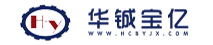
1 含油污泥的来源、性质及危害
含油污泥是石油生产的伴随产品,也是石油产业的主要污染源之一,它是影响油田及其周边环境质量的一大难题。含油污泥是一种极其稳定的悬浮乳状液体系,含有大量老化原油、蜡质、沥青质、胶体、固体悬浮物、细菌、盐类、酸性气体、腐蚀产物等,还包括生产过程中投加的大量凝聚剂、缓蚀剂、阻垢剂、杀菌剂等水处理剂。
1.1 含油污泥来源
1.1.1 原油开采过程
原油开采过程中产生的含油污泥主要来源于地面处理系统,采油污水处理过程中产生的含油污泥,再加上污水净化过程中投加的净水剂形成的絮体、设备及管道腐蚀产物和垢物、细菌(尸体)等组成了含油污泥。
1.1.2 油田集输过程
含油污泥还可能主要来源于接转站、联合站的油罐、沉降罐、污水罐、隔油池底泥、炼厂含油水处理设施、天然气净化装置清除出来的油沙、油泥,钻井、作业、管线穿孔而产生的落地原油及含油污泥。油品储罐在储存油品时,油品中的少量机械杂质、沙粒、泥土、重金属盐类以及石蜡和沥青质等重油性组分沉积在油罐底部,形成罐底油泥。此外一次沉降罐、二次沉降罐、洗井水回收罐的排污也可产生含油污泥。
1.1.3 炼油厂污水处理过程
炼油厂污水处理场的含油污泥主要来源于隔油池底泥、浮选池浮渣、剩余活性污泥等,通常简称为“三泥”,它主要由固体物、油及水组成,其中“油”泛指各种有机化合物,包括多种有毒有害、难生物降解的物质;固体物中含有多种重金属化合物、焦粉及催化剂粉末,经化学调质破乳——离心脱水后的产物仍为油-水-固三相混合物,含水量在75%~90%之间通常含油率在10%~50%之间,同时伴有一定量的固体。
1.2 含油污泥的性质
油泥是一种组分复杂的棕黑色粘稠状物质,主要由水、泥沙和矿物油三部分组成,水、油和泥沙呈现一种非常稳定的悬浮乳化状态。油泥中的水可分为四类,即游离水、絮体水、毛细水、粒子水。存在于污泥絮体空隙之间的游离水,借助污泥固体的重力沉降可部分分离出来絮体水附着在絮体网络内部,只有靠外力改变絮体结构才能部分分离毛细水黏附于单个粒子之间,必须施加更大的外力使毛细孔发生变形才能部分去除。油泥中的油可分为可浮油、乳化油、溶解油等,其中乳化油占很大的比例,这是油泥粘度大、难于脱水处理的主要原因。油泥中的污泥颗粒和微细沙粒都带负电,使污泥中的大多数颗粒是相互排斥而不是相互吸引的,难于结成较大的颗粒沉降除去。油泥固相含量低,含水率高,呈现悬浮分散状态,因而体积庞大。来源不同的油泥,如新鲜的和老化的油泥,其组成和物理性质都可能会有较大的差别,如粘稠度、含水率、脱水性、油水分离性等。
1.3 含油污泥的危害
含油污泥的组成成分极其复杂并且体积庞大,这些污泥中一般含有苯系物、酚类、蒽类等物质,并伴随恶臭和毒性,排放后会占用大量耕地,另外,污泥含有大量的病原菌、寄生虫(卵)、重金属、放射性核素等难降解的有毒有害物质,对人类的身体健康会造成极大的危害,是导致很多致命疾病的罪魁祸首,因此含油污泥已被列为危险固体废弃物之列。含油污泥中大量的有机物和丰富的氮、磷、硫等营养物质,不加稳定处理的污泥任意排入水体,有机物和氨氮将大量消耗水体中的氧,导致水体水质恶化,严重影响水生物的生存,营养物质又会使水体富营养化,在沿海海域造成赤潮和绿潮。总之,含油污泥若直接和自然环境接触,就会对土壤、水体和植被造成较大污染。这也意味着石油资源的浪费。我国现已对含油污泥的排放加强了重视,无论是从环境保护还是从回收能源的角度考虑,都应该对含油污泥进行无害清洁化处理。
2 国内外处理含油污泥的技术研究
