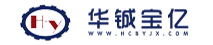
在膜科学技术领域中,开发较早的膜材料是有机聚合膜。近年来,无机膜材料的研究和开发已逐渐引起人们的普遍关注。其中,致密金属Pd膜不仅用于纯氢分离,而且也较多地用于催化加氢及脱氢反应研究之中。Gryaznov等经过系统研究指出,由金属Pd与VIB至VIIIB金属制成的合金膜,其性能更佳。同时指出,致密金属膜通量小、成型难及费用高而降低了其工业应用价值。为了克服这些缺点,相继研究开发了多孔金属膜及负载型金属膜等。
无机陶瓷则是另一类重要的无机膜材料。它具有两个其它膜材料无法比拟的显著特点,即
耐高温(≈1000K);抗腐蚀(化学、生物)。因此,它将在涉及高温及腐蚀过程(如食品加工、催化反应等)中有着更为广阔的应用前景、发挥更为重要作用。目前,无机陶瓷膜在食品加工过程中的应用已进入工业生产阶段;而在催化反应过程中的应用仍处在探索、开发阶段,主要是有许多基本问题还未得到很好的解决。例如,如何制备高通量、高选择性无机陶瓷膜、如何评价其性能以及如何应用等。本文将着重总结、介绍近年来无机陶瓷膜制备、评价及应用等方面研究工作的进展情况。
1 无机陶瓷膜的制备
无机陶瓷膜主要分致密陶瓷膜和多孔陶瓷膜。致密陶瓷膜具有较高渗透选择性、但其渗透通量很低而使其应用范围受到一定限制。例如,致密ZrO2膜对O2具有很高渗透选择性,但由于其渗透通量小而只能用于传感材料研究中。因此,对多孔陶瓷膜的研究和开发显得更加重要。本文将简要介绍多孔陶瓷膜的主要制备方法。
1.1 化学提取(蚀刻)法
将无机固体材料进行某种处理使之产生相分离,其中一相可由化学试剂(蚀刻剂)提取(蚀刻)除去,剩下一个内部相互连接相而制得多孔陶瓷膜。这是一个广义的描述,其中处理步骤可以是高温热处理、也可以是电化学阳极极化、甚至还可以是核辐射处理等。
(1)多孔玻璃膜。将硼硅酸盐玻璃管拉成50μm左右的丝,经热处理分相——硼酸盐相和富硅相,其中硼酸盐相可由强酸提取除去,从而制得富硅中空玻璃丝膜。多孔玻璃膜的微孔结构可由玻璃组成及处理条件控制。孔径为150-400nm;并可在含氟等离子体中蚀刻加以改善。
(2)阳极氧化铝膜。将高纯铝箔在室温下酸介质中进行阳极氧化处理,再用强酸提取除去未被氧化的金属铝,而制得具有均匀孔径分布及直孔氧化铝膜。其微孔结构与所用电解质性质密切相关。Diggle等指出,当电解质分别为硫酸、草酸及磷酸时,氧化铝膜孔径分别为100、200及300Å。
(3)云母陶瓷膜。当核辐射粒子穿过绝缘材料时,其留下的轨迹适当蚀刻后,可得所需微孔结构的直孔陶瓷膜。其孔径与蚀刻时间成正比;单位面积孔密度与辐射在单位表面上的粒子数有关;孔长与膜片厚度有关。该法适用于各种理论研究。其优点是:
①孔径可在6nm-6000nm范围内调节。
②单位面积(cm²)孔密度可在10-1030范围内调节。
③孔径分布、孔长度及孔取向均一等。
(4)负载型二氧化钛膜。硼硅酸盐玻璃经高温分相及酸处理除去可溶相后,再用TiCl4气处理,然后浸入水中使TiCl4转化为TiO2,高温烧结便可制得多孔玻璃负载的二氧化钛膜。其孔径在3nm左右;孔隙率低于35%。
1.2 固态粒子烧结法
将处理成很细的无机粉粒分散在溶剂中制成悬浮液(适当加入无机粘结剂等);然后成型制得未干燥粉粒堆积层;干燥及高温焙烧使粉粒间接触处烧结而相互连接在一起形成多孔无机陶瓷膜或膜载体。
由该法制备的陶瓷膜微孔结构与无机粉粒大小、悬浮液组成以及烧结温度等密切相关。其孔径范围为0.01-10μm,适用于微孔过滤。
Day等应用火焰水解法制备了粒度为4-50nm的超微Al2O3、SiO2、TiO2及ZrO2等无机陶瓷粉末,并且以此为原料通过固态粒子烧结法制得了平均孔径为14-19nm的多孔无机陶瓷膜。
