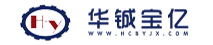
炼油厂“三泥”主要包括:浮选池加药产生的浮渣、生化系统产生的剩余活性污泥、隔油池底泥等。含油污泥(简称油泥)含有酚类、苯系物、重金属等有毒、有恶臭味的物质,是一种比较稳定的体系。其处理成本较高且技术难度大,一直是国内外炼油行业的环保难题。近年来,随着我国环保法规的日趋严格和企业技术进步的要求,“三泥”的减量化、无害化、资源化处理日益成为环保研究的重点工作之一。
1 国内外常用处理技术
(1)焚烧处理。焚烧处理是将预先经过脱水浓缩处理后的“三泥”送至焚烧炉,焚烧温度控制在800℃左右,焚烧后除去大部分有害物质,且减少了“三泥”的质量和体积。
(2)生物处理。生物处理是指利用微生物将含油污泥中的石油烃类作为碳源进行降解,使石油烃类转变为无机物质。生物处理对环境的影响较小,并且费用较低,其费用约为焚烧处理费用的1/3~1/4。
(3)“三泥”的燃料化。含油污泥中的油及有机质燃烧可产生一定热量,如果直接焚烧,不但浪费资源,而且对环境造成二次污染,因此考虑用“三泥”做燃料,充分利用“三泥”的热值。
2006年,某石油化工公司对油泥进行离心脱水,然后用高温蒸汽喷射干化,干化后的污泥再掺入煤粉作为燃料,燃烧后的残渣随粉煤灰和炉渣一起作为水泥原料。
(4)油泥干化+焚烧。干化焚烧工艺是污泥处理的一种有效工艺组合,在欧洲和日本得到广泛应用。
2 概况
油品长时间贮存导致油品组分中的重油组分(如沥青质、胶质等)以及少量的泥沙、重金属盐等沉积在油罐的底部,形成黏稠的胶质层,占储罐容量的1%~2%。其产生的周期较为集中,性质不稳定,需及时清理。目前罐底油泥的处理方式主要有两种,一种是前端的减量化处理;另一种是焚烧处理,焚烧技术在国内工业化应用中较为广泛。
公司炼油厂罐底油泥外委给有危险废物处理资质的单位处理。为节省处理费用,研究利用污水车间现有的“三泥”脱水装置对罐底油泥进行脱水处理。
3 工艺方案与实施
3.1 工艺流程
“三泥”脱水装置主要分为预处理系统、固体聚丙烯酰胺加药系统和脱水系统三部分。
在搅拌池加过滤设施,将罐底油泥用气动泵抽到罐车内,并将罐底油泥按比例掺入到搅拌池中,用污泥提升泵送至混合器加温,以加快污泥的脱水分离。加温后的污泥与0.15%高分子絮凝剂聚丙烯酰胺一同进入三相卧螺离心脱水机进行油、水、泥三相分离。
用罐车将调节储油罐中的油泥转移到“三泥”脱水装置的搅拌池中。由于罐底油泥黏度大,管线输送容易堵塞,利用气动泵将其抽到罐车内,用罐车将其卸入“三泥”脱水装置的污泥搅拌池。在“三泥”脱水装置的搅拌池内加装过滤网。将罐车内的油泥按比例卸入搅拌池,用污泥提升泵将油泥输至混合器加温,以加快油泥的脱水分离。加温后的油泥与高分子絮凝剂聚丙烯酰胺一同进入三相卧螺离心脱水机进行油、水、泥三相分离。
3.2 工程调试及运行效果
本工艺的调试主要是采用实验室烧杯实验,模拟现场工艺条件,确定较佳参数。
3.2.1 烧杯实验
取一定量的剩余活性污泥和罐底油泥分别按1:1,2:1,3:1的比例进行实验,样品体积为500mL,按实际工况加入0.15%阳离子聚丙烯酰胺,在烧杯中搅拌混合均匀后倒入量筒中,观察沉降情况。
剩余活性污泥与罐底油泥3:1的比例混合沉降效果好,渣层薄,水层厚,说明选用的阳离子聚丙烯酰胺絮凝效果好,该比例的剩余活性污泥对油泥中的悬浮物等杂质吸附得比较完全。
3.2.2 运行存在的问题及改进措施
离心脱水机脱油管线较细,到集油池绕行距离长,管线内介质油泥流动性差。脱油线的出口连接为90°弯头焊接,阻力大,弯头处极易堵塞。
针对存在的问题,采取以下措施:一是把脱油线焊接弯头改成蛇形软管连接;二是在脱油线上增加一条蒸汽吹扫线,根据实际情况对脱油线进行吹扫。
3.2.3 工艺运行效果
2015年9月,通过5d连续运行,对油泥的含水率进行分析。经“三泥”脱水装置处理后,罐底油泥的含水率平均由95%左右降至70%左右。运行期间,共处理500t罐底油泥,处理后产生的泥饼约80t,罐底油泥减量率约为84%,大幅度缩减了油泥的体积,节省处置费用74.76万元。不仅节约了资金,而且减少了对环境的污染。
脱水后含水率约70%的油泥使用180℃蒸汽进行加热脱水、干化,含水率可进一步降至25%~30%,干化后再进行焚烧。
4 结论
探讨了炼油厂罐底油泥的减量化处理,探讨了聚丙烯酰胺的选用及对剩余活性污泥与罐底油泥按适当比例混合进行实验分析,充分利用“三泥”脱水装置,使油泥含水率大幅度降低,油泥体积大幅度减小,为油泥的进一步处理处置打下了基础。