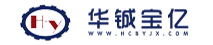
1 前言
氧化铝是近年来国内外研究较为广泛的一种无机分离膜材料。它的出现与迅速应用,一方面是由于膜分离过程在高温、腐蚀性环境的实际需要;另一方面是由于近年来发展起来一些新的陶瓷膜材料制备工艺,使得晶粒细小、孔径均匀、质量可靠陶瓷膜的制备成为可能。目前已商品化的多孔陶瓷膜的构形主要有平板、管式和多通道3种。多通道陶瓷微滤膜由于其较高的通量、优异的机械性能和良好的截流能力,已日益显示出其极强的竞争力。
面向应用体系的陶瓷膜过程设计主要包括膜微观结构、膜材料性质、过程操作参数的优化设计。无机陶瓷膜的分离性能与其结构、材料性质是密切相关的。多孔陶瓷膜的结构参数主要包括平均孔径和孔径分布、膜厚度、孔隙率、孔形状、曲折因子等决定了膜的渗透分离性能;膜材料性质包括膜的化学稳定性、热稳定性、表面性质及机械强度等,它们不仅影响膜的渗透分离性能,更与膜的使用寿命密切相关;操作参数主要包括膜面流速、操作压力、温度等,影响膜过程的浓差极化和膜污染程度,对渗透通量和分离性能都有影响。无机陶瓷膜经过多年的发展,加上本身具有耐高温高压、耐腐蚀、耐有机溶剂等优点,并且膜通量高、清洗方便、使用寿命长,在众多领域获得了广泛的应用,成为膜领域发展较为迅速、也是较有发展前景的品种之一。
2 陶瓷分离膜制备方法
无机陶瓷膜的主要制备技术有:采用溶胶-凝胶法制备超滤膜;采用化学气相沉积技术制备微孔膜或致密膜;采用阳极氧化制备陶瓷分离膜和固态粒子烧结法及假凝胶法制备膜载体及微滤膜。
2.1 溶胶-凝胶法
以金属醇盐及其化合物为原料,在一定介质和催化剂存在的条件下,进行水解-缩聚反应,使溶液由溶胶变成凝胶,再经干燥、热处理而得到合成材料的方法称为溶胶-凝胶法。目前,该方法已成为陶瓷分离膜的主要制备方法,它不仅操作方便、设备简单,更重要的是孔径分布狭窄(0.001~0.1μm),孔径大小可通过调节溶胶和热处理过程来控制,分离效率高。
2.2 化学气相沉积技术
化学气相沉积技术(CVD)已在半导体集成电路的制造等领域得到广泛的应用,它也同样适用于氧化铝分离膜的制备,其特点是可以控制改变微孔膜的孔径。CVD法制备氧化铝分离膜,需要载体孔径3~10nm以上,反应应在高温下进行,反应物先吸附在载体表面或微孔内,再发生表面反应,即其机理为吸附-表面反应。
2.3 阳极氧化法
微孔氧化铝分离膜的研制,先前多以阳极氧化法,近十多年来这种工艺得到了不断完善,其制备方法是以高纯度金属箔为阳极,在酸性电解质溶液中进行阳极氧化。阳极氧化法制备的膜包含两个区域,一个是大面积的微孔层,另一个是屏障层。屏障层是毗连的,实际起着支撑作用,阳极氧化法制备的膜呈很规则的直径,孔径均匀,形成六角形微孔网络。
2.4 固态粒子烧结法
烧结法是选择氧化铝为原料,添加适量助溶剂、粘合剂、增塑剂等,经成形在一定温度下烧结而成。烧结过程中,粉末颗粒间相互接触部分被烧结在一起,粉末颗粒间相互接触部分被烧结在一起,粉末间的空隙形成相互贯通的微孔,孔径范围为0.1~600μm,适应于微孔过滤,所以该法被用来制备多层复合膜中的大孔陶瓷支撑体及中间层。陈艳林等以淀粉作造孔剂,利用普通陶瓷原料为主,适当添加高温粘结剂,用烧结法制备出气孔率较大,气孔分布均匀、抗压强度较大的多孔陶瓷。
2.5 假凝胶法
假凝胶法是将溶胶和一定量的微细粉配制成稳定的悬浮液,将悬浮液涂覆在一定孔径的载体上而制备无机分离膜的方法,该方法适用于制备微滤膜,适宜在医药、食品、纯水制备等领域中应用。李月明等利用Al(NO3)3为前驱体,以氨水水解制备勃姆石溶胶,在溶胶中添加一定量PVA溶液和不同粒径的微粉末制备出Al2O3假溶胶,采用浸渍法涂膜,在一定温度下烧成制备出孔径分布均匀,无缺陷的微滤膜。
