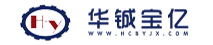
1 前言
膜分离技术由于具有低能耗、高分离效率等特点,已愈来愈引起人们的关注。尤其是陶瓷分离膜由于具有耐高温、高压、抗酸碱和有机溶剂侵蚀,便于清洗、再生等优点,已作为膜分离技术的一个重要分支,近年来得到迅速发展和应用。随着陶瓷分离膜制备技术的不断发展和完善,膜装置不断优化,陶瓷分离膜的应用领域也不断扩大。目前, 陶瓷分离膜市场正以30%以上的年增长速度增长。陶瓷分离膜所具有的大比表面结构特点及膜材料本身具有的化学特性,使人们对分离膜的应用已不再 于分离,而更进一步推广到诸如催化、传感、离子交换等领域,陶瓷分离膜技术将成为21世纪关键技术。
2 陶瓷分离膜技术及制备工艺进展
陶瓷分离膜按孔径大小分为微滤膜(孔径0.1~5μm),超滤膜(0.01~0.1μm)和反渗透膜(0.01~0.001μm)。 上对陶瓷微滤膜研究始于50年代,80年代后期溶胶凝胶技术制备陶瓷分离膜的成功进一步扩大了制膜体系,使目前的陶瓷分离膜不 于微滤,而更趋向于超滤和反渗透。由于超声波震动挤出成型工艺、凝胶浇注及离心注浆工艺的研究及进展,更进一步提高了孔梯度陶瓷载体膜的机械及结构稳定性。另外,采用传统陶瓷制备工艺的固态粒子烧结法及应用溅射、离子镀、金属镀或化学气相沉积等工艺薄膜沉积法也得到发展。目前,在国内已采用粒子烧结法制备大面积的α-Al2O3和Al2O3/ZrO2微滤膜,尚在研究中的CVD/EVD法可广泛用来制备微孔膜和各种复合膜,解决了不同膜材料复合问题,改变了膜的特性。总之,膜制备工艺和技术的不断发展,很大程度上提高了陶瓷分离膜的结构稳定性、微孔和化学特性,同时膜的材质由单一的γ-Al2O3、α-Al2O3膜逐步发展形成了诸如:TiO2、ZrO2、TiO2/Al2O3、ZrO2/Al2O3、镁铝尖晶石膜以及具有催化活性作用的Ag/γ-Al2O3、V2O5/TiO2膜等。陶瓷分离膜应用领域起初由液体分离方面逐步发展到气体分离、高温气体净化、膜反应器和发酵器等。采用各种联用、嫁接技术进行陶瓷分离膜制备,以满足形态复杂、高通量、高选择性陶瓷分离膜,将是膜制备工艺技术发展的主要方向。
3 陶瓷分离膜的市场应用
尽管陶瓷分离膜的研究、开发起步较晚,但以其本身具有的诸多优良特性,使其近10年来的开发、应用取得较大的发展,尤其是在微滤(MF)、超滤(UF)和气体分离(GS)方面显示出巨大的应用市场。据统计, 陶瓷分离膜市场近十年来年增长达到30%以上,其中仅膜组件市场目前已达4亿美元,约占整个 陶瓷膜市场10%左右,其中尤以陶瓷气体分离膜增长速度较快,近年超过100%,陶瓷分离膜在未来各个领域都孕育着巨大的应用市场。
3.1 陶瓷分离膜在微滤领域中的应用
无机陶瓷分离膜已在食品加工等过程中得到工业应用,在化学工业中,无机膜优良的化学稳定性及机械稳定性在许多化工过程中也有用武之地。
