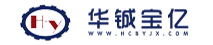
含油污水面广量大,在石油开采、石油炼制、石油化工、油品贮运、邮轮事故、轮船航运、车辆清洗、机械制造、食品加工等过程中均会产生含油污水。油污染作为一种常见的污染,对环境保护和生态平衡危害极大。人们已经对此进行了充分研究,获得了许多行之有效的除油方法,并且还在进行不断的开发创新。膜技术是近30年发展起来的一项高新技术,也是当前促进改革和保证社会持续发展的关键技术之一,已在能源、电子、化工、环保、医药等领域发挥着独特的作用。本文就膜技术在含油废水处理中的应用作综合探讨。
1 油污水的物理化学性质
含油污水中的油分一般认为以浮上油、分散油、乳化油等3种状态存在。
(1)浮上油。它铺展在污水表面形成油膜或油层,这种油的油滴粒径较大,一般大于100μm,占含油量的70%~80%以上。
(2)分散油。它以油粒形式分散在污水中,不稳定,经静止一段时间后往往变成浮油,这种油的粒径在25~100μm。
(3)乳化油。它在污水中呈乳浊状,细小的油珠外边包着一层水化膜且具有一定量的负电荷,水中又含有一定量的负电荷,水中又含有一定量的表面活性剂,使乳化物呈稳定状态,油粒径一般在0.1~25μm之间,油粒之间难以合并,长期保持稳定,难以分离。
2 处理现状及膜法处理的特点
目前处理含油污水基本沿用老三套流程:即由机械分离、凝聚沉淀和活性污泥处理。这种处理方法一般消耗能量大,水也不能回用,从环境保护和节省能源的角度考虑,要求有新的方法对含油废水进行深度处理。含油废水同时含有表面活性剂和其他可溶性有机物,所以在除去油分的同时,必须考虑BOD和COD成分的除去。
含油废水的3种存在状态,即浮上油、分散油和乳化油,其中前两种比较好处理,经机械分离、凝聚沉淀和活性炭吸附,油分可降低到几mg/L以下。而乳化油含有表面活性剂和起同样作用的有机物,油分以微米数量级大小的粒子存在,所以难以分离。超滤膜的孔径可以是几纳米,它可使油分浓缩,使水和低分子有机物透过,实现油水分离。膜法进行油水分离的特征是:
(1)纯粹的物理分离,不需要加入沉淀剂。
(2)不产生含油污泥,浓缩液焚烧处理。
(3)虽然废水中油分浓度变化幅度大,但透过流量和水质基本不变,便于操作。
(4)膜法一般只需压力循环废水,设备费用和运转费用低,特别适合于油分浓度几千mg/L以上含油废水的处理。
随着膜技术的飞速发展,其应用范围已触及各类工业操作过程,当前的研究和实践表明它在油水分离领域也逐渐显示出强大的发展潜力。根据膜本身结构的特点,选择适宜的膜过程和膜组件,可一次去除水体中100μm以下油珠,对分散油和乳化油的适应性均很强,去除率大于90%,且无二次污染,过程无相变,膜组件结构简单,流程缩短,设备能耗低。常用的膜分离技术有微滤(MF)、超滤(UF)、反渗透(RO)和纳滤(NF),超滤应用较多。
3 分散油的处理
在水中以油粒形状分散在污水中呈分散混合状态的油叫分散油。它产生于油槽压舱水、船舱水、压缩机排水、机械工厂台面废水等。这些废水在贮槽内静止就能进行分离。重力分离法、粗粒化法、过滤法、气浮法等都是比较经济的处理技术。膜分离法相对于这些方法来说,占地面积小,分离效果不受震动摇摆的影响,不需预处理,不需添加药剂,装置密闭,特别适合于在船舶上使用。
用超滤技术处理含分散油废水时,处理槽内的含油废水经超滤后,浓缩液返回处理槽,随浓缩进行分散油粗粒化,膜上会覆盖上一层油膜,水通量下降到一定程度,分离就不能进行。不同含油废水的浓缩界限不同,浓缩率一般从75%~95%。为保证流量恢复,要定期用含洗涤剂或表面活性剂的清洗液清洗。油是主要的污染物,如果吸附在膜上的油能够与含表面活性剂和乙醇的胶囊液形成微胞乳胶,它就可能完全被去除,使膜的流量得到恢复。
由于分散油的粒径较大,无机膜在处理这类含油废水时具有突出的优势,主要表现在通量高、使用寿命长、且可采用相对孔径较大的膜。因此,近年来无机膜在处理这类含油废水方面得到了越来越多的应用,如油田采出水、含油废水的前处理等。Chen及Humphery等人采用Membralox陶瓷膜进行了陆上和海上采油平台的采出水处理研究,经过适当的预处理后取得了较好的结果。原水悬浮物含量73~290mg/L,油含量28~583mg/L,出水悬浮物含量小于1mg/L,油含量小于5mg/L。
4 乳化油的处理
4.1 乳化油的性质
