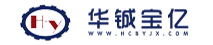
离心力场的创立和运用是科学和技术的成就之一,运用离心力场进行非均相物系的分离是非常有效的。这种分离叫离心分离,它是许多新的工业过程的基础,离心分离装备按有无旋转部件可以分为机身固定的旋转流分离设备和机身旋转的离心分离设备(亦称离心机)。前者如旋流分离器(亦称旋流器),流体在固定的机身内旋转而产生离心力场;后者如各种沉降离心机或过滤离心机,由旋转的机身带动内部流体作回旋运动而产生离心力场。由于前者无运动部件,具有结构简单、设备紧凑、占地面积小和设备成本低等许多优点,受到日益广泛关注。后者可以相当 地,同时迅速地分离极不易分离的非均相液态物系,如原油聚氯乙烯树脂悬浮液等等。
1 离心分离装备
旋转流分离是离心力场在分离科技方面的重要应用之一。旋流分离器(或称水力旋流器)是旋转流分离方面的代表性设备,是一种用途十分广泛的通用分离分级装备。它可用于完成液体澄清、料浆浓缩、固相颗粒洗涤、液相除气与除砂、固相颗粒分级与分类,以及两种非互溶液体的分离等多种过程作业,迄今已经在矿物加工、石油、化工、轻工、环保、食品、医药、纺织与染料、采矿、冶金、机械、材料及煤炭等众多工业部门获得了广泛的应用,而且由于旋流分离器结构及型式的日趋多样化,其应用的领域仍在不断拓展。
离心机是离心分离方面的代表性设备,根据其处理的规模可分为工业用离心机与实验室用离心机。工业用离心机处理量大,而实验室用离心机处理量相对地小,但分离效果好;离心机又可以分成生产用和分析用。作为一种工艺设备,生产用离心机的较有代表性的标志是分离原理、工艺用途、过程的进行方式(连续的或间歇的);根据渣的卸出方法离心机可分为人工卸料离心机、螺旋卸料离心机、料斗卸料离心机、重力卸料离心机、脉动活塞卸料离心机、活塞推料离心机、惯性力卸料离心机、刮刀卸料离心机、机械气动和液力卸料离心机等等。
由于离心机在各个技术领域都有广泛的使用。现只探讨化工工业部门和相关部门使用的离心机。根据分离原理,分为过滤式离心机、沉降式离心机和组合式离心机。
过滤离心机可供在要求滤渣深度脱水和高度洗涤时分离悬浮液用,以及供压滤其孔隙完全或部分为液体所填充的非流动物料用;沉降离心机既可用于分离易于过滤的悬浮液,又可用于分离不易过滤的悬浮液。
离心机的结构特征是:轴的配置、轴的支座装置、卸渣方法、密封程度和防爆等级。
1.1 过滤离心机
三足式离心机是数量较多,用得较广泛的一种过滤离心机,采用离心过滤机过滤含有很小颗粒的悬浮液时,通常需用滤布作过滤介质,同时要求滤饼对滤布不发生相对运动。显然,满足这些要求的较简单的一种离心机为三足式离心机。它具有竖轴、实底和半封闭顶的圆柱状转鼓,顶部的围边称为鼓缘,转鼓支在三足架上,故名三足式离心机。
在一般情况下,转鼓罩面上钻有很多小孔,内侧覆有一层或多层大孔金属滤网,作为装在转鼓中的裳状滤布的支撑。在启动前或启动后,将悬浮液自顶部导入转鼓,使滤液通过罩面流出,而团体颗粒则被截留在滤布上。
一般情况下滤渣是在停机之后用人工移出或采用更换滤布袋的方法进行卸料的。比较 的一种三足式离心机使用时可先将转鼓的转速降至每分钟几转,然后将一犁形刀片推入滤渣以排除固体物料。犁形刀将固体翻向转鼓轴线,使滤渣从转鼓底部开口处落出,借助于定时器,全部操作均可自动进行。
1.2 沉降式离心机
1.2.1 螺旋卸料沉降离心机
高速旋转的无孔转鼓内有同心安装的输料螺旋,转鼓与输料螺旋同向旋转,但两者之间有一定的转速差,该转速差由差速传动系统产生。悬浮液经中心的加料管进入转鼓,悬浮液中大部分固体颗粒在离心力作用下沉降到转鼓内壁并被输料螺旋推送而从小端排出转鼓,澄清后的液体从转鼓另一端的溢流口排出。
