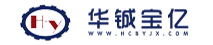
油田含油污泥主要来源于各类储罐、油水分离器以及偷油漏油事故。含油污泥中的油气挥发造成局部地区空气总烃浓度超标,油气中含有的某些烃类物质具有致癌、致畸、致突变作用;流失于地表的含油污泥不仅污染地表水甚至地下水,而且造成土壤板结、草原退化,生态环境遭到严重破坏。据有关部门统计,仅大庆、胜利、辽河三大油田每年产出的含油污泥就达200万m³。近年来,因资源短缺,国内外科研人员对于资源化、减量化处理含油污泥的研究从未间断过,主要研究成果有含油污泥的高温裂解法、溶剂萃取法、生物处理法等。此外,超声波处理和污泥分离器等新技术、新设备作为含油污泥处理的辅助手段也应运而生。而调质-机械离心分离技术作为一种比较成熟的含油污泥处理技术,因其原油回收率高、浓缩脱水效果好、处理量大等优点而被广泛应用。卧螺离心机作为机械离心分离的核心设备,其经济运行方案对于减少运输及后处理费用、增加原油回收量、提高油田经济效益具有重要意义。本文中针对大庆油田某聚驱区块污水站含油污泥进行现场试验及室内化验分析,对离心式污泥减量化处理效果的影响因素进行研究,确定了离心式污泥减量化处理优化运行方案。
1 离心式污泥减量化处理工艺流程
该工艺流程采用外输水经加热、加压后,由喷头对罐内含油污泥进行射流剥离,含油污泥从清扫孔流入罐外的缓冲水池,由浸没泵将污泥泵送至加热搅拌罐,在加热搅拌罐中加热至70℃,并搅拌均匀。然后泵送至卧螺离心机中进行离心处理。为提高处理效果,在污泥进入卧螺离心机前在线加入絮凝剂,使污泥中的细小沙粒进行絮凝,减轻高速离心运动中沙粒的破碎分散。离心处理后,污泥中的水相进入沉降罐,进行油水分离,浓缩后的污泥装车外运。
2 室内化验分析
评价离心式污泥减量化处理效果的指标为卧螺离心机出泥口泥饼的含水率及出水口的含固率。
2.1 泥样检测方法
该检测装置的化学药剂为甲苯,甲苯的沸点为110.6℃,密度小于水且极微溶于水。检测过程为:缓慢加热圆底烧瓶中的甲苯,甲苯蒸气冷凝后回流至分液管和索氏提取器,索氏提取器中泥样逐渐被甲苯浸没,液态甲苯对泥样中的原油进行萃取,同时使泥样中的水加热蒸发。水蒸气同圆底烧瓶中的甲苯蒸气一同经冷凝管冷凝后回流至分液管,由于水的密度大,水位于分液管下层,所以泥样中的含水量可由分液管读取。索氏提取器中甲苯达到一定高度后回流至圆底烧瓶,如此循环直至将泥样中的油和水脱除,剩余的泥沙经烘干后称重。由差重法得知泥样中含油量。
2.2 水样检测方法
水样是卧螺离心机进口和出水口试验样品的总称。水样含水量检测同泥样检测装置类似,将索氏提取器拿掉,直接将分液管与圆底烧瓶连接。简化后的实验装置只能检测水样中的含水量,而水样含油量检测需采取分光光度法,由吸光度值和标准曲线计算得到水样中含油量。而水样中含固量由差重法计算得到。
3 离心式污泥减量化处理影响因素
3.1 设备运行参数对处理效果的影响
3.1.1 转鼓转速
转鼓转速直接影响物料所受离心力大小,转速越高,所受离心力越大,但过高的转速势必会消耗更大的动力,离心机轴瓦温度升高,不利于安全平稳运行。同时,过高的转速还会破坏絮凝体,使脱水效果变差。在卧螺离心机差速9.2r/min、堰板高度112mm、进泥量10m³/h、加药量200g/m³时,调整离心机的转速,考察转鼓转速对污泥处理效果的影响。
转速对处理效果的影响如下表所示:
转速/(r/min) | 含水率/% | 含固率/% | ||||
入口 | 出水口 | 出泥口 | 入口 | 出水口 | 出泥口 | |
2073 | 98.20 | 98.76 | 77.51 | 0.78 | 0.43 | 21.69 |
2194 | 98.17 | 98.85 | 72.83 | 0.86 | 0.39 | 23.51 |
2248 | 98.28 | 99.11 | 71.42 | 0.73 | 0.36 | 23.83 |
2281 | 98.32 | 99.32 | 70.10 | 0.82 | 0.24 | 24.92 |
2339 | 98.40 | 99.51 | 69.30 | 0.71 | 0.22 | 25.76 |
2431 | 98.14 | 99.34 | 71.26 | 0.93 | 0.28 | 23.98 |
在其他条件一定的情况下,随着转速的增加,脱水后污泥的含水率呈下降趋势,转速为2339r/min时,含水率达到低点,当转速进一步提高时,脱水后污泥的含水率反而增加,其原因在于过高的转速降低了絮凝剂的效果。因此,卧螺离心机的转速应控制在2300~2400r/min。
3.1.2 差速
差速直接影响物料在离心机内的停留时间,停留时间越长,离心时间和挤压时间越长,沉渣含水率就越低。在卧螺离心机转速为2213r/min、堰板高度112mm、进泥量9m³/h、加药量200g/m³时,调整离心机的差速,得到污泥浓缩处理效果和差速之间的关系,结果如下表所示:
