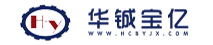
1 陶瓷分离膜的发展历史
陶瓷膜的研究始于本世纪40年代,其发展可分为3个阶段,即用于铀同位素分离的核工业时期、液体分离时期和全面发展时期。
美国曼哈顿原子弹制造所用的铀价格极其昂贵,寻找更便宜的铀提浓方法显得十分重要,通过多孔材料的气体扩散分离技术得到高度重视。由于UF6的活性很高,限制了多孔材料的选择,只能采用金属或陶瓷材料。通过反复实验,选定在多孔陶瓷管内壁涂上一层或几层具有阶梯分布的过渡层和分离层,这就是早期的陶瓷分离膜。这种膜用于UF6同位素的分离,分离系数为1.0043,因此要把含量极少的235UF6提浓到3%以上,需采用多级过程,有时达到千级以上。法国于50年代也加入了这一研究工作,其开发办法是由Commissariat al’Energie Atomiquet(CEA)主持,并SFEC子公司,专门进行在多孔支撑管上制备分离层的研究,并组装成组件。至少有3家公司配合CEA进行多孔支撑体制备技术的研制,分别是Desmarquest,LeCarbone-Lorraine,Compagnie Generale d’Electroceramique(CGEC)。通过政府和配套公司的合作,法国于60年代末开始了工业过程的开发,其目标是为Pierrelatte军用铀富集工厂提供陶瓷膜。其支撑体由CGEC生产,分离层由SFEC提供,所建成的工厂目前尚在运行之中。
1973年石油危机以后,核能得到高度重视,迫切需要大量的浓缩铀。欧洲 拟联合建立大型Eurodif气体扩散分离工厂。在1975年以后的6年里,总共组装了4000000m²的分离组件,浓缩的铀可供90座900MW的核电站使用。
美国所进行的工作规模更大。美国能源部(DOE)建立了几个大型气体扩散分离工厂,其规模约是Eurodif的两倍。在前苏联,也进行了类似的工作,但具体情况不详,只知道其多孔金属膜处于 地位。
70年代是陶瓷膜用于铀浓缩的辉煌时期。进入80年代,随着激光技术的出现,陶瓷膜浓缩铀已不占技术优势,失去核工业市场的陶瓷膜厂家开始积极寻找新的应用领域,无机陶瓷膜发展进入了第二阶段——液体分离时期。Ceraver(CGEC)和SFEC率先开展了这方面的研究工作。由于当时在法国公开陶瓷膜技术秘密尚不可能,SFEC引入了美国Oak Ridge 实验室开发的、由Union Carbide注册专利的ZrO2动力膜技术,并结合从核计划研究中获得的经验,对这种动力膜ZrO2涂层进行了烧结处理,将分离层固定在多孔支撑体上,这即是现在的ZrO2陶瓷超滤膜。
SFEC从1980年开始成套出售这种商标为Carbosep的膜设备。考虑到陶瓷膜在核能领域已无多大前途,CEA于1987年将SFEC出售给法国的Rhone-Poulenc公司,后者将其与高分子部分合并起来,成立了一家新的公司,即 的TechSep公司,其主要产品是在内径6mm碳管内涂上ZrO2的超滤膜。1980年Ceraver公司也开始将陶瓷膜转向民用领域,开发了一系列的α-Al2O3陶瓷微滤膜,这种膜应用领域非常广泛。 在技术方面, 采用了多通道多孔陶瓷支撑体。采用多通道支撑体,并在通道内沉积分离层的设想并不是新的概念,而是来源于1966年的美国专利。多通道陶瓷膜的出现,使得膜的强度大大加强,且生产成本有明显下降,并且在应用过程中也可节约能量。可以说,多通道陶瓷膜的出现是无机陶瓷膜工业化过程中重要的技术进展。