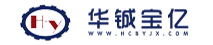
石油开采、石油炼制、石油化工、油品贮运、船舶航运、车辆清洗、机械制造、食品加工等过程均会产生含油废水,特别是石油开采、石油炼制行业排出大量的含油污水、含油污泥,据报道,仅中原油田含油污水总量为12×104m³/d、含油污泥总量为(0.9~1.44)×104m³/d。含油污泥主要产生于油田和炼油厂,如在原油脱水中,脱水罐、贮油罐和污油罐等底部存在大量含油污泥;在油田、炼油厂的污水处理场的隔油池、浮选池、曝气池等也存在大量含油污泥。这些污泥的成分十分复杂,一般由水包油(O/W)、油包水(W/O)以及悬浮固体组成,且充分乳化,粘度较大,难以沉降。为了充分利用污水资源,稳定污水处理(特别是石油采出水处理后回注,可以有效地保持油区地层压力),保护生态环境。近年来,含油污水、含油污泥的处理备受关注,由此推动了含油污水处理、含油污泥脱水、除油设备及相关的处理技术的发展。
1 含油污泥及其处理工艺
含油污泥颗粒细小,呈絮凝体状,密度差小(油、水密度接近)、含水率高(一般在96%左右)、持水力强,且泥、油、水相互包裹在一起,又充分乳化,粘度较大,难以沉降。含油污泥稳定性差,容易腐败和产生恶臭,污染空气环境。
Zall Jonathan等人曾分别研究过一般城市污水厂的污泥和含油污泥的过滤脱水性能。如测定了含油3%、含总悬浮固体4%的含油污泥(浮渣)和含总悬浮固体1%~2%的一般污泥的比阻和可压缩性系数,证实含油污泥的比阻比一般污泥的大40倍,其可压缩性系数大20倍。
另据文献介绍,含油13.1%、含泥16.8%、含水70.1%的含油污泥的比阻为8.9×1014m/kg。由此可知,含油污泥属难过滤性污泥,特别是不易实现油-水-泥的三相分离。
目前,含油污泥处理的主要工艺有以下几种:
(1)浓缩-化学调节-脱水。
(2)浓缩-消化-化学调节-脱水。
(3)浓缩-消化-化学调节-脱水-压制。
(4)浓缩-化学调节-脱水-焚烧。
(5)浓缩-消化-化学调节-脱水-焚烧。
(6)浓缩-化学调节-脱水-熔融。
可以看出,浓缩、化学调节和脱水3个处理单元是含油污泥处理系统必须的环节。
2 污泥的浓缩处理
无论是从脱水罐、贮油罐、污油罐等底部排出的含油污泥,还是从污水处理场的隔油池、浮选池、曝气池等排出的含油污泥(浮渣),其含水率一般都在96%左右,体积很大,对污泥的处理、利用和运输造成很大困难。污泥浓缩的目的就是通过污泥增稠来降低污泥的含水率和减少污泥的体积,根据计算,污泥含水率从99%降至96%时,其体积减少为原来的1/4。这样对机械脱水,可减少混凝剂的投加量及脱水设备数量,提高脱水效率。
污泥中游离水占70%,毛细水占20%,颗粒结合水和内部结合水占10%。污泥浓缩主要去除游离水。污泥浓缩处理主要有以下的方法。
2.1 重力浓缩法
重力浓缩法是依靠污泥中固体物质的重力作用进行沉降与压密,属于自由沉降过程。其装置如污泥浓缩池等。
2.2 气浮浓缩法
气浮浓缩法根据溶气气浮原理,通过压力溶气罐溶入过量空气,然后突然减压释放出大量微小气泡,并附在污泥颗粒周围,使其密度减小而强制上浮,污泥在表层获得浓缩。加压溶气气浮法适用于相对密度接近于1的活性污泥。其装置如气浮池等。
2.3 离心浓缩法
离心浓缩法是利用污泥中固、液间的密度差,在离心力场或负压力场作用下,固相颗粒受外力作用迅速沉降的原理进行沉降的。其设备如离心机、旋流器等。
2.4 转筒浓缩过滤
