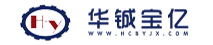
1 含油污泥产生和环境污染
1.1 炼油厂污水处理产生的“三泥”
炼油厂“三泥”就是炼油厂污水处理产生的隔油池底泥、气浮处理产生的气浮渣以及好氧生化处理中产生的剩余污泥,其中以浮选浮渣量较大,占三泥总量的80%。炼油厂“三泥”产生量大约是水处理量的2‰~3‰。特点是:产生量大(含水率按99%计),不易处置、污染严重。
按照《中华人民共和国固体废物污染环境防治法》的要求,有毒有害固体废物不允许不加处理而直接暴露于环境中,而且也不允许进行污染物的转移或变相转移。而炼油厂“三泥”是一种含有大量污染物的危险废物,若不加以处理而直接进入环境则势必对大气、地表水、地下水以及土壤造成严重的环境污染。纵观国内炼油企业的发展,因“三泥”没有得到安全处理和处置而发生环境污染的事件时有发生。因此,对炼油厂“三泥”加以适当的处理是非常必要的,也是践行日益严格的 环保法规的必然要求。
1.2 罐底油泥
炼油厂生产加工过程中各种储油罐在自然沉降过程中也会产生一些油泥,称为罐底泥。此外,在原油输送、装置检修过程中,由于事故、跑、冒、滴、漏等原因会有或多或少的原油流到地上,从而形成落地油泥,这部分油泥在炼油厂内产生量较小。
罐底油泥区别于一般性的含油污泥,由于其极高的碳氢化合物含量,是一种很好的可回收利用的资源。经长期的调查测试发现,油罐底泥中含有约25%的水和5%的无机物,如泥砂等,其余70%为碳氢化合物(其中沥青质占7.8%、石蜡占6%、灰份占4.8%)。通过适当的分离技术,碳氢化合物回收率即可达到98%以上。因此,若对清罐底泥不采取有效的回收减量化处理,将造成大量的石油资源流失,同时对环境造成严重污染。
炼油厂含油污泥的分类和性状见表1:
表1:炼油厂含油污泥分类及性状
油泥分类 | 产生量(t/a) | 性状 |
落地油泥 | 10 | 落地油泥中除泥土、沙石外,还会有其它固体废弃物 |
罐底油泥 | 7800 | 通过适当的分离技术,碳氢化合物回收率可达到98%以上,回收价值较大 |
污水处理厂“三泥” | 7200 | 污泥成分和物性差异大,处理难度高,油含量差别较大,部分具有回收再利用价值 |
1.3 含油污泥处理工艺
1.3.1 工作原理
离心脱水机是利用水分和污泥的比重不同,在转筒高速旋转过程中产生的离心力之差使之相互分离,实现脱水目的。含油污泥通过空心轴中的中心进料管进入转筒,在离心力的作用下,污泥因比重大,而被甩至筒体壁面,转筒与螺旋输送机之间的转速差使螺旋输送机连续不断地将污泥固体推到转筒的圆锥端进一步压缩排出。水分由于比重小,离心力小,在内侧形成液体层,水分则将通过转筒的圆筒端排出。
1.3.2 工艺流程
该炼油厂两套污水处理设施的油泥、浮渣、剩余污泥采用污泥沉降浓缩-絮凝破乳-离心脱水-脱水污泥输送-离心分离液外送的工艺流程(包括絮凝剂制备与稀释、污泥处理控制系统等辅助配套设施)进行处理。
2 存在问题
2.1 “三泥”脱水能力不足
该炼油厂 污水处理厂设计处理量为200m³/h,第二污水处理厂设计处理量为300m³/h,目前两套装置经常处于超负荷运行状态。而“三泥”装置静止脱水罐较少,脱水装置油泥量较大,导致静止脱水时间不够,经离心脱水机分离后产生的大量分离液回到污水系统,在装置内产生恶性循环,给“三泥”脱水装置的正常运行带来较大压力。
2.2 处理浮渣效果差
污水处理厂来水水质较差,浮选产生的浮渣量较大。由于浮渣的比重差异小,离心脱水机处理浮渣的效果较差。
2.3 未有效回收资源
含油污泥的处理还 于简单回收,尚未对含油污泥进行无害化和资源化处理。这种简单的堆存,对于整个社会和外界环境来说,只是污染物的简单转移,并未得到有效处理和利用,容易造成大面积的环境污染和风险。
含油污泥中一般含油率在10%~30%之间,依托外部有资质单位处理,仅仅是集中收集堆存,石油回收率为零。因此含油污泥的产生造成了原油的浪费和流失。剩余的固体废物委托有资质的单位处理,企业还要付出较大处理费用。处理不当还会对环境造成潜在威胁。
3 含油污泥处理方案建议
