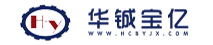
含油污泥主要是石油勘探开发业和石油化工行业生产过程中产生的油泥、油砂,具有产生量大、含油量高、重质油组分高、综合利用方式少、处理难度大等特点。含油污泥的存在对周围的环境质量产生着不良的影响,是目前固体废物处理中一个比较大的难题。
1 含油污泥的特点及处理现状
1.1 含油污泥的来源及特点
目前,油田开发大部分是采用早期注水的方法保持地层压力。随着油田的深度开采,采出油中含水率越来越高。在进行原油脱水中,脱水罐、储油罐、污油罐等底部存在大量含油污泥。同时,在油田、炼油厂的污水处理场(如隔油池底、浮选池、曝气池等)也存在着大量含油污泥。一个日处理20000m³污水的处理厂每日约产生20m³含油污泥。这些污泥成分复杂,属于多相体系,一般由水包油(O/W)、油包水(W/O)以及悬浮固体组成,且乳化充分,黏度较大,固相难以彻底沉降,给污泥处理带来很大的难度。
1.2 含油污泥的危害
(1)含油污泥的存在使回注水中悬浮物含量严重超标,堵塞地层,造成油层吸水能力下降,注水压力不断升高;同时,使水井增注措施(主要是酸化)有效期下降,增加了处理费用和工作量。
(2)为确保注水水质,防止悬浮物在系统中恶性循环,每天被迫外排大量的污水,既造成了水资源浪费,又污染了环境。
(3)由于大颗粒在沉降罐、净化污水罐、污水池中不断沉积,使清罐周期缩短,清出的大量污泥含水率高,无处堆放,污染环境,增加了成本投入。
1.3 含油污泥的处理现状
国内外处理含油污泥的方法一般有:焚烧法、生物处理法、热洗涤法、溶剂萃取法、化学破乳法、固液分离法等。其中焚烧法能耗大、产生二次污染,油资源也没得到回收利用;生物处理法需将含油污泥混以松散剂、肥料和培菌液,经常颤动并自然通风,历时41d才能将97%的石油烃生物降解,同样油资源也没有得到回收利用;溶剂萃取法存在的问题是流程长,工艺复杂,处理费用高,只对含大量难以降解的有机物的含油污泥适用;化学破乳法对乳化严重的含油污泥需另加破乳剂和加热;固液分离对于含油高、污染严重的含油污泥,油回收率低。可见,这些方法由于投资、处理效果及操作成本等原因,未能在国内普及应用。目前,我国含油污泥处理问题一直难以得到有效解决。
2 含油污泥处理技术进展
2.1 调质-机械分离处理技术
调质-机械分离处理技术在国外已经相当成熟,并且在污泥化学调质方面,发展了一系列新型高效的高分子絮凝剂。选用絮凝剂处理含油污泥,可以改变含油污泥颗粒的结构,破坏胶体的稳定性,提高污泥的脱水性能,然后进行机械脱水;机械脱水设备主要有真空过滤脱水机、板框式压滤脱水机、带式压滤脱水机和卧式螺旋卸料离心机。污泥除油工艺是加入破乳剂进行搅拌反应,然后进行三相离心机分离出油、水、泥三相,其中破乳剂的选择、泥水比、搅拌强度、反应温度和时间是影响除油率的重要因素。
文献研究发现,对老化时间较长的含油污泥,选用十二烷基磺酸钠与聚氧乙烯月桂基醚复配作破乳剂,在搅拌强度为400r/min、搅拌时间为40min、搅拌温度为70℃、泥水比为1:10的条件下,脱油效果较好;水溶液可再添加药剂循环使用,不会产生新的污染,多次操作后泥土可达到环保要求直接排放。采用化学破乳加机械三相离心分离技术处理的含油污泥的原油回收率可以达90%以上,分离后油回收利用;分离出的水回用于含油污泥处理,可降低破乳剂的用量,达到重复利用,减少排污量,又降低处理成本的目的。
2.2 高温处理工艺
高温处理工艺是目前国外广泛用于对含油污泥进行无害化处理的一种工艺。含油污泥在绝氧条件下加热到水沸点以上、烃类物质裂解温度以下的温度区间,然后进入分离塔进行闪蒸。在闪蒸塔里轻质烃和水通过蒸发冷凝的方式回收;重质烃和无机物以泥浆的形式从分离塔里取出,进行固液分离后将重质烃回收。由于含油污泥首先被加热到足够高的温度,因此,具备了从含油污泥中分离和回收烃类的条件。在高温下,由于烃类物质的黏度降低,可提高烃类物质从固体无机物中的脱出率。对富含矿物油的含油污泥,可以利用重质矿物油焦化反应的特点,在高温条件下使油泥中的矿物质得到深度的裂解,生成化学性质温度的石油焦和多馏分的轻质油,然后对轻质油进行回收利用。
高温处理与通常的带压过滤、离心作用和细菌处理等工艺相比具有的特点:一是由于高温处理设备与其它工艺的生产设备类似,可利用现有的部分生产设备,经过改造就可以满足要求;二是通常的工艺过程,易挥发有机组分会溢出到大气中,而高温处理工艺可通过冷凝对烃蒸汽加以回收;三是高温处理工艺的整个过程是在一个密闭的环境下进行,减少了外围设施受污染的几率,而且占地面积相对较少。
