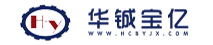
含油污泥是石油勘探开发、运输、炼制及含油污水处理工程中所产生的含油固体废弃物,其中主要是石油勘探与其化工生产过程中产生的油泥、油砂,具有产生量大、含油量高、重质油组分高、综合利用方式少、处理难度大等特点。
含油污泥中污染物质通常分为以下4类:一是以铜、铬、汞等重金属与盐类为主的无机污染物;二是大量共生于污泥中的有害微生物,多为病原菌;三是以多氯联苯(PCBs)、多环芳烃(PAHs)、酚类、苯系物等为主的有机污染物;四是少量的放射性元素。油田生产过程中含油污泥产生量大,若不及时加以处理整治,将势必对周围土壤、水体、空气及其生物圈造成污染。目前含油污泥作为一种常见的暴露污染源,已被 列为重要污染废物,正逐渐引起国内外油田的广泛关注。虽然我国已在各油田推行含油污泥处理技术,积极保护油田环境,但对含油污泥的处理还 于原油的简单回收,剩余污泥尚未得到无害化处理要求。所以,对于含油污泥的有效处理一直是油田环境保护与可持续发展的重要问题之一。当前,我国油田对含油污泥的处理与利用尚处于中试阶段,亟待建立含油污泥有效处理工艺流程及其可行性方案,并基于油田环境、污泥种类不同,衍生出结合实际的具体处理措施。本文主要阐述了国内外处理含油污泥的现状,类比解析了其典型工艺与具体措施,并结合实际分析,探讨了冀东油田含油污泥处理的现状与发展,展望了油田含油污泥处理的发展方向和前景。
1 含油污泥处理技术现状
含油污泥是由油包水(W/O)、水包油(O/W)乳化液及悬浮固体等成分组成的稳定悬浮乳状胶体,主要来源于原油开采、油气集输、炼油化工厂污水处理等生产过程。由于含油污泥成分和物化性状受污水水质、处理工艺、加入药剂等诸多因素影响,差异性较大,处理难度大,各种处理方法在实际应用中皆存在一些问题。但从目前整体技术发展趋势来看,含油污泥的处理方法主要分为减量化、稳定化和资源化三个研究方向,并在各个研究领域均取得了一定的进展和成果。
1.1 减量化处理措施
对于含油污泥的处理,首先可考虑通过易于操作、成本较低的物理化学方法,将污泥中大量颗粒物(>0.1mm)分离出来,从而实现污染物的减量化。
1.1.1 机械脱水工艺
机械脱水工艺是将经过调质、筛分、分选、倾析等各种预处理后的均质液态含油污泥,再进行高速离心,从而实现油、水、泥的三相分离。然后根据不同油泥砂实际性状,采取生物技术和固化技术辅助处理,达到含油污泥减量化、无害化要求。机械脱水工艺过程主要如下:首先选用絮凝剂改变含油污泥颗粒的物理结构,破坏胶体的稳定性,提高污泥的脱水性能;然后通过真空过滤脱水机、带式压滤脱水机、高速离心机等机械脱水设备进行脱水操作。
机械脱水工艺中重要环节为含油污泥的调质技术与不同处理阶段高速离心机的操作技术。其中,调质-机械分离预处理技术体系中,考虑到普通高分子絮凝剂使用后不易降解,极易造成对环境的二次污染,因此选用无毒无害、适用范围广的高效有机高分子絮凝剂是首要考虑的关键因素之一。目前,已有研究报道,通过利用活性污泥中微生物分泌的高分子絮凝剂,结合使用有机絮凝剂可显著改善机械离心脱水效果,并可节省90%左右的高分子絮凝剂使用量。
1.1.2 焚烧处理
焚烧处理多数集中在污水处理场含油污泥的处理。含油污泥焚烧前一般须经过污泥脱水,首先用泵将含油污泥送入污泥浓缩罐中,升温至60℃左右,并投加絮凝剂,再经搅拌、重力沉降后,进行分层切水。经过浓缩预处理后的污泥,可经过设备脱水、干燥等工艺,制成泥饼送至焚烧炉,800~850℃焚烧30min,产生的剩余灰渣进一步处理。焚烧处理对含油污泥的适应能力较强,污泥减量化效果明显,多种有害物在高温条件下几乎被完全清除。但焚烧的燃料费用昂贵,处理过程中易产生有害气体释放到大气中,造成对环境的二次污染。另外,鉴于焚烧处理技术 于中小规模的含油污泥处理,且需要配置除尘、气体洗涤等设备,我国大多数油田关于焚烧处理的应用还不是很广泛。
1.2 稳定化处理措施
1.2.1 固化处理
