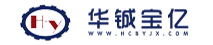
含油废水来源广泛,普遍存在于石油开采、石油化工、机械加工、食品、医药等行业,其COD高,成分较复杂。根据含油废水来源和性质的不同,油类在水中主要是以漂浮油、分散油、乳化油、溶解油4种状态存在。直接排放含油废水不仅浪费资源也会对生态环境造成严重的污染,主要表现在:污染饮用水和地下水资源,影响农作物的生长,造成水生生物死亡,通过生物界食物链的富集作用,会危及到人类的健康和生命。从长远角度来讲,对全人类的可持续发展会造成严重的影响。因此,含油废水治理是当今环境工程领域亟需解决的重要问题。与传统的处理方法相比较,陶瓷膜具有较强的耐酸碱能力、耐高温、孔径分布均匀、分离效率高、能耗低、机械强度大、使用寿命长等突出优点,其在污水处理方面,尤其在含油废水处理方面产生了巨大的经济效益和社会效益。
在陶瓷膜过滤设备处理含油废水的过程中,膜的污染是不可避免的,而且已经成为陶瓷膜分离技术发展和应用的瓶颈之一。陶瓷膜设备运行一定时间后,膜污染造成膜通量下降,不能满足相关生产要求,必需进行合理清洗,恢复膜通量,延长陶瓷膜使用寿命。因此,陶瓷膜清洗方法的研究是膜分离技术应用的关键。本文探讨了陶瓷膜的化学清洗方法,确定了合理的适用于工业化应用的清洗方案。
1 试验部分
1.1 试验药品
十二烷基苯磺酸钠(C18H29O3SNa,AR),氢氧化钠(NaOH,AR);乙二胺四乙酸二钠(Na2-EDTA,AR);实验室自制含油废水。
1.2 试验仪器
试验所采用的陶瓷膜参数为:支撑体及膜材质均为α-Al2O3,膜管长为425mm,19孔道,通道内径4mm,膜管外径为30mm,膜孔径0.1μm,有效面积为0.1㎡。过滤清洗装置为错流式过滤。
1.3 试验方法
将清水加入设备用来清洗装置、润湿陶瓷膜,并记录新陶瓷膜清水通量,然后再进行含油废水的分离过滤处理。待膜通量达到稳定后,进行陶瓷膜化学清洗方法的研究。首先,把含油废水排出并保存,向设备中加入清水循环几次;然后把设备中的清水换成清洗剂循环清洗一定时间,清洗后再用纯水冲洗使之达到中性;向清洗后的设备中加入清水,记录清洗后的清水通量,并计算相应的膜通量恢复率。此时,一个化学清洗周期结束,然后再将含油废水加入设备中进行过滤(即再次污染)一定时间至通量稳定,再用不同种类或不同浓度的化学清洗剂进行清洗,循环操作直至试验结束。
2 结果与讨论
2.1 膜通量随时间的变化
在陶瓷膜处理含油废水的过程中,由于膜污染的存在,膜通量一般随时间的增加而下降。膜通量随时间的变化呈下降趋势,在前25min通量下降较快,25min后通量下降缓慢,在75min后通量几乎无变化,通量稳定在64L/(㎡·h)。在初始阶段,废水中的油粒在陶瓷膜表面和部分孔隙中被大量截留,形成较厚的凝胶层,致使膜通量急剧下降。随着时间的延长,废水中的油滴不断沉积在膜面上,同时又不断被错流循环的液体冲走,当这2个对立的过程达到动态平衡时,滤饼层的厚度基本保持不变,过滤阻力几乎恒定,使膜通量达到一稳定值,即稳定通量。
2.2 单步化学清洗
化学清洗从本质上是污染物与清洗剂发生复杂的化学反应,生成小分子或者溶于水的产物,使污染物从膜表面脱落,膜过滤通量得以恢复。化学清洗剂的选择需结合实际情况进行,本文初步选择了具有代表性的表面活性剂、碱、酸和螯合剂作为清洗试剂。选择C18H29O3SNa、NaOH、HNO3和Na2-EDTA作为代表性的清洗试剂,分别考察各清洗试剂的清洗情况,考察不同浓度下清洗过程随时间的变化。
从考察结果可知,C18H29O3SNa清洗过程表面活性剂包括亲水基和亲油基,可以将油粒细化,脱离膜表面,从而通量得到一定恢复,整体的趋势是通量随时间的延长而下降。NaOH清洗过程,碱可以与油粒发生皂化反应,剥离膜表面,整体的趋势是通量随时间的延长不断增加,30min后增加缓慢。HNO3清洗过程,酸能和油脂类发生水解反应,生成溶于水的羧酸类和醇类,可以透过膜结构,膜通量随时间变化较小,30min后通量趋于一致。Na2-EDTA清洗过程,膜通量随时间先增加,30min后通量变化不明显。
试验表明,不同清洗剂清洗效果不同,同一清洗试剂在不同的浓度下清洗效果不同,清洗时间对清洗效果也有影响,所以,需要选择合理的清洗试剂浓度和对应的清洗时间。判断化学试剂的清洗效果一般用膜通量的恢复率来表示,下表列举了各单步清洗较佳操作条件,为进一步深入研究提供理论基础。
