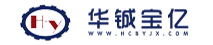
在江汉盐化的漂粉精生产中,LW450*730型卧式螺旋沉降离心机是关键的设备,卧式螺旋沉降离心机是利用离心沉降原理分离悬浮浆料的机器,对0.005~3mm范围内的固相颗粒,比重差较大的固液悬浮浆料,均可进行固液两相分离和颗粒分级。但是随着现运行生产装置的卧式螺旋沉降离心机长周期运行,离心机转鼓内壁、内螺旋等部件磨损损坏较为严重,在使用过程中设备故障频繁,分离效果下降,严重影响了漂粉精的正常生产。为解决离心机存在这些问题,本文将结合LW450*730型卧式沉降离心机在漂粉精生产过程中的使用情况及曾经发生的非常见故障,从操作、日常维护及检修等多个角度探讨避免LW450*730-Ⅰ型离心机在漂粉精生产运行中发生类似非常见事故的诊断方法和进一步改进提高的预防措施。
1 LW450*730卧式沉降离心机的工作原理
LW450*730型卧式螺旋沉降离心机为漂粉精生产的特护设备,主要是把湿的固态次氯酸钙滤饼从氯化浆料中分离出来,用强制离心把母液和固态次氯酸钙晶体分离,固态滤饼的水分含量是40~50%。主要的工作原理是离心机启动到全速后,悬浮浆料由进料管进入离心机螺旋内,浆料通过螺旋内的出料孔进入转鼓,在离心力的作用下,比重较大的固相物料沉附到转鼓壁上,形成一个环形的固相层,螺旋输送器在差速器(保证差转速稳定的装置)的作用下,实现了于转鼓转速、差转速的无级可调,可适应相对的流量、浓度的变化,保证了良好稳定的分离效果。螺旋与转鼓产生相对的差转速,将脱水后的固相沉渣从圆锥转鼓的小端出渣口推出,比重轻的澄清液从圆柱端的溢流口溢出,如此连续不断地工作,达到连续分离的目的。
2 常见的LW450*730卧式螺旋卸料沉降离心机故障
作为高速旋转的设备,正常的润滑油品缺失或变质等导致轴承温度升高,以及异物进入所造成的震动和瞬间电流的异常等常见故障在日常设备管理中得到较好的把控。
3 非常见故障诊断及预防
由于漂粉精物料具有高腐蚀的特性,在离心机的使用过程中,由于硬度相对较小的钛质螺旋叶片和转鼓直接与晶体以及介质中夹带的硬质杂质接触,离心机高速运转时冲击磨损不可避免。虽然这种离心机的螺旋叶片外沿安装有耐酸碱耐磨陶瓷片,但经过长周期使用,螺旋输送器耐磨陶瓷片破裂、脱落造成螺旋叶片、外转鼓内壁磨损等现象仍会发生,如果控制得当,简单维修,维持平衡后就可再次投入使用,否则,就会造成设备返厂大修,不仅费用高,检修周期长,并且会影响钛质设备的基材寿命。这类非常见故障包括:
(1)离心机转鼓螺旋及内壁磨损严重。
(2)离心机内螺旋叶片耐磨瓷片大面积脱落,螺旋钛质基座深度磨损。
(3)长期磨损造成各部件配合间隙尺寸增大。
起初,此类非常见故障都属于事后被动维修,以下是对于关键设备离心机怎样能杜绝类似故障的重复发生,怎样预知设备隐患、主动维修,延长设备完好时间,应予以补救措施。
(1)离心机转鼓螺旋及内壁磨损严重。离心机在运行中,由于浆料进入高速运转的离心机中直接与螺旋和转鼓内壁接触,浆料中的晶体对转鼓螺旋和转鼓内壁长时间摩擦,导致螺旋叶片和转鼓内壁的严重磨损,影响分离效果,给生产带来影响,使装置产能下降,同时离心机故障频繁,检修次数多,投入大量的人力、物力,导致维修费用不断增加。
处置措施:
①离心机螺旋安装陶瓷片,增加螺旋叶片的耐磨性。离心机螺旋上采用粘贴或螺钉固定的方式安装了近350片左右独立陶瓷片,利用陶瓷片的耐磨性能有效保护离心机转鼓螺旋的磨损,增加螺旋叶片的耐磨性,确保了分离的效果,降低离心机故障的频次,节约维修成本。
②对离心机转鼓筒体内壁采取涂抹耐磨涂层处理。传统修复工作基本采用氩弧焊补焊工艺,由于转鼓筒体直径为φ480毫米,壁厚仅为13毫米,直接进行焊接修复易造成转鼓热变形,且焊补质量不稳定,工作操作难度大,焊后修磨量大。而目前市场上有性能较好的耐磨修复产品,其采用聚合陶瓷高分子耐磨技术,对于各种不同磨损机理、不同流速、不同温度、不同颗粒大小、不同酸碱介质等工况,有针对性地设计不同的工艺配方,涂层与基体结合强度高,耐磨性好,操作工艺方便快捷。
