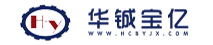
1 含油污泥的性质与危害
含油污泥成分极其复杂,主要由乳化油、水、固体悬浮物等混合组成,其成分与地质条件、生产技术、污水处理技术、污水水质、加药种类、排污方式以及管理操作水平有关。含油污泥的比阻比一般污泥大40倍,其可压缩性系数大20倍,属难过滤性污泥,又由于其颗粒细小,呈絮凝体状,含水量高,体积庞大,因此不易实现油-水-泥的三相分离。我国大部分油田含油污泥的含水率一般为70%~99%,油、盐成分含量较高,且含有重金属和其它有害杂质;炼油厂污泥还含有大量苯系物、酚类、芘、蒽等有毒物质。
含油污泥直接外排会占用大量土地,其含有的有毒物质会污染水、土壤和空气,恶化生态环境;直接用于回注和在污水处理系统循环时,会造成注水水质下降和污水处理系统的运行条件恶化,对生产造成不可预计的损失;同时大量石油资源被浪费。含油污泥已被列入《 危险废物目录》中的含油废物类,《 清洁生产促进法》和《固体废物环境污染防治法》也要求必须对含油污泥进行无害化处理。因此,无论是从环境保护、维护正常生产还是从回收能源的角度出发,都必须对含油污泥进行无害化、资源化处理。
2 含油污泥处理技术
为实现含油污泥的彻底处理和资源利用,国内外进行了大量研究并取得一定进展。含油污泥主要处理技术有:调质-机械分离、生物处理、固化处理、焚烧、填埋与干化、回收油、调剖、生产建材、焦化法生产除油吸附剂、用于橡胶制品等。填埋与干化由于处理易产生二次污染和浪费了大量有用资源而逐渐被淘汰,目前较受重视的是调质-机械脱水、生物处理、固化处理和综合利用技术。
2.1 含油污泥无害化处理技术
2.1.1 含油污泥调质-机械分离技术
浓缩、化学调质(即调质)、脱水是含油污泥处理系统必不可少的三个环节。高含水量的含油污泥不能直接进行机械脱水操作,必须 行调质;通过调质-机械分离,使含油污泥实现油-水-泥的三相分离。污泥脱水过程实际上是污泥的悬浮粒子群和水的相对运动,而污泥的调质则是通过一定手段调整固体粒子群的性状和排列状态,使之适合不同脱水条件的预处理操作。
调质要根据含油污泥的性质、脱水机械的性能和滤饼的后续处理方法等因素选择合适的调节剂。研究发现,无机絮凝剂中,PAC的效果较好;有机絮凝剂中,阳离子型聚丙烯酰(PAM)由于具有正电荷中和与吸附架桥的双重作用,絮凝效果比非离子型聚丙烯酰胺(CPAM)好。有机和无机絮凝剂都有投加量适度的问题,投加量过大会使污泥比阻升高,水分难以去除。经絮凝处理的含油污泥,加入合适的助滤剂CaO可降低污泥的比阻。
脱水的关键是通过解吸附和破乳来降低含油污泥中油的含量。因此,含油污泥的调质,除投加混凝剂、助凝剂外,还必须投加表面活性剂、破乳剂、pH调节剂等,同时辅以加热等强化手段,以改善污泥的脱水性能。Bock等、Srivatsa等、Corti等分别发明了通过调质-机械脱水工艺回收油的专利技术:通过投加表面活性剂、稀释剂(葵烷等)、电解质(NaCl溶液)或破乳剂(阴离子或非离子)、润湿剂、pH值调节剂等,并辅以加热减粘(50℃以上)等调质手段,实现了油-水-泥三相分离。
机械脱水主要技术有真空过滤、加压过滤、滚压过滤和离心过滤,其原理是在过滤介质两面产生压差,使固体颗粒被截留而水分通过。目前国内主要使用板框压滤机和带式过滤机,而国外广泛使用的是带式压滤机和卧式螺旋卸料沉降离心机。集污泥浓缩、油水分离于一体的三相卧螺沉降离心机是今后含油污泥处理的发展方向。带式压滤机在使用中取得较好的脱水效果,调质污泥依次经过重力区、楔形区、中压区和高压区,先在重力区脱除部分水,接着在楔形区脱去大部分水,进入中压区和高压区,脱除油和水,脱水后的泥饼外运。