用球磨法制得的Al2O3粉粒通过改变悬浮液组成及烧结温度等来控制多孔氧化铝膜微孔结构。结果,悬浮液组成对氧化铝膜孔径大小及分布有着至关重要的影响。随相对烧结温度升高,氧化铝膜平均孔径增大、孔隙率降低。由此可见,改变粉粒大小、悬浮液组成及烧结温度即可制得所需微孔结构的无机陶瓷膜。
1.3 溶胶-凝胶法
溶胶-凝胶过程作为一个成熟技术已广泛地应用于光学玻璃制备及分子筛合成之中。近年来才将这一过程用于多孔陶瓷膜制备中。其特点是,制膜时不需要化学提取、也不需要粉粒间烧结,更主要是由于溶胶粒子小(1-100nm)且均匀,且该法制备的多孔陶瓷膜具有相当小的孔径及非常窄的孔径分布。其孔径范围为10-1000Å,适用于超滤及气体分离。
原理:控制金属醇盐水解或水合氧化物胶溶制成胶体溶液;此胶体溶液经过不可逆溶胶-凝胶过渡生成凝胶;干燥、焙烧制得具有陶瓷特性的多孔无机膜。
由该法制备的陶瓷膜微孔结构与溶胶制备条件、溶胶-凝胶过渡方式以及凝胶干燥温度等因素密切相关。
溶胶制备主要通过PMU过程,制备聚合溶胶或通过DCS过程来制备粒子溶胶。通常PMU过程较难控制,应用就少。多数研究者是通过DCS过程来制备溶胶,其控制因素是酸类型及酸浓度。Ulrich考察了不同类型的酸对SiO2凝胶孔分布的影响。结果表明,随着酸强度的增加,孔径分布范围增大,但平均孔径变小。Anderson等研究了酸浓度对TiO2溶胶粒子大小的影响后指出,只有当酸的浓度值合适时才能制得稳定的溶胶。Leenaars等考察了HClO4浓度对负载型氧化铝膜孔径及孔隙率的影响。结果表明,随着HClO4浓度的增加,氧化铝膜的孔径及孔隙率均减小。
从Leenaars和Teichner等人工作中可以看到,溶胶-凝胶过渡方式对多孔陶瓷膜微孔结构也有重要影响。Leenaars等将铝溶胶经过自然干燥而制得干燥凝胶(Xerogels),经高温焙烧制得具有单一孔径分布的超细孔(2.7nm,50%)氧化铝膜。Teichner等则在临界温度下将铝溶胶转化为气凝胶(Aero-gels),由此制得的多孔氧化铝膜,除超细孔外还存在粒子间大孔。
Larbot等对凝胶焙烧温度与氧化铝膜孔径间关系的研究结果表明,膜孔径随焙烧温度升高而增大。Leenaars等也得到了类似结果。同时指出,延长焙烧时间同样可使膜孔径增大。
总之,溶胶-凝胶法已较多地用于多孔陶瓷膜(如Al2O3、SiO2、ZrO2等)的制备过程中,并且通过适当改变制备条件就可获得所需微孔结构的多孔陶瓷膜。
2 无机陶瓷膜的评价
无机陶瓷膜的评价主要包括两方面内容,一是膜的微孔结构;二是膜的分离特性。
2.1 无机陶瓷膜的微孔结构
多孔膜的微孔结构(如孔隙率、孔径大小及分布等)直接影响膜的渗透通量及渗透选择性等。因此,弄清多孔膜的微孔结构对正确理解和解释多孔膜的分离特性具有重要意义。
测定孔隙率、孔径大小及分布的方法很多。不同范围的孔径(大孔0.2-10μm;过渡孔10-200nm;微孔10-100Å)有不同的测定方法。大孔范围孔结构一般采用压汞法、光学显微镜法等;过渡孔采用压汞法、电子显微镜法、气体吸附法;而微孔则一般采用分子试探法。
(1)光学(电子)显微镜法。从原理上讲,光学显微镜和电子显微镜是相似的。它们均由聚光镜、物镜及目镜组合而成。差别在于两者所用“光源”不同。一个是可见光;一个是电子束。该法的局限性:只适用于测定表面直孔,不适用于测定受到遮蔽的孔,如内部交叉孔等。
(2)气体吸附法。根据气体分子在一定压力下毛细管凝聚原理,从Kelvin方程出发,利用吸附(或脱附)等温线数据来计算孔隙率、孔半径及其分布。通常是采用78KN2吸附。由于Kelvin方程限制,该法只适用于过渡孔(10-200nm)测定。