转筒浓缩过滤装置主要由絮凝反应器、转筒、上筒、滤网、机架、集水槽、传动装置和喷水器等组成。待处理污泥通过入口与絮凝剂一起进入絮凝反应器,由絮凝反应器电机带动搅拌器旋转,使待处理污泥在絮凝剂的作用下得以充分凝集,然后通过进料管进入转筒,转筒外有滤网(一定时间喷水器对滤网进行冲洗,以免滤网堵塞),中心轴上有螺旋叶片,由驱动电机带动转筒旋转(转速在一定范围内可调),使得污泥在前进的过程中得以逐渐浓缩,其间的滤液从滤液出口流出,经浓缩后的污泥从浓缩液出口排出。与重力浓缩比较,具有以下优点:浓缩时间短,浓缩效率高,浓缩效果稳定可靠,能够得到比较稳定的污泥浓度,适用浓度范围大等。
3 含油污泥的脱水处理
含油污泥机械脱水前需进行预处理。污泥脱水过程实际上是污泥的悬浮粒子群和水的相对运动,而污泥的预处理则是通过一定手段调整固体粒子群的性状和排列状态,使之适合不同的脱水条件。
3.1 含油污泥的预处理
污泥的预处理主要是为了改善污泥的脱水性能,提高脱水设备的生产能力。
污泥的预处理方法有化学调节法、淘洗调节法等,主要采用化学调节法,即调质。
化学调节法就是向污泥中投加混凝剂、助凝剂,使污泥中的悬浮微粒凝聚并顺利进行脱水。但对于含油污泥要实现油-水-固的三相分离,还必须投加表面活性剂、破乳剂、pH调节剂等使其中粘度大的吸附油解吸和破乳,使吸附油从污泥固体表面脱附及油-水脱附分离。
含油污泥化学调节法的选择依据是:①含油污泥的性质及特点;②使用的脱水机械的性能;③滤饼的后续处理方法。
据文献报道,首先向含油污泥中投加硅藻土、石灰、飞灰等微细固体粉末作为调节剂,使易变形的含油污泥粒子形成有刚性的污泥骨架,使污泥呈毛细结构,改善滤饼透气性,且增加固液相间的密度差,改善脱水性能;也可采用部分滤饼回流到含油污泥中作为调节剂。
其次,投加絮凝剂和破乳剂(或表面活性剂)。絮凝剂分有机和无机两大类。无机絮凝剂为Al2(SO4)3、PAC的絮凝效果较好,据有关研究表明,铁铝复盐聚合物混凝剂比单盐的铁或铝聚合物处理含油污泥效果更好;有机絮凝剂以阳离子聚丙烯酰胺(PAM)的絮凝效果较佳。但经无机絮凝剂处理的含油污泥的过滤性能优于有机絮凝剂处理的含油污泥,且脱水后含水率较低。有关试验表明,有机、无机絮凝剂复合使用可减少用量,絮凝效率大大提高,经复合絮凝剂处理后,可大大改善污泥的脱水过滤性能,降低滤饼含水率,在投加药剂量相当的前提下比单独使用效果好。
含油污泥的化学调节法必须在测试含油污泥性质的基础上进行。对含油量不小于10%的,宜用亲水性表面活性剂,分离后水和固体在下层,油在上层;对含油量不大于4%的,宜用亲油性表面活性剂,分离后含油固体在下层,水在上层。水层中均含有可溶性油和微乳化油。
3.2 含油污泥脱水处理
要使含油污泥的机械脱水效果好,应根据具体情况选用污泥脱水机械和脱水系统,包括污泥物料性质的测试、脱水机械及其参数的选择等。机械脱水的一种方式是以过滤介质(多孔性材料)两面的压力差作为推动力,使污泥中的水分强制通过过滤介质(称为滤液),固体颗粒被截留在介质上(称为滤饼),从而达到脱水的目的。造成压力差推动力的方法主要有:依靠污泥自身厚度的静压力(如污泥干化场的渗透脱水);在过滤介质的一面造成负压(如真空吸滤脱水);加压污泥把水分压过过滤介质(如压滤脱水);利用固液间的密度差,通过离心力使固液分离(如离心沉降脱水)。目前,应用的含油污泥脱水处理主要有下面几种。
3.2.1 真空过滤
真空过滤是用多孔过滤介质截留悬浮物中的固体颗粒,在介质表面形成滤饼,滤饼一经形成就成为后进入悬浮液的过滤介质。真空过滤机虽然设计简单、使用范围广,受力情况简单,能连续生产,但其真空推动力较低,过滤速率不高,滤渣含湿量较高,对含油污水通过浮选工艺产生的浮渣不能正常使用,且介质易被油污染,介质用清水清洗再生造成二次污染及增加单位处理成本。真空过滤的主要设备有转鼓真空过滤机、水平带式真空过滤机等。