3.1 常用的油污泥处理方法及适用性分析
核心处理技术 | 优点 | 缺点 | 主要适用原料 |
热水洗涤法 | 工艺容易实现,投资费用低,可回收大部分油品 | 难于处理乳化严重的含油污泥,可能产生二次污染 | 落地油泥 |
焚烧 | 较大程度的减量化,对原料适应能力强 | 能耗高,设备投资大,工艺技术要求高,一般热量利用率不高,存在粉尘、SO2等二次污染 | 含水量不高,而油含量较高的含油污泥 |
热解吸 | 完全无机化,烃类可回收利用 | 反应条件要求较高,操作比较复杂 | 含水量不高,烃类含量高的油泥 |
溶剂萃取法 | 效率高,处理彻底,大部分石油类物质提取回收 | 萃取剂价格昂贵,过程中存在部分损失,处理成本高 | 罐底泥 |
生物处理 | 能耗低,处理成本低 | 处理周期长,对环烷烃、芳烃、杂环类处理效果较差,对高含油污泥难适应,资源无法回用 | 油含量小于5%的含油污泥 |
综合利用 | 成效显著,提高资源综合利用率 | 工艺要求较复杂,成本相对较大 | 炼油厂“三泥” |
3.2 TPS撬装工艺装置
目前,部分石油生产企业和炼油厂相继建成了TPS撬装工艺装置处理含油污泥。通过该工艺处理后,既回收了石油资源,剩余残渣也变为了一般工业固体废弃物,彻底消除了环境风险。
3.2.1 液态油泥处理
液态污泥进行油水固三相分离和污泥脱水工艺。进料罐车经汽车衡后卸到液态污泥储存池,由提升泵提升到高效内循环油泥分离器,经过自然沉降后,自上而下分成污油、污水和底泥三部分,污油自流到污油池,用污油泵外输回收;污水自流到污水池,再用泵打入污水处理系统;底泥由污泥泵输送到离心机脱水,再经螺旋输送器提升到油泥堆场,脱出污水自流到低位污水池,再经泵输送至污水处理系统。
3.2.2 热相分离处理
热相分离处理是在高温条件下,对干燥油泥中的石油烃类进行分解,回收油气资源,实现油泥的无害化处理。热相分离工艺设备是TPS撬装装置,属于螺旋式间接加热装置。脱水含油污泥及其他固态的含油污泥经上料系统加入TPS撬装装置,经螺旋推进油泥进入间接加热阶段,在一定温度下,油泥中的有机物汽化并部分裂解成低分子气态有机物,气体经过间接冷却,凝结下来的含液相经油水分离的到石油类物质进行回收,水进入污水处理厂,不凝气主要是一些气态有机物或煤气成分,可以作为加热原料使用。处理后剩余残渣有机物含量低于2%,由新鲜水加湿降温、抑尘,而后螺旋输送到储存场地,可用于筑路或制造建筑材料。
4 效益分析
4.1 环境效益
该炼油厂每年产生各类含油污泥15000t,脱水后交由有资质的第三方处理单位处理,含油污泥在运输,处理处置过程中存在二次环境污染风险,如处置不当,也会造成污染转移,对本地环境和处置地环境的大气、地表水、地下水以及土壤造成一定的环境风险。
通过对含油污泥进行资源回收技术处理后,回收了石油资源,使含油污泥无害化和资源化处理,消除了因含油污泥处理处置过程中所产生的环境污染隐患。每年可减少占地面积约12亩,减少填埋费用大约3000万元。减少挥发性有机物排放大约2475t,环境效益可观。
4.2 经济效益
该炼油厂每年的油泥产生量在15000t左右,如果能使其得到有效利用,每年可为该企业带来可观的经济收益。如按照废油里面可提取物质占到总量的21%计算,每年可回收石油资源3150t,带来经济效益1575万元,每年节约油泥处理费用3000万元,共计带来经济收益4575万元/年。
4.3 社会效益
该炼油厂积极开发污染治理的新技术,并能在企业内实现新技术的利用,能带来企业形象的提升,另外可每年从废油泥中回收石油类资源3150t,既节约了成本,减少了对自然资源的浪费,也为企业转型为环境友好型企业奠定了良好的基础。
5 结论
含油污泥无害化处理,回收污油泥中的原油,彻底消除了含油污泥所产生的环境污染以及潜在的环境风险,给企业带来了一定的经济效益和环境效益。同时使企业满足新修订的《中华人民共和国环境保护法》,对促进企业的可持续发展具有重大的现实意义。这一技术得到推广和应用,将会惠及石油炼制类整个行业,对石油炼制类企业含油污泥减量化、资源化综合利用起到良好示范效应。