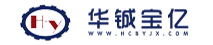
1 项目概述
现阶段中韩石化炼油厂区的污泥处理系统仅采用污泥离心脱水工艺进行处理,脱水后污泥含水率高达84%左右,离心脱水后的污泥依旧具有流体化性质,污泥减量不够充分,污泥后续处置难度和成本仍然较高,需要相当高的后续处置费用,因此有必要进一步减量。
污泥种类中主要难处理的污泥为含油污泥,其一般组成方式为水包油(O/W)、油包水(W/O)以及由悬浮固体(SS)组成稳定的悬浮乳状液体系,脱水效果非常不好,污泥成分和物性均会受污水的水质情况、处理方式、所加药剂的种类等因素影响严重,差异性较大,处理成本高,且含油污泥含有许多PAHs、重金属元素、挥发性物质等有害物质,对环境还存在一定的放射性污染。由于含有污泥性质特殊,降低含水率困难。含油污泥一般的处理工艺:焚烧法、生物去除法、溶剂萃取法、含油污泥调稠法、焦化法、含油污泥综合利用法等。
本文主要阐述在原有系统的末端增设干化单元,对离心脱水后的三泥进一步干化,将污泥含水率从85%左右降低到40%以下,得到减量化处理,降低对环境的影响。本项目实施后,将含水率较高的含油污泥的含水率得到有效的降低,“三泥”外运量显著减少,可以减少社会处理的压力,提升炼油厂社会形象。现在生产的基本要求要做到“三泥”减量化、无害化、资源化的处理,今后污泥处置的方法将会往污泥减量化、无害化、资源化处理技术发展,未来将逐步得到广泛应用。
2 污泥干化技术比选
现在污泥干化主流工艺基本采用间接热干化工艺,主要有:桨叶干化工艺技术、射流干化工艺技术、薄层干化工艺技术、带式干化工艺技术等。针对现有4种污泥干化工艺进行六个方面的对比,见下表所示:
序号 | 项目 | 桨叶干化工艺技术 | 射流干化工艺技术 | 薄层干化工艺技术 | 带式干化工艺技术 |
1 | 能否干化油泥 | 能 | 不能 | 不能 | 不能 |
2 | 工艺的成熟性 | 成熟工艺,在污泥处理中广泛应用 | 新工艺,污泥处理中应用少 | 成熟工艺,在污泥处理中广泛应用 | 老式工艺,在污泥处理中有所应用 |
3 | 安全性评价 | 采用严格的防爆检测及措施,高温150~170℃干化 | 安全性高,一般采用低温60℃左右干化 | 需采用严格的防爆检测及措施,高温150~170℃干化 | 需采用严格的防爆检测及措施,高温120~170℃干化 |
4 | 占地面积大小 | 一般 | 大(另需配套臭气处理场地) | 较大 | 大(另需配套臭气处理场地) |
5 | 运行费用多少 | 大约150~160元/吨 | 大约200~220元/吨 | 大约170~210元/吨 | 大约200~210元/吨 |
6 | 系统复杂性如何 | 工艺相对简单,设备较少,运行操作简单,维护量少 | 工艺相对简单,设备较少,运行操作简单,维护量少 | 设备较多,检修维护工作量较大 | 设备较多,检修维护工作量较大 |
综上所述,根据四类干化工艺对比,本技术方案推荐使用桨叶干化工艺,其原理是先对油泥进行破乳除油后调理预处理,然后与活性生化污泥混合,浓缩后进行离心脱水,离心脱水后的污泥进入干燥机,采用蒸汽作为加热源,蒸汽通过干燥机内部的转轴及楔形的空叶片,与其中污泥发生间接接触对湿污泥进行一定的干燥,转轴及楔形叶片可做到一边加热污泥,一边将污泥往前推进,将干化过后的污泥从出口推出,实现整个污泥干化过程。本套工艺系统设备布置紧凑,占地面积较小。
3 污泥干化技术方案
3.1 工艺描述
