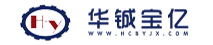
含油污泥主要产生于石油开发、运输、炼制及含油污水处理过程中,属于危险固体废弃物。近年来,随着 环保法规逐步完善及企业绿色低碳发展的要求,对油气田开发产生的污泥处理标准越来越严格,污泥的资源化利用与污染防治问题越来越引起重视,目前曙光油田日产含油污泥量高达300t。
清罐油泥和浮渣底泥是采油及采出液处理过程中分离出来的原生细泥质油泥,占总油泥量的80%以上。经分析,原生细泥质油泥所含泥质粒径绝大部分在100μm以下,其中,清罐和浮渣底泥泥质粒径在50μm以下的占比70%以上。泥质组分矿物分析表明,泥质绝大部分为斜发沸石。曙光油田油泥稠油比重大,胶沥质含量高,一部分落地油泥混合了高含量的原油、固体以及部分植物纤维和塑料垃圾。同时,在稠油开采和采出液处理过程还需要添加大量的化学药剂,在表面活性剂的作用下,稠油与泥质吸附结合紧密,状态极为稳定。因此,辽河油田油泥处理重点在于含有多种类型杂物的分选处理,难点在于对细泥质油泥的处理。
1 主要研究内容
目前,曙光采油厂含油污泥主要有落地油泥、清罐油泥、浮渣、底泥等,按照分质分类处理思路,落地泥和清罐泥采用“逐级分选-化学精细热洗”工艺处理,浮渣、底泥以及化学热洗底泥用于制作油泥调剖剂,用于稠油蒸汽吞吐井调剖封窜。
1.1 稠油细泥质油泥化学清洗技术评价及药剂优选
1.1.1 实验方法
利用传统方式筛选清洗剂效率较低,费时又费样品。根据文献报道,在含油污泥体系中,存在油-水、油-泥、泥-水等多个界面,热化学清洗法主要是利用清洗剂的表面活性降低各界面的界面张力,通过乳化作用促进原油从固体表面分离。
在热化学清洗法处理含油污泥工艺中,有效且常用的药剂可分为以下几类:阴离子表面活性剂、非离子表面活性剂、两性离子表面活性剂,其中,阴离子表活剂与非离子表活剂的研究和应用较为广泛,碱性无机盐能增强表活剂的表面活性,绿色表活剂具有良好的乳化性、洗涤性、增溶性、润湿性等特点,同时易于生物降解。因此,可将化学表活剂、绿色表活剂、碱性无机盐进行组合形成新的清洗剂配方。
1.1.2 清洗条件的优化
根据现场提供的处理条件,固定部分参数:两级清洗、两级离心工艺,泥(含水70%)/水=1:1,温度80℃,清洗剂总加量4%,清洗结束后3000r/min下离心15min。现对热化学清洗的另外两个重要参数搅拌强度和搅拌时间进行优化。
(1)搅拌强度的优化。以混合油泥为处理对象,选择泥/水=1:1,加入清洗剂4%(含水70%的混合油泥质量百分比),80℃下搅拌水洗15min。以一次清洗后油泥含油率(差量法)为指标,对搅拌水洗强度进行优化。清洗后泥中残油率随着搅拌强度增大而减小,当强度大于500r/min后,残油率下降趋势明显减缓,所以选择搅拌强度500r/min。
(2)搅拌时间的优化。选取清洗条件:泥/水=1:1,清洗剂加量4%,搅拌强度500r/min,清洗温度80℃,3000r/min离心15min条件下对搅拌水洗时间进行优化。残油率起初随着搅拌时间的增加急剧下降,当搅拌时间大于30min后,下降趋势放缓,且当时间持续延长以后,残油率反而上升。综合考虑处理效果与能耗成本,选择搅拌时间30min为宜。
1.1.3 混合油泥的清洗
清洗工艺:采用两级清洗、两级离心工艺。
级清洗:向100g混合油泥(含水70%)中加入100g水,清洗剂加量2%(混合油泥质量百分比),80℃保温,500r/min下搅拌水洗30min,清洗结束后取上层浮油测定含泥量,取下层泥水两相离心,离心条件:3000r/min,15min。离心后取中层水相测定水中含油量和水中含泥量,取下层泥相进行二级清洗。
