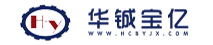
卧螺离心式脱水机(简称离心机)已广泛被用于污泥脱水处理。该污泥离心机,目前负责处理所在石化公司的所有污水处理过程中产生的油泥、浮渣、剩余活性污泥。离心机的运行负荷及运行状况关系到整个石化公司后处理的正常运行,进而影响石化公司污水总排合格率。因此,确保离心机的长周期平稳运行,已成为所在车间的工作重点之一。
1 离心机结构及工作原理
净化水联合车间油泥脱水单元采用的是德国基伊埃韦斯伐里亚离心机。
卧螺离心机是一种螺旋卸料沉降离心机。主要由高转速的转鼓、与转鼓转向相同且转速比转鼓略低的螺旋输送器和差速器等部件组成。当要分离的悬浮液由空心转轴送入转筒后,在高速旋转产生的离心力作用下,立即被甩入转鼓腔内。高速旋转的转鼓产生强大的离心力把比液相密度大的固相颗粒甩贴在转鼓内壁上,形成固体层(因为环状,称为固环层)。水分由于密度较小,离心力小,因此,只能在固环层内侧形成液体层,称为液环层。
由于螺旋和转鼓的转速不同,二者存在有相对运动(即转速差),利用螺旋和转鼓的相对运动把固环层的污泥缓慢地推动到转鼓的锥端,并经过干燥区后,由转鼓圆周分布的出口连续排出;液环层的液体则靠重力由堰口连续“溢流”排至转鼓外,形成分离液(滤后液)。
2 工艺简介
净化水联合车间污水处理场各工段产生的污泥,先经污泥泵排放至浓缩池进行重力浓缩,浓缩后的污泥经切割机绞碎后,再经进泥泵提升至离心机,在离心机入口前,混合絮凝剂聚丙烯酰胺(简称PAM)溶液,经离心机分离后得到含水率为85%以上的干泥饼和滤后液,干泥饼进入焚烧炉进行焚烧处理,滤后液排至污水场重新处理。
3 存在问题及分析
该台离心机原来只负责处理新区炼油和新区乙烯各装置生产过程中排放的污水处理过程中产生的油泥,由于现场工艺条件所限需要间歇运行,自2016年每次计划停机后再次开机经常振动异常上升或者直接超标,导致离心机无法长周期运行或者根本无法再次启动,使得2#工业水场污水处理后的污泥的正常排出受限,进而严重影响2#工业水场的平稳运行。特别是2017年 对污水外排指标提高后,公司通过技术改造增加了老区炼油、第二电厂和老区乙烯部分外排污水进入净化水水场处理,这就使得净化水场的污水处理量不断增加,产生的含油污泥量也逐渐增多,油泥离心机也由间歇性运行改为连续运行,而且处理负荷不断加大。此时,发现了两个严重的问题:一是运行过程中当逐渐提升离心机负荷时离心机机体振动也随之逐渐增大,振动值为20.0mm/s,且离心机处理负荷只能提至6m³/h,就因为离心机振动超标联锁跳车无法运行,远远达不到设计处理能力15m³/h,二是在离心机扭矩过大,平均在32%,进一步制约了离心机的处理能力。由于车间产生的污泥含水率在98%~99%,污泥量约为400m³/d,经浓缩后含水率降低为97%~98%,相应的污泥量减少为约200m³/d,很明显,离心机无法长周期、高负荷运行就不能完全确保车间污水处理场的正常运行。
为了使离心脱水机达到或者接近设计处理能力的同时能够长周期平稳运行,2017年6月12日乙烯钳工车间对离心机进行解体检查。发现下述情况:
(1)圆柱段螺旋槽被黏附物几乎填平,同时黏附物在转鼓表面不均匀分布。黏附物为黑色油性松软固体,带黏性,中间夹带有白色胶状物。对上述沉积物进行分析,认为黑色沉积物是油泥脱水后长时间沉积在螺旋槽内形成的,其中的白色胶状物就是PAM胶体。
(2)螺旋叶片和转鼓存在较严重的不规则磨损。
结合上述发现的情况及离心机的结构进行分析:
(1)从离心机的结构来看,圆柱段螺旋槽被黏附物几乎填平,同时黏附物在转鼓表面不均匀分布,使得螺旋槽被堵和螺旋叶片磨损,使槽深变浅离心机内有效容积变小,同时破坏离心机的动平衡,离心机在高速旋转时(高达4500r/min),这种不平衡力被放大后导致离心机振动上升或超标。螺旋叶片的不规则磨损,使螺旋与转鼓的间隙变大,螺旋的固体传送能力也随之下降,分离效果也逐渐减低,上述两种变化共同作用的结果就是离心机处理能力低,同时离心机振动超标。在此情况下,提高进料泵变频,处理负荷不会有明显的提升,反而因为进料压力增大,导致离心机螺旋内黏附物在压力作用下变实硬化,进一步破坏离心机的动平衡。
(2)从离心机的重量来看,螺旋槽内的黏附物和黏附物在转鼓表面不均匀分布极大的增加了转子的自重,造成低负荷情况下,扭矩过大,甚至是过载联锁保护停车。黏附物在螺旋槽内的分布不均和螺旋叶片的磨损又导致离心机振动幅度增加。
(3)离心机就是利用螺旋将沉降在转鼓内表面上的固体输送到小端排出口,螺旋叶片的边缘与转鼓内表面之间发生相对运行,从而导致螺旋叶片一定程度的磨损,这是无法避免的。