油水乳浊液在金属机械加工过程中被广泛用于工具和工件的润滑和冷却,但因在使用过程中易混入金属碎屑、菌体及清洗金属加工表面的冲洗用水,而使得使用寿命非常短。这类废水主要有金属切削液、金属清洗液、润滑液等。此类废水的特点是油处于乳化状态,油滴直径在1μm以下,采油一般的方法难以得到理想的处理效果。比如用重力分离和粗粒化法处理都比较困难,有的采用电解和溶剂萃取法进行处理,但其操作比较复杂,而且费用高。
有代表性的水溶性切削油性状列于表1。
表1:水溶性切削油性状
水溶性切削油 | 外观 | pH | COD/(mg/L) | BOD/(mg/L) | 油分/(mg/L) |
FC-1的25倍稀释液 | 乳白色 | 9.8 | 12300 | 4604 | 27500 |
GC的35倍稀释液 | 乳白色 | 9.0 | 10500 | 3123 | 23500 |
EE-56的20倍稀释液 | 乳白色 | 9.6 | 14500 | 2863 | 40500 |
使用的油分浓度大约为1%~50%,乳化油粒子直径分布在1~10μm范围内,大部分是2~3μm。pH属碱性,在9~11的范围内,外观呈乳白色。
膜法处理乳化油废水,不需要破坏乳液就能进行分离浓缩,虽然需添加某些絮凝剂,但并不增加污泥量,而是随同浓缩油排出,可直接进行焚烧处理。同时,由于乳化油含表面活性剂,膜面污染较少,可长期运转,通过适当地选择膜材料和组件形式,不需调整pH值和前处理。
4.2 处理方法
单独的油分子就其分子量而言小得可通过超滤膜,而对这些含油废水用超滤法处理则能成功地分离出其油相,这是因为油水界面的表面张力足够使油滴不能透过已被水浸润的膜,经过超滤后渗透液中的油浓度通常低于10mg/L,已达到排放标准,可排入阴沟。而浓缩液中含油达30%~60%,可用来燃烧或它用。
因为低分子物质透过超滤膜,所以它对COD、BOD成分的分离率不高。由于表面活性剂的透过,也往往把油分带入透过液,所以在多数情况下,需要与其他废水合在一起,采用油活性污泥法进行二次处理,也可以用反渗透单独处理。
考虑到含油废水超滤处理时对膜的强度要求较高,另外膜还必须有一定的耐热及耐酸碱性能,因此常采用聚砜超滤膜。但聚砜的疏水性能及亲油性能使得聚砜膜用于含油污水处理时,造成膜通量低和易污染。文献显示,在聚砜分子中经过磺化引进负电荷的亲水基团磺酸基,可显著改善膜的透过流量,而且抗污染性能也有所改善。
近年来,国外对陶瓷膜在处理含乳化油废水中的应用进行了广泛的研究。采用ZrO2陶瓷膜对乳化液进行过滤处理,结果表明:采用螺旋湍流促进器可以延迟膜的污染,提高膜的过滤通量,降低循环量和操作能耗。另外,对膜的化学清洗方法作了研究,结果表明,表面活性剂与HNO3的两步清洗可以较好地恢复膜过滤通量,并具有良好的重复性。
在超滤处理含有类高污染料液时,一般采用管式或板框式。近年来对卷式组件的改进提高了其抗污染的能力,这些组件正在代替造价高的板框式和管式组件。
表2给出了含水溶性切削油废液用超滤技术处理时的透过流量和透过液中油分浓度的关系(操作条件:温度90℃,压力0.14MPa,流速1267mL/s,采用Alcoa公司管状超滤膜,材料为陶瓷)。透过液中油分浓度基本上不受浓缩倍数的影响,对油分的脱除率非常高。
表2:超滤技术处理水溶性切削油的透过液水质
原液油分浓度(mg/L) | 透过液流量(L/m²·h) | 透过液油分浓度(mg/L) | 油分脱除率(%) |
34000 | 40.0 | 33 | 99.90 |
50000 | 36.4 | - | - |
99000 | 28.7 | 28 | 99.97 |
147000 | 14.6 | 12 | 99.99 |
187000 | 14.6 | 28 | 99.99 |
表3 是超滤处理含压延油废水时透过水水质(用Alcoa管状超滤膜,材料为陶瓷),浓缩到15.5倍时,油分、总含固量、COD的浓缩倍数相对原液来说分别是24.5、50.5、14.4倍,而透过液相对原液仅是0.94、1.57、1.95倍。从中可以发现油分基本上没有变化,总的脱除率还是很高的。
表3:超滤技术处理压延油废水的透过水水质
指标 | 原液 | 透过液 | 5倍浓缩液 | 透过液 | 10倍浓缩液 | 透过液 | 15.5倍浓缩液 | 透过液 | |
