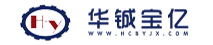
在石化行业,“三泥”通常是指石化污水处理过程中产生的油、水、渣的混合物,主要来源是隔油池底沉积的底泥、浮选池投加絮凝剂后经空气浮选时产生的浮选渣、曝气生化处理的剩余活性污泥和少量污油罐的罐底泥及沉砂池的泥砂。这些污泥由不同含量的油、水及固形物组成,混合在一起形成非常稳定的乳化体系,并含有苯系物、酚类、蒽、芘、重金属等有恶臭味及毒性的物质,其性质特殊,脱水和处理技术难度大且成本高。由于其残油、有机物、重金属含量高,是一种严重的污染物,且随着进厂原油质量变差和数量的增加,“三泥”产量大幅度增加,含有的石油烃类及其它有害物质无法堆放和处置,若不加以处理,不仅占用大量耕地,随雨水的冲刷污染土壤、地面水和地下水,对周围土壤、水体、空气造成污染,而且会造成资源的浪费。因此,完善和严格污泥处理工艺,实现“三泥”的资源化处理具有重要的应用前景。
1 国内外“三泥”处理现状
国内外广泛研究的“三泥”处理技术,主要有填埋、堆放、焚烧、生物降解、溶剂萃取及送焦化处理等,而这些技术在经济、技术及设备运行维护等方面均存在诸多不足。
1.1 填埋、堆放
对于填埋、堆放来说,直接填埋既浪费了其中的宝贵能源,还导致环境污染,产生渗滤液和臭气,而且要占用大量的土地和花费大量的运输费用。而固化后填埋可降低环境危害,但多数不能满足现行的环保要求。因此各国对这种方法并不看好。
1.2 焚烧
焚烧法是对经预先脱水浓缩后的“三泥”送至焚烧炉进行焚烧,温度800℃~850℃,经30min焚烧即可完毕,焚烧后的灰渣需进一步处理。经焚烧后多种有害物几乎全部除去,减少了对环境的危害,大大地减少了污泥的体积和重量;杀死一切病原体,污泥处理速度快,不需要长期储存;污泥可就地焚烧,不需要长距离运输;可以回收能量用于发电和供热。缺点是焚烧过程中产生了二次污染,耗资巨大,设备复杂,对操作人员的素质和技术水平要求比较高。
1.3 生物法
生物法处理是利用微生物将含油污泥中的石油烃类作为碳源进行同化降解,使其完全矿化,转变为无机物质(CO2和H2O)的过程。主要指堆肥法和生物反应器法。堆肥法是将含油废弃物与适当的材料相混合并成堆放置,使天然微生物降解石油烃类的过程。含油污泥的堆肥处理需提供氧气、菌种和营养,为保持油泥的疏松状态,还需加入填充剂。生物反应器是一种将含油污泥稀释于营养介质中使之成为泥浆状的容器。由于生物反应器能人为地控制充氧、温度、营养物质等操作条件,烃类物质的生物降解速度较其他生物处理过程更快,加入驯化过的高效烃类氧化菌,可加快烃类的生物降解。
生物法的优点在于:对环境的影响小,生物处理是自然过程的强化,其产物是二氧化碳、水和脂肪酸等,不形成二次污染或导致污染物转移,费用低,经过生化处理污染物残留量可以大幅降低。缺点是:由于是利用微生物进行处理,处理周期比单纯的物化法要长,且不能回收污泥中的原油,有很多有机物难于降解,重金属等成分则根本无法消除。
1.4 溶剂萃取法
萃取法是利用“相似相溶”原理,选择一种合适的有机溶剂作萃取剂,将含油污泥中的原油回收利用的方法。
超临界流体萃取技术是正处于开发阶段的含油污泥萃取技术,它将常温、常压下为气态的物质经过高压达到液态,并以之作为萃取剂,由于其巨大的溶解能力以及萃取剂易于回收循环使用。常用的超临界流体萃取剂有甲烷、乙烯、乙烷、丙烷、二氧化碳等,这些物质的临界温度高、临界压力低,而且原料廉价易得,是良好的超临界萃取剂,且密度小,易于分离。萃取法的优点是处理含油污泥较彻底,能够将大部分石油类物质提取回收。但是由于萃取剂价格昂贵,而且在处理过程中有一定的损失,所以萃取法成本高,还没有实际应用于炼厂含油污泥处理。此项技术发展的关键是要开发出性能价格比高的萃取剂。为了降低成本,美国开发了溶剂萃取-氧化处理含油污泥的专利技术: 步萃取采用粘度低、碳原子少(较佳为2~4)的丙烯、环丙烷、丁烷等轻质烃为溶剂;萃取后残留泥中仍含一些聚合芳烃等有机物,需用相对分子质量较高的烃进行第二步萃取,而该专利技术则用湿法氧化工艺代替。氧化剂用空气、氧气和硝酸盐等,污泥中保持一定水分,以促进氧化反应。在温度200℃~375℃、压力0.1MPa的条件下,经一段时间后,有机物被氧化为CO2和H2O,残渣可符合直接填埋的要求。
1.5 “三泥”的焦化处理