调质-机械分离技术是一种比较成熟的含油污泥处理技术,油的回收率较高。由于不同地区含油污泥成分不同,需要药剂和脱水机械相适应,同时要优化药剂的种类、投加数量及脱水机械的运行参数。
2.1.2 生物处理技术
对于经过石油提取处理的剩余含油污泥,部分微生物可以将其中的石油和有机物降解,转化成无害的CO2、H2O等,同时增加土壤腐殖质含量,其处理方式包括堆肥处理法、土壤耕作法、微生物降解等。
微生物对含油污泥中的石油和有机物有很强的降解能力。Mishra等采用原位生物修复技术研究了微生物对炼油厂含油污泥的处理能力。加入培养好的菌种与营养物质55d和120d后,原来含油量高(99.2g/kg)的A区污泥中含油率分别下降83.5%和90.2%。许增德等进行的微生物处理技术研究表明,使用培育的假单胞菌和芽孢杆菌对含油污泥经厌氧处理再进行好氧脱油处理,含油23000mg/kg的含油污泥4h内脱油率可达53.4%;添加混合菌可显著提高堆肥效果,且时间越长,油去除率越高,当处理时间为60d时,含油量降至4100mg/kg,接近《农用污泥中污染物控制标准》(GB4284-84)中规定的含油量不高于3000mg/kg的标准值。
土壤耕作法自1954年以来被用于炼油厂含油污泥处理,并于20世纪70年代成为美国石油公司主要的含油污泥处理技术之一,1984年公布的《资源修复法》使该方法的使用受到限制,但该方法目前仍是热带干旱地区含油污泥的主要处理技术。研究表明,在炎热干旱条件下,影响土壤耕作法处理效果的因素有温度、湿度、微生物的数量和组成、营养物质和耕作条件等,其中耕作条件和土壤中营养物质的多少是影响生物降解效果的关键因素。耕作条件包括合适的耕作方法、次数和深度;营养物质能增加微生物活性,提高直链烷烃的降解效果,但营养物质过多会引起土地板结;土壤中过多的水中含有大量氧,会降低生物降解效率,水分过少则会降低微生物的活性,适宜的含水率为1.6%~4.9%;夏季温度高导致土壤中水分减少使微生物数量降低,较冷的季节微生物数量较多,但活性有所降低。研究同时显示,生物降解并不是土地耕作法中碳氢化合物降解的 机理,风化作用在降解中起重要作用。
从炼油废水处理厂得到的活性污泥中不仅含有可用于生物降解的微生物,而且可作为生物降解中营养物的来源(主要是N源),将其添加到含油污泥中会显著提高碳氢化合物的去除率,而从城市污水处理厂中得到的污泥则无法用作添加剂处理含油污泥。活性污泥中的微生物可有效降解含油污泥中的直链烷烃;在含油污泥中添加NH4NO3或经高温杀菌处理的污泥滤出液能有效降解含油污泥中的多环芳烃,但不能有效去除烷烃,说明活性污泥中对多环芳烃起主要作用的是其中的NO3-离子而不是微生物。该方法相对于在含油污泥中添加无机营养物成本较低。
生物处理技术操作方便,作用持久,无二次污染(产物为CO2和H2O),处理成本低,已在国外得到广泛的商业化应用,并将成为未来含油污泥无害化处理的主要方式之一。但目前仍存在着选择合适的菌种困难,处理周期长,对环烷烃、芳烃、杂环类处理效果差,对高含油污泥难适应等问题。
2.1.3 含油污泥固化技术
固化技术是在含油污泥中加入一定组分的固化剂,使其发生一些稳定的、不可逆的物理化学反应,固化其中的部分水分和有毒物质,并使其有一定强度,以便堆放、储存和后续处理。理想的固化产物应该具有良好的机械性能和抗浸透、抗浸出、抗干湿、抗冻、抗融等特性。固化剂的作用是将含油污泥中的有害物质(污油、有害气体等)固定或封闭在惰性物质中,大幅降低有害物质的渗透性和溶出率。固化剂分有机固化剂和无机固化剂。有机固化剂包括脲醛树脂、聚酯、环氧乙烷、丙烯酰胺凝胶体、聚丁二烯等。目前使用较多的是以水硬材料为主体的无机固化剂,如波特兰水泥、波特兰水泥混合物、磷石膏、河沙等。