国内外处理含油污泥的方法一般有:焚烧法、生物处理法、热洗涤法、溶剂萃取法、化学破乳法、固液分离法、焦化法、含油污泥调剖、含油污泥综合利用等。但其中许多方法都存在着一些问题,对于实际应用很不适合。应该在已有的实验研究的基础上进一步探究含油污泥的处理技术,因此首先要了解国外的一些 技术,然后从这些技术中提炼出在我国可实行的部分来,再与本国的传统处理方法相结合,方可探寻出一种高效且实用性强的处理方法
含油污泥主要处理方法优缺点比较见表1:
序号 | 处理方法 | 适用范围 | 优点 | 缺点 |
1 | 简单处理 | 各类含油污泥 | 简单易行 | 污染环境,不能回收原油 |
2 | 物理化学处理 | 含油量在5%~10%以上的含油污泥 | 回收原油、综合利用 | 需处理装置,需加入化学药剂,仍有污水、废渣排放,处理费用较高 |
3 | 生物处理 | 各类含油污泥 | 节省能源,无需化学药剂 | 处理周期长,不能回收原油 |
4 | 焚烧处理 | 含油量在5%~10%以下的含油污泥及含有害有机物的污泥 | 含油污泥处理彻底 | 需焚烧装置,通常需加入助燃燃料,有废气排放,不能回收原油 |
5 | 作燃料、制砖 | 各类含油污泥 | 综合利用,较易施行 | 不能回收原油,有废气排放 |
2.1 国外含油污泥处理技术现状
国外对于寻找合适的含油污泥处理技术也经历了漫长的探索,对多种处理方法进行了实验研究。经萃取分离法能得到可直接利用的原油及有机物,而余下的泥水则返回变为可利用的资源,从而消除了污染,是油田上环境保护的有效措施之一。炼油厂废物的溶剂萃取已被美国环保局评定为已验证的较佳可用工艺。与污泥焚烧处理相比较,溶剂萃取工艺具有投资和操作费用较低、不生产烟气以及容易利用现有设备等优点。用过的溶剂可以直接返回炼油厂或者增加辅助设备回收并使之在萃取系统内循环,溶剂回收与炼油厂相结合可以大大降低费用,提高该工艺的经济效益。萃取法工艺过程简单、快速、选择性高于连续化和远距离操作有利于消除污染,改善环境节约能源等。但是,这种方法存在流程长、工艺复杂、处理费用高的问题,还有待进一步完善。
热解吸是一种改型的污泥高温处理方法。即使含油污泥在绝氧条件下加热到水沸点与烃类物质裂解温度之间,然后在闪蒸塔里轻质烃和水通过蒸发冷凝的方式回收;重烃质和无机物以泥浆的形式从分离塔里取出,进行固液分离后将重质烃回收。高温处理工艺因为通过冷凝对烃蒸汽加以回收,故不会污染空气。
热水洗涤法也称热吸附法,是美国环保局处理含油污泥优先采用的方法。一些专利技术中也提出了投入表面活性剂、稀释剂、电解质、破乳剂、润湿剂、调节剂,或在搅拌器中加水、化学药剂,加入油泥,加热,混合搅拌后静止沉淀等。法国、德国的石化企业多采用焚烧的方式,灰渣用于修路或埋入指定的灰渣填埋场,焚烧产生的热能用于供热发电。
2.2 国内含油污泥处理技术的现状
尽管国外的许多 的技术目前都已有了成功的例子,但是由于我国的各方面条件都受到了极大的限制,使得这些高效的技术不能在国内得到有效的应用。下面将部分技术在我国运用的情况和出现的问题作一简单分析。
2.2.1 含油污泥固液分离技术现状
在国内炼油厂含油污泥处理系统中,通常采用固液分离技术,即将油水分离或称为调质-机械脱水处理。实验证实,对于含油污泥,通过掺入一定比例的水以后,投加无机絮凝剂等,在增温措施下可进行污油回收。而在回收处理中,机械脱水也是关键步骤,因为只有实现“水清、泥干、油纯”,才能减少后续的处理费用。现在国内普遍采用的絮凝剂包括高分子无机絮凝剂如聚合氯化铝,聚合硫酸铁等和高分子有机絮凝剂如高聚合度的非离子、阳离子、阴离子聚丙烯酰胺等长链大分子,多数单位在机械脱水前使用阳离子有机絮凝剂或有机絮凝剂和石灰联用,以提高絮凝、脱水效果。我国炼厂污泥前处理普遍采用的机械脱水工艺,以带式压滤机、离心机为主,脱水后污泥的含水率为75%~80%。经多方面实验结果确定,在多种针对含油污泥处理的工艺中,污泥调质-机械脱水处理工艺发展的比较成熟。
