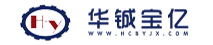
在油气田的勘探、开采过程中将产生大量的含油废水和污水,我国每年约有十几亿吨油田采出水需要处理,仅大庆油田平均每年油田采出水就高达5亿吨。油田采出水除有少量外排外,大部分经处理后回注地层,这样既解决了注水水源又保护了环境。但是,油田采出水中含有大量的乳化油(或烃类)、可溶性有机物、固体颗粒、无机离子、细菌等,用一般的物理法或化学方法很难将其分离,难以满足排放水质和回注水的要求。特别是我国已开发的陆上油田中约占10%为低渗油田,在已探明储量中有50%以上为低渗油田。低渗油田对回注水有更严格的要求,其中油含量要求小于5mg/L,悬浮物小于1mg/L。从环境保护和资源利用的角度出发,经济、有效地处理含油污水直接关系到油田的可持续发展。
与传统的分离技术相比,膜分离技术具有设备简单、操作方便、分离效率高和节能等优点、是油田含油污水处理技术的重点发展方向之一。陶瓷膜是以陶瓷材料,如氧化铝、氧化锆、氧化钛等制成的不对称分离膜,具有良好的耐腐蚀性、耐高温性、无污染易清洗、结构稳定、孔径分布窄、化学稳定性好、不易被微生物侵蚀、机械强度大及寿命长等优点。近年来,陶瓷膜在水处理中的应用研究愈来愈受到重视,并在很多过滤分离过程中得到成功应用。陶瓷膜处理油田含油污水是目前陶瓷膜应用中一个很有前景的方向,引起了国内外研究者的广泛关注。但是,由于含油污水成分复杂,影响因素较多,再加上理论基础不足,目前还主要处于实验研究阶段,未能实现大规模的工业应用。
本文从油田采出水和陶瓷膜的特点出发,介绍了陶瓷膜在油田采出水处理方面的应用,提出了面临的主要问题及建议。
1 油田采出水的特点
油田采出水是指油田在采油的过程中随原油一同采出的地层水。由于地层不同、采油过程不同,采出水的成分复杂多变,是一种以水为主体,含有一定量的油、硫化物、有机酚、氰、细菌、固体颗粒以及所投加的破乳剂、絮凝剂和杀菌剂等化学药剂为一体的复杂混合物。总体来看,油田采出水一般都具有以下特点:
(1)矿化度高,高矿化度会加速腐蚀速度,同时给废水生化处理造成困难。
(2)含大量结垢离子,采出水中含有HCO3-、Ca2+、Mg2+、Ba2+、Cr2+等结垢离子,容易在管道、容器中结垢。
(3)含油量高,高含油量的污水,回注容易堵塞地层,外排会造成油污染。
(4)含大量微生物,细菌大量繁殖不仅腐蚀管线,而且还造成地层严重堵塞。
(5)悬浮物含量高,颗粒细小,容易造成地层堵塞。
(6)有的还含高分子聚合物,使污水水质恶化,净化难度加大。
面对成分复杂、难以处理的油田采出水,单一的某种传统处理方法常常达不到要求。在实际应用中,通常将几种方法组合起来,形成多级处理工艺。这就使含油废水处理的造价高,操作复杂。随着环境保护要求对油田废水排放标准要求的提高,使得传统的含油废水处理方法的局限性日益突出。另外,采油传统的油田含油污水处理方法并不能满足对地渗透油层注水水质的要求。一方面造成大量污水无法回用,只能空注或排放;另一方面消耗大量的淡水来满足注水的要求,而淡水性质与储油层的不匹配会伤害底层,降低原油采收率。膜技术以其分离效率高、易操作、占地面积小、无需添加化学药剂等优点,近十年来一直为含油废水处理领域中的研究热点,被认为是“21世纪的水处理技术”,是一种新兴的绿色工业科技。
2 陶瓷膜处理油田采出水的原理
2.1 陶瓷膜的油水分离机理
起初用于水处理的膜是有机膜。陶瓷膜是在1996年才由日本的大日本印刷公司和东洋油墨公司开发引入市场的。陶瓷膜一经问世,就以其优异的特性获得了广泛的关注。
陶瓷膜也称CT膜,是固态膜的一种,是经特殊工艺制备而成的非对称膜,呈管状或多通道状。陶瓷膜管壁密布微孔,在压力作用下,原料液在膜管内或膜外侧流动,小分子物质(或液体)透过膜,大分子物质(或固体颗粒、液体液滴)被膜截留从而达到固液分离、浓缩和纯化的目的。
一般认为,陶瓷膜是利用膜孔的筛分截留和亲油膜面对油滴的破乳作用实现油田采出水的油水分离。油水分离膜的推动力主要是压力差、分压差、浓度差、电位差等。选择性和通量是膜分离的重要技术指标。在膜分离过程中通量和选择性往往是相互矛盾的,工程界所期待的膜是同时具有高通量、高选择性的膜。当需要从流体中除去高分子、颗粒、低分子溶质等时,常用去除率表示选择性。