含油污泥固化实验表明,污泥、固化剂、促凝剂之比为4:1:0.01时,一般在1d内达到一定的强度,3d后基本较硬,10d后基本达到极大硬度;污泥固化后,矿化度下降了46%,含油量从未固化时的40000mg/L降至0.4mg/L,硫化物含量仅为0.4mg/L,将固化产物作为建筑材料和进行填埋都可满足环保要求。
水泥固化实验研究表明,水泥的添加量越多、固化时间越长,固化物硬度越高,但增容比较大,可通过减少水泥的添加量控制增容比和pH。固化浸出液测试结果表明,除pH稍大于 标准外,浸出液中石油物质、悬浮物、COD含量都能满足 工业废水排放标准的要求。
固化处理是一种较为理想的含油污泥无害化、减量化处理技术,近年来对该技术的研究受到重视。但固化后的污泥堆放占用了大面积土地,造成了资金的浪费,且加入有机固化剂可能带来二次污染。因此,只有将固化后的污泥进行资源再利用,才能从根本上解决污染问题。
2.1.4 焚烧处理技术
国内炼油厂通常采用焚烧技术处理含油污泥。法国、德国的石化企业将含油污泥焚烧后的灰渣用于修路或填埋,焚烧产生的热量用于供热发电。常用的焚烧炉有固定床式、流化床式、回转流化床式、耙式、窖式和方箱式等。
含油污泥采用流化床式焚烧炉进行焚烧后,燃烧率[CO2/(CO2+CO)]可达98.5%;去除率可达99%[(输入质量-输出质量)/输入质量];固体残留物中的重金属含量很低,可直接填埋处理。在茂福炉中进行的含油污泥焚烧实验表明,干化后的污泥通过喷射天然气可进行彻底焚烧,焚烧炉的温度、通风情况以及是否搅拌对污泥在炉内的停留时间有较大影响,含水率对停留时间的影响不大。
焚烧技术适用于各种成分的含油污泥,是一种较好的污泥无害化和减量化处理方式。但该方法成本和操作费用较高,含油污泥中的大量石油资源被浪费,焚烧产生的热量不能充分利用,且焚烧产生的SO2、CO及粉尘会对空气造成严重污染。
2.2 含油污泥资源化利用技术
2.2.1 回收油技术
在含油污泥回收油方面,目前主要技术有:溶剂萃取法、热洗涤法、热处理法、回收油加热法、化学破乳法和固液分离法等。
(1)溶剂萃取法。
溶剂萃取法被广泛应用于回收污油,其特点是能回收大部分石油类物质,溶剂可循环使用。超临界萃取技术是一种正在研究中的新技术,它将常温常压下的气态物质经高压达到液态用作萃取剂,其溶解能力大、易于回收循环,常用的超临界萃取剂有丙烷、三乙胺、重整油和临界液态CO2等。但是由于萃取剂价格较高,且处理过程中有一定的损失,较高的成本阻碍了该技术的应用。目前溶剂萃取法的关键在于开发性价比合理的萃取剂。
(2)热处理技术
热处理技术是利用全封闭式固控设备循环系统,将含油污泥加热到一定温度,使烃类物质解吸并回收烃类物质的方法,处理后的剩余泥渣能达到BDAT(美国环保局按指定的示范有效技术的处理标准)的要去。该技术包括高温处理技术和氧化热处理技术。
在高温处理工艺中加入合适的催化剂和添加剂可缩短反应时间,降低反应温度,提高液体产品质量,减少固体残渣含量。Shie等用廉价的铁化合物和铝化合物代替普通催化剂,对含油污泥高温催化降解进行了研究。实验表明,Fe2O3和Fe2(SO4)3·nH2O可提高油的产量;加入添加剂后,650~710K之间的反应速度提高。对炼油厂含油污泥进行的催化热解试验表明,以Na2CO3为催化剂、CH2Cl2为萃取剂,产油率随温度的升高而增加。含油污泥经高温处理后得到的气态产物(298K)包括CO2(50.85%)、碳氢化合物(25.23%)、H2O(17.78%)、CO(6.11%);液态产物成分接近柴油,但含有9.57%的固态杂质;液体产物热值为45311kJ/kg。
