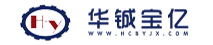
随着国民经济的快速发展,各个行业对石油资源的需求都急剧增加。据报道,2003年我国的石油消耗量达到3亿t,超过日本称为 第二大石油消费国。石油使用量的增加必将导致含油废水及含油污泥排放量的快速增加。我国石油石化行业中,平均每年产生80万t罐底泥、池底泥和高达数百万吨的隔油池底泥、浮选池浮渣等含油污泥,通常其含油率、含水率分别在10%~50%和40%~90%之间,并混有一定量的泥、砂、无机矿物质、重金属等物质。石油是由非水相或憎水化合物如烷烃、烯烃、芳香烃、沥青等组成的混合物,这些物质大多具有一定的毒性并具有致突变和致癌作用。含油污泥处置不当会造成地下水、土壤、大气的环境污染,从而对人类健康和生态安全造成威胁。
近年来,随着环保意识的增强,我国在含油污泥处理处置方面的研究开始获得重视,为增进对含油污泥处理与处置技术的发展状况的了解,本文回顾了国内外近10年来炼油厂含油污泥处理和处置上所采用的相关技术。
1 从含油污泥中回收石油技术
含油污泥中含有大量石油烃类等有用物质,经过处理可以回收利用,这样不但减小了含油污泥的不良环境影响,还能带来一定的经济效益。从含油污泥中回收石油的方案主要有热处理技术、溶剂萃取技术、冻融技术。
1.1 热处理技术
热处理技术又可以分为热解、有氧热处理、化学药剂辅助热处理技术。热解是指在无氧条件下加热含油污泥,使烃类物质及水蒸发出来,废油得到回收。有氧热处理技术是指在有氧条件下加热含油污泥,回收废油。化学药剂辅助热处理技术是通过添加化学药剂,在加热条件下处理污泥,通过改变油分的物理状态和油分与污泥的结合方式以提高油的回收率。
1.1.1 热解
根据加热温度的不同,热解技术可以分为低温蒸馏技术和高温裂解技术。低温蒸馏技术可以回收分子量较低的轻石油,而高温裂解技术,可通过大分子的油的裂解转化,使其中的油分得到蒸发回收。
低温蒸馏技术的温度往往为230~270℃,由于处理温度较低,油泥中的油分并未发生剧烈的分解,轻石油主要通过蒸馏作用从污泥中逸出得到回收。以该法处理含油率为45%的污泥时,油回收率可达到97.4%。此过程中废油不氧化、不分解、不炭化,保证废油的品质。但这种处理方法主要集中在回收轻石油上,对于重油的回收很少,对含油污泥的回收和环境危害的降低有一定局限。
高温热解技术的处理温度一般高达460~650℃,污泥中的油类可以得到70%~80%的回收。含油污泥经过高温裂解,可获得商业用机动车燃料和粗汽油。若将干燥和高温裂解技术结合起来处理含油污泥,产油率达到35%;若在流化状态、460~650℃下处理含油率为30~35wt%的污泥,污泥中的油分可以得到70%~84%的回收;若在搅动的状态、550℃下处理含油污泥,油泥中的油也可得到30%左右的回收。反应过程中若添加适量的催化剂和添加剂可以缩短裂化时间、降低裂解温度、增加污泥的裂解能力、减少固体残留物,有研究表明,在含油污泥中添加铝化物和铁化物、钠盐和钾盐、以及飞灰、油泥灰、DAY沸石废物、废聚乙烯醇聚合物(PVA),可较大地提高油的转化率,有效地提高裂解油的质量和产量。
热解技术在回收污泥中油分的同时,还可以使含油污泥中重金属和放射性物质含量明显降低。但这种方法目前成本较高,能否产业化应用,有待进一步研究。
1.1.2 有氧热处理
有氧热处理技术可以提高废油质量,减少剩余污泥含量,在较高的氧浓度下可以提高含油污泥的有氧热分解速度。如果含油污泥含水量大,还可以实现较好的油水分离。有氧热处理过程是放热的,可以为吸热的热解反应提供热能,减少了能源的消耗。目前,该技术在台湾已经有产业化应用。
1.1.3 化学药剂辅助热处理
化学药剂辅助热化学处理处理法往往可以达到较好的油回收效果。针对不同物理化学性质的污泥,需要选取不同的化学药剂和确定合适的添加量,热处理的温度也会有所差别。当污泥比较粘稠时,可以投加稀释剂。采用此法对含油率为46.7%的污泥进行处理,当回流温度为80℃,稀释倍数为2时,油回收率可以达到95.6%。当污泥处于乳化状态时,需要投加破乳剂或碱液等洗涤剂,有报道显示,用该方法可将含油率为29.0%的含油污泥洗涤至残油含量为2.7%,污油回收率可以达到92.2%;也有研究表明,采用该原理处理41.89%的含油污泥时,油回收率甚至可高达95%~98%。
