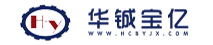
含油污泥具有油含量较高、黏度大、固体颗粒极细、呈胶状结构的亲水性黏稠液体,同时,具有沉降性能差、脱水困难等特点,造成处理难度较大。因此,长期在污水处理构筑物内不断沉积,不仅影响外输原油质量,还导致注水水质和外排污水难以达标。同时,含油污泥中除含有大量的残留油类,还含有苯系物、酚类等有毒、有害物质。若不进行处理直接排放,不但占用大量耕地,而且对周围土壤、水体、空气都将造成污染。
2009年2月20日吉林省环境保护厅下发《吉林省2009年整治违法排污企业保障群众健康环保专项行动 阶段工作方案》;松原市环境保护局下发的《松原市环境保护局行政处罚告知书》,对直接向环境排放污染物的单位加大了处罚力度。
1 污泥无害化处理技术
1.1 处理技术选择
根据目前国内含油污泥处理技术的发展状况,结合吉林油田实际,通过对超热蒸汽喷射法、污泥浓缩法、自然干化法、机械脱水法、焚烧法、生物处理法、热洗涤法等工艺技术的使用条件和产出物达到的标准等,经优化对比后,决定采用超热蒸汽喷射技术,实现含油污泥无害化处理。
1.2 超热蒸汽喷射原理
超热蒸汽(≥500℃)以超高速从特制的喷嘴中喷出,与油泥颗粒进行垂向碰撞,油泥颗粒在超热气体热能和高速所产生的动能作用下,颗粒内的石油类和水等液体迅速从颗粒内部渗出至颗粒表面,并迅速被蒸发,从而实现油等液体与固体的分离。蒸汽由管道输至油气回收单元经冷却后在重力作用下实现油水分离,油可直接回收,废水经处理后外排或回用,残渣呈粉末状。
1.3 工艺流程
含油污泥由提升泵提升至均质罐中搅拌均匀,然后再由提升泵输送到换热器加热或者直接输入离心机,经离心机脱水后的油泥再输送至高温处理槽,在高温高速蒸汽喷射下被粉碎,同时,油分和水分被蒸发出来,被粉碎的细小颗粒连同蒸汽一起进入气旋室,在旋分作用下实现蒸汽与固体颗粒的分离,固体颗粒直接进入回收槽,蒸汽进入油水分离槽经冷却后实现油水分离。
2 现场应用情况
吉林油田扶余采油厂产污泥量约3000m³/a,其污泥成分:平均含水率为85.85%,平均含油率为10.04%,平均固体含量为4.11%。
2010年吉林油田在扶余采油厂新建1套撬装污泥处理装置,于6月投产试运行,2011年移至新木联合站运行。装置由7个撬块组成:1#污泥调质撬,有螺杆泵2台、水力旋流器1台、加药装置2套、污泥均混装置2套、控制箱1座;2#污泥脱水撬,有螺杆泵3台、反洗泵1台、离心脱水装置1套、加药装置3套、控制箱1座;3#污泥净化撬,有原料输送斗1座、螺旋输送泵1台、超热蒸汽发生装置1套、高温处理槽1座、双旋风分离器1座、干渣输送器1座、控制箱1座;4#冷却水循环撬,有输油泵1台、冷凝器1台、油水分离槽1套、热交换器1座;5#、6#冷却撬,冷却塔9座;7#锅炉撬,锅炉1座。其中:1#、2#撬为污泥浓缩脱水系统,3#、4#撬为超热蒸汽净化系统,5#、6#、7#撬为辅助工艺系统。
整套装置全自动控制,设备采用露天撬装形式,设计生产周期为每年5~10月。
设计规模:超热蒸汽喷射处理装置处理量为0.5t/h。
2.1 污泥浓缩脱水系统
污泥经一级提升泵进入1#撬体的水力旋流除砂装置,筛分除去大颗粒杂质,剩下粒径小于1mm的污泥,经二级泵提升、添加药剂,输送至均混搅拌装置,进行浓度均质化处理;将处理后的均质污泥输送至2#撬体换热器,利用7#撬体中锅炉产生蒸汽进行加热,而后加药,再进入离心机进行脱水处理,处理后的残渣含水率小于70%。利用输泥泵进入污泥净化系统。
其流程:预处理后的油泥→水力旋流除砂装置→污泥均混装置(配置2套加药装置)→热交换器(配置1套加药装置)→离心脱水装置→污泥进入3#撬体(污水送至回收池)。
2.2 污泥超热蒸汽喷射净化系统
