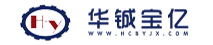
近年来,头台油田开发进入高含水阶段,为了提高采收率和保证原油产量,采用了聚合物驱和三元复合驱等高效采油技术。然而,在采收率得到提高的同时,采出的原油不仅具有较高的含水率,而且还伴随有许多促使生成乳状液及稳定乳状液的乳化剂,以及胶质、沥青质等重组分杂质和固体杂质,这些物质促使老化油形成并稳定存在。由于老化油乳状液成分复杂,含有许多导电性较强的黏土和FeS等机械杂质,经常会导致脱水系统净化油含水超标或脱水后污水水质超标。同时,由于这些杂质的导电性较强,往往会导致电脱水装置频繁出现短路跳闸现象,甚至出现电场击穿事故,严重影响生产系统的安全运行。因此,老化油的及时回收与高效处理,对于保证油田地面系统安全生产运行及解决污水水质恶化、超标等问题至关重要。本文针对老化油的物化特性及头台油田老化油回收处理工艺现状进行分析研究,改善其回收处理工艺,提高处理效果。
1 老化油物化性质与特点
对集输工区老化油样品分析结果表明,老化油含水率为60.5%,含油量为34.2%,其他为以氧化铁、硅铝酸盐等为主的无机盐。由于采出液长期积存、老化而使乳化液的乳化稳定性增强,引起油田开发中地面工程能耗上升,设施、设备运行不稳定,运行负荷率降低,破乳脱水及污水处理用剂量增加,处理难度增大,处理指标不达标等各种影响正常生产的问题。故了解老化油的物化特性与特点是老化油高效回收处理的前提。经过分析,老化油内部的化学组成决定其物理化学性质,所含元素绝大部分以有机化合物的形式存在,主要为饱和烃和芳香烃为主的烃类,以及含氧、硫、氮等杂原子的非烃化合物。由于老化油成分复杂,硫酸盐还原菌大量生长和繁殖,形成菌胶团,同时,原油采出液中夹带的大量机械杂质混合各种生物异形物,使得老化油在表现上呈粘稠状。其次,由于存放老化油的污油池内的轻质组分已经部分或全部挥发,重质组分占有 优势,因此老化油密度较大,粘稠度高。老化油的长期存放还使得其中的部分原油组分被氧化成复杂的氧化物,这些氧化物和原油中的胶质、沥青质等重组分杂质与机械杂质共同作用使得老化油的乳化性能稳定。另外,老化油中总铁的含量比较高,且以无机形态与其他导电离子存在于所含污水中,所以老化油的导电能力远大于普通原油。总之,由于老化油复杂的物化性质和特点,使其形成的乳状液稳定性增强,难以处理。
为了进一步了解老化油的性质特点,将提捞油与落地油2种老化油与普通原油的物化性质进行分析,见下表:
项目类别 | 凝固点/℃ | 含蜡量/% | 重组分含量/% | 机械杂质/% | 总铁/% | 倾点/℃ |
普通原油 | 37.1 | 26.09 | 24.00 | 1.01 | 0.19 | 38.6 |
提捞油 | 38.0 | 25.06 | 26.77 | 1.27 | 0.18 | 39.3 |
落地油 | 36.4 | 26.41 | 24.10 | 58.50 | 1.75 | 38.2 |
由上表可知,老化油中胶质、沥青质等重组分杂质与机械杂质的含量远远高于普通原油,这些物质的存在会使老化油的稳定性大大增强。另外,老化油的含蜡量及总铁含量也均高于普通原油,这些性质特点为老化油的脱水处理增大了难度。
2 老化油乳化稳定性研究
老化油的形成需要一定的过程,通常从地下刚采出的原油乳状液稳定性较低,易实现破乳脱水。但在曝氧条件下,受空气、温度和光照等环境因素的作用,油水界面膜上聚集的乳化剂增多且聚结强度不断变大,导致原油乳化液的稳定性显著增强,形成了所谓的“老化油”。
2.1 老化油乳化形态描述
油水沉降分离实验表明,高乳化程度的老化油在脱水过程中易于在上部油相与下部水相之间形成厚度不一的中间层,中间层呈半固态状黏附在离心管电极上,且难以脱落。中间层杂质经洗油、烘干后,聚结有块状和粉末状,测试其粒径分布为8~500μm,粒径越小,分离难度越大。
进一步分析认为,随着含水率的降低,老化油乳状液以油包水型为主,乳化液不同局部位置处的机械杂质和水的相对含量变化相当,在高效物理或化学处理过程中二者将相互聚并、同步游离分层。
2.2 老化油乳化液的黏度
选择含水率相当的老化油和普通机采油,通过实验对比分析其流变性和黏温特性可知:对于相同的含水体系,老化油乳化程度高,黏度大,流动性能差。
2.3 固相杂质对老化油破乳脱水的影响
通常原油乳状液中的杂质并不是以1种固体颗粒形式单独存在,而是1个聚集体。这一聚集体带有电性,加之原油中一些表面活性物质的存在,不同粒径的机械杂质会被油相润湿并吸附于油相中,主要存在于油水两相界面上,增厚油水界面膜,提高乳化稳定性。
在相同的脱水条件下,随着固相机械杂质含量的增多,破乳脱水效果明显减弱,脱水率大幅降低。当老化油中固相颗粒含量达到0.8%左右时,发现脱水器皿油水界面处有明显的絮状乳化中间层形成。
2.4 老化时间对原油采出液破乳脱水的影响
