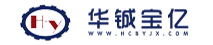
目前,我国污泥处理处置技术主要有:稳定填埋、干化焚烧+填埋、干化+土地利用、厌氧消化/好氧堆肥+土地利用、干化+热解、烧制+建筑材料。实际运行中,污泥处理过程基本实现了减量化,但处置端未实现真正的稳定化、无害化、资源化,存在严重的二次污染风险。本项目采用的“连续深度脱水耦合低温干化”工艺,将污泥初步机械脱水之后经热处理法进行干化,可将污泥含水率降低至20%~30%,减量化明显且产物热值高,大大增加了污泥终端处置出路。
1 泥量确定
截至2019年底,山东某污水处理厂总设计处理规模为15万m³/d,实际处理规模达到近20万m³/d,日均产泥量已突破220t。依照远期预测,至2030年污水总量将达到35~40万m³/d,污泥量将达到350~470t/d(含水率80%)。考虑到生活污水增加及出水水质提标的可能性,污泥量会有一定量的增加,因此污泥处置工程设计规模按600t/d(含水率80%)分期建设,其中一期工程污泥处置规模为300t/d,二期污泥处置规模扩建至600t/d。
2 技术路线确定
根据《山东污泥处理处置规划》,本项目污泥的处置出路为焚烧后用作建材或填埋。污泥焚烧又可分为污泥单独焚烧和协同处置2种方式。协同处置方式是通过污泥干化工艺将含水率80%的污泥降至30%后运至电厂或垃圾焚烧厂进行焚烧,是投资较为经济的污泥处置方式。污泥协同处置可与电厂或垃圾焚烧厂公用烟气、飞灰等处理装置,因此所需投资运行成本大幅降低。自建污泥焚烧系统相对独立,系统投资高,但焚烧过程中产生的烟气含有臭气、氮氧化物、二恶英等污染物,全部妥善处理的费用很高。两者相比,本项目选定协同焚烧。
污泥燃烧过程中,污泥带入炉膛内的水分都以水蒸气的形态排出,蒸汽以汽化潜热的形式带走了燃料中的能量。若直接燃烧含水率80%的污泥,污泥中的水分会吸收大量的热,对锅炉燃烧的稳定性及锅炉的设备材质要求较高。因此大规模焚烧污泥必须要降低污泥的含水率。考虑到节省投资和运行费用,本项目先通过深度脱水对污泥进行初步减量后再进行干化处理,达到污泥较大程度减量化目的的同时,较大限度地降低了项目的投资和运行费用。因此,本项目技术路线确定为“连续深度脱水耦合低温干化”后运至电厂协同焚烧。
3 工艺流程
含水率为80%的污泥通过污水厂的污泥运输车送入处理厂内的湿污泥缓存仓,为防止臭气扩散,料仓车间设置电动卷帘门,料仓做密闭加盖,卷帘门和料仓盖在卸泥时打开,卸泥后关闭,且车间和料仓内做负压臭气收集。料仓内的污泥经输送机输送至连续深度脱水设备经处理后污泥含水率降至70%,然后进入低温干化系统,除湿干化后污泥含水率降至30%,干化后污泥运至发电厂掺烧,系统内的废水回到污水处理厂进行处理。
4 工程设计
4.1 厂区布局
本项目工程占地约17000㎡,一期污泥干化车间、除臭装置布置在厂区东侧,一、二期共用变配电室布置在厂区东南角,在厂区西侧预留二期污泥干化车间、除臭装置安装位置。
按照工艺设计,本期污泥干化单体主要有污泥脱水干化车间(1座)、生物滤池除臭设备基础(1座)、高压变电室(1座)、地磅设备基础(1座)、门卫(1座)。
污泥干化厂厂区主要建筑物结构类型为框架结构,现浇钢筋混凝土楼板。一期污泥干化车间厂房地上建筑面积3756㎡,预留二期污泥干化车间厂房面积2188㎡。
4.2 湿污泥缓存料仓
该项目使用4套容积为60m³的滑架料仓储存和输送含水率80%的市政污泥。料仓采为矩形平底结构、重力卸料的高架料斗结构型式,储存的污泥仅靠重力自动下落。仓底配有滑架装置,将污泥纳入双轴螺旋输送机将污泥输出。
自卸式污泥运输车运来的污泥直接倒入滑架料仓内,料仓顶部设有液压驱动的活动仓门,活动仓门下方安装钢格栅板,防止大块的硬物进入料仓内。运泥车卸料前,先打开该活动门,卸料完毕后,关闭该活动仓门。每套料仓底部设置1套滑架装置和1个出料口,每个出料口都有液动插板阀和双轴螺旋输送机,滑架装置由液压缸驱动,于仓底往复运动。
4.3 药剂投加设备