氧的存在对含油污泥热处理后得到的液体产品质量有较大的影响。对含油污泥氧化热处理动力学原理的研究发现,高温分解和氧化热分解在处理过程中并存,在613K以下,高温分解为主要反应;可以用5个平行的反应阶段来描述氧化热处理的反应过程,得到的反应动力学方程为含油污泥热处理系统的设计提供了依据。
热处理技术效果较好,但操作复杂,反应条件要求高。该技术已在国外广泛应用,国内目前仍处于研究阶段。
(3)热洗涤法。
热洗涤法是美国、英国、荷兰、加拿大等 广泛采用的含油污泥处理方法。将含油污泥用70℃的热碱水和洗涤剂反复洗涤,在液固比值为2:1的条件下,洗涤20min,可将油含量为30%的含油污泥洗至残油率为0.3%。国内对热洗涤法处理含油污泥的研究证明,含油污泥经化学热洗涤后呈中性,残油率在3%以下,处理后的污泥可固化填埋,或通过生物处理技术和做型煤填料进行处理。值得注意的是,目前油的回收通常与其它技术相结合,一般不单纯以回收油为目的。
2.2.2 含油污泥用于注水井调剖
含油污泥与地层有良好的配伍性,可将其用作调剖剂。利用含油污泥中的泥组分、油组分,采用化学处理方法,加入适量的各种悬浮剂、分散剂和增粘剂,能使悬浮其中的固体颗粒延长悬浮时间、增加注入深度,提高封堵强度,同时使油组分分散均匀,形成均一、稳定的乳状液。由含油污泥配制成的乳化悬浮液调剖剂用于油田注水井调剖,在地层中到达一定的深度后,受地层水冲释及地层岩石的吸附作用,乳化悬浮体系分解,其中的泥质吸附胶沥质和蜡质,并通过它们粘联聚集形成较大粒径的团粒结构,沉降在大孔道中,使大孔道通径变小,封堵高渗透层带,迫使注入水改变渗流方向,提高注入水波及体积。通过优化施工工艺,可使含油污泥只封堵住高渗透地带,而不污染中、低渗透层。
对河南油田含油污泥的室内实验和现场试验证明,经过化学药剂处理后的含油污泥可泵性好,粘度低于300mPa·s,悬浮性能好,沉降时间在4h以上,作为调剖剂用于注水井调剖在技术上是可行的;增油效果明显,可减少无效注水量,解决了含油污泥外排造成的环境污染问题,提高了注入水水质,经济效益和社会效益明显。
2.2.3 含油污泥生产建筑材料
将含油污泥作为原料,采用一定工艺可生产建筑材料,如用于铺设路面或墙体材料以及筑坝等。该技术可以较彻底的解决含油污泥对环境的污染,并能产生一定的经济效益,是近年来含油污泥资源再利用和无害化处理的一个研究方向。
Mansurov等将含油污泥处理后用作道路建设材料。加热后石油中的轻质组分挥发,剩余的重质组分(主要是沥青质)粘附在固体残渣上。将冷却后的固体残渣(40%~50%)与沙子(27%~35%)及粉末状石灰石(20%~25%)混合,然后加入新的液态沥青(3%~5%),混合15min后即可得沥青混凝土建筑材料。
童辉等利用中原油田含油污泥烧结制作建筑材料,并对其中的影响因素进行了讨论。将含油污泥和粘土按一定的重量比混合均匀,控制物料总含水率在8%左右,在6~30MPa压力下压制成试样,经烘干和自然干燥后,高温炉中煅烧1~2h然后随炉冷却,得抗压强度为49.1MPa的产品。实验发现,污泥含量大于30%时,CaCO3分解会产生明显的体积倒缩现象,影响试块的容重和强度;污泥粒度大于60目时,试样易炸裂;污泥中可溶盐含量大于0.5%时,将对强度产生影响;烧结过程中,污泥中的CaCO3分解后与粘土中的活性SiO2反应生成主晶相为硅灰石的稳定矿物,SiO2的存在对污泥中CaCO3的分解有明显的诱导作用。
2.2.4 焦化法制备含碳除油吸附剂
含油污泥可用作焦化装置的原料,用其生产的浮油吸附材料可以高效地清除溢油污染和回收浮油。含油污泥中的矿物油重质组分沉积居多,利用焦化法处理含油污泥的实质是对重质油的深度热处理,即重质油的高温裂解和热缩合。