2.2.2 含油污泥焚烧技术现状
以焚烧为核心的处理方法是彻底的污泥处理方法,它能使有机物全部碳化,杀死病原体,可极大限度地减少污泥体积,因此我国绝大多数炼油厂都建有污泥焚烧装置,如湖北荆门石化厂、长岭石化厂采用的顺流式回转焚烧炉;燕山石化采用的流化床焚烧炉。但是,其缺点在于处理设施投资大,处理费用高,有机物焚烧会产生二恶英等剧毒物质,同时污泥焚烧尚需要大量的柴油或污油,热量大且没有回收利用,焚烧装置的实际利用率较低,因此国内的焚烧处理技术有待改善。
2.2.3 含油污泥生物处理技术现状
从20世纪80年代开始,生物处理方法逐渐发展起来,它是一种经济和环境友好的处理方法,目前受到国内外的广泛关注。含油污泥的特征污染物是石油烃类,在自然条件下石油烃类可发生生物降解而达到逐渐自净,在生物处理法中,影响石油烃类降解的因素有污染物化学生物特征、微生物周边生活环境(如温度、营养物质、氧气浓度、pH值、含水率)、微生物自身的特征(微生物的种类、菌种的数量)等。研究表明,从石油污染的土壤中筛选出来的混合菌对原油中饱和分的降解率达到28%~51%,芳香烃的降解率可18%。营养物质的添加对有机物的降解也被广泛研究。但生物降解过程相对缓慢,若能优化某些环境条件则可大大提高烃类的生物降解速度,因此许多科研人员都致力于研究可降解有机物的高效微生物,并已开发了许多新的高效菌种,处理范围也相应地拓宽。目前国内采用较多的生物处理方法有地耕法、堆肥法以及污泥生物反应器法等。
3 含油污泥资源化处理技术进展
3.1 焦化处理
含油污泥中含有一定数量的矿物油,它主要由烷烃、环烷烃、芳香烃、烯烃、胶质及沥青质等组成,并且含油污泥中的矿物油重质组分居多,而焦化法处理含油污泥实质就是对重质油的深度热处理,其反应是一个烃类物质的热转化过程,即重质油的高温热裂解和热缩合。其反应过程大致如下:
石蜡烃→烯烃→二烯烃→环烯烃→芳烃→稠环芳烃→沥青质→焦炭
烃类的热反应是一种复杂的平行顺序反应,基本上可分成裂解和缩合两个方向。
目前焦化处理主要分两个方向,一是焦化法处理含油污泥回收矿物油,二是利用含油污泥添加适量的强度添加剂和炭化添加剂,通过控制焦化反应条件能够生产出净化效果较好的含碳吸附剂,油吸附效果优于PAM和陶粒,仅次于活性炭。国内赵东风等基于焦化反应机理,提出如下工艺及基本反应条件:油泥经过预处理(脱水)后除去较大机械杂质,利用传输设备与一次性催化剂掺和后送入已经预热的焦化反应釜(180℃),闭釜加热进行催化焦化反应,反应温度控制在490℃,反应时间为60min;焦化反应气通过伴热管线进入三相分离器;三相分离器由循环水控制降温(<100℃),分离器上部气相组分送入燃烧系统回收利用;底部含油污水排入污水处理系统,回收油送入储罐储存。该流程与目前其他含油污泥处理方法相比,具有设备操作简单,含油污泥处理彻底,矿物油有回收率高等优点,有利于推广应用。
3.2 溶剂萃取处理
溶剂萃取是利用萃取剂将污泥中石油类有机物从污泥中分离出来,然后蒸馏回收萃取剂进行循环使用,并回收利用分离出来的有机物。研究表明,污泥与溶剂比适当时,随着抽提次数的增加,所得油品中的重组分比例增大。张秀霞等人以三氯甲烷为萃取剂通过溶剂萃取-蒸汽蒸馏联合处理工艺,减少萃取剂用量,缩短处理时间,脱油率仍可达93%以上。程雁等综述国内外文献介绍了一种萃取分离工艺,可有效分离水,尾泥和油;回军等介绍了一种“热萃取-脱水”技术用于处理炼油厂含油污泥,脱出水中的COD小于150mg/L,含油量小于30mg/L,可直接排入污水处理场,溶剂油取自炼油厂馏分油。但萃取剂在回收循环过程中仍有部分遗失,处理成本高。此项技术发展的关键是要开发出性能价格比高的萃取剂,同时萃取后泥渣需做进一步处置。因此,萃取工艺必须与其他处理处置方法结合使用。除常规的萃取技术外,超临界流体萃取技术,是一种新兴的含油污泥萃取技术,由于超临界流体巨大的溶解能力,萃取剂易于回收循环使用。由于目前萃取法的处理成本较高,还没有实际应用于炼厂含油污泥处理。开发出性能价格比高的萃取剂成为此项技术发展的关键。另外,正处于开发阶段的超临界流体萃取技术有望取代传统的萃取法处理含油污泥。