通过上述分析,认为螺旋槽内的黏附物及黏附物在转鼓表面不均匀分布是造成这两个问题的根本原因,所以解决问题的关键就转为如何控制和消除螺旋槽内的黏附物及黏附物在转鼓表面不均匀分布。
4 原因分析
综合上述发现的情况及离心机的结构进行分析,认为造成该问题的主要原因有如下几点:
(1)该离心机处理的污泥,由预处理系统产生的油泥、浮渣等收集排放后形成含油污泥。它是由固体污染物、油、水组成。为黑臭黏稠的浆液,主要成分是油、有机物,其粒子质轻,常温下呈固体或半固体而易变形,一般由水包油、油包水以及悬浮固体组成的稳定的悬浮乳状液体系,是导致其脱水困难的根本原因,也是脱水难度较大的。由于含油污泥的物化性质,造成离心脱水性能差,并且易于黏附在螺旋槽内较难去除,从而导致泥进去后就出不来,逐渐在螺旋槽内黏附与在转鼓表面不均匀分布,形成上述沉积物。车间为保证含油污泥的可脱水性,采用的在含油污泥浓缩池进料中增加剩余活性污泥,使得油泥、浮渣及生化系统排出的剩余活性污泥,这“三泥”一起进入含油污泥浓缩池进行浓缩处理,再进行离心脱水处理。由于剩余活性污泥里面含有部分活的微生物,其会对油泥中的油和有机物起一定的降解作用,降低油泥的黏度,从而使污泥物化性质有所改变,脱水性能得到一定改善。根据车间的实际产泥情况,含油污泥与剩余污泥的体积比,控制在3:1到5:1。
(2)由于离心机是利用固液两相的密度差来实现固液分离的,因此,污泥颗粒比重越大越易于分离。为进一步改善污泥脱水性能,进行离心脱水前需投加絮凝剂,使固相凝聚,污泥固相和液相分离后更易于脱水。车间是在离心机入口前投加浓度为3‰的絮凝剂PAM溶液,采取自动配药系统,投加前絮凝剂PAM已在药罐充分熟化,无块状未溶物。但在实际运行中,PAM投加量平均在250~600L/h,泥饼干度和上清液质量控制均较好,满足处理要求。但由于PAM溶液浓度较大,当PAM需要量较小时,只能降低加药泵的供给量,这样势必造成因投加量过低,与进泥混合不均,导致PAM和污泥混合不均局部PAM过量。过量的PAM因不发生絮凝而“失效”,聚集形成块状物,被黏附物包裹并一起黏附在螺旋槽内,表现为白色胶状物。
(3)因生产的需要,离心机自2018年10月开机以来,直至2020年10月检修未做任何清理,其间只按照厂家说明进行常规的自动冲洗,由于水的去污能力不强,加之转鼓内壁及螺旋槽内的黏附物为疏水的油性污垢和沉积物,冲洗的强度不够,效果不明显,导致螺旋槽内的沉积物越积越多,厚度越来越厚。
5 预防措施
针对以上分析制订了以下五点预防措施。
(1)增加进入油泥浓缩池的活性污泥,分析含油污泥理化物性及时调整含油污泥和活性污泥进入油泥浓缩池的比例,根据车间的生产情况,合理安排生化污泥的排放量。污泥浓缩时间由2h延长至4h,使不同种类的污泥之间充分混合,更好的压缩沉降,增加污泥比重。
(2)在污泥浓缩池中投加聚合氯化铝铁,并充分鼓风混合反应,破坏污泥的胶体结构,减少其与水的亲合力,对污泥进行预调理,使其胶体颗粒进一步增大,提高污泥颗粒的比重。
(3)絮凝剂PAM投加浓度由3‰降低为1‰~2‰,在保证PAM投加量的前提下,加大了药泵的供给流量,避免或减少了其与污泥混合不均而发生局部过量的情况,同样多的流量所含的PAM有所减少,所以减少了PAM形成的白色胶状物。
(4)增加停车冲洗时长及冲洗强度。每次停机冲洗时在执行PLC程序的自动停机冲洗程序后,对含有离心机进行全速(4500rpm左右)冲洗1小时,再按照全速(4500rpm左右)冲洗5分钟,中速(2500rpm左右)冲洗5分钟,低速(800~1000rpm)冲洗五分钟的程序执行。
(5)每次停机后对转鼓和螺旋进行一次CIP清洗(亦可根据实际生产情况,灵活安排),CIP清洗液即配制1%~1.5%的氢氧化钠溶液,确保pH在12~13。浸泡24h,并每间隔2h,将转鼓和螺旋分别旋转180°,使转鼓和螺旋充分浸泡,用水冲洗直至澄清。
6 总论
检修后试运行,各主要参数如下表所示:
主要参数 | 进料泵变频(%) | 进料量(m³/h) | 扭矩均值(%) | 振动均值(mm/s) |
数值 | 40 | 3.8 | 4.5 | 3.8 |
60 | 9.3 | 8.3 | 4.7 | |
100 | 14.8 | 12.7 | 5.6 |
由上表可知,离心机处理在接近设计负荷15m³/h的大负荷处理污泥的情况下,扭矩、振动都明显下降,在设备长期运行的允许范围内,振动值远远低于该离心机的振动报警值12mm/s。2020年10月~2021年1月,离心机的运行振动值主要保持在3~6mm/s。
2021年1月,离心机停机经过冲洗后对离心机解体检查,很明显,螺旋槽内沉积较少,说明以上措施对黏附物有一定的预防和清除作用,保证了螺旋和转鼓组成的转子部分保持有效的动平衡,为离心机平稳高负荷运行创造了条件。