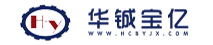
1 项目概况
1.1 项目背景
昆明市11座污水处理厂日产80%含水率污泥约800t,若直接送至垃圾填埋场填埋将给填埋场的运行管理带来危害。按照国务院发布《水污染防治行动计划》(水十条)的全面控制污染物排放中第二条,强化城镇生活污染治理中关于推进污泥处理处置有明确要求。污水处理设施产生的污泥应进行稳定化、无害化和资源化处理处置。
为解决城市污水处理厂污泥处置问题,执行 有关污泥处理处置标准,昆明市对11座污水处理厂产生的污泥集中采取高负荷厌氧消化+离心脱水+桨叶式热干化工艺处理处置,以实现污泥的四化。
1.2 工艺流程
昆明主城污水处理厂污泥处置工程搬迁项目采用高负荷厌氧消化+离心脱水+桨叶式热干化的技术路线,经处理后的污泥含固率达到75%以上,外运作为矿坑回填料、垃圾焚烧厂掺烧原料、建材利用或作为绿化介质土使用。
1.3 各工艺段污泥处理量
项目设计污泥处理处置量为100TDS/d,折算80%含水率污泥即500t/d;消化总容积15000m³,设计停留时间22.5天;脱水配置4台阿法拉伐离心式脱水机,设计单台处理量1.04TDS/h,折合每日污泥处理量99.84TDS;干化配置2台桨叶式干化机,单台处理量150t/d。
2 系统调试运行
2.1 卸料站调试运行
存在问题:昆明主城水质净化厂运至昆明主城污泥处理处置厂的脱水污泥含石块、木条等,对卸料站及后续污泥均质设备、污泥输送设备造成严重损坏,导致系统不能连续稳定运行。
解决措施:一是降低卸料站进料格栅高度,并减小格栅孔隙,防止污泥外泄,并阻止污泥中杂质进入系统;二是彻底清理卸料站,清除原有杂质;三是卸料站液压仓门启闭有序,做到车来开启卸料站液压仓门,车离关闭卸料站液压仓门,防止施工人员及保洁人员误将杂物倒入其中;四是将摄像监控移至消化、脱水中控室,将卸料情况实时监控,一旦发现车运污泥内含有杂质,禁止卸泥;五是针对进口设备老旧无配件,先选用国内精加工购买替代品,同步采购进口配件替换。
达到效果:污泥中杂质被隔绝在系统之外,设备修复后无跑泥漏泥现象。卸料站及输送设备的稳定运行为后续消化系统的连续稳定运行奠定了基础。
2.2 离心脱水调试运行
存在问题:一是因进泥有机质含量低于设计值,且偏差较大,导致降解率低,因而增加脱水机系统负荷;二是因脱水机进泥含固率高,导致设备厂家在调试设备时,将设备运行负荷定性在0.96TDS/h(出厂设计负荷为1.04TDS/h),再增加处理量,上清液将无法保证回收率;三是上清液浊度过高,平均在20000mg/L(设计值为5000~8000mg/L)。
解决措施:一是各种污泥絮凝小试,寻找适合高浓度污泥脱水的絮凝剂,并对应调整脱水机运行参数,更换设备轴承、皮带、润滑油脂等,提升脱水机运行负荷至1.08TDS/h;二是增加絮凝剂管道混合器,缩短污泥絮凝周期,提高污泥脱水过程的固体回收率至97.5%以上,并同步使出水水质COD、T-P、T-N、NH3-N等指标降低。
达到效果:一是提升脱水机的运行负荷至1.08TDS/h;二是脱水机上清液浊度降至3000mg/L以内(设计值为5000~8000mg/L),同时降低出水水质COD、T-P、T-N、NH3-N等指标至设计范围;三是脱水机的稳定运行,为后续干化系统持续供泥提供了保障。
2.3 桨叶式干化系统调试运行
存在问题:一是干化系统无法连续进泥,项目前期干化调试,进泥螺杆泵进泥量无法控制;二是悬斗输送设备连接方式有误;三是锅炉系统无法实现恒温,项目尚未完成锅炉燃烧器PID恒温控制调试,导热油温度无法根据干化机的需要进行恒温控制,生产时导热油温度波动较大,换热量不稳定,严重影响干化机调试运行;四是前期调试干化系统存在粉尘浓度大、出泥含固率高、生产扭矩大、出水水质差等问题;五是项目前期干化系统调试,废热蒸汽频繁大量泄漏,存在较大安全隐患。
解决措施:一是通过现场分析,因进泥螺杆泵所配电机为非变频电机所导致,在确认电机防腐等级后,安装独立风扇,及配套电气自控系统,实现干化系统连续进泥生产;二是改变悬斗输送设备悬斗与链条连接方式为锁扣连接,防止因悬斗掉落导致设备坍塌事故发生;三是经现场分析,因前期干化调试时,干化设备频繁卡堵、进泥量不稳定、热源需求量不稳定所导致,在保证干化机热源需求量稳定的条件下,调整燃烧器PID,使导热油油温及时根据干化机的需求及时相应,保证导热油温度恒定在设定值的±2范围以内;四是干化机自身破碎功能有限,出泥为块状,且大小不均后续输送设备通量无法满足,为加快推进调试生产,购买并安装符合现场工况环境的成品破碎机及输送设备,启动干化系统开始生产;五是根据现场工况环境,设计并向厂家定制污泥牵引破碎机,同时改造卸料螺旋、冷却螺旋,增大卸料螺旋及冷却螺旋输送通量,使干化系统单日处理提升,提升含固率;六是经现场分析,通过定制安装前置冷凝器,加强冷凝效果,提升系统负压。
达到效果:一是通过实现干化系统连续稳定进泥、导热油锅炉恒温控制、增加出口应急输送设备、后续悬斗输送设备平稳运行,启动干化系统开始生产,单日处理量210t,含固率约65%;二是通过实现牵引破碎设备安装调试、提升卸料螺旋及冷却螺旋通量,使干化系统单日处理提升至288t,含固率提升至75%;三是增加前置冷凝器,解决停机清洗冷凝系统问题同时提升干化系统年生产时间6.67%。
3 稳定运行
通过对各工艺段实施优化技改,项目消化、脱水系统已接近90%负荷稳定运行,日均污泥处理量438t(含水率80%);干化系统稳定实现96%负荷运行,单日污泥处理量288t。
项目污泥干化系统未运行前(2018.12.1~2019.3.31),污泥接收总量为46433.36t,污泥外运总量为29973.77t, 系统减量16459.59t,削减率仅35.45%。自污泥干化投入运行起(2019.4.1)至2019.8.31,项目污泥接收总量为63039.06t,外运污泥总量为24628.46t,系统减量38410.6t,削减率达60.93%。2019年8月起污泥干化系统两条线实现96%负荷连续稳定运行,项目当月污泥接收总量12314.31t,外运污泥总量为3508.56t,系统减量8805.75t,削减率提升至71.51%。
月均污泥外运总量从污泥干化系统未运行时(2018.12.1~2019.3.31)的7493.44t下降至逐步连续稳定运行后(2019.4.1~2019.8.31)的4925.69t,下降幅度约34.27%,减量化效果明显。
4 结论
综上所述,项目采用高负荷厌氧消化+离心脱水+桨叶式热干化工艺技术,通过优化调试,已实现整体稳定运行。