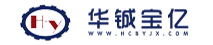
石油开采、运输以及贮存过程均会产生油田采出水,其具有含油量大、悬浮固体浓度高、有机物种类复杂等特点。油田采出水处理处置不当会破坏生态环境并对人类健康造成巨大危害。对油田采出水进行深度处理,达到回注标准后回注,则既可避免油田采出水进入环境危害生物,也可避免水资源的大量浪费,因而成为近年来油田采出水处理处置领域的研究热点。
传统含油废水处理工艺一般有气浮、离子交换、吸附、混凝等。然而由于油田采出水中乳化油的稳定状态,传统方法处理油田采出水达到回注标准难度大,往往需做进一步的精细处理。随着膜法水处理技术的发展,利用膜分离技术处理含油废水近年来应用日益广泛。利用膜技术处理油田采出水具有分离效果好、药剂投加量少、出水水质稳定、易于实现自动化控制等优点。相较于有机膜,陶瓷膜以其强度高、耐腐蚀、耐高温、热稳定性好等特性,在膜技术处理油田采出水领域展现出更大的优势,但陶瓷膜处理油田采出水过程中,膜污染问题依然存在。由于油田采出水水质的复杂性,陶瓷膜过滤一段时间后会形成污垢,堵塞膜孔,导致过滤压力增大,膜通量下降,产水量降低,给陶瓷膜在油田采出水处理工程中的大规模应用造成了阻碍。合理优化陶瓷膜处理油田采出水系统运行控制工况,明确陶瓷膜处理油田采出水过程膜污染机理,开发更为高效的膜污染控制方法已成为陶瓷膜处理油田采出水领域亟待解决的关键问题。
本研究针对陶瓷膜处理油田采出水过程中存在的膜污染机理不明晰的问题,构建了陶瓷膜反应器,处理两级过滤后的实际油田采出水。通过四因素三水平正交实验,筛选出膜污染控制效果较优的运行控制工况。结合微观表征和膜阻力分析等手段,确定了造成陶瓷膜污染的主要污染物,揭示了油粒对陶瓷膜污染的微观机理,可为陶瓷膜在油田采出水处理及回用领域的推广应用提供参考。
1 材料与方法
1.1 实验装置
本研究采用的平板陶瓷膜处理油田采出水实验装置。进水为取自胜利油田坨六站经2次除油罐出水的油田采出水,纯净水作为反冲洗用水。膜池的材质为PVC,有效容积为250L,膜组件反应器及其相关配制置于膜池内,膜组件反应器内可同时运行4片平板陶瓷膜,通过气体流量计和膜组件底部的微孔曝气管对平板陶瓷膜表面进行定量曝气。膜材质陶瓷部分为Al2O3,集水部分为高分子聚乙烯,膜孔径为0.1μm,有效过水面积为0.10086m²,pH为2~12;实验以油田采出水为膜前原水,蠕动泵连接管路抽吸出水,通过量筒和真空表测定滤出液的体积和出水压力。平板陶瓷膜出水口使用三通分为抽滤系统和反冲洗系统,分别由自控装置控制运行。自动装置由电磁阀、计时器组成,通过自控装置控制蠕动泵的开关完成实验运行。
1.2 实验用水
本实验用水采用胜利油田坨六站经核桃壳、双滤料两级过滤后出水的油田采出水:水温为22~25℃,pH为6.7~6.9,含油量为15~38mg/L,悬浮固体含量为17~46mg/L,粒径中值为2.5~3μm。
1.3 处理水要求
在后续所有陶瓷膜处理油田采出水的实验中,出水含油量均在5mg/L以下,SS<1mg/L,粒径中值<1μm,符合《碎屑岩油藏注水水质推荐指标及分析方法》(SY/T5329-2012)中A1级回注标准。这也验证了平板陶瓷膜处理油田采出水的优良效果。
1.4 实验方法
(1)含油量测定。按照《碎屑岩油藏注水水质推荐指标及分析方法》中测定含油量的方法配制标准油溶液,采用分光光度法测定,并绘制标准曲线。利用石油醚作为萃取剂,萃取油田采出水中的含油量,以石油醚为参比,测其在波长212nm下的吸光度,计算含油量。
(2)膜通量测定。采用体积法进行平板陶瓷膜膜通量测定,自量筒内取一定时间内通过一定膜面积的过滤液体积,计算膜通量。