差速/(r/min) | 含水率/% | 含固率/% | ||||
入口 | 出水口 | 出泥口 | 入口 | 出水口 | 出泥口 | |
9.0 | 98.32 | 99.42 | 63.21 | 0.71 | 0.21 | 23.41 |
9.5 | 98.21 | 99.44 | 64.13 | 0.76 | 0.25 | 22.56 |
10.0 | 98.25 | 99.35 | 68.36 | 0.67 | 0.37 | 21.75 |
10.5 | 98.24 | 99.36 | 71.92 | 0.81 | 0.39 | 21.03 |
11.0 | 98.13 | 99.30 | 74.17 | 0.77 | 0.45 | 19.96 |
11.5 | 98.29 | 99.10 | 76.85 | 0.83 | 0.68 | 18.67 |
从试验数据可以看出,随着差速的降低,处理后的污泥含水率越低。但过低的差速,扭矩会逐渐升高,当接近离心机预设的扭矩连锁停车值时,离心机会自动停车,同时会造成污泥停留时间过长,离心机出泥缓慢,甚至堵塞。因此,差速在9.5~10.5r/min比较合适。
3.1.3 堰板高度
堰板高度直接影响出泥口泥饼的含水率及出水口物料含固率。在卧螺离心机转速2373r/min、差速10r/min、进泥量9.5m³/h、加药量200g/m³时,调整离心机的堰板高度,以获得污泥离心处理与堰板高度间的变化规律,具体测试数据见下表:
堰板高/mm | 含水率/% | 含固率/% | ||||
入口 | 出水口 | 出泥口 | 入口 | 出水口 | 出泥口 | |
106 | 98.21 | 99.39 | 59.15 | 0.96 | 0.35 | 24.53 |
108 | 98.30 | 99.35 | 60.81 | 0.91 | 0.33 | 22.67 |
110 | 98.24 | 99.39 | 61.95 | 0.99 | 0.27 | 22.15 |
112 | 98.04 | 99.39 | 64.92 | 1.02 | 0.23 | 21.39 |
114 | 97.96 | 99.39 | 66.44 | 1.06 | 0.22 | 21.20 |
116 | 98.28 | 99.37 | 67.80 | 0.97 | 0.19 | 19.22 |
随着溢流堰板高度的降低,离心机处理后污泥的含水率逐渐降低。当溢流堰板高度下降至108mm时,脱水后污泥含水率60.81%,但出水口滤池的含固率为0.33%,超过了设计要求的0.30%。因此,堰板高度为110mm比较合适。
3.2 试验介质参数对处理效果的影响
3.2.1 进泥量
污泥的进泥量决定了离心机的处理负荷和污泥在离心机内的停留时间,这将对处理效果产生影响。在卧螺离心机转速2185r/min、差速11r/min、堰板高度114mm、加药量200g/m³时,调整离心机的进泥量,以获得进泥量对污泥浓缩处理的影响。具体测试数据如下表所示:
进泥量/ (m³/h) | 含水率/% | 含固率/% | ||||
入口 | 出水口 | 出泥口 | 入口 | 出水口 | 出泥口 | |
5 | 97.93 | 99.56 | 52.88 | 1.01 | 0.24 | 35.14 |
6 | 98.05 | 99.50 | 54.03 | 0.97 | 0.24 | 32.67 |
7 | 97.80 | 99.48 | 55.21 | 1.08 | 0.23 | 29.55 |
8 | 98.17 | 99.40 | 61.22 | 0.95 | 0.27 | 24.91 |
9 | 98.20 | 99.34 | 66.56 | 0.88 | 0.28 | 22.04 |
10 | 98.14 | 99.25 | 69.62 | 0.83 | 0.36 | 19.63 |
随着进泥量的增加,脱水后的污泥含水率总体呈升高趋势。当进泥量为5~7m³/h时,处理后的污泥含水率变化不大,上升较缓;当进泥量继续增加时,处理后的污泥含水率增加明显。所以离心机入口的进泥量应控制在6~7m³/h较为适宜。
3.2.2 絮凝剂投加量
添加絮凝剂在实际应用中俗称“加药”,加药的目的在于使污泥中分散的物质絮凝,利于污泥在离心力的作用下与水分离。在卧螺离心机转速2296r/min、差速10.5r/min、堰板高度112mm、进泥量6m³/h时,调整加药量,获得加药量与处理效果之间的变化规律。具体测试数据如下表所示:
加药量/ (g/m³) | 含水率/% | 含固率/% | ||||
入口 | 出水口 | 出泥口 | 入口 | 出水口 | 出泥口 | |