2.3 溶剂萃取处理技术
溶剂萃取技术被广泛用于去除污泥夹带的油和其他有机物。溶剂萃取技术是利用萃取剂将含油污泥溶解,经搅拌和离心后,大部分有机物和油从污泥中被萃取剂抽提出来;然后回收萃取液进行蒸馏,把溶剂从混合物中分离出来循环使用,回收油则用于回炼。溶剂萃取一般在室温下进行,溶剂比越大萃取效果越好,但溶剂比大萃取设备的负荷较大,能耗相对好大。经萃取后,大多泥渣都能达到BDAT(美国环保局按指定的较佳示范有效技术的处理标准)要求。对含有大量残余重油的泥渣需进行二次萃取,对萃取处理过的泥渣,在320~480℃的高温条件下,用氮气吹扫或者水蒸气携带出其中的油气。经过萃取后的含油污泥,再经蒸馏处理,能有效地脱出含油污泥中的重油,脱油率可达90%以上。
2.4 生物处理技术
目前,生物处理是比较有效的一种含油污泥处理技术,也是今后发展的方向之一。生物处理的主要原理是微生物利用石油烃类作为碳源进行同化降解,使其完全矿化,转变为无害的无机物质(CO2和H2O)的过程。污油微生物降解可以按过程机理分为两个方向:一是向油污染点添加具有高效油污降解能力、自然形成并经选择性分离出的细菌、化肥和一些生物吸附剂;二是曝气,向油污染点投加含氮磷的化肥,刺激污染点微生物群的活性。
采用生物法处理的优点:一是对环境影响小,生物处理是自然过程的强化,其产物是二氧化碳、水和脂肪酸等,不会形成二次污染或导致污染物转移;二是费用低,其费用约为焚烧处理费用的1/4~1/3;三是处理效果好,经过生化处理,污染物残留量可以大幅度降低。其缺点:一是生物法在筛选石油降解菌和菌种培养上存在很大的困难;而是对含油率较高的污泥处理效果不是很好。
3 含油污泥的综合利用
3.1 污泥固化、制砖
污泥固化处理是把水泥、塑料、石膏、水玻璃等凝结剂同污泥加以混合进行固化,或是在污泥中加入硅酸钠、黏土之类的添加剂烧结固化(玻璃化)。污泥中的有害物质被封闭在固化体中不析出污染环境,从而达到稳定化、无害化、减量化的目的。在油田污泥脱水干化后,采用固化处理填埋简单易行;另外,固化物还可以制砖,抗压强度达到普通砖块的标准。其工艺流程:干污泥+黏土→混合→碾磨→干燥砖样→烧结。
3.2 污泥的燃料化
污泥燃料化的途径:一是使污泥厌氧发酵产生沼气用于供热发电。由于炼油厂污泥的碳水化合物、脂肪、蛋白质含量较低;而矿物油、硫化物、酚含量较高,故沼气产率只有2.64m³/m³,城市污泥沼气产率能达到8~15m³/m³;二是通过多效蒸发器脱水把污泥直接合成燃料,一部分干污泥用来发生蒸发热源的蒸汽,其余部分作燃料,提高了污泥脱水过程的经济性。在日本,这种污泥燃料用作水泥厂的燃料,对水泥质量没有影响。
3.3 作为焦化装置的原料
20世纪90年代,许多炼油厂就采用油泥焦化工艺来处理隔油池污泥。该工艺主要是把污泥注入到延迟焦化装置,作为骤冷介质在清焦前对热焦炭进行冷却,使烃类再循环到工艺装置中。在此工艺运行中,没有出现焦炭质量明显下降的现象。目前,采用焦化工艺实施污泥处理有两种技术路线:一是将污泥掺入焦化进料,处理炼油厂污泥;二是将污泥作为焦化急冷液,处理炼油厂污泥。在采用掺入焦化进料方式处理污泥时,还可分为从焦化塔底进料和从塔顶进料两种。
3.4 污泥回灌调剖技术
含油污泥回灌调剖技术是利用含油污泥与地层的良好配伍性,用含油污泥中的泥组分、油组分,加入适量添加剂,不仅能悬浮其中的固体颗粒和延长悬浮时间,还能有效地提高封堵强度,使油组分分散均匀,形成均一、稳定的乳状液。在油田注水井调剖中,由含油污泥配制成的乳化悬浮液调剖剂,到达地层一定深度后,受地层水冲释及地层岩石的吸附作用,乳化悬浮体系分解;其中的泥质吸附胶沥质和蜡质,并通过它们黏联聚集形成较大粒径的团粒结构,沉降在大孔道中,使大孔道通径变小,封堵高渗透层带。迫使注入水改变渗流方向,提高注入水波及体积。该调剖剂与其他的化学调剖剂相比,具有抗盐、抗高温、抗剪切、性能优异和无风险注入等特点,便于大剂量调剖挤注,不受矿化度、温度影响,有效期长,可广泛用于注水井的调水增油挖潜。
污泥回灌调剖技术既解决了污水处理系统污泥大量淤积影响水质的问题,又解决了污泥的出路及二次污染问题,还能确保注入水质,增油效果显著。污泥回灌调剖技术与传统治理措施相比,经济效益和社会效益显著。该技术已在华北油田、江汉油田等地得到应用,并取得良好的效果,具有很好的发展潜力。