本项目污泥采用“双向自净干化-尾气治理一体化”污泥减量工艺。该干化单元主要配套相应的污泥干燥机、干化进出料系统及相应的尾气处理系统。经过离心脱水后油泥污泥含水率在85%左右,通过现场的污泥泵打入到可移动的储泥槽,通过叉车定期运送到污泥干化现场(距离约500米)。油泥含量按一定配比定量地输送至湿污泥料仓与生化污泥混合后,再通过进料螺旋输送机送至双向自净干化机进料端,干化后污泥从干化机中排出,通过螺旋输送机和斗式提升机输送至干污泥料仓,干化后的污泥由干化料仓卸料阀控制,卸料至危废公司专门的危废运输车。双向自净干化机以低压蒸汽为加热介质,将含水率小于85%的污泥在干化机叶片的不断搅拌作用下与热载体及热表面得到相对充分的接触,使内部物料在升温的过程中做到同时将表面水分进行蒸发。干化机内的污泥在螺旋叶片的不断往前推动下向污泥出料口的方向进行移动,在这个过程中污泥的水分沿轴线方向不断蒸发至含水率小于30%,污泥重量达到缩减,真正实现污泥的减量。
污泥尾气处理工艺主要是处理污泥在干化中蒸发出来的水分及分解或释放的少量污染废气、微量的粉尘。利用尾气引风机的作用,以负压形式,经旋风分离器将产生的粉尘去除,并通过喷淋塔做到降温,并经过活性炭预处理去除污染后,送入污水处理场原有的催化燃烧系统装置。
3.2 双向自净干化系统
3.2.1 工艺简介
干化机一般分为热对流式和热传导式两类。热对流式即通过热载体(如热空气)与被干燥的物料相互接触并进行一定的干化;传导式加热过程中热载体并不与被干燥的物料直接接触,而是热表面与物料之间相互接触。考虑到现在石化企业所产生的污泥的复杂性,进料含水率较高,采用热传导(间接)加热形式会更安全,效率也会更高。
双向自净干化系统为间接传导加热的方式,是一种在设备内部设置搅拌自净叶片,使湿物料在叶片的搅动下,与热载体充分进行接触,从而达到干燥目的的低速搅拌干化机,结构形式一般为卧式。干化机带有刮刀的独特叶片设计形式,能够保证单位有效容积内传热面积大,其中热介质可以采用低压蒸汽作为热源,更好地利用工业余热,减少热污染,降低整个项目的运行成本。双向自净干化机所用热量均用来加热内部物料,热量损失仅有的损失为通过器体保温层和排湿向环境的散热,说明热量损失较少,节约能源。双向自净干化机圆盘叶片传热面具有自清洁功能,物料在设备整个腔体内输送的过程中,物料颗粒与叶片表面的相对运动会产生一定的分散力,具有清洗作用,能够使附着于加热斜面上的残留污泥自动地清除,进而能够保持叶片高效的传热功能,现场不需要人工清理,即可以达到内部自净的目的。这即为双向自净干化系统的优越性。
3.2.2 工作原理
双向自净干化机是由带有夹套的壳体、搅拌轴、机座以及一些传动部分组成,污泥的整个干燥过程都在封闭状态下进行,同时有机气体及异味气体在密闭条件下也送至尾气处理装置中,进而避免环境的污染。
本套干化机设备以蒸汽作为加热能源,轴两端装有热介质导入和导出的旋转接头。加热能源分为两处,分别进入干化机壳体夹套中和叶片轴腔内,可将机器内部全身和搅拌轴同时进行加热,以传导加热的方式对泥料进行加热干燥。被干燥的泥料由螺旋输送机定量地连续送至干化机的加料口处,泥料进入到加料器后,通过叶片的不断转动使物料进行翻转、搅拌,在这个过程中不断更换加热介面,让器身和叶片充分接触,做到充分加热,使泥料所含的表面水分进行蒸发。同时,泥料随搅拌轴的旋转成螺旋轨迹向出料口方向进行输送,在输送过程中继续搅拌,使污泥中渗出的水分不断蒸发。干燥过后均匀的合格产品由出料口排出。
3.2.3 设备特点
本套设备采用的双向自净干化机存在一定的优势,具体如下面四点:
(1)设备整体结构布置紧凑,占地面积小。由设备的整体结构可知,干燥所需的热量主要是由排列于空心轴上的叶片壁面所提供,此外夹套壁面也可提供部分传热量,所以单位体积设备的传热面大,可节省设备占地面积,减少基建投资。
(2)热量利用率高。本设备双向自净干化机采用热传导的方式进行加热,所有传热面均被泥料覆盖,减少了一定热量损失,热量利用率可高达85%往上。设备内部叶片为整体焊接,强度较好,叶片上的刮板可防止污泥粘结在叶片上,同时也能更好地破碎进料污泥,提高热量的利用率。
(3)热介质可以采用低压蒸汽作为热源,对于石化企业能够更好地利用工业余热,减少热污染,降低运行成本。
