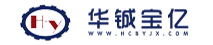
污泥经过干燥后,不仅可显著减少体积,而且能够明显地减少臭味、病原菌、黏度等负面特性,干燥后的污泥更是具有多方面的用途。因此,干燥是污泥实现减量化、无害化和资源化处理的关键一步。由于污泥干燥是能量净支出的过程,能耗的费用占整体干燥运行成本的80%左右,减少污泥干燥能耗可以有效降低干燥运行成本。选择合适的热源和干燥工艺是减少能耗的两种主要途径,选用热电厂或垃圾发电厂排放的烟气余热作为热源,可以在不增加新能源的情况下干燥污泥,从而大大减小污泥干燥的运行成本;另外通过一定的工艺减小污泥颗粒可以提高污泥干燥的效率。
经过机械脱水的污水处理厂污泥含水质量分数仍然高达70%以上,而且富含有机质和具有高黏性,这些特性区别于普通的化工物料。除利用返混降低污泥含水质量分数和黏性的工艺外,一般污泥在干燥时都呈直径达数厘米以上的团粒状,直至含水质量分数降到一定程度后才会被进一步分散,这样直接影响了污泥干燥的效率。Coackley等对污泥中的水分和污泥的干燥特性进行了实验研究,初步了解了污泥含水质量分数与干燥之间的相互联系,并研究了污泥干燥过程中表观形态的变化与水分析出的特性。然而,对于在低温条件下污泥干燥热量平衡与污水污泥颗粒大小之间的关系还不清楚,而这正是直接影响污泥干燥效率的因素。本文模拟在烟气余热温度下,通过恒温干燥实验,研究了不同污泥颗粒在干燥过程中,含水质量分数与干燥速率和干燥时间的变化趋势,分析了温度和颗粒大小对污泥干燥过程的影响,为低温污泥干燥提供了理论依据和技术参数。
1 材料与方法
本次研究的污泥样品来自浙江省桐乡市污水处理厂经过机械脱水后的新鲜污泥(污泥的相关理化性质见下表:
pH | w(H2O)/% | w(OC)/% | w(OM)/% | D/mm | w(S)/% | w(P)/% | q/kg/m³ |
7.26 | 70.06 | 35.76 | 60.26 | 0.0185 | 1.63 | 2.01 | 1.05×103 |
表中w(H2O)、w(OC)、w(OM)、w(S)、w(P)分别为污泥中水分、有机炭、有机质、硫和磷的质量分数,D为平均粒径,q为湿污泥的密度。
重金属的质量分数见下表:
w(As)/% | w(Cd)/% | w(Cr)/% | w(Cu)/% | w(Ni)/% | w(Pb)/% | w(Zn)/% |
0.0053 | 0.0043 | 0.0353 | 0.2567 | 0.0302 | 0.0425 | 0.1926 |
分别称取1.0±0.05、2.5±0.05、5.0±0.1、10.0±0.1g的湿污泥,将其制成球状,分别置于100、120、140、160、180、200℃(湿球温度分别为48、52、56、60、64、68℃)的温度下(风速均为0),进行恒温干燥实验,每隔6min称量其质量,直到恒重为止。一般工业锅炉的排烟温度为120~150℃,热电厂锅炉或垃圾发电厂锅炉的实际排烟温度略高,但是由于烟温每升高10~20℃,锅炉热效率会降低1%左右,实际的烟气温度一般在100~200℃。
由于在确定不同污泥颗粒的干燥速率时,需要污泥的表面积参数,而实验中污泥的表面积是无法实时测量的,并且在100~200℃时污泥有少量的有机物分解,因此在计算表面积时,假设原始污泥颗粒内部水分均匀分布,污泥内部各点的物性,如热导率、密度和比热容等都相等,且污泥在干燥过程中进行等比收缩,形状保持球形不变,无裂纹产生,这样可以通过污泥体积推算其表面积。污泥的体积近似等于水的体积和干污泥的体积之和,其计算公式如下:
V=Vw+Vd=mw/qw+md/qd
式中:V、Vw、Vd分别为污泥、污泥中水分、污泥中干泥的体积;m、mw、md分别为污泥质量、污泥中水分质量、污泥中干泥质量;qw、qd分别为水和干泥的密度,根据实验数据,干泥密度为1.20×103kg/m³。
实验结果如下表所示:
θ/℃ | 100 | 120 | 140 | 160 | 180 | 200 |
WLoss/% | 70.06 | 70.18 | 70.41 | 70.62 | 70.85 | 71.13 |
