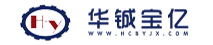
1 前言
食盐溶液电解生产烧碱或氯化钾溶液电解生产氢氧化钾的盐水精制过程中必然有盐泥生成,如果将稀盐泥直接排入附近江河或空地,由于排放量大会造成环境污染。近年来环境保护工作对氯碱工业生产中的盐泥处理提出了严格要求,盐泥的分离处理各厂都已提到重要议事日程上来。
目前国内各厂为降低盐耗避免泥浆外流污染环境,一般采用三层桶或自动板框式压滤机回收其盐水,盐泥收集处理加以利用,但是卧式螺旋卸料沉降式离心机,用于氯碱工厂盐泥分离至今尚未有过报导。
成都化工厂万吨离子膜法制氢氧化钾引进工厂盐泥分离处理原设计使用板框压滤机,考虑到板框压滤机的使用缺点,以及原有一台闲置的旧WL-350离心机,分析了该机的使用特性和生产能力后,认为可以用于盐泥的分离处理,大胆地在引进工厂中改用WL-350卧式螺旋卸料沉降离心机,并自行设计了盐泥分离工艺。该系统自1990年8月投入生产运行至今取得较为满意的效果。WL-350卧式螺旋卸料沉降离心机在该厂的 使用成功,为氯碱行业盐泥分离处理方法提供了新途径。
2 沉降离心机用于盐泥分离技术可行性分析
WL-350卧式螺旋卸料沉降离心机主要特点是采用离心沉降方式分离悬浮液,无滤网或滤布,自动连续卸料,主要由转鼓、螺旋推料器、差速器、机壳、机座等部件组成。待分离的悬浮液由中心加料管加入螺旋推料器的进料仓内,在高速旋转的离心力作用下较重的固相物沉积在转鼓内壁形成沉渣层被螺旋推料器推送到转鼓小端卸渣口排出,清液则形成内环分离层以溢流方式从大端出液口排出。
该机与料液接触部件均为不锈钢材质,且有关部件表面进行硬化处理。WL离心机特别适合于悬浮液中固相脱水和固相粒子的分级,也可澄清含少量固相的液体,更适合于分离滤布再生困难的物料以及浓度,颗粒粒度变化范围较大的物料,其悬浮液进料浓度范围2%~5%,温度0~100℃悬浮液中固相粒度范围0.005~5mm,运转时间可24小时连续运行。
氯碱工厂盐水精制后生成的盐泥浆含固相物浓度一般为10~15%,温度30~60℃,固相粒度0.01~1.0mm,均在该离心机分离特性范围内,因而WL-350卧式螺旋卸料沉降离心机用于盐泥的固液分离从技术上来讲是可行的。
3 氯碱工厂盐泥分离方法简介与比较
目前国内氯碱厂盐泥分离方法有以下几种。
3.1 盐泥存放自然蒸发增浓处理盐泥
盐泥经洗涤澄清(间断或三层洗泥桶连续洗涤)回收含盐清液后排入泥浆贮池自然蒸发水分后定期人工式机械清除池内泥渣。
该方法设备简单,动力消耗少,操作简单,但占地面积大,下雨天或清除泥渣不及时会造成周围环境污染。泥渣含水量高,排渣量大,清除泥渣劳动强度大,操作环境差,不符合环保标准,国内多数工厂已不采用此法。
3.2 叶片式真空抽滤压缩空气反吹分离方法
澄清桶盐泥排入泥浆地池,叶片式抽滤器放入池中真空抽滤回收含盐溶液,达一定真空度后吊出池外继续干抽至有龟裂时停止干抽,通入压缩空气反吹,泥饼脱落收集。
该方法因主体设备通常工厂可自制而投资不高,干泥渣含水量50%左右,排除泥量较少,操作不复杂,但需配真空泵,空气压缩机等附属设备,投资费用增大,盐泥分离能力低,能耗高,盐泥未经洗涤而泥渣含盐较高,周期性人工控制操作,滤布、叶片易损坏,维护维修工作量大,劳动强度较大,操作环境差,泥渣收集不方便。此法国内部分工厂采用。
3.3 叶片式压力过滤机分离方法
盐泥经洗涤澄清(间断式三层洗涤桶连续洗涤)回收含盐清液后排入泥浆贮池由泥浆泵将盐泥压入过滤机过滤,滤液回收。干泥于机内经压缩空气收脱在U型槽内由螺旋输送器送到贮泥仓。
该方法滤泥含水量45~50%,排泥量少,操作易掌握,能连续操作,结构紧凑,密闭性好,滤液收集方便,操作环境好,劳动强度较低,该机既可真空、加压联合操作,也可单独真空或单独加压操作,但过滤机叶片(碳钢)存在腐蚀,滤布、叶片使用寿命不长,维护维修工作量较大,配套泥浆泵要求大于主机内压力,压力应大于0.4MPa,选泥浆泵较困难,加上空压机、真空泵等附属设备动力消耗较高,投资费用较高,设备体积大而重。
3.4 板框式压滤机分离方法
盐泥经洗涤澄清(间断式三层洗泥桶连续洗涤)回收含盐清液后排入泥浆池由泥浆泵压入板框过滤机,滤液回收,滤泥压干后经压缩空气正反吹脱落收集、处理。
该方法的特点是滤液含水量45%左右,排泥量少,操作易掌握,采用可洗涤盐泥的自动板框压滤机可省去三层洗泥桶,但周期性间断操作,板框存在腐蚀,滤布、板框易损坏,拆装、更换、维护维修工作量大,泥渣收集不方便,工作环境较差,劳动强度较大,配套泥浆泵要求出口压力高,选配严格,盐泥分离需用压缩空气等辅助设施,设备体积大而重。如FBXY-54/870板框过滤机,过滤面积54m²,机体尺寸4500×1450×1650,设备自重6.8t。目前国内大多数工厂采用此法分离盐泥。