Ceraver公司是 家出售多通道无机陶瓷膜的公司,从1984年起,19通道的陶瓷膜以Membralox商标出售。与SFEC相比,Ceraver对膜分离过程进行了更为深入的研究,结合陶瓷膜的特点,将错流过滤和反冲洗技术进一步发展,使得无机陶瓷膜所具有的优势得以充分发挥。早期开发的Membralox膜主要是α-Al2O3微滤膜,当时开发的γ-Al2O3超滤膜由于化学性能不好,未能在工业上推广使用。多通道ZrO2陶瓷超滤膜于1988年开发成功,它具有更为优异的耐酸碱性能。1986年,Ceraver被出售给美国的Alcoa公司,1992年,该部又转让给U.S.Filter,这是目前全球较大的无机陶瓷膜及设备的供应商。
法国核计划的另一个参加者,LeCarbone-Lorraine公司利用其在碳材料上的优势制备出碳膜,并于1988年投入工业应用。而在陶瓷膜技术解密后,相继有一些公司、大学和研究机构加入了陶瓷膜的研究。由Euroceral的前雇员在80年代初建立了一个小型Ceram-Filtre公司,生产19通道、内径4mm的陶瓷微滤和超滤膜。日本也进入了这一领域的竞争,其中 的几家陶瓷公司如:NGK,Cemet,Toto,Corning等,开发的无机膜设备在工业过程中获得了成功的应用,陶瓷分离膜产业逐步形成。
进入90年代,无机分离膜,尤其是应用广泛的陶瓷膜(占80%以上)具有优异的耐高温、耐溶剂、耐酸碱能力已为人们所认识,在食品工业、生物化工、化学工业、能源工程、环境工程等领域获得越来越广泛的应用,而无机膜在气体分离、膜催化反应等领域也显示出广阔的发展前景,在全球范围引起了高度重视,无机陶瓷发展进入了第三阶段,即全面发展的时期。
这一时期的特点就是 各发达 的政府对陶瓷膜的发展予以充分的重视,将其作为一门新兴的高技术前沿学科进行研究,因而带动了陶瓷膜研究和产业化的全面发展。在政府支持下,美国一些大学和科研机构成立了无机膜研究中心,投入大量的人力、物力和财力研究和开发陶瓷膜技术。美国能源部对无机膜的应用领域展开了广泛的调查,对一些项目提供巨额资助,并与无机膜设备生产公司合作,共同开发市场,用新技术改造传统产业,推动技术进步。目前正在开发研究的主要项目有:金属清洗液的净化再生系统、油田回注水处理技术与成套设备、高温气体除尘技术、烟道气除尘脱硫一体化技术、生物化工下游产品分离净化技术、高温气体陶瓷膜分离、膜催化反应等。日本政府也对陶瓷膜的研究投入大量人力、物力,并对陶瓷膜产业化技术极为重视,短短几年时间,已成为陶瓷膜技术 的 之一。
通过以上3个阶段的发展,陶瓷膜分离技术在国外已初步产业化,尤其是陶瓷膜在80年代初期成功地于法国的奶业和饮料业(葡萄酒、啤酒、苹果酒)推广应用后,其技术和产业地位逐步确立。据1986年统计,其市场为2000万美元,并以年30%的增长速度发展着,1991年市场销售额为6600万美元,预计本世纪末,将达4~5亿美元,无机膜工程可达20~30亿美元,其中陶瓷膜占80%以上。
国外商品陶瓷膜主要有3种形式:管式、管束式和多通道式,单台组件膜面积已达6m²,民用工业成套装置规模已达160m²以上,基本形成规模化、成套化、系列化。所提供的商品膜孔径从4nm至10μm,应用较广泛的是孔径在0.2μm以上的陶瓷微孔过滤膜。