螺旋卸料沉降离心机的主要操作参数为:转鼓转数,转鼓与输料螺旋间的转速差,溢流口位置和进料速度;主要结构参数为:转鼓大端内直径D,转鼓长度L,转鼓长径比L/D,转鼓半锥角,以及输料螺旋的螺旋头数和螺距。
螺旋卸料沉降离心机的主要优点:自动连续操作,不需用滤布,能长期连续运行,维护简便;应用范围广,可用于固体脱液,液体澄清,固体颗粒按粒度分级,以及用于液-液-固分离;对物料的适应性好,能分离的固体粒度的范围0.005mm~2mm,悬浮液的体积浓度范围2%~40%。浓度波动对分离效果的影响不大;结构紧凑,容易实现结构上密闭,密闭式机器可在一定的正压下操作;单机生产能力大(大型机可达190m³/h),操作费用低,占地面积小。
螺旋卸料沉降离心机的缺点是:沉渣的含液量一般较高;虽能对沉渣进行洗涤,但洗涤效果不好;结构较复杂,机器造价较高。
1.2.2 碟式分离机
分离机是沉降式离心分离中的一种类型,用于分离难分离的物料。分离机中的碟式分离机是应用较广泛的沉降式离心机。可以完成分离和澄清两种操作。
碟式分离机是立式离心机,转鼓装在立轴上端,通过传动装置由电动机驱动而高速旋转。转鼓内有一组互相套叠在一起的碟形零件——碟片,碟片与碟片之间留有很小的间隙。悬浮液(或乳浊液)由位于转鼓中心的进料管加入转鼓。当悬浮液(或乳浊液)流过碟片之间的间隙时,固体颗粒(或液滴)在离心力作用下沉降到碟片上形成沉(或液层)。沉渣沿碟片表面滑动而脱离碟片并积聚在转鼓内直径大的部位,分离后的液体从出液口排出转鼓。积聚在转鼓内的固体在分离机停车后拆开转鼓由人工清除,或通过排渣机构在不停车的情况下从转鼓中排出。
碟式分离机主要的操作参数为:转鼓转数,轻液转速,轻液与重液分界面的位置,加料速度等;碟式分离机的主要结构参数为:转鼓内直径,当量沉降面积,碟片的尺寸与碟片总片数,排渣方式及排渣机构。
碟式离心机结构紧凑,占地面积小,生产能力大,适于液-固也适于液-液分离,因而在化工、医药、轻工、食品、生物工程以及交通运输部门都获得广泛应用。碟式分离机的缺点是结构复杂,转速高,因而操作和维修保养的要求比较高,另外清洗较麻烦。
1.2.3 室式分离机
室式分离机是应用比较广泛的离心沉降设备,用于分离固体含量在2%以下的悬浮液,其结构除转鼓外其余部件(如传动机构、机座、测速装置、制动器等)与碟式分离机基本相同。
室式分离机的转鼓中,一组同心的分离圆筒将转鼓内空间分割为多个互相串联的室(即环形空间),转鼓内空间一般按照各室的径向间距相等或各室的横截面积相等的原则分离。欲澄清的悬浮液进料管加入转鼓中心,然后由中心向外逐一流过各个室,液体在各室中的流速逐渐减小(在各室的径向间距相等时)或保持不变(当各室横截面积相等时)。由中心向外由于半径不断增大,各室分离因数越来越大,故较大的固体颗粒沉积在位于中心的 室内壁,较细的固体颗粒在外面的各室沉降。澄清后的液体用向心泵排出转鼓,排出压力可达0.28MPa。室式分离机由于转鼓内安装了同心的分离圆筒,缩短了固体颗粒的沉降距离并扩大了沉降面积。与碟式分离机相比其结构较简单,转鼓内的零件少,转鼓容纳沉渣的空间较大,可用来分离固体含量稍高的悬浮液,且排除沉渣和清洗转鼓也比碟式分离机方便。
1.2.4 管式分离机