污泥超高温蒸汽喷射净化设备的主要功能是实现污泥的固液分离。由7#撬体中锅炉产生的蒸汽通过超热蒸汽发生装置,使其温度上升至550℃,随后进入3#撬体中的高温处理槽,将2#撬体脱水后的污泥击碎。高温处理槽内,300℃的油泥液体和固体经过双旋风分离装置进行固液分离,被分离出的固体将被彻底地干化并落入双旋风装置中,螺旋输送器将干渣输出。被汽化的液体部分则被送至4#撬体中的冷凝器,在油水分离槽中进行喷淋冷凝。回收的油中含水率低于0.5%,处理后的固体残渣中油含量小于0.3%,含水低于10%。
其流程:来自污泥浓缩脱水装置的污泥→原料输送斗→高温处理装置(配置蒸汽发生器、超热蒸汽发生器)→双旋风分离装置→固体干渣(油水等混合蒸汽进入冷凝器冷却回收)。
2.3 自控系统
整套含油污泥处理装置的自控系统由各处理单元可编程序控制器(PLC)、彩色触摸屏、通讯电缆、污泥处理控制程序软件及相关仪表和设备组成。
可编程序控制器(PLC)是各处理单元的核心,为模块化结构,实时采集各部分的温度、压力、流量等参数,通过变频器调整电机的转速,控制药剂的投加、污泥的流量,以实现污泥的分选、调质、脱水、净化等处理。各处理单元的流程全屏显示于彩色触摸屏上,所有控制参数均可在触摸屏上设置、修改,人机界面友好,直观、简洁,整个污泥处理过程可在触摸屏上操作实现。
含油污泥处理装置的自控系统具备故障报警及自动保护功能,可直接输出电机启停等控制信号。该系统支持远程控制。整套处理装置各参数的采集均采用屏蔽通讯电缆传输,提高了系统的可靠性、稳定性。同时,具有三级密码管理功能,防止非授权者非法操作,确保数据和机器安全运行。
污泥浓缩脱水系统控制柜内置PLC可编程序控制器,实现对主电机、副电机、进泥泵、加药泵等变频器、螺旋输送机和加药装置的控制,实现完全自动化的操作,设备运行的各种参数也是通过人机界面输入的,并对污泥浓缩脱水系统内部各种设备的运行状态进行监控,当出现故障时进行相应的报警,并显示故障信息,易于操作,维护方便。
污泥超热蒸汽喷射净化系统由彩色触摸屏、可编程序控制器、变频器控制及前端仪表、设备组成。各种参量采集及反向控制均为有线方式,具有可靠性高、精度高等特点。通过变频器、温度传感器、可编程序控制器组成的PID闭环调节控制系统监控处理效果,保证污泥进料的平稳、连续,进而保证处理效果。实时采集气化物质和固体残渣进入旋风分离室进口时的温度,变频控制污泥输送泵的排量。
3 运行情况及处理效果
3.1 运行情况
撬装污泥处理装置在扶余采油厂于2010年5月24日投产运行至2010年9月19日,运行160h,共处理含水65%~95%含油污泥32t,产固体干渣3.2t,消耗天然气量初期未计量,原料处理量2.5t/d,产渣量70kg/h。
在新木采油厂于2011年5月20日投产运行至2011年9月17日,运行259h,产渣量在15~480kg/d,共处理含水65%~95%含油污泥36t,产固体干渣2.6t。原料处理量4t/d,产渣量70kg/h。
根据2010年至2011年现场生产运行报表数据,由于设备部分功能、设施不完善,产出部分干渣含油超标,高达4.2%;燃气单耗标准体积Vn为180.5~459m³/t。通过手动调试运行能耗可将控制在较低水平,产干渣量0.07t/h,但未达到0.5t/h的设计要求。
3.2 处理效果
处理后产出物指标:原油含水≤0.5%;残渣含水≤10%;残渣含油≤0.3%,符合GB 4284-84《农用污泥中污染物控制标准》中有关规定。
3.3 运行成本
含油污泥脱水处理、超热蒸汽喷射处理运行成本:电按0.51元/kW·h计,水按2.00元/m³计,燃气按1.14元/m³计。经核算后,处理含油污泥成本为295.63元/t(不含折旧费)。
4 结语
超热蒸汽喷射技术应用于吉林油田污泥处理工程,处理效果较好。但是,由于设备本身零部件质量、控制系统稳定性等存在一些问题,直接影响了处理效果,增加了处理成本。今后还需要对该设备做进一步调试、改造,使该技术在吉林油田得到进一步推广应用。