表中θ为干燥温度,WLoss为失重率。从上表可以看出,在100℃时,污泥的失重率等于其含水质量分数,而在120~200℃时,失重率仅略大于含水质量分数,200℃时的失重率为71.13%,也与含水质量分数仅差1.52%,为便于比较,假设100~200℃时含水质量分数等于失重率,即约为70%。
2 实验结果
下表给出了表征试验污泥颗粒性状的有关参数。
m/g | V/cm³ | S/c㎡ | r/cm |
1.0195 | 0.96 | 4.70 | 0.61 |
2.4753 | 2.35 | 8.54 | 0.82 |
5.0632 | 4.81 | 13.78 | 1.05 |
10.0826 | 9.60 | 21.85 | 1.32 |
表中,S为污泥颗粒表面积,r为半径。表中的质量和污泥体积为140℃污泥干燥时3组实测数据的平均值,表面积和污泥半径是假设污泥为球形时的计算值。
在给定温度下,不同大小的污泥颗粒含水质量随干燥时间出现变化。在100~200℃时,污泥含水质量分数从70%降到40%(半干化)或0(全干化)的所需时间随着温度的升高或污泥颗粒的减小而减小,例如10g污泥颗粒的全干化时间在100℃时为450min,到200℃时降到108min,而同样在100℃下1g污泥的全干化时间为120min。
在不同温度下,不同颗粒的污泥干燥速率随含水质量分数出现变化。污泥的干燥速率随着温度的升高或污泥颗粒的减小而变大,且所有的干燥曲线和干燥速率曲线趋势是相同的,分别经历不稳定加热阶段、恒速干燥阶段、 降速干燥阶段和第二降速干燥阶段4个阶段。由于不稳定加热阶段的时间非常短,在讨论时将其一并计入恒速干燥阶段,并将恒速干燥阶段结束时的含水质量分数称为临界含水质量分数, 降速干燥阶段结束时的含水质量分数称为第二临界含水质量分数。
3 讨论
3.1 污泥干燥过程的变化ZZ
从实验结果中可以看出,污泥干燥过程中恒速干燥阶段占总干燥时间的33%~50%,但是这个阶段失去的水分却占污泥总水分的50%~80%,因此恒速干燥阶段是污泥干燥的主要阶段。总体来说,当干燥温度升高或污泥颗粒变大时污泥的临界含水质量分数变大,恒速干燥阶段失去的水分比例减小。但在100和120℃时,临界含水质量分数保持在35%左右,不受温度和颗粒大小的影响。从140℃开始,当污泥颗粒大小相同时,污泥临界含水质量分数随干燥温度的升高而变大。例如10g污泥在140℃时的临界含水质量分数为44%,在200℃时增加到53%;当干燥温度相同时,污泥临界含水质量分数随颗粒的变大而变大,例如在180℃下1.0、2.5、5.0、10.0g污泥颗粒的临界含水质量分数分别为43%、44%、46%、48%。
降速干燥阶段占总干燥时间的0.50~0.67,然而这个阶段失去的水分仅占总水分的0.20~0.50,并且第二降速干燥阶段所占的比例随着温度升高或颗粒变大而逐渐增大,第二临界含水质量分数在100~120℃时仅为5%左右,而到180~200℃时,已增加到20%~30%。
根据Fick扩散定律,水分在物料中的分布呈抛物线型,实际污泥干燥时由于表面干燥速率不同,污泥内部水分分布情况也是不同的,主要有两种类型,即均衡分布型与不均衡分布型。当干燥强度较弱时,表面水分蒸发速率小于污泥内部向表面传递速率,因此在包括预热的恒速干燥阶段,污泥表面和内部的水分饱和度整体均衡下降,污泥内部水分属于均衡分布型。直至当表面水分达到临界饱和度时,内部水分也接近临界饱和度,如再干燥则无法保持表面的整体湿润,污泥颗粒表面将出现干区,此时的含水质量分数即为临界含水质量分数;均衡分布型的特点是,在整个干燥过程中污泥颗粒内部的含水质量分数和表面的含水质量分数相差很小,因此外界条件对临界含水质量分数和降速转折点含水质量分数的影响也很小,如实验中100和120℃时的干燥特性。当污泥的干燥速率大于一定值时,污泥内部水分向表面的传递速率小于表面水分蒸发速率,因此在整个过程中污泥近表面的水分饱和度远小于内部的水分饱和度,污泥内部水分属于不均衡分布型,并且温度增大和颗粒变大将加剧这种情况,因此在140℃以后,临界含水质量分数和第二临界含水质量分数均随温度升高及污泥颗粒增大而增大。
3.2 颗粒大小和干燥温度对干燥速率的影响