3 陶瓷分离膜的过滤机理
陶瓷分离膜的过滤机理包括静态过滤和动态过滤。
3.1 静态过滤
静态过滤或称“死端”过滤,是一种传统过滤方式。对陶瓷膜来说,其过滤是集吸附、表面过滤和深层过滤结合。对液-固、气-固系统的过滤与分离来讲,其过滤机理主要是惯性冲撞、扩散和截留。
3.2 动态膜过滤
动态膜过滤又称十字流过滤。十字流过滤的原理是使原料液从很高的流速平行流过膜表面,以限制溶质向膜面的沉聚;同时还有助于强化膜面已沉积的溶质向主体流扩散,从而有效地削弱浓差极化,实现高速连续过滤操作。
3.2.1 反渗透
反渗透亦称逆渗透(RO)。是用一定的压力使溶液中的溶剂通过反渗透膜(或称半透膜)分离出来。因为它和自然渗透的方向相反,故称反渗透,根据各种物料的不同渗透压,就可以使大于渗透压的反渗透法达到分离、提取、纯化和浓缩的目的。
3.2.2 超滤
超滤的作用原理为滤膜的筛除作用,即在一定压力作用下,超滤膜的孔隙能通过溶液及由溶液带走的小于滤膜孔隙尺寸的溶质(如无机盐类),而截留大于孔隙尺寸的溶质(如有机物胶体等)。超滤膜主要应用于液体中的颗粒物、胶体和大分子与溶剂等小分子物质的分离,如溶液中细菌、热源、病毒以及胶体蛋白质、大分子有机物,分别实现净化分离和浓缩的功能。
3.2.3 纳滤
纳滤(NF)膜早期称为松散反渗透(Loose RO)膜。纳滤膜介于反渗透与超滤膜之间,NF膜主要去除直径为纳米级的溶质粒子,截留分子量为100~1000,几乎对所有的溶质都有很高的脱除率,其操作压力一般小于1.5MPa。
3.2.4 微滤
微滤与超滤和反渗透膜技术相比,微滤的过滤速率要高2~4个数量级,特别是进料的悬液已不再是超滤和反渗透的单相流体,一般都是固液两相流体。
4 陶瓷分离膜的应用研究
4.1 膜的微观结构对渗透通量的影响
4.1.1 膜孔径的影响
膜孔径是影响通量和载体截留率等分离性能的主要因素,一般说来,孔径越小,对粒子或溶质的截留率越高而相应的通量往往越低。
4.1.2 膜厚度的影响
膜厚度对膜性能的影响主要表现在渗透通量上,由于膜厚度的增加必然使流体通过的路程增加,因此过滤阻力增加,通量下降。
4.1.3 膜孔隙率的影响
孔隙率高的膜具有较多的开孔结构,所以在相同的孔径下具有高的渗透通量。一般来说,多孔无机膜特别是陶瓷膜,其膜层的孔隙率在20%~60%之间,支撑体孔隙率高于分离层,对微滤膜而言,孔隙率大于30%。
4.2 膜材料性质的研究
膜材料的亲水性和膜表面荷电性对实际体系的分离性能有很大影响,膜表面性能的电化学性质会对膜和流体之间的作用本质和大小产生影响,从而影响溶质和溶剂(或大分子颗粒)通过膜的渗透通量。通常表征膜表面电化学性质是膜的ξ电势和等电点,也有用表面电荷和零电荷点等来表征。
4.3 溶液性质对膜过程的影响
溶液性质是指液粘度、pH、离子强度、电解质成分等。这些性质直接影响到与之接触的膜的表面性质,同时溶液性质的变化还会改变其中所含的待分离的颗粒或大分子溶质的性质,造成膜与溶剂、与颗粒溶质等之间的作用发生变化,从而影响到膜的分离性能。一般认为,pH及离子强度的变化会改变体系性能如胶体。
4.4 操作参数对膜分离过程的影响
操作条件的优化是膜应用过程研究的另一个重要方面。不同操作条件下(过膜压差、膜面流速和温度等)对膜分离性能的影响很显著。相同的膜装置在优化的操作参属下工作,能提高膜的拟稳定通量(在膜过滤过程中,当通量不再衰减时,此时膜过滤处于拟稳定态,该阶段对应的通量即为拟稳定通量),减少膜面积,降低能耗,节约工业生产成本,因此,确定一套合适的操作参数是决定膜过滤过程的一个主要方面。所有膜过滤过程都应该工作在较优操作条件下,操作条件的渗透通量临界值为研究者所关注。