3.2.2 加压过滤脱水
污泥加压过滤脱水是通过在过滤介质两面加压,使污泥水分压过介质。压滤机构造简单,过滤推动力大,脱水效果好,滤饼含湿量低(可达50%),但设备笨重,操作劳动强度大,不能连续生产、效率较低。同样存在介质易被油污染、清水清洗再生造成二次污染及增加单位处理成本的问题。主要设备有板框压滤机、厢式压滤机。
3.2.3 滚压脱水
污泥滚压脱水的主要设备是带式压榨过滤机。带式压榨过滤机把压力加在滤带上,用滤带的压力或张力使污泥脱水,而不需要真空或加压设备。进行污泥脱水时,首先将加了絮凝剂的污泥送入混合筒进行充分混合以促进絮凝,然后进入重力脱水段,依靠重力脱掉污泥中的游离水,使污泥失去流动性便于挤压(加长重力脱水段,可提高重力脱水效率)。经重力脱水后进入“楔形”压榨段,经施压脱水,滤液穿过滤带进入排水系统,滤饼经刮刀剥落,粘在滤带上的污泥经冲洗水冲洗随滤液排走。据文献介绍,带式压榨过滤机处理污泥效果好(如用对含油污泥投加飞灰100kg/m³,4%FeCl3溶液33L/m³,絮凝剂100~150μg/g的化学调节法),能连续生产,但必须加大药剂量使污泥充分絮凝后完全沉降,且污泥含渣率在3%以上,否则难以处理。
带式压榨过滤机对通过浮选工艺产生的浮渣不能正常使用,且同样存在滤带易被油污染、清水清洗再生造成二次污染及增加单位处理成本的问题。
3.2.4 离心脱水
污泥离心脱水无需过滤介质,依靠离心力场作用,使固体颗粒迅速沉降而实现固液分离。其主要设备有以下几种:
(1)带撇液装置和刮刀的三足式沉降下卸料离心机。该设备处理较粘的污泥,可不加化学药剂而获得较好效果,滤饼含湿量与沉降时间有关。澄清液与软塑料沉渣由撇液装置分别排出。但处理量小,间歇操作,不适于处理大量污泥。对含油污泥特别是含沥青质、石蜡等的处理,沥青质、石蜡等易粘附在撇液装置上而堵塞。
(2)卧式螺旋卸料沉降离心机。该设备具有处理量大,处理效果好(滤饼含湿量一般为75%~85%),操作简单,自动化程度高,对原液适应性好,工作环境卫生,基建费用少,占地少等优点,已成为一种新型高效的污泥脱水设备。对含油污泥处理,据有关文献介绍,要获得好的分离效果,则在含油低时,应使泥中的少量油进入泥饼,即分离因数小,一般取1000;反之,要求泥饼中含油量尽量低时,分离因数宜大,一般取2500~2700。同时对含油污泥还必须注意离心机的分离因数、泥饼层厚度和污泥停留时间的平衡和调节。
目前国内含油污泥处理主要使用板框压滤机和带式过滤机,而国外使用较广泛的是带式压榨过滤机和卧式螺旋卸料沉降离心机。
4 含油污泥脱水设备的发展
随着环境保护要求的不断提高,对含油污水采用不同的处理工艺而产生多样化、复杂化的含油污泥,因而开发多功能、高功效、自动化的机械脱液设备或系统已成为目前含油污泥处理的发展趋势。
4.1 自动板框压滤机
自动板框压滤机可大大提高生产率,降低劳动强度。据文献报道,对稠油污泥采用全自动拉板厢式板框压滤机进行脱水,在不加任何脱水剂的条件下,脱水后浮渣含水从95.2%左右降至70%,其含油量约占污泥重量的2%,滤饼可进行外运或填埋等后续处理。
4.2 集污泥浓缩、脱水于一体的机械水液设备
转筒浓缩带式压榨过滤机集污泥浓缩和带式压榨于一体,克服污泥浓度低等不利因素,大大提高污泥处理能力,比传统的带式压榨过滤机更具高效、节能、处理量大等优点。卧式压榨螺旋卸料沉降离心机是90年代初KHD公司发明的,它与普通卧式螺旋卸料沉降离心机相比,在分离具有可压缩性固体悬浮液时,其沉渣含湿量可降低5%左右(市政初沉污泥含固量4.4%时,滤饼含湿量为71%左右),与带式压榨过滤机相比,具有的处理量大、混凝剂消耗量小、单位处理成本低等优点。卧式压榨螺旋卸料沉降离心机在国外已广泛用于污泥脱水中,国内已有广州猎德污水处理厂等从国外引进设备用于污泥浓缩脱水处理,自主开发生产的此类设备也在深圳南山污水处理厂等用于污泥浓缩脱水处理。