常用于油水分离的微滤膜和超滤膜的膜分离机理一般以筛分原理为主,油粒的分离主要取决于膜孔径的大小。但实际上油粒在压力下的变形以及吸附、电荷等因素导致大直径油粒通过小膜孔。这一现象可用膜分相原理来解释。膜分相技术是利用多孔薄膜(分相膜)的亲油性或亲水性将液-液分散体系中的有机相(油相)和水相分开。当两种液体互不相溶,且对同一种分相膜的亲和力有一定的差别时,在一定的水力学和外力作用下,必有一种液体在膜的表面形成一定厚度的纯液层,另一种液体在该纯液层中的浓度形成梯度。在有分相的条件下,分相能力与分相产液的纯度有一定的关系。分相能力越小,产液的浓度越高。膜分相技术具有常温操作、无相变、不添加杂质、节省能源等优点,所面临的问题是膜的污染有待解决。
实际上,筛分原理和膜分相原理都不能完善地表达实际分离过程中膜的传质过程。膜的传质机理一般认为由两部分构成:膜内传质和膜表面传质。对油水乳液而言,膜内传质比较符合孔模型的筛分原理。超滤和微滤基本上都是典型的筛分-过滤过程,在不考虑浓差极化时,将流体通过膜孔的流动看作毛细管内的层流。实际上,膜分离受表面浓差极化和凝胶层形成的影响。
2.2 陶瓷膜的优势
在污水处理中,与有机膜相比,陶瓷膜具有热稳定性好、刚性及机械强度大、化学稳定性好、抗微生物能力强、易清洁等优点。此外,还具有孔径分布狭窄,使用寿命长等优点。因此可以在处理要求更高、使用场合更为苛刻的环境中使用。
在对油田采出水的处理中,陶瓷膜表现的尤为卓越。其优点主要表现在:
(1)材料具有亲水憎油特性,有利于防止有机类物质的污染。
(2)抗微生物能力强,与一般的微生物不发生生化或化学作用。
(3)材料的化学稳定性好,清洗再生性好。
(4)机械强度高,耐冲刷,对使用和清洗条件的要求不高。
(5)出水水质好,水质稳定,完全能满足低渗透油层注水水质的要求。
从目前国内外陶瓷膜研究应用的情况来看,陶瓷膜处理采出水的设备投资和运行成本较其他水处理方法也具有较明显的优势,这主要是由于陶瓷膜设备使用寿命长(一般三年到五年)、占地面积小、配套设施少等。
3 陶瓷膜处理油田采出水的应用
陶瓷膜处理油田采出水的研究始于美国在1991年开始的用于油田回注的采出水研究,并在路易斯安娜、墨西哥湾的海上及陆上油田进行了小规模生产试验。该滤膜材质为具有不规则微孔的α-铝矾土,由法国生产,商品名称为Membralox。Alcoa公司的Chen等的试验结果表明,采出水经预处理后,再经陶瓷膜横向流微滤,处理效果十分明显,滤后水中含油量可降至2~8.8mg/L,总悬浮固体含量可降至1mg/L以下,大于2μm的固体颗粒的去除率为99.2~100%。他们采用0.2~0.8μm陶瓷微滤膜在美国墨西哥湾采油平台上进行试验,在保持膜面流速2~3m/s,进口含油为28~583mg/L的情况下,出口含油降到所用方法能够测到的极限值,固体悬浮物含量从73~290mg/L降低到1mg/L以下,采用恒流量方式中,过滤速率保持1600L/(m²·h),依据操作条件的稳定程度,清洗周期为66~330h。这些早期的研究,为陶瓷膜处理油田采出水的工业性试验奠定了基础。
Simms等分别采用聚合物超滤膜和陶瓷微滤膜对加拿大西部油田采出水进行了实验研究,在进口含油为125~1640mg/L,悬浮物含量为150~2290mg/L的条件下,前者过滤速率在50~90L/(m²·h)之间,过滤后水中含油小于20mg/L,后者采用0.8μm陶瓷微滤膜,通过预处理工艺和脉冲工艺,膜面流速保持在0.5~4m/s之间,运转周期为24~73h,过滤速率可保持在200~500L/(m²·h),滤过水含油<20mg/L。
Buarki等在科威特的“Edena-1”试验场采用微孔陶瓷膜对采出水进行了处理试验。对分散油含量4800mg/L,油脂含量6000~500000L/(m²·h)的来水,经处理后可分别降至5mg/L和20~40mg/L,COD去除率为83%~89%。
Ebrahimi等采用陶瓷微滤膜和纳滤膜两级处理过程对油田采出水进行了处理。在跨膜压差1bar,膜面流速0.6~1.3m/s,过滤速率3.1~3300L/(m²·h),进水温度60℃条件下,0.1μm微滤膜的通量5h后由初始的1150L/(m²·h)降到200L/(m²·h),两级处理后原油去除率达99%,TOC去除率达39%。此外,他们还通过陶瓷膜微滤、超滤和纳滤膜多级处理过程使原油去除率和TOC去除率提高到99.5%和49%。
