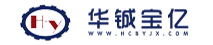
1 前言
在污水处理行业,污泥经浓缩及消化处理后,尚有95%~96%的含水率,体积仍然很大。为了进一步综合利用和处置污泥,必须对其进行脱水处理,提高泥饼的含固率。一般大中型污水处理厂常用的污泥脱水设备有真空过滤机、压滤机和离心脱水机,而离心脱水机因具有连续生产、操作方便、自动化程度高、卫生条件好以及占地面积小等优点,目前应用前景呈日益增长趋势。
某污水处理厂设计规模为12万t/d,采用改良型A2/O处理工艺,处理后的尾水达到《城镇污染物排放标准》(GB18918-2002)一级B标准,剩余污泥经机械浓缩、脱水处理后外运处置。污泥脱水设备选用两台D5LX型离心机,该机型具有双电动机双变频独特结构,达到节能减排的优良功效。
2 离心机介绍与应用
2.1 离心机工作原理
离心脱水机主要由转鼓和带空心转轴的卸料螺旋输送器组成。运行时通过回转体——转鼓和螺旋的高速旋转,使离心机内的固液混合物随之高速旋转,并产生较高的离心力而形成液环。在此高离心作用下,加速固液混合物的沉降与分离。其中,密度较大的固体颗粒沉降在液环层的外圈,即沿转鼓的内壁形成泥环层。转鼓与卸料螺旋旋转方向相同,但两者存在着一定的转速差,由此卸料螺旋将分离出的干泥推出回转体,滤液则通过堰池口导出回转体而排出机外。离心机进料、分离、排出滤液和干泥的工作过程是连续不间断的,且在全封闭环境下进行,污泥、滤液及臭气均不会从机内溢出。
2.2 选型原则
离心机选型的主要依据包含两方面:水力负荷,指单位时间内离心机处理的进料量;固体负荷,指单位时间内离心机处理的绝干物料量。当进料浓度较高(大于1.5%)时主要考虑的因素为固体负荷;当进料浓度较低(小于1.5%)时主要考虑的因素为水力负荷。
此外,对于离心机本身处理能力来讲,其主要影响因素有三方面:直径、长径比和转速。其中前两个因素决定了离心机的外形大小,也即决定了离心机的分离面积和容积。转鼓直径愈大,脱水处理能力愈强,但制造及运行成本都相当高。转鼓长度愈长,污泥的含固率就愈高,但转鼓过长会使性能价格比下降。转鼓转速是一个重要的控制参数,对于相同直径不同的转速,决定了离心机分离因数α的大小。适当控制转鼓的转速,既能获得较高的含固率,又可降低能耗。
2.3 技术参数
污泥处理工艺参数如下:
污泥处理量 | 58m³/h | 进泥固体含量 | 0.6~2% |
脱水后污泥含固率 | >20% | 污泥回收率 | ≥95% |
流量调节范围 | 55~60m³/h | 絮凝剂用量 | 3~5kg/tDS |
离心机性能参数如下:
主机(即装机)功率 | 75kW | 额定转矩 | 7960N·m |
发电机功率 | 15kW | 转鼓内径 | 520mm |
转鼓长度 | 2340mm | 长径比 | 4.5 |
转鼓锥角 | 11° | 额定转速 | 2800r/min |
差速调节范围 | 0~15r/min | 设计转速 | 3200r/min |
2.4 结构特点
(1)双电动机双变频驱动。新型离心机采用独特的双电动机双变频控制技术。转鼓通过差速器带动发电机的转子旋转,当发电机的转子转速超过发电机的同步转速时,发电机开始工作,即发电机转子旋转产生磁场,产生逆变作用,在定子上形成电动势,通过变频器接回到系统中,给主电动机供电,以达到节约电能的目的。因此,离心机的实际正常工作能耗为两电动机之差,一般情况下可节约10%~20%的电能。