(1)干粉自动投加设备(固化剂投加量200~1000kg/h)。污泥改性剂自动投加系统是将一定量的改性粉剂存放在1个特制的立式圆形储罐内,粉料入仓时产生的粉尘由微孔收尘器收尘,吸附在微孔管表面的粉尘由振打器激振下落回粉料仓。存储的粉料经振荡器疏松均匀下料,变频调速给料机定量给料,粉状物料经由管链输送机输送至4套称量料斗和定量投加装置,分别为4套污泥深度脱水带式机提供药剂。
(2)改性剂溶解投加设备(流量范围不大于500L/h)。整套装置包括改性剂拆包机、定量加药器、溶解槽及搅拌器、流量计、计量泵、转运泵及内部管道阀门、液位传感器和控制箱。
(3)一体化污泥改性设备(处理能力4~5m³/h)。污泥药剂混合系统主要设备为一体化污泥改性装置,其主要工作方式为利用搅拌剪切污泥,并同时将污泥与污泥药剂混合向前推送避免混合物料在筒体后部堆积,达到连续均匀混合的目的。该设备主要用于待脱水污泥与改性药剂的混合搅拌,经过混合搅拌处理后的污泥进入带式污泥深度脱水设备进行压榨脱水。
4.4 污泥深度脱水带式机
含水率为80%的污泥与污泥改性剂充分混合、反应、调质后,经高压压榨脱水至含水率70%左右。
污泥深度脱水带式机是由上下2条拉紧的滤带夹带着污泥层,从一连串有规律排列的辊压筒中呈S型经过,依靠滤带本身的张力形成对污泥的压榨和剪切力,把污泥层中的毛细水挤压出来,获得含固率较高的泥饼,从而实现污泥的深度脱水。污泥深度脱水带式机含有低压、中压、高压、超高压4个压滤区,压滤动作均由气动元件自动控制,根据污泥性质及处理要求变频调节。
本项目配置4台(3用1备)污泥深度脱水带式机,单台处理能力4.0~5.0t/h。
4.5 低温干化系统
经污泥深度脱水带式机脱水后的含水率70%的污泥,进入低温干化系统进一步干化到含水率30%,再经输送系统输送至干泥料仓储存。
低温干化技术利用除湿热泵对污泥采用热风循环冷凝除湿烘干,由于污泥水份汽化潜热等于除湿热泵水蒸汽冷凝潜热,干化过程无需接入外界热量,能源消耗为压缩机输入的电耗。除湿热泵烘干与传统热风干燥的区别在于空气循环方式不同,干燥室空气降湿的方式也不同。除湿热泵烘干时空气在干燥室与除湿干燥机间进行闭式循环,不排放废热;传统热风干燥是利用热源对空气进行加热,同时将吸湿后空气排放的开式系统,排放废热,能源利用率低。
本项目配置4套低温干化带式机,单台设备去水量1600kg/h。
4.6 除臭系统
除臭系统主要功能是收集和处理部分产生臭味区域的臭气,如污泥料仓、污泥深度脱水干化系统等区域,对设备点源除臭和干化车间空间除臭。
臭气经臭气收集系统有效收集后,平流进入洗涤池,完成臭气中水溶性及酸性物质的吸收、除尘、加湿和调节pH值的预处理,然后进入生物滤池过滤区,污染物从气相中转移到生物膜表面,在微生物的氧化分解下去除。
各构筑物臭气收集原则上按有人活动与否分为2种形式,结合工程实际经验,拟定设备和密封通道换气频率为8次/h,确定项目的除臭风量为45000m³/h。
5 效益分析
本项目设计规模为300t/d(含水率80%),采用“连续深度脱水耦合低温干化”工艺,将污泥含水率从80%降至30%后外运至电厂协同焚烧。污泥由300t/d减量至96t/d,减量化明显,大幅降低了污泥处置费用和处置难度。同时通过增加深度脱水段对低温干化工艺进行优化,可降低电耗40%以上,降低运行成本20%以上。
6 结论
污泥处置并没有较优方式,需要因地制宜地制定方案,是一个系统性的工程。本项目创新的“连续深度脱水耦合低温干化”工艺减量化明显,产物热值高,可进行协同焚烧或用于园林绿化、土壤改良基质土制备原料等多种出路。
本工艺路线是对低温干化工艺的优化,具有以下优势:
(1)经济性。增加深度脱水段对污泥进行初步减量后再进行低温干化处理,在满足污泥较大程度减量化的同时,通过增加投资和运行成本均较低的机械脱水段进行二次脱水,降低低温干化段的投资和能耗,从而降低系统整体的投资和运行成本。
(2)安全性。该工艺运行温度较低,干化阶段温度仅为70℃,并且操作环境中无粉尘产生,无爆炸风险,具备良好的安全性。
(3)灵活性。干化热源可采用电或者余热,技术适用性广。
本项目的成功实施对城镇污水处理厂污泥处理处置工艺的选择具有一定的示范意义。