理日益成为环保工作的焦点。
九江石化污水处理场每年产生含水率98%的剩余活性污泥量约14000t/a,含水率98%的含油污泥量约为28000t/a,总污泥量约为42000t/a。经过离心脱水后,产生含水率85%的污泥约5600t/a,按江西省污泥处置价格2800元/吨计算,每年污泥处置费用需1568万元,给企业造成较大的经济负担,且需承担第三方污泥处置过程中的环保风险。
为降低污泥处置的经济负担和环保风险,九江石化采用了油泥破乳脱油及干化处理技术对原有三泥处理设施进行了改造。
1 工艺流程及原理
1.1 工艺流程
该装置由污泥浓缩、酸化破乳、污泥干化三部分组成。污水处理场产生的含油污泥到油泥调节罐沉降浓缩脱水后,进入油泥分离装置,在油泥分离装置中加入浓硫酸调节pH值在1~2.5,对油泥破乳除油。除油后的油泥进入污泥调理器调整pH值至中性,然后进入泥水分离器,与活性污泥一起进行污泥浓缩处理,处理后污泥含水率98%。浓缩后的污泥通过给料泵送入离心脱水给料罐,送入离心脱水机。经过离心脱水处理后的污泥在重力作用下排入污泥罐中暂存,然后通过干泥泵将脱水污泥送入“双向剪切楔形扇面叶片式污泥干燥机”中进行干化处理。
干化过程中产生的水蒸气采用排湿风机引入洗气塔中进行冷凝和洗气处理。排出气体送入粉末活性炭生化处理池。装置产生的污水送污水处理场处置,污油送到焦化装置回炼。
1.2 工艺原理
1.2.1 污泥浓缩原理
搅拌刮泥装置采用悬挂式中心传动形式,工作桥横跨池子,工作时整机载荷都作用在工作桥中心,污水经中心导流筒均匀流向池四周,随着流速的降低,污泥沉淀于池底,通过刮臂带动栅条旋转起搅拌作用,加速活性污泥的下沉,从而达到浓缩的目的。底部刮泥系统将沉淀在池底的污泥刮集到中心泥坑中,靠静水压力将其从污泥管中排出。
1.2.2 油泥破乳原理
油泥主要由罐底油泥和浮渣组成,其中固体颗粒高度乳化,且含有较高的石油类物质,形成了水、泥和油的稳定混合液,从而使得这种污泥有别于剩余活性污泥和其他污水处理系统所产生的污泥。这类污泥不宜采用传统的污泥脱水方法处理,且油泥中所含的主要污染物是具有回收价值的石油类物质,至于油泥中所含的固体物质,则主要是氢氧化铝和其他一些无机悬浮固体颗粒。
在破乳剂的作用下,可对油泥进行破乳分离和污油回收处理。经过对油泥中的污油进行破乳分离这一特殊的预处理后,油泥分离装置底部的泥、水、混合物自动排入后续的调理器中,向调理器中投加烧碱,利用油泥分离液中高价金属离子反应时产生的混凝作用,对污泥进行混凝调理。油泥分离装置上部的污油自流至污油罐中暂存,当回收污油达到高液位时,用污油泵输送至污油回收设施。
1.2.3 污泥干化原理
污泥脱水主要设备是卧螺离心机,其利用固液两相的密度差,在离心力的作用下 ,加快固相颗粒的沉降速度来实现固液分离。具体分离过程为污泥和絮凝剂药液经入口管道被送入转鼓内混合腔,在此进行混合絮凝,由于转子(螺旋和转鼓)的高速旋转和摩擦阻力,污泥在转子内部被加速并形成一个圆柱液环层(液环区),在离心力的作用下,比重较大固体颗粒沉降到转鼓内壁形成泥层(固环层),再利用螺旋和转鼓的相对速度差把固相推向转鼓锥端,推出液面之后泥渣得以脱水干燥,推向排渣口排出,上清液从转鼓大端排出,实现固液分离。
污泥干化主要设备为传热型双向剪切楔形扇面叶片式污泥专用干化机,其是一种间接加热低速搅拌型干化机。设备内部有二根或者四根空心转动轴,空心轴上密集并联排列着扇面楔形中空叶片。轴体相对转动,利用角速度相同而线速度不同的原理和结构巧妙地达到了轴体上污泥的自清理作用,极大限度地防止了污泥干化过程中的“抱轴”现象,以较快速度使得污泥在干化过程中迅速冲过“胶粘化相区域”。同时巧妙的结构使得污泥在干化过程中达到了双向剪切状态。采用夹套式壳体结构,使得污泥在机器内部各个界面均匀受热,轴体转动,污泥在设备内不断翻腾,受热面不断翻新,大大提高了设备的蒸发效率,既达到了污泥干化的目的,又实现了整套装置的低成本运行。
1.3 主要工艺参数
油泥分离装置处理规模为6.53t/h,油泥含固率2%(w)、含油率2%(w),除油率大于90%。剩余污泥设计处理规模为0.53t/h,含水率88%。
污泥干燥机污泥处理能力为0.675t/h,处理能力为1t/h,污泥含水率85%,干化污泥含水率25%~40%(平均30%)。
2 装置运行情况
2.1 装置运行标定情况
三泥处理装置建成投运后,经试运及调整,达到稳定运行状态,为检验装置的运行状况、能源消耗、运行效率等,并为进一步优化工艺操作,降低装置能耗物耗,实现装置效益提供依据,2020年3月9日9:00-3月12日9:00对装置开展72h连续运行标定。
标定期间主要操作参数见下表:
时间 | 油泥分离出口pH值 | 调理器出口pH值 | 蒸汽压力/MPa | 干化机内排气温度/℃ | 干化机内氧含量1/% | 干化机内氧含量2/% |
设计值 | 1.5~2.0 | 6.5~7.5 | 0.5~0.7 | <160 | <2 | <2 |
3月9日 | 1.59 | 6.95 | 0.66 | 101.15 | 0 | 0.065 |