4.3 集污泥浓缩、油水分离于一体的三相机械设备
液-液-固旋流器已用于油田含油污水的油、水、悬浮物的分离,但其排出的含油污泥仍具有流动性,需进一步脱水处理以便对污泥的后续处理(如运输或填埋等)。目前,国外已有Alfa-lafa公司、Flottweg公司及Guinard公司等开发了三相卧螺沉降离心机,并用于钢厂、炼油厂的含油污泥处理中,效果很好;国内也有厂家自主开发了三相卧螺沉降离心机。三相卧螺沉降离心机实现了油-水-泥(固体)三相的分离,对含油污泥处理效果很好。
三相卧螺沉降离心机是今后含油污泥处理的理想设备及发展方向。用于污泥浓缩脱水的卧螺沉降离心机的分离因数高达5000,长径比达5,这进一步为卧螺沉降离心机用于污泥处理提供了广阔的发展前景。目前,重庆江北机械有限责任公司与四川大学合作开发含油污泥处理技术及三相分离,主要进行含油污泥的混凝效果研究、三相(普通三相卧螺离心机、压榨三相卧螺离心机)分离的试验工作。相信在不久,国内对含油污泥的三相处理会取得突破性的进展。
5 对含油污泥脱水处理的几点建议
目前,我国在含油污泥等废渣的处理技术上和发达 有很大的差距,因此在吸收国外 技术的基础上,结合我国国情开发合适自己的含油污泥脱水设备(系统)及处理技术乃是当务之急。
5.1 重视含油污泥的化学调节技术
要使含油污泥机械脱水达到预期效果,只靠 的脱水设备是不可能实现的。必须根据不同含油污泥的性质,通过试验开发相应的化学调节技术。武钢能源总厂用三相卧螺沉降离心机分离冶金含油污泥所取得的效果,是在该公司根据该油泥特性,通过试验自主开发油泥调节技术(投加适当的表面活性剂、少量的石灰固体微细粉末、加热到50℃以上及适当的搅拌速度处理一定时间)的基础上获得的。因此,应重视含油污泥的化学调节技术的研究。除对研究和筛选有效快速的混凝破乳剂外,还应大力研究开发固体粉末调理剂、表面活性剂等以及通过对含油污泥的试验获取相应的化学调节技术。
5.2 重视含油污泥的机械脱水
机械脱水是含油污泥处理技术的关键,只有做到“水清、泥干、油纯”的三相分离,才能显著减少含油污泥的后处理成本。大力开发高效多功能的集污泥浓缩、油水分离于一体的三相设备,可减少因过滤介质再生而产生的二次污染及增加单位处理成本,改善工作环境,降低劳动强度。
提高固体回收率和减少泥饼含湿率,以大大降低含油污泥处理的总成本,如泥饼含湿率从85%降至50%,体积可减少2/3,可减少运输或后处理费用,故应大力开发脱水效果更优的脱水设备。
5.3 应力求做到无二次污染处理
在开发含油污泥的机械脱水和化学调节技术时力争做到不产生二次污染,如机械脱水设备无过滤介质(不存在介质再生问题),采用沉降式脱水分离;机械脱水设备自身做成封闭型(如卧螺沉降离心机)等,以免污染工作场地;化学调节的添加剂便于后续处理。
5.4 开发合适的油泥处理技术
由于不同的含油废水采用不同的处理工艺,所产生的含油污泥性质和量也不同,因而应采用不同的油泥处理技术。因此,应注重因地制宜地开发不同的油泥处理技术。对引进国外的 处理系统应进行具体的分析,以适合于国内的具体情况。如川东钻探公司1997年引进Hydrocal公司的钻井污水处理系统,该系统的FBP污泥脱水系统对由气浮产生的浮渣处理效果很好,但通过运行,气浮工艺对钻井废水处理是不合适的,故该系统对混凝沉降产生的油泥处理是否合适需进一步分析测试,以确定油泥处理工艺技术。因此,应根据具体情况引进 技术,并不断增强自主开发能力,以适应日益严格的环境保护要求。