20世纪90年代后期,国内也有陶瓷膜用于处理油田注水的试验报道。王怀林等人在实验室研究了不同温度、压差膜面流速、孔径等参数对陶瓷膜处理油田采出水时过滤特性的影响,针对膜处理中关键的膜污染问题,研究了延长过滤周期的几种处理工艺,确定了一种较好的清洗方案。他们还通过对国产的和U.S.Filter的陶瓷微滤膜的对比研究发现,国内陶瓷微滤膜已达到国外同类膜的水平,且价格仅为国外的1/4~1/6。
江汉石油机械厂联合抚顺石化研究院共同利用U.S.Filter公司的0.8μm陶瓷膜过滤器,对辽河油田茨榆沱采油厂注水站砂滤罐的出口水进行了处理试验研究。原水中油含量为20~50mg/L,固体悬浮物含量20~50mg/L,装置进口流量为20gpm,出口流量为5gpm,经膜装置处理后,水中悬浮物固体含量基本上小于1mg/L,颗粒直径小于1μm,含油量小于3mg/L,可满足特低渗透油田注水水质要求。
彭德强等利用美国进口的陶瓷膜过滤试验装置,对油田常规工艺处理后的采出水进行了深度处理试验研究。原水中油含量20~50mg/L,固体悬浮物含量80~100mg/L,COD值180~250mg/L。经膜装置处理后,水中油含量降到5mg/L以下,固体悬浮物含量降到1mg/L,COD值降到100mg/L,水中悬浮物粒径小于1μm,试验取得了满意的效果。
徐晓东等采用陶瓷膜处理宝浪油田采出水,处理后的采出水完全能满足宝浪油田注水水质要求。0.1μm膜处理后,滤出水中悬浮物含量平均值为0.417mg/L,粒径中值小于1μm;0.2μm膜处理后,滤出水中悬浮物含量平均值为0.57mg/L,粒径中值小于1.5μm;滤出水中油含量低于检测限,膜清洗周期为85h。
徐俊等对大庆油田采油二厂聚南八污水处理站出水采用孔径为0.1μm的ZrO2陶瓷超滤膜进行了处理,通过选择适宜的操作条件,使采出水中浊度、油和悬浮物的去除率分别达到97%,98%,94%以上,硫酸盐还原菌(SRB)、铁细菌(IB)、腐生菌(TGB)的去除率接近100%,渗透液浊度<1NTU,原油含量和悬浮物由来水的12~25mg/L和13~26mg/L均下降到不足1mg/L,粒径中值由原来的0.90~4.68μm变为未检出。除部分点腐蚀外,超滤出水达到了油田低渗透层回注水质A1级要求。
罗杨等采用0.1μm的陶瓷膜对胜利油田东幸采油厂采油四矿油水联合站的二次沉降污水进行处理,对膜污染和清洗进行了初步研究。结果表明,在膜处理过程中对污水采用曝氧方式过滤的效果要好于密闭方式。对悬浮物含量28.1mg/L,油含量22.7mg/L的来水经陶瓷膜曝氧处理后,两个指标分别下降为0.77mg/L和0.11mg/L。对膜污染物的分析表明,主要堵塞物为Fe(OH)3沉淀及原油。化学清洗不能做到对膜污染物的彻底清洗,有关工艺和方法有待进一步完善和提高。
4 问题及建议
从文献资料和实际现场试验结果看,陶瓷膜在处理油田采出水方面具有很好的效果,已得到了一定的应用和发展,其工业应用是可能的,但要实现大规模的工业应用还有一些迫切的问题需要解决,必须做进一步的基础性和工程研究工作。
归结起来,陶瓷膜处理油田采出水面临的问题主要有以下两点。
(1)设备投资成本大,运行费用高。降低装置的一次性投资,通过工艺条件的优化设计和强化传质过程,降低操作成本是当前实现陶瓷膜大规模应用的首要条件。
(2)膜的清洗再生方法。由于各油田的水质情况差别很大,同一地层不同时间段的水质也很不稳定,污染物的结构和成分也很复杂多变,必须针对具体对象开发合适的清洗方法。此外,通过预处理等方式,实现提高膜通量的运行稳定性、减少清洗的次数,避免对膜的清洗损伤也是十分关键的问题。
综上,陶瓷膜处理采出水主要适用于必须进行注污水开发的低渗透或者特低渗透油藏的回注水处理,且是常规处理工艺难以达到处理要求或采用其他非常规处理工艺的处理费用比采用陶瓷膜更高的情况。陶瓷膜水处理工程的上马必须面向对象,从小试做起,对适用性进行论证和优选,不能直接进行大规模的推广应用,避免造成浪费。