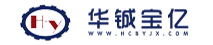
1 项目研究的目的及意义
含油污水处理站普遍采用重力沉降→压力过滤流程,该流程具有建设费用小、运行成本低、操作简单等优点。但因其依靠重力分离原理,导致污水中大量悬浮固体和杂质在沉降设备中沉积形成细颗粒油泥,占据沉降设备的有效沉降空间,从而影响沉降设备的分离效果和运行效率;积存的细小颗粒油泥还会随反冲洗水在系统内恶性循环,对水质造成二次污染,加重了设备的运行负担,严重影响水质的稳定达标。
目前,沉降设备内虽均设有静压穿孔管和泵吸式排泥等工艺,但排出的油泥含水率在99.0%以上,排出油泥量占处理量的3%~6%,存在含水率高、排液量大、后续集中处理费用高、运输过程中易产生二次污染等弊端。现阶段各污水站基本采用储泥池沉降、上清液回收的浓缩工艺。但由于沉降设备排出的油泥成分多而复杂、乳化充分、密度差小、再次沉降困难;大量油泥露天置于储泥池中容易腐败和产生恶臭,污染空气和站库周围土壤环境;而且受气候温度影响,该流程冬季无法运行。通过对低速叠螺污泥脱水机污泥稠化处理工艺进行了现场调研和试验分析,确定运行方案,为完善污水处理系统实时在线排泥及浓缩稠化提供有效的技术手段。
2 细颗粒在处理系统内沉积及分布
由于污水处理站各处理单元对悬浮固体的去除效率不同,因此对某含油污水处理站各节点水样进行化验,分析悬浮固体的分布情况。
根据检测数据,22.56%的悬浮固体在沉降设备中沉积;58.94%的悬浮固体被过滤设备截留。从上述分析可见,污水处理系统中含油污泥主要沉积在沉降罐并在过滤设备中截留。其中过滤系统截留所占比例较高,大量被截留的细颗粒油泥随反冲水进入回收水池,但受排泥工艺、回收水池构造等因素影响,这部分细颗粒油泥不能及时去除,只能随反冲洗水回到沉降罐中再次沉降或在系统内反复循环。因此,从现阶段已建成污水处理系统工艺分析,原水中的悬浮固体及杂质无论是靠自重沉降,还是被过滤罐截留,沉降罐是细颗粒油泥 可以稳定沉积的场所。
3 叠螺污泥浓缩脱水机现场试验
叠螺污泥浓缩脱水机由固定环和游动环相间排列,螺旋推力轴贯穿其中构成,分为浓缩区和脱水区。
(1)工作原理。加压后的油泥进入叠螺脱水机计量槽,通过计量槽限制其进入混合槽的流量;加药系统按设定量向混合槽内投加絮凝剂,并通过搅拌与油泥中的细小悬浮固体充分作用形成絮状体;含有大量絮体的污泥进入叠螺主体,受自身重力和螺旋轴距不断收缩积压作用,大部分污水通过游动环和固定环相对运动时排出;螺旋推力轴将被截留的絮体推送到污泥脱水区,通过背压板调压,使滤饼含固量不断提高,污泥不断受挤压脱水排出。
(2)现场流程。沉降罐底部污泥由排泥泵增压输送至叠螺污泥脱水机,经过浓缩稠化后,液相回流至站内储泥池,浓缩后的污泥装车外运。
(3)效果评价。调研地点为大庆油田污水处理站,试验处理规模为10m³/h(进液量),有机絮凝剂加药浓度为20mg/L。从试验数据可知,沉降罐排出的油泥含水率在99.00%以上时,经叠螺脱水机浓缩稠化后,得到的泥饼含水率为50.00%~70.00%,油泥体积缩减98%以上。另外,浓缩后污水悬浮固体含量在250mg/L以下时,污泥中油类物质含量为9.50%~40.20%,含油量较高。
(4)工艺特点。叠螺污泥脱水机工艺占地面积小、系统构成简单、故障率低、检修方便;设备运行无噪音、无震动,不会影响员工身体健康;属转速运行状态,不存在危险性;无滤布、滤网设计,永不堵塞,停产时不需清洗内壁。但对药剂依赖程度大,针对不同污泥需筛选合理的药剂种类和投加浓度,浓缩后污泥中含油量比例高,适用于低含油污泥的浓缩处理。
4 认识及结论
(1)沉降设备外排细颗粒油泥经上述两种浓缩稠化工艺处理后,污泥含水率可由99.0%降低至70.0%以下,污泥体积缩减98.0%以上,处理费用降低80.0%以上,为进一步深度无害化处理奠定了基础。且浓缩稠化后污水中含固量在250mg/L以下,满足污水处理系统进水指标要求。
(2)油田污水处理系统中含油污泥主要来自沉降沉积的污泥,以及过滤设备截留的杂质,含水率通常在99.50%左右;受现阶段排泥工艺、回收水池构造等因素影响,沉降罐是细颗粒油泥 可以稳定沉积的场所。
(3)污泥稠化技术的应用主要的是带来了社会效益,沉积设备底部外排油泥经浓缩稠化后,含水率可由99.0%降低至70.0%以下,体积缩减98.0%以上,解决了污泥沉降浓缩和运输过程中对空气和站库周围土壤环境的污染;同时,还可实现沉降设备的连续排泥,缓解了污泥在沉降设备底部影响分离效果以及在系统内恶性循环造成水质二次污染的问题。