管式分离机的分离因数很高,一般在13200~50000;结构小巧紧凑,是应用很广的沉降式高速离心分离设备。管式分离机为立式结构,可分为澄清型和分离型两种。澄清型用于含少量固体的悬浮液的澄清,悬浮液从转鼓下部进入转鼓,在由下往上的流动过程中,所含固体颗粒沉积在转鼓内壁,清液从转鼓上部溢流排出。分离型用于乳浊液的分离,乳浊液在离心力作用下分成重液和轻液两液层。
管式分离机适用于固体含量低于1%、固体颗粒小于5μm以及固体与液体的密度差很小的悬浮液的澄清;也适用于轻液与重液的密度差小于分散性很高的乳浊液的分离。管式分离机结构较简单、体积小、运转平稳,且分离因数很高,能分离难分离的物料,因而广泛应用于化工、制药、生物制品的生产、制漆、植物油精制以及矿物油加工等工业部门。
主要用途:分离固体含量低的粘性悬浮液,如清漆、果汁、细菌培养液等的澄清;将悬浮液中的固体颗粒按大小分级,如搪瓷原料用管式分离机分级以清除其中的杂质;分离难分离的乳浊液,例如从植物油、鱼和动物脂肪以及矿物油中分离出水分;用于高分散物系和胶体物系的分离和粒度分布。
管式分离机主要缺点是间歇操作,转鼓容积小,为避免频繁地停机清除沉渣,用管式分离机分离的物料其固体含量不要超过1%。
1.2.5 撇液管式沉降离心机
撇液管式沉降离心机为间歇操作沉降离心机,其特点是在转鼓卸除沉渣之前先用撇液管撇除沉渣层上面的液体,使沉渣与液体分离。撇液管式沉降离心机主要有三足式沉降离心机和卧式刮刀卸料沉降离心机两种。
2 离心分离设备新进展及其展望
离心机发展到现在产品已经程式化,但是随着新的材料及技术的出现,离心机的发展出现了一些新的趋势。
2.1 新材料的应用
2.1.1 玻璃钢材料的应用
玻璃钢是玻璃和树脂组成的复合材料,虽然玻璃和树脂的韧性和强度都不高,玻璃钢却有很高的强度和韧性,而且耐腐蚀性能好,重量很轻。所以玻璃钢发展很迅速,已成为一种重要的工程结构材料,使机器构件不用金属成为可能。由于玻璃钢有强度高、耐腐蚀的性能特点,可以考虑用玻璃钢来制作离心机转鼓。这是因为玻璃钢的高强度,满足了在高速旋转情况下转鼓对强度的要求;玻璃钢的耐腐蚀性保证了一般情况下转鼓直接与物料接触也不会被腐蚀。用玻璃钢制作离心机转鼓不仅可行而且还具有许多金属材料所不具备的优点:由于玻璃钢的密度约只为不锈钢的1/4,同样大小的玻璃钢转鼓的质量远远小于不锈钢转鼓的质量,而转鼓自身的质量所引起的应力约占总应力的一半左右,所以玻璃钢转鼓的总应力大大降低了。并且在总消耗功率中占相当大比重的离心机的启动功率也与转鼓质量(密度)成正比,降低了转鼓的密度,就意味着降低了功率消耗,所以玻璃钢转鼓节省了能耗。
除此之外,因玻璃钢满足了离心机机壳对优良的耐磨性(以承受强力冲刷)的需要,故它还可用来制作离心机的机壳。例如在三足式离心机中,转鼓的转速可达750~2000r/min,抛出的液体对壳体内壁有很强的冲击力,如果接触的介质腐蚀性不很强,可选用通用不饱和聚酯做基本材料,增强材料外层采用表面毡,其余均采用中碱玻璃纤维布铺覆和短切玻璃纤维纱喷射交替成形并在内表层加入氧化铝粉末以增加其耐磨性。
2.1.2 工程塑料的应用
工程塑料发展历史较短,但由于质轻、节能、强度高、耐腐蚀等特性,几十年来发展迅速。如今已经出现比钢材硬,强度超过钢、钦的塑料。在氟塑料品种中,产量较大,用途较广的是聚四氟乙烯(PTFE)。PTFE具有较低的摩擦系数和特异的自润滑性,有卓越的耐药品性和耐溶剂性,酸、碱、溶剂对它均无侵蚀。
卧螺离心机的径向滑动轴承是一种非自润滑轴承,常用的轴承材质是ZQSnlo-1,一般在有润滑条件下才能正常工作,否则就会发生轴瓦与轴颈的“干磨”现象,轴瓦与轴颈都会受到比较严重的损坏。而这是卧螺离心机在高负荷运行条件下,停机检修的主要原因。