3.5 WL-350型卧式螺旋卸料沉降离心机分离方法
盐泥经洗涤澄清(间断式三层洗泥桶连续洗泥)回收含盐清液后由泵(控制流量)将泥浆送入离心机分离,含盐清液回收利用,泥渣自动排入小车后送贮仓集中处理。
该方法特点是滤液含水量35~40%,排泥量少,能连续操作,分离因数高达2400,分离效果好,操作易掌握而又简单,易实现自动化操作,密闭性好,操作环境好,结构紧凑,设备体积小而重量轻,无滤网式滤布,生产能力大,动力消耗低,对配套泵无严格要求,盐泥分离不需压缩空气。WL-350电机功率7.5kW,机体外型尺寸仅为1660×1400×540,设备自重仅0.67t,不足的是盐泥只能分离泥渣不能洗涤。
从以上目前国内使用的各种盐泥分离方法简介和优缺点比较可以看出,使用WL-350卧式螺旋卸料沉降离心机分离处理盐泥方法无论从处理工艺流程,分离效果,操作的难易,劳动强度,操作环境,动力消耗,机械化自动化程度等各方面均优于板框式压滤机等其它盐泥分离方法。
4 WL型离心机盐泥分离工艺流程
澄清桶按规定定时定量排泥到洗泥桶(2-3个桶轮换洗泥或采用三层洗泥桶)加入蒸发来二次蒸汽冷凝水(或废热水)搅拌均匀后自然澄清6-8h,清液排至淡盐水池再加冷凝水搅匀,泥浆出泵并经泵出口阀和回流阀控制盐泥量将盐泥送至离心机,经分离后清液由管道送淡盐水池,再由淡言水泵送配水桶用于溶盐。分离后的干泥渣自动卸至运泥小车,然后送干泥堆仓集中后送煤炭公司作生活煤球添加粘结剂或用作建材添加剂使用。
WL型离心机盐泥分离工艺流程的特点是省去盐泥高位稳压槽,直接由泵通过回流量控制进离心机的盐泥量,同时利用回流盐泥自身搅拌洗泥桶盐泥,保持盐泥浓度均匀,简化流程,节省动力。
5 生产操作运行情况总结
WL-350卧式螺旋卸料沉降离心机分离系统由该厂自行设计安装于1990年8月,随该厂万吨离子膜法制KOH引进装置建成一道正式投入生产运行。该机运行两年来取得较为满意的效果,运行稳定,分离的泥渣含水量取样测定为35~40%,含盐量10%左右,低于板框压滤机含水量,机器运行噪声测定<75分贝,减少环境污染,达到环保规定。原设计每小时处理盐泥浆量1.5~2m³,每日离心机运行时间8~12h,实际该厂澄清桶平均每班排泥3m³左右,日排泥量6~9m³,离心机处理洗涤后盐泥量平均9~14m³/d,每日离心机平均运行时间6~8h,干泥渣量600kg/d左右。该厂目前使用的是一台WL-350旧设备,待以后更新使用WL-350B型,预计效果会更好些。
总结两年来生产运行经验WL型离心机分离盐泥操作上应注意以下几点:
(1)盐泥浆浓度不要控制过高,密度控制在1.15以内为好。盐泥浆浓度高可加废热水调整。这是由于进离心机盐泥浆体积量按规定不超过3m³/h,因而单位时间进离心机流量低。如果盐泥浓度过高,易出现沉积阻塞断流现象,进离心机流量控制不好而造成进料波动大,不稳定,致使分离清液返浑,影响分离效果。
(2)离心机进料量不允许超过离心机能力,否则清液返浑分离效果差。
(3)热水洗涤盐泥有利于盐回收,进离心机盐泥浆温度适当高,比常温盐泥分离效果好,推荐使用蒸发二效冷凝水或其它废热水洗盐泥和调整泥浆浓度。
(4)每次盐泥分离处理完毕应让机内盐泥排净井用清水清洗设备,避免因停机时间长使机内转鼓和螺旋推料器结泥垢。离心机应严格按操作规程操作并严格按使用、维护规定加润滑油,调整传动皮带松紧等,按规定时间中、小修才能保证设备长周期正常运行。
6 结论和存在问题
两年来生产运行说明WL-350离心机盐泥分离流程具有流程简单,盐泥分离因数高,分离效果好,无滤网和滤布,操作运行稳定并能连续操作的优点,而且密闭性好,结构紧凑,体积小,重量轻,附属设备少,简单易选配,动力消耗低,操作简便,劳动强度低,操作环境好,使用维护也方便。
实践证明WL型卧式螺旋卸料沉降离心机用于氯碱行业盐泥分离是可行的。该机优于板框式压滤机和叶片过滤机,是一种较为理想的 设备,建议在氯碱行业中推广运用。
该机不足之处是在分离的同时不能堆盐泥洗涤,必须配盐泥洗涤系统。泥渣含盐高低与盐泥洗涤好坏有关,但该厂目前间断洗泥一次分离后的干泥含盐量已低于规定的指标。
由于目前还没有适用于泥浆计量的流量计,进入离心机流量控制凭经验人工控制,有时操作不好,进料量偏大会造成清液返浑。
建议制造厂家与氯碱厂用户合作进一步改善WL型离心机结构使之更适合于盐泥的分离处理。