由上述分析可知,在曝氧条件下,原油的化学组成会发生一定的变化,极性组分含量有所上升。因此,开展了相同条件下的脱水效果评价实验,研究老化时间对原油乳状液稳定性的影响。
实验表明,乳化稳定性因曝氧老化时间的不同而不同,曝氧老化越充分、时间越长,采出液的乳化程度越高、脱水难度越大、脱水率越低。这说明在曝氧老化过程中,乳化剂分子与油水两相中的某些组分可能反应形成新的表面活性化合物,使界面膜的厚度和强度进一步增大。
通过以上室内实验研究,从直观现象和量化上揭示了老化油乳状液的形成及稳定机理,并认识了影响其稳定性的各主要因素,为改善头台油田老化油的回收处理工艺提供了实验和理论依据。
3 头台油田老化油回收处理工艺的应用
3.1 头台油田老化油回收处理工艺现状
头台油田成立于1993年,位于黑龙江大庆市内。近年来,头台油田每年产生老化油都超过1000t,2009年达到2000t以上。为减少老化油的危害,头台油田自2008年将化学脱水器改造为电化学脱水器后,目前已经拥有1套独立的老化油处理工艺流程。其基本处理工艺为:将5000m³事故罐中老化油抽入脱水炉中进行加热,然后进入电化学脱水器进行油水分离,按照分离后含水率的不同,可选择直接进入原油储罐或掺混入正常原油脱水流程进行二次脱水。该流程在试运行中没有达到预期效果,主要是因为原油性质复杂,所用药剂无法在有限的时间内将乳化层完全分解,而且老化油的储存时间较长,轻组分损失较多,固体杂质含量较多,掺混入正常流程后严重影响脱水电场的运行。
3.2 头台油田老化油回收处理工艺改善措施
由上述实验可知,老化油中的重组分杂质与不同粒径的机械杂质等固相含量较高,且曝氧时间过长会导致老化油的乳化稳定性增强,因此,积存时间过长的老化油若采用直接进入油系统的常规处理技术,即便进行处理参数的调节与控制,也将造成电场作用力不够,破乳脱水不达标。头台油田为取得高效的老化油处理效果,在矿场试验中,先后采取了以下几种老化油回收处理工艺改善措施。
(1)改变收油方式。由于浮动连续收油工艺对来水的含油、固体悬浮物、硫化物的去除率远远高于原有的收油槽式固定收油工艺,并且回收的污油含水率较低,只有少量的污水返回脱水系统,降低了脱水系统的处理负荷。连续浮动收油工艺运行以后,沉降罐内可实现连续收油,罐内没有形成老化油层,能够提高污水系统含油污水的处理效果。因此,头台油田在2000m³污水沉降罐中安装了浮动式收油装置。该装置的运行为下一级污水处理减轻了负担,经过现场运行取得了较好的效果。
(2)调整电脱水器的工作压力。一般来讲,适当提高电脱水器的工作压力可以减少原油中轻质馏分的汽化,并增加对蜡质等重组分的溶解能力,从而起到降黏,加速水滴结合、聚并、沉降的作用。为此,在回收老化油过程中,头台油田将电脱水器的压力由回收前的0.15MPa左右提高到了0.25MPa。
(3)适当提高脱水温度。温度升高,在黏度降低的同时,油水界面上附着的各类乳化剂溶解度增大,界面膜的强度自然消弱,分散相的碰撞结合几率增加,有利于脱水。但温度过高,也会使原油中的轻质馏分发生汽化,汽化物上升会阻碍水滴的沉降。因此,头台油田在回收老化油矿场试验期间,将脱水加热炉的出口温度由45℃提高到60℃。
(4)加大破乳剂药量。由于破乳剂的亲水能力远远大于天然乳化剂(沥青、胶质及石蜡等),破乳剂的加入有利于水颗粒的合并,靠油水密度差将水沉降下来,有效地减少了老化油的曝氧时间。但是破乳剂用量过大,会造成脱水器进料含水低,不利于建立底水,易使脱水器电场不能发挥作用,因此,调整来液加药量使电脱水器进口含水率控制在15%左右。在老化油回收试验期间,破乳剂加量由正常生产工况时的180kg/d提高到了320kg/d。
(5)合理控制收油量。老化油回收3~4h后开始进入脱水系统,收油量不宜过大,否则会造成脱水器运行不稳定,甚至“垮电场”。在控制收油量时,对于回收周期过长的老化油,每天收油1~2h,收油量控制在35~60m³,同时加强油中含水及水中含油的化验监测,若脱水效果达标,隔天继续收油,否则暂停收油,采取其他技术措施。
4 结论
(1)由于老化油成分复杂且稳定,因此对老化油的处理应单独进行。与机采油相比,提捞油、落地油中含有较多的导电性较强的黏土和FeS等机械杂质,且由于长时间积存而滋生了大量硫化物及硫酸盐还原菌,给“两段式”净化处理工艺中电脱水器的稳定运行带来了隐患。
(2)影响老化油乳化稳定性的主要因素是较多的胶质、沥青质等重组分及固体杂质含量和长时间的曝氧老化。同时,各种杂质易富集于油水界面上,使界面膜的强度增大,形成稳定性很高的原油乳状液。
(3)对头台油田老化油处理工艺采取以下改善措施:在污水沉降罐内安装浮动式收油装置、将脱水器工作压力提高到0.25MPa、将脱水温度提高到60℃、使破乳剂加药量控制在230kg/d以及合理控制收油量。经现场应用取得了较好的应用效果。