污泥的干燥速率随温度的升高或污泥颗粒的减小而增大。100~160℃时,各颗粒污泥的干燥速率随着干燥温度的增加而平缓增加,说明此时温度对干燥速率的影响相对是比较平均的;而在180~200℃时,小污泥颗粒(1.0和2.5g)的干燥速率明显加快,说明此时温度对小颗粒污泥的影响更加明显。结果说明,减小污泥颗粒可以在增大比表面积的同时提高其干燥速率,例如:10g污泥颗粒的干燥速率从100℃时的1.4mg/(c㎡ min)增加到120℃时的2.0mg/(c㎡ min),而10g污泥颗粒与1.0g污泥颗粒相比较,同样在100℃,可以将干燥速率提升到2.3mg/(c㎡ min),也就是说污泥颗粒减小,即将污泥颗粒从10g减小到1.0g,比干燥温度提高20℃更有利于提高污泥干燥效率。
在同样的干燥温度下,减小污泥颗粒可以提高干燥速率,说明污泥的干燥速率并不仅仅取决于干燥温度,否在在同一温度下不同大小的污泥颗粒在恒速干燥阶段的干燥速率应该是相同的。污泥颗粒表面单位面积得到的实际用于蒸发水分的热量决定了污泥的干燥速率。干燥过程是传热和传质的矛盾体,热量由外向内传递形成的温度梯度和水分由内向外传递形成的湿度梯度相互制约,当热量传递和水分蒸发达到一定平衡时,污泥干燥便进入了恒速干燥阶段。此时,干燥介质向单位面积的污泥表面传递的热量是相同的,其中部分热量又传到了污泥内部,由于大污泥颗粒单位表面积占有的质量大于小颗粒,而温度梯度大于小污泥颗粒的温度梯度,大污泥颗粒表面传入内部的热量大于小污泥颗粒,实际用于蒸发水分的热量小于小污泥颗粒,因此表面干燥速率也小于小污泥颗粒。
3.3 温度对干燥时间的影响
干燥温度越高,污泥颗粒达到相同含水质量分数所需的干燥时间越短,而且通过对干燥时间和温度的分析,发现相同污泥颗粒在不同温度下的干燥时间具有一定的比例关系。
以5g污泥颗粒的干燥过程为例,假设间歇干燥实验中的单位时间间隔内干燥速率是一定的,利用差值法计算出干燥到含水质量分数分别为65%、60%、50%、40%、30%、20%、10%时所需的时间,并将100℃时的干燥时间作为基准值,各温度干燥时间与基准值的比值为P。结果显示:
(1)随着干燥温度的升高,每升高20℃干燥时间差值逐渐减小,以达到含水质量分数40%为例,100和120℃时的干燥时间差值仅为6.3min。
(2)各温度下的干燥时间具有一定的比例关系,例如120℃时的干燥时间为100℃时的77%左右,而200℃时的干燥时间为100℃时的30%左右。
通过对各污泥颗粒干燥时间平均比例与干燥温度之间的关系分析发现,二者之间均呈现二次方关系。但是各个颗粒的关系式存在差异,说明干燥时间与污泥的颗粒大小间也具有一定的关系。
3.4 污泥颗粒大小与干燥时间的关系
以干燥温度为140℃为例,以10.0g污泥的干燥时间作为基准值求出P。可以发现,相同污泥颗粒的干燥时间与颗粒表面积呈线性关系,当干燥温度不同时,污泥颗粒与表面积之间的关系式存在一定的差异,这进一步说明了污泥颗粒大小对干燥时间的影响;另外,100和120℃的线性方程非常接近,其他4各温度的线性方程比较接近,这与污泥干燥过程中弱干燥强度和强干燥强度的两种情况是相对应的。
3.5 烟气湿度及速度对实验结果的影响
本文探讨了温度对污泥干燥过程的影响,前提是假设烟气的气速和温度不变,但是在实际干燥工程中烟气速度和湿度也会影响干燥速率。江阴康顺污泥处理厂的数据显示,该热电厂烟气温度均为155℃,烟气体积流量为13.5万m³/h,相对湿度为8%~10%,20℃下实验室的相对湿度为75%~80%,加热到155℃时的相对湿度仅1%~1.27%。可见,实际烟气的相对湿度略大于实验空气湿度,因此在实际工程中其干燥速率比实验数据略小,但是干燥趋势是相同的,上述实验结果同样适用于实际工程中的干燥过程。江阴工程中干燥其内烟气的速度达8~10m/s,其对干燥速率及干燥过程的影响仍需进一步研究。
4 结论
(1)污泥在100~120℃时,属于弱干燥强度,污泥干燥过程中临界含水质量分数不受温度和颗粒大小的影响;在120~200℃时,属于强干燥强度,温度升高或颗粒变大时临界含水质量分数增大,这是因为在弱干燥强度和强干燥强度下污泥内部水分分布类型不同所致。
(2)污泥表面的干燥速率不是取决于干燥介质的温度,二是取决于污泥颗粒表面单位面积上实际用于蒸发水分的热量。
(3)提高干燥温度或减小污泥颗粒都可以提高干燥速率,减少干燥时间,但是减小颗粒大小可以更大幅度地提高干燥效率,因为减小污泥颗粒大小不仅提高了单位面积的干燥速率,而且增大了比表面积。
(4)干燥温度与干燥时间呈二次方关系,污泥颗粒的表面积与干燥时间呈线性关系。