4.4.1 操作压差对膜分离过程的影响
在微滤过程中,一般随着操作压力的升高,膜通量开始上升较快,当压力超过一定值后,膜通量随压力的变化趋于平缓,对有些体系膜通量甚至随压力的升高下降。这是由于操作压差升高虽然增加了过滤推动力,但同时也增加了污染的可能性。黄江丽等在利用陶瓷膜微滤技术浓缩草浆黑液的研究中发现,开始膜通量随压力变化较大,但当压力大于0.2MPa后,膜通量随压力的变化不大。
金珊等在陶瓷微滤膜滤除骨架镍催化剂微粒的研究中发现,在温度为58℃、膜面流速4.6m/s的条件下,测得压差在小于0.25MPa范围内,随着过滤压差的增大,膜通量随着增大。在大于0.25MPa的压差下,随着过滤压差增大,膜通量的变化趋于平缓。曾坚贤等在陶瓷膜处理肌苷发液的研究中发现,当压差低于0.1MPa时,膜的拟稳定通量随压差的增大而增大,并达到极大值。超过0.1MPa后,膜的拟稳定通量随压差的增大而逐步下降。钟璟等在陶瓷膜处理炼油厂“三泥”水相的研究中发现压力是膜过滤时的传质推动力,也是影响膜过滤的重要因素之一。压差≤0.135MPa时,膜的初始通量和拟稳定通量随压力升高而增加;压差>0.135MPa时,初始通量和拟稳定通量随压力升高变化很小。
Wang等人在作轧钢废水中试验发现,过膜压差增大到0.2MPa时,渗透通量逐渐增大;超过0.2MPa时,渗透通量有变小的趋势,过膜压差对于这种乳化油体系存在临界值。Zhao等人在用陶瓷膜处理钛白废水体系时也发现这种现象,操作压差在0.2MPa出现极大值,膜面流速在3.0m/s也有这种极大值。隋贤栋等在硅藻土梯度陶瓷微滤膜的饮用水净化中发现,在0.05MPa水压下,膜通量为1.31m³/(m²·h),随着水压的增加,通量逐渐增大,在0.3MPa水压下,膜通量达到6.59m³/(m²·h)。
4.4.2 操作温度对膜分离过程的影响
一般情况下,温度的升高,会使溶液粘度下降,悬浮颗粒的溶解度增加,传质扩散系数增大,可以促进膜表面溶质向主体运动,减薄了浓差极化层,从而提高过滤速度,增加膜通量。稀溶液过滤时,通量随温度的变化可由粘度与温度的关系来预测。赵宜江等在对陶瓷膜精制菜油的工艺研究中发现,当膜厚为0.2μm,错流速度5m/s,操作压力0.1MPa,粘土用量10%时,脱色率的变化与单纯吸附的变化规律基本一致,在90℃以下,温度升高,脱色率增加,这主要是温度升高,植物油粘度降低,更有利于有色物质向粘土表面的传质作用;当进一步升高温度后,脱色率反而下降,这是因为温度过高,已吸附的有色物质发生脱附现象又回到油中,同时高温下油中有些物质加酚类的氧化作用增强,也会使油的色泽有所加深。对于稀溶液的过滤,Cheryan等实验发现,当温度从303K升高到318K时,使渗透通量提高了一倍,Bhave等在油水分离中发现,当温度从293K上升至323K时,膜通量增加了两倍。当过滤过程属浓差极化控制,温度对膜通量的影响将取决于液相传质系数和粘度之间的关系是非线性的。
Deschampes在催化剂回收中发现温度升高,通量升高比预计的还要高,认为温度升高使大分子物质形成的动态膜减薄所致。温度对膜通量及肌苷的降解都有着较重要的影响,因此温度的优化即要能较大提高膜通量,又要尽量避免肌苷的降解。曾坚贤等在用陶瓷膜处理肌苷发酵液的研究中,分别在40,50,60,70,80,90℃下,测定温度对膜通量的影响,考虑运行成本及肌苷的收率等因素,适宜的操作温度为70℃。黄江丽等用陶瓷膜微滤技术浓缩草浆黑液时发现,在实验压差为0.2MPa的条件下,温度较低时,随着温度升高,膜通量加大;当温度接近50℃以后,膜通量变化缓慢;当温度大于58℃后,膜通量下降。金珊等在用陶瓷微滤膜滤除骨架镍催化剂微粒时发现,当料液浓度为1.5%、膜面流速为4.6m/s、操作压差为0.20MPa时,温度对膜通量的影响显著,通量与温度基本呈直线上升关系。徐南平等对陶瓷膜在钛硅分子筛固液分离过程中的应用研究中发现,钛硅分子筛水溶液所谓粘度明显受温度影响,23℃时物料粘度为1.9mPa·s,温度升高到80℃时粘度降为1mPa·s,因此温度升高将有利于提高膜的渗透通量。