固化处理是指采用物理或化学方法将含油污泥固化或包容在惰性固化基质的一种无害化处理过程,使污泥废弃物具有化学稳定性和密封性,以便于运输、利用或处理。该方法适用于采油污泥及含有NaCl、CaCl2等盐类较高的含油污泥的处理,特别是对于含油量较低的污泥一般可优先考虑采用固化措施。目前固化基质以水泥固化剂为主,李利民等通过对长庆油田采油三厂含油污泥性质和矿物组成的分析,发现合适配比的固化处理配方(污泥/固化剂/促凝剂B)可有效地对含油污泥进行固化处理,固化物的抗压强度达到3MPa,其浸出液的各项指标均达到 污水综合排放标准,满足安全土地填埋处理的要求。
含油污泥的固化处理效率高,处理后的污泥具有资源化利用的优势。针对不同油田含油污泥的性质各有差异,如何开发、选用高效的固化剂,保证固化产品环境安全性,将是今后固化处理研究的主要方向。
1.2.2 生物处理
生物处理是指微生物利用石油烃类作为主要碳源进行同化降解,使其完全矿化,转变为无害的无机物质(CO2和H2O)的过程。在生物处理过程中,影响石油烃类降解的主要因素有:污染物的化学生物特征、微生物生长环境(如温度、营养物质、氧气浓度、pH、含水率等)、微生物自身特征(微生物的种类、菌种的数量)等。微生物对底物的降解过程,是整个微生物区系对环境中各种可利用的底物综合作用的结果,不同的微生物对含油污泥中的各种烃类成分的降解能力也各有差异,或者在降解中发挥的作用也并不一致。因此,接种混合微生物菌株可能较单一菌种能有利于提高生物处理的效率。潘峰等利用筛选得到的10株酵母菌组成复合酵母菌对模拟含油污泥进行处理,研究发现复合酵母菌在反应速率和除油效率方面皆优于活性污泥,且原有组分中的脂肪烃部分于处理8d后基本被完全降解。陈荣灿等由新疆克拉玛依油田准东采油厂作业污水池污泥中分离筛选出5株高效降解石油菌,构建复合菌对污水池底含油污泥进行降解性研究,结果发现复合菌体经过10d的适应期后,即可显著降解污泥中的油,20d内对含油在5%~26.7%的污泥降解率达到20.5%~48.5%。
生物处理是自然本质过程的强化,其产物是二氧化碳、水和脂肪酸等无害物质,不会造成环境的二次污染或形成污染物的潜移,而且生物处理费用低,处理效果优越,将成为今后含油污泥多元化处理的主要发展方向之一。
1.3 资源化措施
1.3.1 溶剂萃取处理
溶剂萃取处理是利用萃取剂将含油污泥溶解,经搅拌、离心后,通过萃取剂将大部分有机物和油从污泥中抽提出来,回收油经过回炼后可作为燃料油使用,萃取剂经回收蒸馏可从混合物中分离出来并循环使用。在实际工艺运行中,萃取技术还需与其他技术联合使用,才可取得较高的油分回收率。如将萃取剂和低频声波相结合,或与加热、溶解相结合的方法处理含油污泥时,均可得到很好的处理效果;将萃取剂与稀释、添加抗絮凝的分散剂、机械剂分离方法相结合处理含油污泥,可得到98%的油回收率。
1.3.2 热解处理
含油污泥热解是指在缺氧条件下,有机质受热分解为低碳烃类燃气、液态燃料油和固体碳等。热解反应与加热速率、加热温度以及原料组成有关。王万福等通过分析溶剂萃取、热化学洗油、热解等6种污泥资源化技术的利用程度、二次污染和适用范围及特点,对比发现含油污泥热解处理具有较好的油气回收和残渣再生利用价值,是值得推广的含油污泥资源化处理技术。
1.3.3 焦化处理
含油污泥焦化处理技术是利用重质油或渣油焦化反应机理,其反应是烃类物质的热转化过程,即重质油或渣油的高温裂解和热缩合。目前采用焦化工艺实施含油污泥处理主要分为两个方向:一是将油田产生的含油污泥脱水预处理后,再与匹配的催化剂混合进入焦化反应釜进行焦化反应,经过一系列的裂解和缩合反应,生成液相油品、不凝气和焦炭产品。二是由于含油污泥中添加适量的强度添加剂和炭化添加剂,通过控制焦化反应条件可生产出净化效果较好的含碳吸附剂。周建军等通过分析天津大港油田联合站含油污泥焦化处理的影响因素,确定了焦化处理较为理想的反应参数为:反应温度490℃,反应时间为60min,氮气吹扫量90mL/min,加热速率为4℃/min。该反应条件下含油污泥的液相油品回收率高于80%,反应转化率大于99.9%,经焦化处理后的废渣含油率低于3%,达到了农用污泥排放标准,实现了达标排放和回收资源的目的。
1.3.4 化学热洗处理
化学热洗法是利用热碱水溶液反复洗涤含油污泥,洗涤过程中常加入水、化学药剂、油泥等物质,再经加热、混合搅拌后静置沉淀,通过气浮实现固液分离,分离出的水相中添加清水和洗涤剂进行重复洗涤。当污泥中含油率降至3%后,可进一步采取固化填埋或焚烧发电。该工艺在发达 已得到广泛的应用,但我国油田单独采用化学热洗处理工艺的还较少。