因此,为了保证在润滑条件不良情况下离心机能正常的高负荷运转,必须对滑动轴承的材质进行改进。通过对多种材料的性能比较,结合常压离心机的工作特点(径向载荷较大),选择了以聚四氟乙烯为主要成分的复合材料,又添加了一定量的碳纤维、青铜粉、二硫化钥、玻纤,以增加其强度、硬度、自润滑性、耐磨性能等。由于PTFE材料不仅自润滑性能好,而且其减震性能也较好,设备在运行时振动也相应降低,保护了轴颈,大大减低了备品配件的消耗。除此外,PTFE径向滑动轴承的使用,延长了设备的运行周期,避免了因经常性停机而造成的产量的降低。
聚四氟乙烯还可以用于卧螺离心机螺旋叶片的制造。螺旋叶片的耐磨性关系到螺旋输送器的寿命。以聚四氟乙烯为基材,填充高分子粉或合金粉和氧化物等材料,采用粉末冶金烧结成型的螺旋叶片,其耐磨性很高,年磨损量只有0.002-0.004mm,超过了采用硬质合金来硬化后的螺旋叶片的耐磨性。
2.1.3 硬质合金的使用
作为刀具材料使用的碳化物基金属陶瓷常被称为硬质合金。硬质合金的硬度很高,耐磨性很好,强度和韧性都较好,适于做切削刀具、表面耐磨材料以及某些高刚度结构件。
硬质合金的优异性能,可以充分利用在螺旋卸料离心机上。螺旋输送器是螺旋卸料离心机的主要部件,它的寿命取决于螺旋叶片的耐磨性。螺旋叶片磨损较严重的地方是它的顶部。它磨损后,通常使螺旋的输渣能力降低,含渣量增大,所以要求叶片材料有高的硬度和耐磨性。常用的方法是在螺旋叶片表面堆焊硬质合金或在叶片上喷涂硬质合金或采用可更换的耐磨的硬质合金叶片。
硬质合金也适于做刮刀离心机的刮刀片。因为刮刀片工作时不仅受到剧烈的磨损和冲击载荷,而且长期与有腐蚀性的介质接触,所以要求刮刀片应具有耐磨、机械强度高、耐腐蚀等性质。目前国外使用的刮刀材料多为耐磨、耐腐蚀的高镍铬硬质合金,如ElcomatK,其成分大约为Cr24%,Ni20%,Cu3.5%,Mo2.0%,Si1.25%,Mn6.3%,C≤0.13%,每把刮刀可连续使用刮削硫钱2000吨左右,磨损后经修理刨平能修复使用4-5次。其效果比采用Icr18Ni9为好。有的使用堆焊硬质合金及镶陶瓷片,使用寿命可以提高5-6倍。
2.2 一些新式离心机
由于离心机发展和应用了很多年,如上文所提到的离心机在理论上和技术上已经很难有改进的空间,但是近年来出现了一些新式离心机,推动了离心机技术的进一步发展。
2.2.1 盘栈式离心机
Plat设计开发了一套垂直的板取代盘栈。该型离心机构造可使临界分离粒达到2μm。但远低于该值是不切实际的,因为要实现这一极低值必然对应着极低流量,这会使分离工艺毫无价值。
在板式分离器的分离腔里,流动油滴从入口到出口与连续水相具有相同的水平速度,由于油水间的密度差,油滴有一垂直速度,因而它能到达顶部并与其它油滴聚结而实现分离。
2.2.2 新型卧式螺旋离心机
卧螺式离心机近年来也有发展。如日本三菱公司生产的带有沉降叶片的卧式螺旋卸料沉降离心机,由于沉降片分离板的存在使它的分离性能介于碟片式离心机和卧式螺旋卸料沉降离心机之间,它可以分离出粒径为0.5μm的微粒,分离后滤渣含固率亦较高,已应用子氧化钦的分级、超细铁氧体的洗涤和浓缩、食品工业及城市污水处理的剩余活性污泥脱水中。德国Flottweg公司生产的新型卧式螺旋卸料沉降离心机分离因数已可达5000。
3 总结
离心技术发展和离心机的应用已经有几十年的历史,通过对离心分离理论的再挖掘以及新材料和精密加工工艺的出现,离心机的性能得到进一步的提高,其应用范围也将会进一步的扩大。离心机在工业生产中将会起到越来越重要的作用。