150 | 97.92 | 99.45 | 67.40 | 1.02 | 0.35 | 20.39 |
175 | 97.15 | 99.45 | 62.20 | 9.87 | 0.29 | 23.11 |
200 | 96.92 | 99.44 | 56.37 | 9.96 | 0.27 | 27.73 |
225 | 98.07 | 99.44 | 53.16 | 1.05 | 0.23 | 29.64 |
250 | 98.01 | 99.40 | 52.06 | 1.07 | 0.22 | 34.38 |
275 | 97.95 | 99.42 | 51.22 | 1.02 | 0.19 | 37.41 |
随着加药量的增加,处理后的污泥含水率总体呈下降趋势。加药量增加到275g/m³时,脱水后污泥的含水率可降至51.22%。在加药量由150g/m³增加到225g/m³的范围内,污泥含水率随加药量的增加急剧降低,加药量在225~275g/m³含水率降低缓慢。同时考虑到加药成本,加药量维持在225~250g/m³较为合理。
3.2.3 污泥含水率
卧螺离心机进口污泥的含水率直接影响离心机运行和加药量大小。在卧螺离心机转速2271r/min、差速10.5r/min、堰板高度112mm、进泥量6m³/h时,对不同含水率的污泥进行处理,获得污泥含水率与处理效果之间的变化规律。具体测试数据如下表所示:
污泥入口含水率/ % | 含水率/% | 含固率/% | ||||
入口 | 出水口 | 出泥口 | 入口 | 出水口 | 出泥口 | |
98.66 | 98.66 | 99.13 | 65.46 | 0.49 | 0.31 | 20.39 |
96.39 | 96.39 | 96.81 | 64.22 | 2.63 | 2.38 | 23.36 |
94.37 | 94.37 | 96.11 | 62.79 | 3.31 | 2.03 | 25.15 |
91.71 | 91.71 | 96.39 | 61.09 | 4.41 | 1.56 | 29.06 |
89.85 | 89.85 | 95.43 | 59.62 | 4.23 | 1.49 | 32.17 |
随着污泥入口含水率的增加,处理后污泥含水率不断上升,当入口污泥的含水率从89.85%上升到98.66%时,与之对应的是浓缩后的污泥含水率由59.62%升高到65.46%。
4 工艺方案制定及结果分析
卧螺离心机的处理效果是各个因素综合作用的结果。在现场工艺中可以调整优化的影响因素有转鼓的转速、转鼓与螺旋输送器之间的差速、堰板高度、进泥量、加药量、污泥入口含水率这6项因素。由于同一沉降罐中的污泥含水率相差较小,堰板高度需要停机调整,加药量与进泥量的大小相关,因此,在工艺方案的初步制定中,堰板高度为110mm,加药量为225g/m³,只考虑工艺中重要且容易操作实现的转速、差速和进泥量作为研究对象。为了通过较少的试验次数得到较优的工艺运行方案,采用正交试验方法设计试验。因素水平表如下:
水平 | 因素 | ||
A转速/(m/s) | B转速/(m/s) | C转速/(m/s) | |
1 | 2248.0 | 9.5 | 6.0 |
2 | 2281.0 | 10.0 | 7.0 |
3 | 2339.0 | 10.5 | 8.0 |
由试验结果可知,RA>RC>RB,所以转速是影响离心处理效果的主要因素,进泥量和差速次之。此外,A因素水平的变动对实验结果有影响,由KA3<KA1<KA2可以断定A3为A因素的优水平。同理,可确定B2和C2分别为因素B和因素C的优水平。3个因素的优水平组合A3B2C2为本次实验的较优水平组合,即转速为2339m/s,差速为10m/s,进泥量为7.0m³/h,为本次试验的较优运行方案。在此工况下,污泥含水率由97.03%下降到47.44%,达到了污泥减量化处理的目的。
5 结论
(1)针对污水站含油污泥组成及分布特点,设计了污水站离心式污泥减量化处理的工艺流程。该工艺流程利用污水站现有流程,处理后含油污水直接进沉降罐进行油水分离,可有效回收污泥中原油。
(2)对污水站离心式污泥减量化处理进行现场试验及室内化验,结合化验结果,分析了卧螺离心机运行参数和试验介质参数对减量化处理效果的影响规律。结果表明,转速过高会影响脱水效果,且考虑到经济及安全因素,差速、絮凝剂添加量及进泥量应控制在合理的范围内。
(3)综合考虑离心式污泥减量化处理的影响因素,采用正交试验方法设计试验。对试验结果进行分析,确定了较佳处理工艺参数为:转速2339r/min,差速10r/min,进泥量7m³/h,堰板高110mm,加药量225g/m³。采用该方案,处理后污泥含水率由处理前的97.03%下降到47.44%,处理效果良好。