同时,采用可靠的双变频控制机械差速装置,通过离心机内泥层的厚度自动调节控制转鼓与螺旋输送器之间的差速,达到自动调节转矩的功能。差速调节精度值为0.1r/min。差速器可通过变频器调节离心机的脱水效果,以适应不同的进泥特性。当进料固相含量低时,选择低差转速以增大转矩;当进料固相含量高时,选择高差转速以减小转矩,使脱水污泥的含固率、固相回收率满足设计要求。
(2)高性能卸料螺旋。卸料螺旋叶片采用中空式设计。中空式设计使得固液分离的方向正好相反,大大减少了对固体层的扰动。实际运行测试表明:在保证污泥回收率的前提下,相对提高出泥的干度1%左右,在保证出泥干度的情况下提高了污泥的回收率。老式卸料螺旋上滤液的排出需经卸料螺旋与转鼓形式的密闭腔沿螺旋方向排出,而高性能卸料螺旋滤液的排出则只需沿轴向直接排出,降低了离心分离后的滤液排出离心机时的阻力及行程。
(3)浓缩脱水一体化。卧式螺旋沉降离心机有且只有两种操作方式:一种是中部进料的操作方式,即逆向式操作(理想状态下固液混合物进入离心机后立即分离,沿相反的方向排出);另一种为端部进料的同向式操作(固液混合物进入离心机后不是立即分离,而是沿着同一轴向方向位移一段距离后,滤液由导流管排出)。一般情况下逆向式操作多用于脱水,同向式操作用于浓缩。新型离心机采用混流技术,可以在同一个卸料螺旋下实现两种不同操作方式,可调节选择的范围更广。
(4)新耐磨设计。有以下两方面改进。
①碳化钨耐磨片。转鼓或螺旋的外缘极易磨损,对其材质应有特殊要求。在耐磨损防护设计上,离心机显著的特点是在卸料螺旋全长方向与污泥接触磨损相对较为严重的部位,全部采用可更换的耐磨片新式结构。此耐磨片表面喷涂碳化钨材料,且喷涂碳化钨层硬度达维氏硬度2000~4000,耐磨性完全达到烧结碳化钨的程度,而且 的焊接工艺确保其不会脱焊,并且每片耐磨片焊接完成后均进行二次焊接强度试验,确保其焊接强度,具有无可比拟的优点。同时卸料螺旋磨损后只需更换耐磨片即可,极大地降低了维修费用。
②耐磨喷嘴。对进料的喷嘴和污泥排出口采用了可更换式的陶瓷碳化钨喷嘴。卸料螺旋上的进料口及转鼓上的进料口均采用可更换式的耐磨衬套,耐磨材料为陶瓷,亦可采用碳化钨材料。同时对出料口的刮泥板亦采用碳化钨结构的耐磨防护措施。
(5)PLC自动控制。离心机对污泥处理全过程采用PLC自动控制,操作、调节灵活,同时为污泥供料泵、絮凝剂制备、加药泵、污泥无轴螺旋输送机和流量计等辅助设备运行提供显示、控制和故障报警,并将模拟信号和数字信号通过现场总线传至中央控制室,以确保污泥脱水系统的安全运行。主要控制功能有:
①离心脱水机、切割机、供料泵、螺旋输送器以及絮凝剂投加泵等的联动控制和保护。
②离心机自动差速及转矩控制系统的调控。
③离心机卸料螺旋转矩过大及差速过低报警。
④离心机紧急停机保护,现场紧急停机按钮。
⑤加药系统在低药剂量、断水和水压不足等情况下报警。
(6)防腐蚀设计。选用全不锈钢结构。离心机的转鼓和卸料螺旋均采用AISI316不锈钢离心浇铸而成,材料密度均匀、刚性强,动平衡性能好。离心机转鼓内壁加工有纵向的沟槽或配有纵向不锈钢条,可以防止固相粒子在转筒内壁滑动而引起转鼓内壁磨损,同时避免泥环随卸料螺旋旋转而不排出。
2.5 应用分析
通过2010年7月试运行表明,D5LX型离心脱水机运行状况良好,处理能力和效果达到了设计要求,可适用不同污泥特性介质,脱水后污泥含水率可以达到77%。
3 结语
综上分析,D5LX型离心机结构特征与其使用工况是一致的。由于采用了双电动机双变频独特设计,处理每吨污水污泥耗电量降低了0.0045kW·h。按设计处理负荷12万t/d计算,每年可节省运行电能202500kW·h,达到了节电、降低污染、提高含固率的目的,真正意义上实现了节能减排综合效益。