1.3.5 调剖技术
含油污泥调剖技术是利用含油污泥产于地层以及与地层有良好的配伍性的有利因素,于含油污泥中的泥组分、油组分中加入适量的悬浮剂、增粘剂、分散剂,按一定比例混合制成悬浮液,通过化学处理将其转变为活性稠化含油污泥调剖剂。该方法能较好地解决含油污泥污染与实际利用问题,在河南油田、华北油田、江汉油田等多个油田得到了广泛的实验和应用,具有性能稳定、封堵能力强、价格低廉等优点。李丹梅等对河南油田含油污泥进行化学药剂处理,使其转变为调剖剂,可有效地封堵高渗透地层,提高注入水波及体积。王亚等基于河南油田含油污泥组分和粒度分析结果,筛选出合适的悬浮剂、固化剂,并结合不同油藏区块地层适应性研究结果,开发了含油污泥调剖堵剂系列化堵剂复配体系,并对其进行室内评价,经河南油田54井次现场试用证实封堵效果良好。
虽然含油污泥乳化液的活性较强,经过化学处理后的含油活性污泥调剖剂可以起到封堵高渗透层带的作用,但是,由于含油污泥组分、活性等特征和各调剖区块油藏特征的不同,对含油污泥调剖剂的配方要求差异也很大,仍需通过不断实验优选出适合本油田生产情况的含油污泥调剖剂复配体系。
1.4 联合调理技术
目前含油污泥处理多数基于单独的化学、物理或微生物等单一处理技术,随着各项处理技术的不断成熟,近年来出现了联合调理技术,较单一处理措施可获得更加理想的效果。例如,化学热洗-生物处理工艺具有能量消耗低、费用不高等特点,是我国目前研究较多的含油污泥处理方法。它将含油污泥中油、水、泥三相分离,回收大部分油品,可实现资源回收,同时通过生物稳定法处理剩余污泥,达到无害化处理效果。赵虎仁等采用化学热洗-生物处理工艺对石油炼油厂的含油污泥处理发现,通过化学热洗单一处理可将含油率为29%的污泥洗涤至残油量2.7%,污油回收率达到92.2%,体积减少16%。洗涤后的污泥再进行生物处理,经过好氧堆肥40d后,石油类物质去除率可达95%。
2 冀东油田含油污泥处理的现状及探讨
冀东油田位于渤海湾北部沿海,周围河流纵横分布,渔业发达,环境极为敏感,环保责任重大。近年来,随着油田对环保工作要求的提高和环保意识的增强,冀东油田不断加大污水处理的治理力度,保证了外排污水长期达到《污水综合排放标准》中的一级排放标准。但是,在生产过程中也伴随产生了一部分含油污泥,主要包括原油储罐罐底积累的油泥、污水罐罐底的絮凝物以及生化处理产生的活性污泥。因此,油田开始逐渐摸索和寻找含油污泥处理的有效方法。
通过对目前国内外含油污泥处理技术以及油田含油污泥处置现状的分析和总结,认为联合调理技术方法将会是今后含油污泥处理的主要攻关方向,可按照“减量化与再利用相结合”的思路,根据油田油藏特点、污泥产生量及污泥性质等特征参数,有机融合并不断优化含油污泥调剖、溶剂萃取、热解及固化等处理技术。一方面可将部分含油污泥进行化学处理,制成含油污泥调剖复配体系,在达到污泥减量化的同时,还可提高作业区井场的封堵和注水效果。另一方面,剩余大部分污泥可先通过溶剂萃取处理,将有机物和油回收作为燃料使用,或通过热解处理将污泥中的有机物分解为低碳烃类燃气、液态燃料油等并回收,剩余物可通过固化处理或经浓缩、干化后制成建筑材料或回填。
3 含油污泥处理技术的发展前景与展望
目前,国内油田对于含油污泥的处理和再利用仍处于实验研究和中试阶段,尚缺乏完善可靠的技术、工艺以及典型示范工程。大多数研究主要针对含油污泥中原油的回收,有关剩余含油污泥的净化处理的研究还处于起步阶段。含油污泥的处理措施众多,每种方法都有其自身的优缺点和使用范围。含油污泥直接填埋或将含油污泥脱水制成泥饼等简单处理措施是我国多数油田采用的主要方法,但这种方法带来了一定程度上的经济损失和环境污染。以回收原油为目的处理含油污泥的各种物理化学方法,主要适用于含油量较高的污泥,由于处理过程中需要额外添加成本昂贵的化学药剂以及匹配的处理设施,处理过程复杂、成本较高,还会引起废水、废渣等二次污染问题,需要进一步处理利用。生物处理措施虽然节约能源、工艺投资少、运行费用较低,但是对于生物反应器中废渣的处理较为复杂。随着各项处理技术的日臻完善,物理-化学、化学-生物等联合调理措施将是今后研究的主要方向,同时鉴于含油污泥中成分复杂,应及时分级、分阶段处理,从而达到含油污泥的无害化处理和资源化应用。