清洗试剂 | 质量分数(%) | 清洗时间(min) | 通量恢复率(%) |
C18H29O3SNa | 1.0 | 5 | 40.9 |
NaOH | 1.5 | 20 | 40.0 |
HNO3 | 2.0 | 10 | 44.0 |
Na2-EDTA | 1.0 | 10 | 34.7 |
2.3 复合清洗
陶瓷膜单步化学清洗膜通量恢复率不足50%,远不能达到实际生产的要求,因此,需探索各种清洗试剂联合使用,进行复合清洗,提高膜通量的恢复率。复合清洗的原则是将单步清洗的较佳方案作为复合清洗每一步的选择基础。
2.3.1 两步化学清洗膜通量的恢复率
根据单步清洗的较佳条件,组合成6种不同的复合清洗方案,试验结果见下表:
方案序号 | 清洗组合 | 通量恢复率(%) |
1 | 1.0% C18H29O3SNa→1.5% NaOH | 75.1 |
2 | 1.0% C18H29O3SNa→2.0% HNO3 | 68.2 |
3 | 1.5% NaOH→1.0% C18H29O3SNa | 55.6 |
4 | 1.5%NaOH→2.0% HNO3 | 64.4 |
5 | 2.0% HNO3→1.0% C18H29O3SNa | 71.8 |
6 | 2.0% HNO3→1.5%NaOH | 57.8 |
由上表可知,方案1、2和5的清洗效果较好,膜通量恢复率有了进一步的提高。结果表明,第1步采用C18H29O3SNa进行清洗较为合理,主要是由于C18H29O3SNa是表面活性剂,可以将膜表面和膜孔内较大的油粒细化,变成较小的油粒,容易被水冲刷带走,从而达到初步清洗的目的。在第1步清洗的基础上,再用NaOH(可与油粒发生皂化反应)或HNO3(能与脂类发生水解反应生成易溶于水的醇类和有机酸类)进行第2步清洗,使膜通量恢复率有了较大的增加。另外,采用方案5清洗时,膜通量恢复率也有了较大的增加,主要是因为HNO3先与脂类发生反应,生成易溶于水的醇类和有机酸类,之后再配以 C18H29O3SNa清洗,达到了进一步清洗的目的。
2.3.2 多步化学清洗膜通量的恢复率
经过两步复合清洗,通量有了较大提高,恢复率高达75.1%,基本满足生产要求,为了寻找更佳的清洗效果,在两步清洗的基础上,再增加1种清洗试剂,初步确定三步清洗组合方案,考察其清洗效果,试验结果如下表所示:
方案序号 | 清洗组合 | 通量恢复率(%) |
1 | 1.0% C18H29O3SNa→1.5% NaOH→2.0% HNO3 | 96.2 |
2 | 1.0% C18H29O3SNa→2.0% HNO3→1.5% NaOH | 88.6 |
3 | 2.0% HNO3→1.0% C18H29O3SNa→1.5% NaOH | 91.8 |
由上表可知,三步清洗组合中方案1的清洗效果较好,膜通量恢复率为96.2%,完全达到再次过滤的膜通量要求。该方案第3步骤用的HNO3可以更好地清洗掉第2步骤NaOH清洗时皂化反应的产物,另外还能中和少量残留的NaOH。第2种和第3种清洗方案的膜通量恢复率也达到再次过滤的要求。较佳清洗方案组合确定为:先用质量分数1.0% C18H29O3SNa清洗5min,再用质量分数1.5% NaOH清洗15min,然后用质量分数2.0% HNO3清洗10min(注:每一步化学清洗后需用清水清洗3~4遍,然后再进行下一步化学清洗)。
2.4 清洗效果的重复性考察
为了考察化学清洗的稳定性,对三步清洗中的较佳方案进行了3次相对独立的重复性清洗试验,结果分别为96.2%、95.3%和94.6%,其清洗结果比较接近,这表明较佳清洗组合有较好的重复性,完全满足实际工业化生产的需要,适合工业化推广。
3 结论
采用陶瓷膜过滤法处理含油废水,受到污染的陶瓷膜通量下降,需要对其进行化学清洗。在单步清洗的基础上,考察复合清洗对膜通量的恢复率影响,其中,较佳的清洗组合为:先用质量分数1.0% C18H29O3SNa清洗5min,再用质量分数1.5% NaOH清洗15min,然后用质量分数2.0% HNO3清洗10min,膜通量的恢复率可以达到96.2%,工艺较简单,适用于实际工业化应用。