第二级清洗:向一级清洗并离心后的泥相中加入100g水,清洗剂加量2%(含水70%的原始混合油泥质量百分比),80℃保温,500r/min下搅拌水洗30min,清洗结束后全部取出离心,离心条件:3000r/min,15min。离心后取水相测定水中含油量和水中含泥量,取下层泥相105℃烘干2h并测定含油率。
1.1.4 实验结论
(1)使用不同方法测定的清洗后泥相总油含量在2.5%~4%,TPH<2%,原油回收率超过90%,水中含泥和水中含油均小于1%,油中含泥小于2%。
(2)针对混合油泥以界面张力法筛选出了清洗剂B。采用两级清洗、两级离心工艺结束后全部取出离心(3000r/min,15min)。清洗后泥相总油含量小于2%,TPH小于1%,原油回收率超过90%,水中含泥和水中含油均小于1%,油中含泥小于2%。
1.2 分选预处理-化学精细热洗工艺
该工艺的原理是油泥在加热、机械搅拌及离心条件下,利用化学药剂的润湿和乳化作用,将原油从泥砂表面剥离。主要工作机理:油泥通过破碎、流化搅拌、筛分、清洗等工序逐级分选清洗杂物和粗质泥砂,通过两级清洗离心分离实现细泥质的净化。
分选预处理-化学精细热洗工艺主体为一体化油泥处理装置,装置由多个撬装组合,结构紧凑、占地面积小,装置分为“分选预处理撬装区”和“化学精细热洗撬装区”。分选预处理由破碎、预热、流化、转笼筛分、水洗分选、洗砂分砂、格栅除杂、振荡筛分、溶药加药等工序组成,主要清洗分离出达标的粗质泥砂和重质杂物,分离出少量需后续处理的轻质杂物和丝状物;化学精细热洗由均质除油、三相离心、二次洗泥、两相离心、油水分离等工序组成,主要清洗分离出达标的细泥,产生污油和污水。
1.3 油泥调剖技术
组分及特性分析表明,含油污泥具备制成调剖剂的可行性。稠油油藏经过长期蒸汽吞吐,其孔隙度、渗透率等地层参数与原始状况已有很大差别,需针对不同油泥加入适合的改性化学剂和添加剂,制成有一定强度和耐冲刷能力的调剖剂。
1.3.1 油泥颗粒调剖剂
以污水厂活性泥为原料,加入一定量悬浮剂和分散剂,同时,添加合适种类和大小的固相颗粒,提高封堵强度。悬浮剂为与油泥配伍性较好、具有一定触变性的钠基膨润土,其能保持体系有较高悬浮性和强度;固相颗粒选择200目以上有一定膨胀系数的树脂颗粒,产生桥架作用,对孔道进行封堵;分散剂为一种聚有机电解质,主要是降低油泥调堵剂的界面张力,防止形成油、泥、水聚集体。该体系悬浮性大于8h,封堵率50%~90%。
1.3.2 油泥聚合物复合调剖剂
配方主要成分为底泥,加入适量聚丙烯酰胺及絮凝剂,利用油泥微粒表面-OH基团与聚丙烯酰胺分子的-NH2基团结合形成氢键,大量氢键作用使聚合物能稳定地吸附在油泥微粒表面,使油泥絮凝成更大的颗粒,从而产生封堵作用。体系成胶时间12~24h,黏度80~500mPa·s,耐温大于200℃。
1.3.3 油泥改性高温封口剂
以固相含量较高的浮渣为主料,加入无机凝胶、固化剂、增强剂、活化剂、悬浮剂等,按适当比例复配而成。通过控制反应温度和活化剂用量,调节成胶速度和强度。体系封堵率≥95%,突破压力大于20MPa,耐温超过300℃。
实验表明,3种油泥调剖剂岩心封堵率75.2%~95.2%,可通过段塞优化组合满足不同类型储层封堵需求。
2 现场应用效果
近年来,污泥复合段塞调剖现场实施58井次,累计投入资金598万元,累计增产原油2.8万吨,调剖使用油泥19.1万吨,化学精细热洗达标处理油泥6.8万吨,创造综合经济效益1.16亿元。
3 结语
化学精细热洗+油泥调剖的分质分类处理模式,有效满足了落地泥、清罐泥、浮渣、底泥等不同成分、不同性质的油泥处理需求,实现了油泥的减量化、无害化及资源化,应用前景广阔。