(3)膜污染阻力分析。根据Darcy定律的过滤模型来确定平板陶瓷膜过滤过程中的阻力分布情况。
(4)正交实验设计。本研究将运行控制因素优化作为实现膜污染有效控制的关键技术手段,确定了初始膜通量、过滤时间、水力反冲洗时间和曝气强度作为平板陶瓷膜运行调控的关键因子,平均膜通量为响应值的四因素三水平正交实验。使用SPSS对正交实验结果进行统计学分析,验证正交实验的结果。
(5)分析手段。傅里叶变换红外光谱(FTIR),检测未知物的官能团、测定化学结构、观察化学反应历程;扫描电镜(SEM),利用电子束扫描样品表面从而获得样品信息,了解物体表面微观结构;X射线能谱(EDS),检测元素发出的特征X涉嫌的频率,用于分析污染层和膜表面的微观结构和元素组成。
2 结果与讨论
2.1 渗透特性及临界通量研究
平板陶瓷膜一般具有自身膜通量较高、机械强度高、耐高温耐腐蚀能力强的特点。掌握平板陶瓷膜的渗透特性利于控制后续的实验过程。
(1)平板陶瓷膜清水通量测试。测定新膜抽滤蒸馏水的通量作为清水通量,调节蠕动泵转速,使实验装置在每个转速下持续运行30min,记录平板陶瓷膜的出水量。将5min出水量代入公式计算膜通量。在实验条件下,平板陶瓷膜清水通量随管内压力增大而增加。当管内压力为15kPa时,平均清水通量为408.93L/(m²·h)。这说明平板陶瓷膜具有良好的过滤性能。
(2)平板陶瓷膜临界通量测试。通过阶梯法来确定本实验条件下的临界通量:保持反应器在较低的通量运行一段时间,记录固定间隔内该过程中跨膜压差的变化;提高膜通量,通量的增加值称为通量阶梯,记录每个固定时间间隔内过滤过程中跨膜压差的变化。重复以上步骤,不断提高膜通量,直至跨膜压差有突然的飞跃或者是在某阶梯间隔里跨膜压差不再稳定时为止,设此时的膜通量为为JN+1(N为实验中流量阶梯的增加次数),则JN为在该实验条件下允许保持跨膜压差恒定的膜通量,即为临界通量。
调节蠕动泵转速为30、40、50、60、70r/min,使每个转速对应的压力梯度持续运行30min。膜通量以5min内滤出液的体积来计算。记录每5min的压力和通量变化。在临界通量测试过程中,前90min内,平板陶瓷膜运行通量不高于50L/(m²·h)。前60min内,管内压力和膜通量基本保持一致,在第3个周期内,压力基本稳定,膜通量开始呈下降的趋势;在90min之后的2个周期内,管内压力随时间增加急剧升高,且膜通量下降趋势加重,这说明当膜通量高于50L/(m²·h)后,膜污染的速度较之前加快。此时,即便再次降低膜通量,膜压也不能恢复到原有的水平,这说明膜面开始形成滤饼层,即发生了不可恢复的膜污染。因此,确定本实验条件下平板陶瓷膜处理油田采出水的临界通量为50L/(m²·h)。
2.2 优化运行控制研究
(1)正交实验。如前所述,本实验构建了以初始膜通量、过滤时间、水力反冲洗时间和曝气强度为影响因素,平均膜通量为响应值的四因素三水平正交实验。为了更全面地研究初始膜通量的影响,结合前期实验结果,初始膜通量选取大于、等于、小于临界通量3个水平,即30、50、80L/(m²·h),其通过调节蠕动泵的转速来实现;过滤时间3个水平值分别为10、15、20min;反冲洗时间分别选取30、60、90min;曝气强度选取1、3、5L/min。本实验采用相同的反冲洗强度,为400mL/min。
依次开展9种工况下的实验,每个工况同时运行2片同一批次的全新的陶瓷膜,并分别记录各自的管内压力及膜通量随时间的变化情况,取2片膜的平均膜通量均值作为该工况的平均膜通量,将15L/(m²·h)作为此后所有实验的污染终点,以进行后续实验分析。