(3)压汞法。在不润湿情况下(接触角大于90°),表面张力会阻止汞液体进入小孔,利用外加压力,可使汞充满某一给定孔径的孔道中,根据不同压力下压入的汞量即可求出孔径大小及分布等。所依据的基础是Washburn关系式。该法的不足是:
①操作压力高(0-70MPa)。
②测大孔时,分辨率低。
③测小孔时,压力过高易使样品结构破坏。
④汞具有毒性。
(4)液体驱逐法。这是一种新方法,它依据的基本原理是毛细管虹吸作用。当将毛细管放入液体中时,由于液体表面张力作用,液体将在毛细管中上升直到与重力平衡为止。
该法通过监测压力和流速的关系即可求得膜的孔径大小及分布等。其优点是:
①低压操作(0-0.1MPa)。
②非破坏性。
③无毒。
但它不适用于微孔及过渡孔等测定。孔径测定范围为0.05-300μm。
2.2 无机陶瓷膜的分离特性
无机陶瓷膜是否具有工业应用价值将依据其分离特性而定。因此,对无机陶瓷膜分离特性的评价对评估其工业应用价值具有重要意义。
(1)液体分离。
a.渗透通量:决定着无机陶瓷膜在分离过程中对原料的处理能力。其影响因素有:
①膜的微孔结构。
②原料组成。
③操作条件等。
b.载留率:决定着无机陶瓷膜对某一组分的分离能力。其影响因素同样是,膜微孔结构、原料组成及操作条件。
c.渗透稳定性:决定着无机陶瓷膜在液体分离中的应用价值。
一般而言,在液体过滤过程中,渗透通量随着分离过程进行而很快下降。因此,渗透稳定性是液体分离过程中必须考察的参数之一。
(2)气体分离。无机陶瓷膜在气体分离中的应用还未实现工业化。描述膜分离特性的参数主要有渗透通量和渗透选择性。此时,渗透稳定性显得并不重要。
3 无机陶瓷膜的应用
3.1 在分离过程中的应用
无机陶瓷膜已在食品加工等液体过滤过程中得到工业应用;并且在气体分离过程中应用的研究也取得了一些进展。
3.2 在催化过程中的应用
(1)膜反应器结构。它主要由两部分组成,一是反应区;二是渗透区。其特点是将催化反应和产物分离 在同一体系中,从而可以在催化反应进行的同时将产物(至少其中之一)从反应区分离出来。其意义不仅是简化了产物分离过程;而且,更重要的是可以使催化反应进行超平衡态转化或提高催化反应选择性。
(2)在催化中应用。根据膜在膜催化过程中所起作用的差异,以下将分下面4个方面来介绍无机陶瓷膜在催化反应过程中的应用途径。
a.膜只作分离器:这是陶瓷膜在膜催化过程中所具有的基本功能,即它至少应对产物之一起分离作用。
b.膜既作分离器又作载体:陶瓷膜一般为耐高温金属氧化物,它用作分离器的同时,又可用作催化剂活性组分(特别是贵金属)的载体。
c.膜既作分离器又作催化剂:适当选择金属氧化物材料,可以使膜在用作分离器的同时,还可以用作催化反应的催化剂。
d.膜既作分离器又作隔离器:膜在膜反应器中的作用一方面可以使产物之一进行分离;另一方面又将膜反应器隔离成既相互独立又相互联系的两个区。适当利用这两个区,则可以获得常规催化反应难以得到的反应结果。其中较有代表性的例子就是膜反应器中的偶合反应。所谓偶合反应是指在膜反应器中两个区同时进行两个反应,其中一个区的反应产物之一经膜分离后进入另一区而进行另一个反应;这样,在膜反应器两个区进行的两个反应就能相互促进而偶合。
4 结束语
(1)对无机陶瓷膜制备而言,各种方法联用技术将是高通量、高选择性陶瓷膜制备的一个发展趋势。
(2)对无机陶瓷膜性能评价而言,除对其分离特性进行评价外,还应对其微孔结构进行表征。并且,膜微孔结构的表征也常需要联用技术。
(3)对无机陶瓷膜应用而言,陶瓷膜除了已在高温分离中得到广泛应用外,它在许多催化过程中的应用也将受到充分重视。例如,脱氢反应、选择氧化反应以及其它脱除小分子反应等。