相比于发达 ,我国的无机陶瓷膜研究及产业化工作起步较晚。 自然科学基金委员会从80年代末就从材料学科和化学工程学科安排无机膜研究,设计膜制备、表征、应用、膜反应等领域,90年代又安排了重点项目进行无机膜研究,取得重要的进展,促进了我国无机膜基础研究的发展。1994、1996年在美国召开的第三、四届无机膜国际会议,我国出席人数和论文数均占第三位,显示出较强的科研基础。
80年代末,中国科学院、 教委等部门的科研人员即开始了无机膜的研究工作,取得了多项基础研究成果。其特点是从无机膜催化反应的需要出发,对膜的制备、表征进行研究,尤其重视对具有气体分离能力的金属膜、分子筛膜等进行了较深入的研究,并在膜催化反应和膜制备机理等研究领域取得了令人鼓舞的基础理论成果。南京化工大学则充分发挥自身在化学工程、化工机械、陶瓷材料3大领域的优势,致力于陶瓷分离膜的工业化技术开发,在国内率先实现了管式陶瓷膜的工业化生产。多通道陶瓷膜的研制也已取得实质性的进展,已制备出品质优良的实验样品,为进一步发展奠定了良好的工作基础。 科委对陶瓷膜发展予以充分的重视,将“陶瓷微滤膜成套装置与应用技术”列为 “九五”重点科技攻关项目,必将对我国陶瓷膜的发展起着很大的推动作用。
2 陶瓷分离膜的应用现状及趋势
陶瓷膜的工业应用目前主要是在液体过滤分离方面。首先应用在牛奶、果酒除菌过滤,采用孔径1~1.5μm的微滤膜脱除低脂牛奶中的细菌,效率达99.6%,滤速达500~750L/(m²·h),由这种工艺生产出的牛奶其低温保存期由未处理的6~8d延长至16~21d,处理过程中通过提高膜面流速而减少污染。此外,将巴氏灭菌过程与陶瓷膜结合可以生产出浓缩型巴氏灭菌牛奶,Membralox和Carbosep膜在这方面均有成功的经验。果汁澄清是陶瓷膜应用较为成功的例子之一,160m²的工业装置用于苹果汁澄清已达10年以上,生产出的果汁品质优良,更具芳香味。
陶瓷膜在酒类过滤除菌、除杂领域的应用已有近15年的历史,过滤白酒通量可达50~250L/(m²·h),对红酒则只有50~100L/(m²·h)。在啤酒生产中,采用孔径0.5μm的陶瓷膜,色度截留率仅3%,发泡蛋白没有显著损失,除菌率达100%。
陶瓷膜在生物化工领域中的应用研究是近期的热点之一,涉及领域包括细胞脱除、无菌水生产以及低分子有机物发酵液的澄清和生物膜反应器的研究。根据陶瓷膜优异的抗微生物侵蚀能力,在这一领域中应有着广泛的应用,但由于膜的污染严重,目前尚无工业规模的报导。此外,陶瓷膜在水处理、纺织工业废碱液回收、废油的高温超滤回收等领域中都已开始投入应用。
陶瓷膜在液体过滤领域中的应用已有近20年的历史,但膜污染制约着这一领域的发展。近几年关于陶瓷膜污染处理以及怎样降低膜污染的研究日益受到重视。污染机理的研究主要涉及蛋白质在陶瓷膜表面的吸附,认为与吸附相关的孔阻塞是大孔径膜通量随时间下降的重要原因。Richard等对地表水透过陶瓷微孔膜的污染进行模拟计算,并提出一些解决污染的方法:Miller等对4nm的Membralox γ-Al2O3膜的液体输运性质进行了较全面的研究,此外,一些学者用分子模拟手段去探索物质在微孔中的运动规律,这对深入研究膜污染机理是极有意义的。
减少污染的方法主要是提高膜面流速、高压反向冲洗、用各种清洗液对膜进行反复清洗。此外,一些新的方法也正在开发中,如在进料液冲入气体、采用脉冲流动、让膜处于旋转状态等。
陶瓷膜在气体分离中的大规模应用仅有铀同位素分离一例,而且这一用途也已被其它方法逐步取代。陶瓷膜在气体分离中存在的困难为:对致密膜而言,通量低、成本高,膜在高温下不稳定;而对多孔膜,则存在分离系数与膜通量的矛盾。陶瓷膜分离领域中另一个值得开发的市场是利用毛细冷凝机理进行原料气脱湿、有机溶剂回收以及强腐蚀性气体干燥等。