3月10日 | 1.86 | 7.04 | 0.73 | 107.77 | 0.028 | 0.013 |
3月11日 | 1.72 | 6.47 | 0.72 | 111.32 | 0.039 | 0 |
平均值 | 1.72 | 6.82 | 0.70 | 106.75 | 0.022 | 0.026 |
物料平衡见下表:
项目 | 3月9日9:00 | 3月12日9:00 | 总量 | 每小时进料量 |
离心机进料/kg | 11090911 | 11479959 | 389048 | 5403.33 |
破乳装置进料/kg | 11305416 | 11507011 | 201595 | 2799.93 |
干化污泥/kg | - | - | 10500 | - |
注:离心机进料包括破乳后油泥量及剩余污泥量
主要分析数据:
时间 | 原料油泥含油率/% | 破乳污泥含油率/% | 污油回收率/% | 离心脱水污泥含水率/% | 干化污泥含水率/% |
3月9日 | 4.73 | 0.41 | 91.33 | 66.67 | 15.34 |
3月10日 | 5.38 | 0.45 | 91.64 | 71.81 | 11.20 |
3月11日 | 6.54 | 0.52 | 92.05 | 69.34 | 13.45 |
平均值 | 5.55 | 0.46 | 91.67 | 69.27 | 13.33 |
化工辅材消耗统计:
项目 | 每小时消耗量 | 累计消耗量 |
32% NaOH/kg | 94.46 | 6801.2 |
98% 浓硫酸/kg | 56.69 | 4081.7 |
油泥脱水剂/kg | 31.25 | 2250.0 |
能源消耗统计:
项目 | 设计每小时消耗量 | 3月9日9:00 | 3月12日9:00 | 总量 | 每小时进料量 |
回用水 | 6t | 17448586kg | 17510044kg | 61458kg | 0.85t |
循环水 | 0.3t | 3017861kg | 3070348kg | 52487kg | 0.73t |
1.0MPa蒸汽 | 0.7t | 775871.6kg | 787451.5kg | 11579.9kg | 0.16t |
低压氮 | 10m³ | 90448.1m³ | 92667.7m³ | 2219.6m³ | 30.83m³ |
耗电量 | 83kW·h | - | 74.9kW·h |
从上面五表可以看出,标定期间装置工艺参数均符合设计要求。处理含水率为98%以上的油泥、污泥共389t,经干化至含水率为15%内的污泥降低至10.5t,实现了污泥减量化。
装置运行期间,油泥平均进料量为2.8t/h,原料油泥平均含油率为5.55%,破乳后油泥含油率为0.46%,污油平均回收率为91.67%,油泥处理的资源化效果显著。
2.2 运行效益分析
油泥破乳运行费用见下表:
项目 | 实际单耗 | 单价 | 吨耗/(元/t油泥) |
32% NaOH | 33.74kg/t | 600元/t | 20.24 |
98% 浓硫酸 | 20.25kg/t | 700元/t | 14.18 |
油泥脱水剂 | 5.79kg/t | 4800元/t | 27.76 |
电 | 0.97kW·h/t | 0.54元/kW·h | 0.52 |
合计 | 62.71 |
污泥干化运行费用见下表:
项目 | 实际单耗 | 单价 | 吨耗/(元/t油泥) |
循环水 | 0.1352t/t | 0.26元/t | 0.0352 |
1.0MPa蒸汽 | 0.02963t/t | 100元/t | 2.9630 |
低压氮 | 5.7093m³/t | 0.7元/m³ | 3.9965 |
耗电量 | 13.8704kW·h/t | 0.54元/kW·h | 7.4900 |
合计 | 14.48465 |
乳除油单元的运行费用为62.71元/t油泥,离心机和干燥机的运行成本为14.48元/t污泥。
标定期间,处理三泥389t,其中油泥201.6t,活性污泥187.4t,干化污泥产量10.5t,干化污泥含水率平均为13.33%,折算成含水率为85%的三泥处理费用约为209元/t。在该装置投运前,三泥经离心机脱水,脱水后含水率为85%的污泥外委处置,处置费用约为2400元/t(2020年框架协议)。三泥处理装置投运后,三泥处理费用约下降了2191元/t,实现了油泥减量化、低成本处理。
3 结论
对应用“油泥破乳脱油与干化处理集成技术”建成的三泥处理装置标定,从标定结果可以得出以下结论:
(1)污油平均回收率为91.67%,油泥处理的资源化效果显著。
(2)干化后的污泥仅为原污泥量的2.70%,减量97.39%,减量效果显著。
(3)吨污泥处理费用下降了2191元,处置费用大幅下降。
(4)干化污泥相比原污泥,外委处置运输环节环境风险大幅降低。
综上所述,应用该技术实现了浮渣、油泥及剩余活性污泥的减量化、资源化处理,污泥处置费用大幅下降,为炼化企业的油泥处理探索出一条良好途径。