3.3 含油污泥热解
该方法是90年代初国外迅速发展并得到应用的工艺。1967年丹麦开始了有关热分解处理方法的研究,后来在美国、日本等 得到应用。含油污泥热解是指在无氧或少量氧的环境下有机物大分子转化为小分子的热化学反应,亦称为干馏。热解产物分为回收油、不可冷凝气体、冷凝水和固体残渣(焦炭、半焦)。热解过程中反应温度、压力、停留时间是三个重要的影响因素。陈超等人试验回收的气、液、固产物质量分占10%、20%和70%。热解气体主要成分为甲烷、二氧化碳、乙烷和氢气等。热解油以柴油馏分(75%)为主,热值可达47MJ/kg,可直接作燃料油。残渣以沙粒为主,固定了大多数金属元素(Pb、Cr、Ni除外),可用于铺路或建材材料。王万福等人发现含油污水处理污泥热解的产油率可达10%以上。采用热解工艺处理,其具有显著的直接经济效益和社会效益,对配套工艺技术与装置值得深入研究。对含油污泥热解技术已经开展初步试验研究,并根据小规模试验和实际操作经验进行工艺设计,部分已进入中试或工业规模阶段的研究,有的已经进行了商业化应用,但热解法一般较适用于含油率较高的污泥。
4 几种新型含油污泥处理技术的研究
4.1 超临界水氧化处理含油污泥的研究
4.1.1 超临界水的特性
超临界水氧化法是利用水的特殊理化性质得以实现的。水在通常情况下以蒸气、液态水和冰三种状态存在,它是一种良好的极性溶剂,可以溶解大部分电解质,但对气体、非电解质类物质及大部分有机物质的溶解性能较差。当温度和压力达到水的临界点(Te=374.3℃,Pe=22.05MP)时,水的密度、介电常数、粘度、扩散系数等就会发生巨大的变化,此时水就会处于一种既不同于气态,也不同于液态和固态的流体状态——超临界状态,此状态下的水就称为超临界水。超临界水具有以下物理化学特性:
(1)水的介电常数在通常情况下是80,而在超临界状态下,则下降到2左右,超临界水呈现非极性物质的性质,成为非极性有机物的良好溶剂,而对无机物的溶解能力则急剧下降。
(2)氧气等气体在通常情况下,在水中的溶解度较低,但在超临界状态下,氧气、氮气等气体,可以以任意比例与超临界水混合成为单一相。
(3)气液相界面消失,电离常数由通常的10-23下降到超临界条件下的10,流体的粘度降低到通常的10%以下,因此,传质速度快,向固体内部的细孔中渗透能力非常强。
4.1.2 超临界水氧化的反应机理
反应机理是研究超临界水氧化技术的重要部分。一些学者提出的自由基反应机理认为,自由基是由氧气进攻有机物分子中键合力较弱的C-H键产生的。过氧化物通常分解生成较小的化合物,生成甲醛或乙酸,甲醛或乙酸被氧化成为CO2和水。
4.1.3 超临界水氧化处理含油污泥的研究
超临界水氧化技术(简称SCWO)是以超临界水为反应介质,空气、氧气或过氧化氢等为氧化剂,高温高压下的自由基反应。该工艺被认为是湿式水氧化(WAO)的进一步发展。超临界水氧化法(SCWO)用于处理各种有毒化学物质、造纸污水、城市污水、人类代谢污物和生物污泥的研究已经取得成功。目前欧、美、日等发达 对SCWO进行有机污染处理应用研究较为深入,有的已经达到中试规模,而我国在这方面的研究大多处于实验阶段。