4.4.3 膜面流速对膜分离过程的影响
在陶瓷膜过滤体的应用中,膜面流速是影响膜渗透通量的重要因素之一。理论上讲,提高膜面流速将有利于减轻浓差极化和减少膜表面的沉积的影响。一般的文献认为膜面速度越大,膜通量越高,但是膜面速度的提高意味着能耗的提高,膜的操作压力高等弊端,同时对有些体系,膜面流速的增加还会造成渗透通量的下降,对实验体系为颗粒体系,错流速度增大对膜通量的影响有两方面。一方面带走膜表面的颗粒使沉积层减薄而使膜通量增大,另一方面是首先带走了粗颗粒,使表面沉积层上细颗粒比例增高、比阻增大而使膜通量见效,因此研究膜面速度对过滤性能的影响很有必要。
钟璟等在陶瓷膜处理炼油厂“三泥”水相的研究中发现流速小于1.17m/s时,流速对通量的影响较为显著,当流速高于1.17m/s后,随流速的增大,通量增大的幅度降低,通过计算不同流速所对应的雷诺数Re证实了这一点。流速从0.58m/s变化到1.17m/s的过程中,流型是从过渡区发展到湍流区,因此流速对膜通量的影响明显;而流速大于1.17m/s后,流动进入湍流区,无流型的变化,所以流速对通量的影响减小。金珊等在用陶瓷微滤膜滤除骨架镍催化剂微粒时发现,在温度45℃,操作压力为0.15MPa条件下,膜面流速选在2.0m/s以下比较适宜。曾坚贤等在陶瓷膜处理肌苷发液的研究中发现当膜面流速超过3.25m/s时,膜的拟稳定通量已达到极大值,超过该流速,拟稳定通量保持不变,因此,选用3.25m/s的膜面流速,有利于提高膜通量和节省耗能。党亚固等在陶瓷膜过滤洗毛废水回收羊毛脂的研究中发现,在流速很低时,随着轮流速的增加,滤液通量也增加,在4m/s时达到极大值,以后随错流速度的增加,滤液通量反而减小。
5 展望
膜材料与高效分离技术是当代新型高效分离技术,是多学科交叉的产物,亦是化学工程学科发展的新增长点。与传统的分离技术比较,它具有高效、低能耗、过程简单、操作方便、不污染环境、便于放大、便于与其它技术集成等突出优点。它适合于现代工业对节能、低品位原材料再利用和消除环境污染的需要。在近几十多年来获得了极其迅速的发展,已广泛而有效地应用于石油化工、制药、生化、环境、能源、电子、冶金、轻工、食品、航天、海运、人民生活等领域,形成了独立新兴的技术产业。特别是在中药领域的应用,随着我国加入WTO,我国的制药工业正面临着全面的挑战,根据联合国 卫生组织的要求,符合现代化、国际化的中成药优良品种的标准是“安全、有效、稳定、均一、经济”,而其技术开发关键仍是获取与中医复方的作用机理相吻合的“药效物质基础”。因此现代陶瓷膜分离技术被国际上认为是21世纪较有发展前途的一项重大高新技术。
然而陶瓷膜分离技术毕竟是一门年轻的发展中的综合性学科,正处于发展和上升阶段,无论是理论上还是应用上都有许多工作要做,如:
(1)材料的脆性。
(2)缺乏完整材料的大规模生产系统。
(3)缺乏对材料的孔径大小、形状分布等的 控制方法。
(4)缺乏将孔结构与力学性能相联系的有效模型。
(5)膜通量提高。
(6)膜污染及其清除。
(7)对某些成分的吸附。
综合以上分析可知,陶瓷膜的制备方法有待于进一步的完善,它的分离机理还需要进一步的研究,尤其是膜材料的传质结构模型的研究,同时还要达到按应用过程进行材料设计与过程优化的目的。