陶瓷膜处理气体成功的例子是电子工业用气体的净化,如U.S.Filter公司提供的产品对0.01μm尘粒脱除率达99.9999%。Ceramem公司开发了一种新型膜过滤器,它对高温气体的除尘率达99.9%以上,其压降可与袋式除尘器相比,但膜装填面积达155m²/m³。美国能源部与陶瓷膜在煤发电系统中的应用前景作了调查,认为可能的应有领域是存在的,但必须解决膜的分离因子小、膜在高温下稳定性和设备的密封问题。
根据陶瓷膜的特点和国外发展陶瓷膜的经验,陶瓷膜在我国的应用领域极其广泛。食品工业是其主要应用领域之一,诸如矿泉水生产、酒、饮料过滤、调味品、果汁过滤等,对膜设备的要求是抗污染能力强,可以蒸汽原位消毒,使用寿命长,而陶瓷膜恰具有这几个优势。
化学工业领域常涉及工艺原料气、工艺原料液的净化问题,其中少量固体杂质必须极大限度地除去。由于原料气、液常涉及高温、高压或强腐蚀性,高分子膜无法应用,只能采用无机陶瓷膜。国内的很多厂家已向有关部门提出此类问题的需求,如碱厂料液过滤、聚氰胺工艺料液净化、硅胶催化剂颗粒回收、分子筛和催化剂生产过程中的产品回收、钛白粉生产过程中偏钛酸细微粒子的回收、超细粉体生产过程中的产品回收等,均亟待解决。陶瓷膜的应用必将提高产品质量,推动 重点建设工程和技术改造的发展。
1993年,中国石油化工总公司17套延迟焦化装置,总加工量816万t,蜡油产量194万t。焦化油是一种劣质蜡油,而我国原油日趋变重,直馏蜡油收率降低,催化裂化、加氢裂化等二次加工装置原料也日趋不足,开工负荷降低,因此外用延迟焦化所产焦化蜡油去加氢裂化制造优质油品,已成为一种发展趋势。从经济效益角度考虑,焦化蜡油作催化裂化原料较好。Unocal公司有25套以上的催化裂化装置,其掺炼焦化蜡油高达进料量的30%~50%,而我国引进的4套加氢裂化装置,设计允许加工10%的焦化蜡油,但实际生产中不足10%,甚至没有掺炼,其主要原因就在于焦化蜡油中焦粉含量高,达200~300mg/g。这种焦化蜡油粘度大,所含焦粉粒径小,又涉及高温、有机溶剂等苛刻条件,到目前为止,尚未找到合适的方法解决这一重大技术难题,已成为制约我国石油化学工业发展的一个重要技术问题。以某炼油厂为例,其加氢裂化每小时可吃进29t焦化煤油,现在掺入量不足1t。如果除去蜡油中的焦粉,全年可多掺炼20万t焦化煤油,全国有20余套类似装置,其经济效益十分可观。
油田回注水净化技术是我国石油工业所面临的重大技术难题之一。我国现产原油1.4亿t,随油采出的水量约在2.8亿t左右,这些废水中含有少量石油、固体颗粒、菌体等,回注前必须除去这些杂质,否则将导致渗油口堵塞,油质变坏,导致油井报废。鉴于回注水的特殊性,对其处理技术的要求是:处理量大,净化要求高,成本低,设备经久耐用,到目前为止尚没有一种比较合适的处理方法。国外从80年代末开始用陶瓷膜技术处理这一问题,目前已经在海洋钻井平台上有规模应用。
Alcoa公司从80年代末即开始采用陶瓷微滤膜进行油田回注水净化技术的研究,其目标是达到排放标准或回注标准。油田废水经处理后,一般尚含有100×10-6~500×10-6数量级的油、脂和部分微小固体颗粒,采用陶瓷膜可以将其除去,处理后的过滤水中油、脂含量达到回注和排放标准,固含量可降至1×10-6数量级以下,展现出良好的发展前景。