化学药剂辅助热化学处理技术简便、快速,但往往还需要与机械分离装置联用,方可达到较好的油泥分离效果;还会产生污水,需要进一步的后续处理以减少对环境的危害。
1.2 溶剂萃取法
溶剂萃取法是基于相似相溶原理,利用萃取剂把有机废物从污泥中抽提出来,通过蒸馏把萃取剂从混合物中分离出来循环使用,剩余的废油得到回收利用。萃取剂包括有机溶剂和超临界溶剂。
萃取技术若与其它技术联用,可以取得较高的油分回收率。将萃取剂与稀释、添加抗絮凝的分散剂、机械分离方法相结合处理含油污泥,可取得98%的油回收效果;采用萃取和低频声波相结合,与加热、溶解相结合的方法处理含油污泥,都可以得到很好的处理效果。如采用三氯甲烷作为萃取剂,在320~480℃、0.2MPa压力条件下处理含油污泥,可取得80%~95%的脱油率。
溶剂萃取法具有工艺过程简单、快速、选择性高等优点。但是萃取剂费用较高。
1.3 冻融技术
冻融技术本是污泥调理的常用方法,应用于含油污泥的处理中,能够改变污泥中的毛细管结构,从而提高了污泥的脱水性能,同时也可改变油泥中油对矿物颗粒的附着性能。含油污泥经冻融法处理后,可出现明显的分层,即上面的油层、中间的水层和底部的矿物泥层。从目前报道的研究结果来看,经过简单的冻融处理可使污泥中50%~60%的废油得到有效回收,并可以明显的改善污泥的过滤性能。冻融技术若辅以其他方法,可进一步提高油的分离性能,如污泥冻融后再经微波辐射方法处理,可使废油的去除率达到90%。
然而,冻融技术只适合于一定类型的含油污泥,和一定地区应用。对于北美、加拿大、中国的北部地区,具有结冰季节的地区,这种方法是简单适用,经济可行的。但对于不具备自然低温条件的地区,这种方法的优势就不那么明显了。
2 含油污泥的处置技术
当含油污泥中含油率较低,回收利用价值较低时,可以采用生物技术、焚烧、稳定化/固化等方法进行处置,把含油污泥对环境的不良影响减小到较低。
2.1 生物技术
生物技术是通过微生物的生长、繁殖及内源呼吸使原油等污染物逐步矿化,生成二氧化碳、水、氨和磷酸根等,消除原油的污染。含油污泥中本身会存在一些对油类具有降解能力的微生物,可以降解含油污泥中多种芳香烃;这些微生物可以通过分离、纯化、驯化,强化其石油降解功能,得到具有高效降解石油的微生物。
为提高油泥中原油的降解效果,在油泥中投加对油类具有降解能力的外源微生物也是必要的。在25~55℃,向含油污泥中添加水和菌种,原油可以得到高效的降解。在间歇式系列反应池中投加对油类具有降解能力的微生物菌株,油泥经过2周的处理,其中的烃类物质得到降解,含量从20000ppm减少到100ppm。
在油泥生物处理中,为维持微生物的正常生长和繁殖,保证微生物对油泥中油的快速降解,还需要投加一些特定的微生物营养物质,如木屑或麦秆、砂子、木屑,磷酸盐、硝酸盐,鼠李糖、脂生物表面活性剂和磷钾溶液等。据报道,采用这种方法处理含油污泥,处理率可高达90.2%。
生物技术具有低成本、高效率、操作和设计简单,环境友好等优点,是未来处理石油污染的一种主要技术。但是生物技术往往处理周期较长。
2.2 焚烧
焚烧是现在含油污泥处理的重要的处理处置方法之一。可以实现减量化、无害化的固体废物处理要求。焚烧温度大多为1073~1173℃。常用的焚烧设备包括流化床燃烧、循环液化床燃烧、窑、回转炉、阶梯式炉等。采用流化床焚烧炉对含油污泥进行处理,可以把污泥中大部分有机组分转化为无害的CO2和水。燃烧效率和焚化效率分别可以达到98%和99%。
焚烧可以很好的降低含油污泥的体积和毒性,但价格昂贵,设备腐蚀往往比较严重,在焚烧中,一般还需要添加燃料支持燃烧,并需要配套的空气处理装置来减少空气污染。
2.3 稳定化/固化
利用固化剂将含油污泥中的有害物质(污油、有害气体等)固定或锁在惰性物质中,使有害物质渗透性和溶出率大大降低,并具有一定的机械强度,便于堆放,不泄露污染物,达到环保要求。根据采用的固化剂的不同可以分为水泥固化和石灰固化等。稳定化/固化技术对处理含油污泥是有效的,固化产品符合环境要求。添加合适黏合剂,与固化剂联合使用,也可以取得很好的固化效果。但这种处理方法成本较高。