陶瓷微滤膜在溶剂和化学物质的净化、油脂过滤、流体、烟雾净化、催化反应和各种环境净化、核反应中的“热反应废水”净化、选矿及水净化、废水处理等领域具有广阔应用前景。目前, 陶瓷微滤膜市场销售额已达10多亿美元,年增长率达到25%,约占 整个微滤膜市场的10%。比如,采用0.5~10μm TiO2微滤膜,由于该陶瓷分离膜具有无毒、耐酸碱等特性,故特别适用于食品、水源净化、化工、医药等方面的分离,采用0.2~0.5μm的陶瓷分离膜进行油田行业的油水分离,其滤水速率可达2~3m³/h,过滤后杂质含量<0.5mg/L,含油量<1mg/L,去除效率达99.99%。另外,在许多溶液的催化反应中都可以采用1~10μm的微滤膜作为膜催化剂或载体。
3.2 陶瓷分离膜在超滤领域中的应用
陶瓷超滤膜应用市场主要在于:食物、制酪业及果汁的分离、废蒸汽处理等,其中食物和果汁的分离将是增长较快的市场,其另一潜在的应用市场将是工业上的反应器。陶瓷分离膜在工业领域应用包括:液体碳氢化合物的分离、废蒸汽净化、油水乳化液的分离及润滑油再生等,这些都需要大量的陶瓷分离膜产品。再者,陶瓷超滤膜在食品、生物、化工、制药领域的应用日益增长,诸如霉菌的分离、酵母菌的过滤、细菌的净化、病毒去除等,还有食物工业中从果酒中分离出酸类及果汁澄清、牛奶分离等。比如将350~500Å的超滤膜用于低度酒过滤,可以有效去除一些脂类、蛋白质等物,在不改变酒色味的前提下,可大大提高酒类澄清度,延长存放期。据资料报道,目前 陶瓷超滤膜市场已达8000万美元。
3.3 陶瓷分离膜在气体分离领域中的应用
尽管无机陶瓷分离膜实际上的工业应用全在液体分离方面,但目前在气体领域中的应用研究已取得较大的进展。陶瓷分离膜在气体领域的应用一方面使许多工业过程气体分离成为可能,另一方面对膜反应器这一概念在膜分离技术普及化后渐为人们所熟悉,尤其用于生物工程反应器、发酵器取得较大的进展。用于气体分离领域的陶瓷分离膜主要有分离膜和催化反应膜,虽然常温下采用陶瓷分离膜进行O2/N2、H2/N2等气体分离没有太大的优点,但在有些介质分离,诸如:CO2/CH4、CO/CO2、H2O/空气、酸性气体去除(H2O、HCl、SO2)或氢碳化合物/空气等,由于陶瓷分离膜具有的良好耐介质腐蚀稳定性,因此要优于其它膜。另外,在高温领域,像300℃左右碳氢化合物/蒸汽分离、水/乙醇分离、高温下合成氨工业中空气和氮气分离等,通过微孔陶瓷分离膜都可以进行有效的选择、吸收或转化。其它陶瓷分离膜在油田天然气气体的分离方面,在煤气及煤气净化方面具有较大的市场。目前在气体分离领域,陶瓷分离膜市场约占整个分离膜市场的15%左右,达到8000万美元,预计未来5年将以100%速率增长。
由于陶瓷分离膜在催化反应过程中既可以做分离器的催化剂载体,又可以作为催化剂,因此各种催化活性陶瓷分离膜在气体反应、分离领域具有较大的应用市场。比如3nm γ-Al2O3或载银γ-Al2O3分离膜已成功地应用于甲醇的氧化脱氢。3~4nm TiO2或V2O3陶瓷分离膜用于合成氨中脱NOx反应可有效的控制NOx和NH3反应速率,提高NOx转化率,使其在350NOx的转化率可达到40%以上,N2转化率大于75%。另外采用陶瓷分离膜反应器进行环己烷脱氢反应,可在反应器一边进行脱氢生成环己酮,而同时在另一边进行苯酚加氢生成环己烷反应,这样在683℃苯酚的转化率可达到39%,得到环己烷的选择率达到95%以上。类似这些类型的膜催化反应,从催化工艺和催化技术开发上着眼是十分值得重视的。