环保领域应用是陶瓷膜成功的典范之一。国外陶瓷膜高温气体除尘技术已作为一种较新、较有效的技术应用于电厂除尘。国内电厂有几百座,工业锅炉几十万台,每年排尘1亿t以上。造成严重的环境污染问题,采用陶瓷膜除尘技术,所带来的经济效益和社会效益不可估量。用陶瓷膜处理金属表面清洗液,可使清洗液的使用周期从7d延至3个月以上,其环境和经济效益十分显著。全国有上千家金属表面处理工厂,若采用此技术,效益十分显著。
生物化工领域中,陶瓷膜的抗微生物侵蚀、耐高温能力倍受重视,其地位不可替代,需求量较大。
3 我国陶瓷分离膜的发展对策
总之,根据对国内石油化工、化学工业、食品工业、环境工程、生物化工等领域的调查,对陶瓷膜设备的需求十分迫切,其中许多项目是 支柱产业中的重大技术难题,又涉及 重点工程和技术改造项目,加速陶瓷膜工程化关键技术研究,对国民经济发展具有重要的促进作用。根据国内外陶瓷膜的发展现状,本着“有限目标,突出重点”,“有所赶,有所不赶”的原则,我国陶瓷膜的发展应以产业化为中心,集中力量在以下领域进行研究和开发工作:
(1)加强大面积、无缺陷商品膜的制备研究工作,重点解决Al2O3,ZrO2,TiO2,SiO2陶瓷膜的工业制备过程中的自动控制和质量检测问题,其目标是尽快使我国的商品陶瓷膜达到国外 技术水平。应重视的研究方向有:
纳滤膜:主要是膜的制备和膜的输运机理研究。一般尚是以溶胶-凝胶法在超滤基础上改性而成。
复合膜:金属氧化物之间的复合:如让片状的Al2O3与球形的TiO2,ZrO2或CeO2粒子混合,以改善Al2O3膜的化学和热稳定性;将RuO2和TiO2混合在氧化铝支撑体上成膜,可以得到具有电导性质的多孔膜,这种膜在电分离或化学反应器领域具有发展前景。有机-无机材料之间的复合:这源自有机-无机高分子材料,通过复合,使膜兼具有机、无机的优势;目前研究的主要有两类:聚硅氧烷与氧化硅中间层的复合和聚磷酸盐高分子与碳管的复合。其它复合膜尚有:碳与碳纤维复合膜、玻璃-陶瓷复合膜、陶瓷-不锈钢复合膜等。
陶瓷膜的改性:对已有的膜进行改性,是改变膜性能的重要技术,使膜更适合特定的应用领域。改性的主要目标有3个:降低有效孔径,得到超薄膜或改变膜的内表面物理化学性质。例如用SiO2,TiO2,MgO的聚合溶液对Al2O3膜的改性,也可用CVD,MOCVD等技术对膜的表面改性。
致密膜:主要提高金属膜的稳定性,降低膜的厚度。对陶瓷致密透氧膜而言,则重点在于新材料的开发和制备技术的研究。
其它膜:如阳极氧化铝膜、玻璃膜、电导膜、沸石膜和分子筛膜等,制备工艺的研究较多,其目标是进一步改进性能,开发大面积工业用膜的制备技术。
新的膜制备方法:其目标是降低膜的孔径、降低制备成本、开发性能更优异的膜,目前研究的有:高分子材料的热裂解、CVD、ECVD、MOCVD、电泳、热蒸发、阴极溅射、超临界沉积技术等。
(2)提高陶瓷膜成套装备技术水平,扩大应用领域。包括组件设计、装置成套化和应用技术开发,其目标是使装置紧凑、能耗较低,重点是防止膜的污染和开发出合适的清洗方法。目前正在开发的方法有:荷电以提高膜的通量和选择性,采用脉冲流动方式以提高通量、降低膜的污染,旋转管式膜以改善膜的过滤性能等。在装置方面,除成熟的管式和多通道式以外,目前根据特定目标而开发的平板膜、中空纤维膜、金属筛网支撑陶瓷膜等均展示出较好的发展前景。
(3)重视对膜反应技术和反应膜制备技术的研究工作,以期在新的高技术竞争中占有技术优势。目前尤其要加强膜反应的化学工程基础研究,建立数学模型,开发放大技术,解决高温膜反应器的密封问题。