2.4 填埋
填埋是一种广泛使用的有效处置固体废物的方法,具有处理成本低、运行稳定的优点。目前,我国油田原油加工过程中产生的污泥,大多采用填埋的方法进行处置。含油污泥在进行填埋前,需要经过脱水脱油等处理,以较大幅度地减少运输量与填埋占地面积、满足填埋场土力学要求。但含油污泥中石油类物质的含量往往超过填埋标准(<3%),限制了填埋方法的使用。如果含油污泥稳定不完全,填埋是存在风险的,很可能污染地下水和土壤,并威胁人类健康。所以对含油污泥进行填埋处置之前,必须做必要的处理,使其达到填埋要求。
3 含油污泥的综合利用技术
含油污泥综合利用技术有效利用了含油污泥,变废为宝,是一种有效、环境友好处理危险废弃物的方法,同时可以取得良好的经济效益。主要的综合利用技术包括含油污泥的建材利用、含油污泥制燃料、含油污泥的焦化处理,以及一些其它的利用方法。
3.1 含油污泥建材利用
含油污泥建材利用是一种实用性的污泥利用发展方向,它可以广泛应用于砖、水泥、陶粒、活性炭、熔融轻质材料以及生化纤维板的制作。但目前,含油污泥建材利用大多处于研究及尝试的阶段。
含油污泥可以代替制砖原材料(泥、沙和水)制造砖块,并且在烧结过程中,废油燃烧放热,可以减少烧砖所需的燃料。含油污泥中所含的重金属在玻璃化过程中得到固定,毒性实验满足EPA标准。采用含油污泥焚烧后的焚烧灰制砖块也取得了成功。采用含油污泥作为原料生产水泥,在烧结过程中,油类物质得到蒸发和完全燃烧,水泥成品基本满足各项要求。但由于含油污泥中矿物质含量的不同,烧制出来的水泥性质也有所差异。此外,利用含油污泥制造混凝土以及陶瓷等方面,也有成功的试验报道。
3.2 利用含油污泥制燃料
含油污泥中含有大量的废油,具有较高的热能,经过一定的处理,可以作为燃料使用。如将含油污泥进行干化处理后,可作为锅炉燃料使用。把含油污泥和其它废物或燃料混合可以制成满足各项要求的固体燃料。如将含油污泥与工业废物混合可制成固体燃料。含油污泥与煤按一定比例混合进行焚烧,经检测,锅炉的烟气及炉渣满足环境标准。含油污泥制燃料,不但可以有效的保护环境,还可以获得高热量的固体燃料,经济可行。
3.3 焦化处理
焦化处理含油污泥实质就是对重质油的深度热处理,其反应是一个烃类物质的热转化过程,即重质油的高温热裂解和热缩合。在温度为490℃,反应时间为60min时,对含油污泥进行焦化处理,可获得88.23%的液相产品回收率,产品主要为汽油、柴油和蜡油。通过添加强效添加剂和炭化添加剂,在焦化温度为400℃,反应时间为80min的条件下,可以把含油污泥制成净化效果较好的吸附剂。
焦化处理不但有效利用了含油污泥,而且是一种有效、环境友好处理危险废弃物的方法,并且经济效益良好。
3.4 其他利用
含油污泥的资源化途径很多。含油污泥经过分离后,可分成废油、含油液体和固相沉积物,这些分离相可作为特殊的添加剂用于混凝土用水、建筑、油漆的添加剂等使用;含油污泥还可以与环氧树脂、聚乙烯、苯胺产品蒸馏液混合,用做阻塞沟和道路裂缝的防水物质,这种防水物质对混凝土表面的黏附力有所提高。
此外,石油冶炼厂的含油污泥经纯化后可以代替芳香油作为天然橡胶和苯乙烯/丁二烯橡胶配方的工艺油。含油污泥对于混合物的特性和硫化作用的物理组分没有不良影响。并且与芳香油相比,含油污泥的添加使得较佳硫化时间明显减少,抗老化能力、橡胶张力和撕拉力提高。
4 结语
含油污泥的处理处置方法很多,每种方法都有各自的优缺点和使用范围。含油污泥成分复杂,各种物理化学和生物化学性质都有所不同,所以在实际应用过程中要根据含油污泥性质和经济技术条件选择合适的处理处置方法。对于含油量较大的含油污泥要着重考虑采用热处理、溶剂萃取和冻融等技术对污泥中油分的回收,减少其对环境的危害的同时,又实现了对有用物质的回收,经济效益可观;经济技术条件允许时要强化含油污泥的综合利用,采用含油污泥制建材、燃料和进行焦化处理等,变废为宝,实现环境效益和经济效益的双赢,实现含油污泥处理的资源化;采用生物处理技术、焚烧、固化/稳定化和填埋等处置技术把含油污泥的环境危害性降低到极小,实现含油污泥的无害化。另外积极寻求含油污泥多种利用途径,彻底解决其污染问题,探索经济和环境上可行的方法仍旧是以后研究的热点。