(2)优化运行控制正交实验结果分析。S7工况下的膜平均通量较大,为27.82L/(m²·h),S6工况下膜的平均产水量较小,为17.75L/(m²·h)。各工况平均膜通量依次为S7>S9>S3>S4>S2>S8>S1>S5>S6,极差分析结果确定S7为平板陶瓷膜处理油田采出水较佳运行工况。
为验证实验结果的准确性,采用SPSS软件对正交实验数据进行分析。对膜平均通量影响大小的显著性顺序为初始膜通量>反冲洗时间>过滤时间>曝气强度。其中,初始膜通量和反冲洗时间的影响较为显著。在初始膜通量80L/(m²·h),过滤时间10min,反冲洗时间30s,曝气强度3L/min时可以获得更高的平均膜通量,与前述四因素三水平正交实验极差分析得出的较佳运行工况一致。
从较优工况S7下平板陶瓷膜处理油田采出水的通量曲线和平均通量可以看出,在开始的1h内通量衰减快,膜通量由80L/(m²·h)迅速降至32.1L/(m²·h)。此阶段膜污染形成的主要原因是浓差极化;在60~2400min,膜通量衰减速率开始减缓,平均膜通量基本稳定在27.82L/(m²·h)附近,此时膜表面形成的滤饼层较稀疏,原水中的污染物颗粒仍然可以通过,因而对膜的过滤性能影响较小,并且水力反冲洗的水力冲刷作用能冲击掉稀疏的滤饼层上部分的污染物颗粒,因而效果显著,导致膜通量衰减缓慢;在2400min之后,随着膜过滤进程的进行,滤饼层逐渐变得密实,此时水力反冲洗对通量恢复几乎没有效果;在3300min时,膜通量已经降低至14.87L/(m²·h),此时滤饼层已经成为泥饼层,对膜孔和表面的堵塞程度十分严重,此时的膜通量迅速下降,管内压力也迅速增大,仅依靠水力反冲洗已经不能恢复其通量,需要对其进行化学清洗。这说明即便在较优运行参数下,膜污染依然不可避免。因此,判定膜污染的主要成分以及考察膜的污染阻力分布对于阐明膜污染机制是必要的。
2.3 油田采出水膜污染形成机制分析
(1)膜污染成分分析。采用能谱分析(EDS)对原水和平板陶瓷膜污染层进行了元素组成及含量对比表征,可以看出,原水层中Cl、Na元素含量较高,体现了油田采出水中无机盐含量很高的特点;C元素在原水和污染层中的占比均较大,污染层中O、Si、S元素较原水出现了富集,说明油田采出水中有机污染物含量较高。此外,污染层中含有Ba、Fe、Ca和Mg等无机金属元素。这说明无机金属离子也是导致膜污染的重要因素。
(2)膜污染阻力分析。实验中通过3次平行实验测定并计算各部分过滤阻力,陶瓷膜各部分过滤阻力及占总阻力比例的平均值。在本条件下,平板陶瓷膜自身阻力Rm,即由膜自身性质决定的阻力,约占总阻力的24.5%;浓差极化层阻力Rc约占总阻力的39.7%,这部分阻力主要发生在膜滤开始阶段。凝胶层阻力Rg约占总阻力的27.7%,这部分阻力是由于溶质吸附在膜面直至浓度达到饱和后沉积在膜表面所产生的,需要通过高强度的反冲洗或者化学清洗来去除。膜孔内阻力和凝胶层阻力占总阻力的65%以上,对过滤影响较大,尤其是膜孔内阻力,对膜污染起着主要作用。
3 结论
(1)正交实验得到的较优运行工况为初始膜通量80L/(m²·h),过滤时间10min,反冲洗时间30s,曝气强度3L/min,此工况下平均膜通量为27.82L/(m²·h),出水水质满足回注要求;对结果进行方差分析,四因素的影响顺序为初始膜通量>反冲洗时间>过滤时间>曝气强度。
(2)胺类或酰胺类、烃类、羧酸类、芳香族、醇类等有机化合物是造成陶瓷膜污染的主要污染物,Si、Fe、Ca、Mg、Ba等无机盐离子也是膜污染的重要组成部分。
(3)陶瓷膜自身阻力、膜孔内污染阻力、浓差极化层阻力、凝胶层阻力分别占总阻力的24%、40%、8%、28%。膜孔内阻力和凝胶层阻力占总阻力的65%以上,对过滤效果影响较大。