4 陶瓷分离膜优缺点及目前存在问题
4.1 陶瓷分离膜的优缺点
陶瓷分离膜尤其是孔梯度载体陶瓷分离膜,除具有一般分离膜的特性外,同时兼具了陶瓷耐高温、高压、抗介质腐蚀等优点,具有更大的优越性。
(1)耐高温,高达1000℃,因此适用于高温气体分离、净化以及需要高温灭菌、消毒的饮食业。
(2)耐高压,工作压力高达6MPa,因此适用于高压体系。
(3)耐腐蚀,适用于酸、碱介质和有机溶剂,对于堆积在膜表面的物质可采用酸洗处理,这在涉及到耐高温和腐蚀过程的工艺(如食品加工、催化反应等)中有非常广泛的应用前景。
(4)陶瓷分离膜大多数为亲水性膜,具有梯度变化微孔结构,孔隙率高,0.02μm陶瓷分离膜的透水量高于许多0.1μm有机膜。
(5)陶瓷分离膜清洁状态好,无毒、无味,具有良好的抗微生物侵蚀能力和良好的生物及化学相溶性,便于清洗、再生,因此在生化制药和化工、食品业中有着良好的应用前景。
当然,陶瓷分离膜也有一些缺点,陶瓷分离膜一般脆性较大,不易加工,且密封困难。另外,陶瓷分离膜成本较高,约为有机膜的20~30倍,这些缺点也在很大程度上限制了陶瓷分离膜的推广和应用。
4.2 目前存在的问题
尽管 上对陶瓷分离膜技术研究和推广应用已取得了突破性进展,但目前尤其我国在该项技术上仍存在一些科学技术问题。主要表现在:
(1)对陶瓷分离膜材料总体结构及制备技术系统研究不够,不能完全通过控制条件来达到期望的性能。
(2)对陶瓷分离膜分离技术的机理研究大多停留在静态,对表面扩散、毛细管冷凝的气体动力学研究较少。
(3)高温、高压下气体通过陶瓷分离膜行为研究较少,耐高温是陶瓷分离膜的主要特征,需要对陶瓷分离膜在高温下的分离过程进行深入研究。
(4)对膜载体研究较少,目前 各国研究的陶瓷分离膜大多数为双层或三层膜,载体孔径小,相对阻力大,另外膜制品尺寸小,制备大面积、稳定性能良好的膜较困难。
(5)陶瓷分离膜工程技术化研究较少。对膜装备优化组装、膜选择、膜抗污染能力、再生性能、使用寿命、投资及运行费用等研究较少。
(6)目前研究开发应用陶瓷分离膜大多是单一组份膜。由于物理分离过程很难同时实现高通量与高选择性,因此对陶瓷分离膜需要进行化学改性,以改进分离组份与膜内孔表面作用方式,改进分离膜的性能,并进一步开发膜材料具有催化活性的催化功能膜及各种膜敏感材料等。
总之,陶瓷分离膜作为分离膜领域的一个重要分支,作为21世纪关键技术,目前仍存在许多难题需要科研工作者去研究、解决,该项技术没有完结,具有很大的发展空间。
5 陶瓷分离膜的发展趋势
(1)载体及膜的制备技术。目前开发应用的陶瓷分离膜绝大部分是单一组份2载体膜,如何提高载体膜的高效选择性和透过性、制造大比表面积无缺陷膜、降低成本是目前亟待研究解决的难题。因此,采用联体、嫁接技术,集中精力开发各种复合膜,如各种反应膜、催化功能膜、电传导膜及膜敏感材料等是陶瓷分离膜制备技术发展的一个方向。
(2)陶瓷分离膜应用技术。陶瓷分离膜应用不仅只限于液体分离、气体净化,而且可以用于选择催化、冷凝气体分离、生物反应及反渗透等。其他一些应用,比如光电催化、电解隔膜、传感等都有较大的发展前景。