含油污泥中含有一定数量的矿物油,其组成主要有烷烃、环烷烃、芳香烃、烯烃、胶质及沥青质等。焦化法处理含油污泥是利用高温条件下烃类的热裂解和热缩合反应产生液相油品、不凝气和焦炭产品。如美国阿瑟炼油厂在1992年8月前用Mobil技术处理固含量平均为2.5%的污泥,此后5个月采用Scaltech技术处理固含量平均为10%~12%的污泥,注入量由8个月前的2.1%增加到5.8%。焦炭的灰分含量由0.5%上升到0.86%。戴永胜等利用矿物油的焦化反应机理,对含油污泥焦化反应制备含碳吸附剂的工艺进行研究,结果表明,在焦化温度为400℃、反应时间为80min的条件下,可以将其净化成效果较好的吸附剂。较好处理的优点是投资少,不足的是涉及焦化装置的改造比较复杂,注入量有限,处理总量少。赵东风等利用平均含油率为69.46%,含水率为4.71%的含油污泥进行焦化反应,反应时间为60min,反应温度为490℃,反应压力为常压。在此条件下,液相产品的回收率为88.23%,产品主要为汽油、柴油和蜡油。
2 “三泥”的资源化处理
2.1 污泥的燃料化
“三泥”中含有石油烃类,燃烧产生大量的热量,如果直接焚烧,造成资源的浪费,因此考虑用“三泥”做燃料,充分利用其中的热量。
污泥的燃料化是污泥综合利用的一种方法。其一是使污泥厌氧发酵产生沼气用于供热发电。另一途径是通过多效蒸发器脱水把污泥直接合成燃料,如东京都下水道局和茬原株式会式把污泥机械脱水和多效蒸发结合起来,一部分干污泥用来发生蒸发热源的水蒸气,其余部分作燃料,提高了污泥脱水过程的经济性。在日本,这种污泥燃料用于代替水泥厂的燃料,且对水泥质量没有影响。
邓皓等在充分吸收国外 处理技术的基础上,了解到含油污泥和浮渣中含有相当大的热值,其热值虽然低于原油,但与煤和焦炭接近,有着非常可观的利用价值。因此实验将含油污泥干化处理成粉状物与燃煤混烧或直接做成型煤,送入锅炉直接焚烧,该法既实现了脱水后含油污泥的无害化处理,又充分利用了其热能,在解决环境问题的同时又实现了废物的综合利用。
2.2 生物浮选回收原油
李大平等从石油污染物中分离的一组微生物菌株(其中包含一株产气细菌和两株起协助作用的芽孢杆菌)对胜利油田含油污泥进行了生物浮选处理,即利用微生物产气与表面张力改变的生物浮选去除含油污泥中大部分油并将其回收,通过实验获得生物浮选较佳运行参数为:温度40℃,稀释率98%,加菌量3.75%,加糖量0.25%,在该参数运行条件下,原油去除率可达95%以上。使用混合菌株进行生物浮选有利于回收原油中含油量的提高,既有效利用了资源,又减少了对环境的污染,缺点是周期比较长。
2.3 掺重油做乳化剂
扬子石化公司进行了大量试验工作,开发了油泥浮渣掺重油乳化技术,生产出优质乳化燃料油,减少了环境污染,大大提高了油泥浮渣的附加价值。其乳化方法是在浮渣含污油和重油混合加温至50℃后加入乳化剂,搅拌15min后,调入轻质油,经混合器混合过滤,产品即为成品油。原料油的配比为浮渣60%,重油25%,轻质油15%,乳化剂加入量一般控制在0.2%~0.4%。产品的性能:该燃料油热值可达41.87kJ/kg,20℃时流动性能较好,不需要加温可以直接作为喷枪油使用,闪点高于65℃,且使用安全性能较好。采用油泥浮渣加重质油乳化技术,不仅解决了炼油厂处理浮渣的难题,而且可以获得很高的经济效益和社会效益。
2.4 对“三泥”中污油进行处理回收燃料油的研究
蒋培华等对炼油厂“三泥”中污油进行了回收实验。采用破乳、离心、减压蒸馏等方法处理炼油厂“三泥”的污油,并确定了破乳剂,较佳的破乳条件和离心条件。研究结果表明,该工艺不仅脱水效果显著,而且能回收大量燃料油。
2.5 化学热洗-生物处理法
含油污泥经化学热洗工艺处理后,残油率在3%以下,且污泥呈中性,可以比较方便地通过生物处理技术或做型煤填料实现油泥的处置。室内研究发现,利用化学热洗技术处理含油污泥沉淀后水相澄清透明,可多次重复使用,泥相呈灰白色,体积可减少16%。由于蒸发和排泥要带走水分,因此需要不断补充清水(加量为5%~8%),同时系统无废水外排。该技术工艺简单,技术的载体容易设计制造,易于工业化实现。经化学热洗处理后的含油污泥可以通过生物处理实现无害化处置。该工艺处理含油污泥不但可以产生良好的社会效益,而且具有可观的经济效益。
3 结论
综上所述,虽然“三泥”处理研究已久,但是由于其难度大,目前已成为油田、炼化环保领域的突出问题之一。从综合利用的工艺技术现状来看,其处理大部分只停留在堆置、掩埋(或回填)及制砖等较低层次上,缺少具有高附加值的深度处理。目前焚烧工艺仍被 各国认为是污泥处理中的较佳实用技术。在欧洲、美国、日本等 该工艺日渐成熟。它以处理速度快,减量化程度高,能源再利用等突出特点而著称。近年来 各国的环境条件均对废弃物处理所花费的时间和所占的空间提出了更高的要求。因此,从长远观点来看,回收污油、综合利用污泥是实现减量化、无害化和资源化的有效途径。一方面应积极开展含油污泥性质的基础研究,寻找较佳处理含油污泥的方法;另一方面应积极寻求含油污泥多种利用途径,彻底解决其污染问题。