针对含油污泥,国内荆国林等人利用超临界水氧化法,对模拟的含油污泥及实际油田产生的含油污泥进行研究,考察用超临界水氧化法处理含油污泥的可行性。实验研究主要是考察反应温度、反应压力、反应停留时间、氧化剂浓度等实验参数对含油污泥降解率的影响,寻求较佳的操作条件。模拟的含油污泥由原油、水和泥沙组成,含量与实际污泥相同,以便对比研究。实验装置为自行设计的高温高压超临界流体间歇反应系统,包括加热器、反应器、分离器等主要设备。实验结果显示,在该实验条件下,随着反应时间的增加,温度的升高,油的去除率也随之增加。试验结果显示,温度在420~440℃时,反应时间控制在10min时,处理效果较好,油的去除率均在90%以上;反应压力24MPa、反应时间5min时,氧化剂的倍量对含油污泥原油去除率也有影响。随实际氧化剂(H2O2)量与理论需求量之比的增加,含油污泥原油去除率增加,当氧化剂(H2O2)的倍量超过3后,含油污泥原油去除率增加呈平缓趋势,因此得出结论,即实际H2O2的倍量为3~7比较适宜。而处理实际含油污泥的效果明显好于模拟含油污泥,其原因可能是多方面的。首先实际含油污泥从原油开采到后期污水处理过程中加入了大量化学药剂,里面含有原油、细菌、盐类、腐蚀产物、凝聚剂、缓蚀剂、阻垢剂、杀菌剂等水处理药剂,所以实际含油污泥的成分比模拟含油污泥成分复杂,有些化学药剂更易降解,更易被氧化。超临界水氧化反应能有效去除油田含油污泥中的原油,在条件不是很苛刻的情况下,原油去除率可达95%,反应停留时间、反应温度、反应压力和实际过氧化氢质量与理论需氧量之比是影响含油污泥原油去除率的重要因素,pH值对去除率也有影响,但不大。可见,利用超临界水氧化法处理含油污泥有较大的可行性,还有待进一步的研究。
4.2 超声波处理含油污泥的研究
4.2.1 超声降解机理
超声波的频率范围一般为20KHz~10MHz,当一定强度的超声波作用于某一液体系统中时,将产生一系列物理和化学反应,并明显改变液体中的溶解态和颗粒态物质的特征。这些反应是由声场条件下大量空化泡的产生和破灭引起的。超声空化是指在很高的声强下,特别是在低频和中频范围内,液体中将产生大量空化泡,它们随声波改变大小并在瞬间破灭。气泡破灭时,将产生极短暂的强压力脉冲,并在气泡及其周围微小空间形成局部热点,产生高温(5000K),高压(100MPa)和具有强烈冲击力的微射流。当空化发生时,液体中产生很高剪切力作用于其中的物质上,同时伴随发生的高温高压并将产生明显的声化学反应。
4.2.2 超声处理含油污泥
王新强等人运用超声技术,对含油污泥进行了处理研究。通过对超声空化状态、频率、功率、作用时间、作用温度对除油率影响的实验,探讨了超声处理含油污泥的可行性及适用条件。
在该实验条件下,从超声空化状态的试验结果来看,弱空化状态下对含油污泥除油效果较好,无空化状态时次之,经强空化状态处理后的含油污泥,沉降效果非常差,主要原因是在强空化状态含油污泥乳化程度加剧所致。
而实验中得出的较佳超声频率为40KHz。同时,随着功率的增大,除油率增加。这是因为超声波的功率(声强度)增大时,超声波本身具有的能量增强,超声空化时增强传质,同时,功率提高可以使半径更小的乳化油滴结合,上浮,从而提高了除油率。作用时间不宜过长,这是因为随着作用时间的增加,输入的总能量逐渐增大,对油/泥的剥离强度加大,除油率增加;但时间过长时,超声波可能会改变污泥的内部结构,使污泥颗粒变小,增加了污泥颗粒对油的再吸附能力,从而降低了除油效率。温度也要适当,这是因为,在温度较低的情况下进行超声除油,超声作用在短时间内不易破坏油-固体颗粒之间的粘附力,除油效率较低,温度升高时,超声作用力增强,对除油有利。但温度过高时,超声作用强度会降低,不利于除油,实验确定的较佳温度为50℃。
5 展望
基于国内外对含油污泥的各项处理技术的研究,应进一步加强科研工作,积极探索切实可行的处理技术,减少含油污泥对环境的污染及对人体造成的间接危害,使含油污泥的利用资源化,处理经济化,借鉴国外的 经验技术,开发新的处理技术,含油污泥处理定会取得较大的进展。