将含油污泥注入焦化装置,可以充分利用焦化过程的废弃热量或过剩余热使污泥中的有机组分经高温热裂解变为焦化产品,同时含油污泥可以作为骤冷介质在清焦前对热焦炭进行冷却,既消除了含油污泥的污染,又得到有用的焦化产品。
戴永胜等进行了焦化反应制备含碳吸附剂的研究。将预处理过的含油污泥与强度添加剂和炭化添加剂混合后送入已预热至一定温度的焦化反应器中,恒温加热进行焦化反应。当混合物温度达到泡点时,轻组分汽化生成的蒸汽经管线引出后冷凝,冷凝产物经分离得到回收油,可继续加工利用。反应结束后,反应器中的固体剩余物即为生成的焦炭。实验证明,温度太低、加热时间太短,固相产物焦化不完全,无法起到吸油作用;温度过高、时间过长,焦炭强度和吸油率降低,反应温度以400℃为宜。加入添加剂可提高焦炭的机械强度和吸油率。
粗粒化除油技术的关键是粗粒化载体。研究发现,碳-无机吸附剂比陶粒和聚丙烯的粗粒化除油效果好,但因其孔结构不如活性炭的孔结构均匀、致密,所以除油效果略差于活性炭。碳-无机吸附剂是亲油性材料,除油过程包括吸油润湿粗粒化和重力沉降除油,属于“湿润聚结”原理,所以投加PAM能提高出油率,投加PAC则使后续除油效果变差。
含油污泥制备含碳除油吸附剂,含油污泥处理彻底,生产的焦炭应用广泛,产生的轻质液态烃可回收用作燃料,是一种有应用前景的炼油厂含油污泥处理方法:但该方法工艺复杂,成本较高,生产的焦炭除油率还有待提高。
2.2.5 含油污泥在橡胶制品中的应用
我国部分油田产出的污水水质矿化度高、SRB高、H2S高、CO2高、pH低,对注水系统的设备和管道腐蚀严重,为此在处理中加入生石灰乳以中和酸性污水,但此方法会产生大量被原油污染的CaCO3膏状沉淀。因此可将含油CaCO3污泥制备成橡胶填料剂和补强剂,代替陶土和轻钙在橡胶制品中使用。
张巧莲在对河南油田污泥进行成分分析后,通过湿法粉碎、洗盐、除杂、干燥、过筛等工艺将含油CaCO3污泥加工成平均粒径为1.86μm的填料。实验证明,将其应用于天然橡胶(NR),污泥填料既具有陶土补强性能好和轻质CaCO3高填充性能的优点,又克服了陶土撕裂性能差和轻钙补强性能差的缺点,在NR中可代替陶土和轻钙;将其应用于丁苯橡胶,与轻钙相比,污泥填料补强性能较强。但该产品带有浅土黄色,不宜在白色制品中使用。
由于含油污泥中原有的原油极性不够强,直接用作填料效果不理想,因此中国科学院等有关院所用苯丙乳液对油田CaCO3固体废渣进行了表面改性,利用碳氢化合物和苯丙乳液都是有机物,容易相互吸附反应的特点,使羧基键合或吸附到碳氢化合物表面,形成以羧基为主要极性基团的改性活化CaCO3填料,其性能优于有机物对CaCO3的改性。具体方法为:在油田固体废渣中加入质量为20%的苯丙乳液,投入混合机中充分搅拌30min后,进入压滤机中压出水分,再进入旋转闪蒸干燥机中进行喷雾干燥,用布袋收集器收集其干燥粉体。该产品用于PVC管材、PVC地板革等建材制品,产品性能符合 相关规定。
含油污泥用于橡胶制品充分利用了其中的CaCO3资源,制得的污泥填料价格低廉,能降低橡胶制品的成本,同时可消除环境污染。但该技术只适用于CaCO3含量较高的含油污泥,其使用受到污泥成分的制约。
3 结语
含油污泥因处理难度大而成为困扰环境保护和石油工业发展的难题,同时各地区含油污泥成分也不同,应积极寻求多种处理途径彻底解决含油污泥污染问题。调质-机械脱水、生物处理、固化处理等技术实现了含油污泥的减量化和无害化,而综合利用技术则进一步实现了资源的回收利用。随着环境保护要求的不断提高和含油污泥处理技术的不断深入,资源化处理已成为含油污泥处理技术发展的主要目标。