(4)设备叶片具有很好的自净能力,这样可提高叶片的传热能力。旋转叶片的倾斜面与颗粒或粉末层的联合运动会产生一定分散力,使附着于加热斜面的污泥自动地清除,保持叶片有着高效的传热能力。另外,由于两轴叶片能够反向旋转,交替分段进行压缩和膨胀搅拌,传热能够均匀,提高了传热效率。
因此,从上述特点中可以看出该套系统应用于污泥干化的未来前景非常广阔,具有很大的市场应用潜力,是一种新型的、比较离心的污泥干化系统。
4 项目运行情况分析
4.1 干化后物料分析
含油污泥含水率在45%~70%之间时,属于含油污泥的“黏滞区”,黏性较大,此时的油泥很容易黏壁,会造成干化效率低,这个含水率区间的油泥不利于进行干化处理。如果想要进一步降低含油污泥的含水率,将含水率控制在<35%时,干化后污泥的粉尘含量将得到一定提高,很容易发生爆炸。当湿污泥含水率在35%~45%之间时,污泥黏性就开始逐渐降低了,水分起到凝塑的作用,污泥会呈现颗粒状,即易于运输,且热值也较高,此区间很适合在工程中应用。
经过现场摸索,含油污泥含量与生化污泥含量配比值在1:5的情况下,出泥含水率较好。
2020年7月~10月期间,污泥干化设施混合污泥样进出口泥样数据如下表所示:
序号 | 油泥含量 | 进泥含水率 | 出泥含水率 | 减量化 |
1 | 20 | 86.4 | 35.4 | 78.95 |
2 | 85.3 | 34.3 | 77.63 | |
3 | 86.5 | 33.2 | 79.79 | |
4 | 86.7 | 35.4 | 79.41 |
经过数据整理分析可得出:进口平均含水率为86.22%,出口平均含水率为34.58%,实现了污泥79%减量化目标,基本满足了污泥干化后含水率要求,且干化后污泥便于后续运输、存储,同时可以考虑进CFB锅炉掺烧。
4.2 废气治理情况分析
本项目中,废气治理的流程主要包括旋风分离器、喷淋塔、活性炭吸附罐、催化燃烧装置,由于干化过程中会形成少量的粉尘颗粒,在尾气治理系统中增设旋风分离器,可去除粉尘颗粒。其中在干化过程中产生的有机挥发气体及异味在密闭氛围中先通过洗涤吸收塔进行初步洗涤吸收,再经过活性炭吸附装置,进入催化燃烧装置焚烧去除,经过以上流程,基本可去除尾气中的挥发性有机物(VOCs)和易挥发含氮、含硫恶臭有机污染物,尾气排放达标。
4.3 运行成本分析
该项目污泥脱水-干化项目按干化机实际处理量0.7t/h(平均含水率85%),每天运行24小时,污泥含水率≤35%进行成本核算。依据设计方案计算,本项目实际运行负荷约为71kW,功率因子取0.8,综合电价暂取为0.6元/度。根据该项目的实际特点,蒸汽(0.6MPa· G)的使用以130元/吨计算,每小时消耗蒸汽量为1.5吨,根据项目经验,中水用量为10m³/h,水费按1.0元/吨计算,得出每吨污泥处理成本约341.55元。
5 存在问题及后续思路
(1)鉴于生化污泥目前正在开展鉴定工作,待鉴定为一般固废后,可考虑后续将生化污泥干化后送入乙烯CFB锅炉进行掺烧。煤粉锅炉污泥掺烧技术是现有主流处理技术,该技术工艺是先将污泥进行干化,干化后的污泥输送至炉前,与煤进行混合进入制粉的系统,再进入锅炉内燃烧,混烧比例控制在5%以内,掺烧少量的污泥,不会影响锅炉环保指标。
(2)目前污泥干化尾气进催化燃烧装置,但目前催化燃烧装置处理量已处于高负荷,会影响其它系统的废气抽吸。生物法是处理污泥干化废气中恶臭气体的常见的处置方法,使用菌液生物处理法对恶臭气体进行吸收,效果可好于水喷淋吸收法。目前二污生化池的尾气采用的是生物滴滤法,故后续计划将干化后尾气经活性炭吸附后送入生物滴滤系统。
(3)考虑到项目运行成本问题,污泥干化设施进料口等区域未施行全封闭,故该干化设施无法干化油含量较高的含油污泥。现将含油污泥与生化污泥按照一定比例混合后干化,可提升含油污泥干化量。