油分 | 浓度 (mg/L) | 9880 | 62 | 56576 | 63 | 129590 | 77 | 241260 | 58 |
脱除率 (%) | 99.37 | 99.89 | 99.94 | 99.98 | |||||
总含固量 | 浓度 (mg/L) | 10000 | 1890 | 47340 | 2300 | 12800 | 2710 | 505000 | 2960 |
脱除率 (%) | 81.10 | 95.14 | 97.88 | 99.41 | |||||
COD | 浓度 (mg/L) | 36500 | 1750 | 158500 | 2430 | 348900 | 2390 | 524300 | 3401 |
脱除率 (%) | 95.21 | 98.47 | 99.31 | 99.35 | |||||
BOD | 浓度 (mg/L) | 3400 | 730 | - | - | 30000 | 660 | - | - |
脱除率 (%) | 78.53 | 97.80 |
4.3 应用实例
拔丝润滑油废水(含油分0.5%),沉淀120h后用NTU-2020型超滤装置处理,水通量比不进行沉淀直接超滤高得多。
把含油4%的废水用氢氧化钠预处理,沉淀120h后,用NTR-1095型反渗透装置处理,操作压力4MPa,其结果与未处理的比较列于表4。
表4:反渗透实验结果
水通量/(m³/(m²·h) | 油分脱除率(%) | |||||
30min后 | 1h后 | 8h后 | 30min后 | 1h后 | 8h后 | |
有预处理 | 0.80 | 0.28 | 0.27 | 99.99 | 99.99 | 99.99 |
无预处理 | 0.28 | 0.20 | 0.12 | 99.99 | 99.99 | 99.99 |
5 脱脂液的处理
5.1 膜技术处理脱脂液的特征
脱脂是金属涂装的前处理,是把由碱和表面活性剂组成的脱脂液喷洒在被处理物上,或是把被处理物浸在脱脂液中,而后进行水洗。脱脂液油分的浓度随脱脂处理而增加,其脱脂能力则不断下降,因此需定期废弃更新。
一般来说,脱脂液中油分浓度达到5~10g/L就需更新,脱脂油如果在脱脂液中不以乳化状态存在,就会重新附着在被处理物上。脱脂液的更新次数除了与液量和脱脂量有关外,还决定于带入水洗工厂的油量。环境保护的要求是:水洗工程应闭路循环化,如果减少带入到水洗工程的油量,则脱脂液中油分浓度增加的速度加快,脱脂液更新次数增多。
膜在这方面的应用是:用超滤浓缩脱除脱脂液的油分,延长脱脂液的使用期。其特点是:
(1)脱脂液的更新次数非常少,废液处理负荷低。
(2)脱脂液中油分浓度能够维持在允许值以下,脱脂能力和产品质量稳定。
(3)脱脂液得到充分利用,减少费用。
(4)除油操作和脱脂操作同时进行。
5.2 脱脂液的膜处理方法
间歇操作流程中,设有与脱脂槽容量相同的两个槽A和B,A槽贮有油分离后调整好的脱脂液,脱脂液槽贮的脱脂液需更新时打入B槽,同时将A槽的脱脂液打入脱脂槽。用超滤处理B槽的废脱脂液,透过液存入A槽,浓缩液排出,未达到浓缩界限时,可重新打入B槽浓缩。这样,分离油的操作可很好地进行,不影响脱脂处理。目前,超滤法处理脱脂液在国外大多采用管式膜,而国内相关方面的报道很少。
5.3 透过特性
用膜技术处理脱脂液,希望只截留油分,而不改变脱脂液的组成。但是,由于脱脂油分因表面活性剂的作用而以乳化状态存在,所以表面活性剂会有所消耗,其中消耗的多少取决于它的组成和浓度。同时,脱脂液中碳酸盐、磷酸盐、硫酸盐和其它不溶性盐类也会被膜阻止。大矢晴彦的实验表明,当温度超过25℃后,脱脂液的透过流量随温度提高而降低。
6 小结
随着科学的飞速发展,膜技术处理含油污水已逐步被人们接受并在工业中逐步得到了应用。我国也在积极研究推广膜分离技术在环境保护中的应用。过去处理乳化油、分散油时,常常采用加药破乳,同时采用使油滴絮凝的方法。这样做的缺点是造成水体二次污染,后继工序必须去除前面加入的药剂。采用膜分离法具有不需加混凝剂、不产生含油污泥、能耗低、占地面积小等优越性。在用膜分离技术处理含油废水时,只要根据废水具体情况采取相应的预处理,并且选用宽流道的膜组件,加之工艺设计合理,选用膜技术处理含油废水在技术上是可行的。随着对膜分离技术研究的深入、新材料的出现以及制膜工艺的改善,膜分离作为一种有效的分离技术,在不久的将来一定会在含油废水处理中得到更广泛的应用。