离心机筒体修复采用了北京新天山TS228耐磨涂层(倍造耐)产品,该产品不流淌,成型性好,涂层厚度可达30mm,与基体结合强度高,附着力强,固化速度快,操作工艺性好,可进行大面积耐磨修复及预防护耐磨性好,适合于中等负荷的粗颗粒磨损工况如:溜槽、旋流器、振动筛、离心机等。
(2)内螺旋叶片耐磨瓷片大面积脱落,螺旋钛质基座深度磨损。离心机在长期使用过程中,由于漂粉精浆料中含有部分坚硬的颗粒(小石子)物,使其夹在转鼓与螺旋之间,由于陶瓷片较脆,碰撞时极易破碎,造成破碎后的陶瓷片卡在转鼓与螺旋之间,造成其他正常的瓷片随之破碎的脱落,就将离心机螺旋片基体(>15mm)磨损的非常严重,转鼓内壁磨出多条凹槽,深度大于3mm以上,严重的深达6mm,宽8mm。由于陶瓷片脱落,造成螺旋叶片直接与沉渣接触,由于沉渣和叶片间的相对运动,导致螺旋叶片急剧磨损。由于螺旋叶片磨损量较大,造成螺旋输送沉渣能力显著下降,沉渣的湿含量增加,对工艺造成较大影响。同时,由于螺旋与转鼓筒体的径向间隙增大,使离心机的分离效果不好,达不到漂粉精浆料的分离工艺要求。同时,由于螺旋与转鼓筒体的径向间隙增大,使离心机的分离效果不好,达不到漂粉精浆料的分离工艺要求。
同时随着转鼓内的沉渣浆料填满沟槽,由于转鼓本体质量增加不均布,导致离心机分离效果差、平衡失去,振动大。造成磨损主要有两个因素:
①离心机所分离的浆料内含有大颗粒硬质杂物在通过离心机螺旋和外转鼓内壁时,与安装螺旋上的耐磨瓷片产生摩擦,甚至卡碰,造成瓷片快速磨损和崩落,这些颗粒来源主要是原料石灰携带的矾石、砂砾等。
②离心机转鼓振动造成基座上的陶瓷片断裂脱落,而外转鼓内壁与内螺旋叶片外沿只有1~3毫米配合间隙,耐磨陶瓷片有5毫米厚,一旦陶瓷片断裂脱落,如能被螺旋叶片推出去还好,否则被卡在某个位置就会出现耐磨瓷片的大量迅速脱落问题,并有可能对离心机外转鼓内壁产生切割性划伤。表观上,离心机的运行工况无明显变化,但失去耐磨瓷片保护的螺旋钛质基座就会迅速磨损。
处理措施:离心机螺旋叶片焊接修复,并镶固陶瓷片。
针对各离心机螺旋叶片磨损情况,采取了两种修复方法, 种为去除全部螺旋叶片,在筒体直接焊接叶片成型,其成型后的螺旋叶片强度高,但焊接时叶片螺旋曲线不易控制。第二种为去除部分叶片,在剩余叶片上对焊同等厚度钛板成型。其叶片螺旋曲线在焊接时较易控制,但成型后螺旋叶片强度较低。
螺旋叶片修复完成后,对内螺旋的螺旋叶片焊接修复,螺旋叶片增加陶瓷片座,镶耐磨陶瓷片,并用钛螺钉固定。满足内螺旋叶片与转鼓内面配合间隙在指标范围内。从而有效防止陶瓷片脱落,避免了螺旋叶片直接与沉渣接触,造成叶片磨损。
(3)长期磨损造成各部件配合间隙尺寸增大。由于离心机的长时间运行,各部件磨损损坏较为严重,配合间隙增大,造成离心机轴承跳动明显,引发离心机整机振幅增大,影响设备运行。通过对磨损后的离心机各部件的现场实测,各部件磨损后的配合情况如下表:
配合部位 | 实测尺寸 | 配合间隙 | 结论 |
转鼓带轮端轴径 | φ108-0.05 | 间隙0.43 过盈0.15 | 带轮孔明显椭圆变形,配合差 |
带轮内径 | φ108+0.38/-0.20 | ||
转鼓差速器端轴径 | φ108-0.02 | 间隙0.07 过盈0 | 差速器法兰孔径微椭圆变形,配合较差 |
差速器法兰内径 | φ108+0.05/-0.02 | ||
主轴承(带轮端)轴径 | φ110-0.06 | 与轴承配合 | 配合差 |
螺旋轴(带轮端)轴径 | φ75+0.04 | 间隙0.28 | 配合差 |
轴瓦(带轮端)内径 | φ75+0.32 | ||
螺旋轴(差速器端)轴径 | φ75+0.05 | 间隙0.32 | 配合差 |
轴瓦(差速器端)内径 | 0.75+0.37 | ||
螺旋推力轴承轴径 | φ70-0.07 | 与轴承配合 | 配合差 |
根据上表可以看出,离心机长期运行,各部件持续磨损造成各部件配合间隙尺寸增大,无法保证离心机分离效果,达不到漂粉精生产工艺的要求。
处理措施:
①对转鼓带轮端及差速器端两处配合进行修复。具体措施为对带轮及差速器法兰孔进行焊接并加工至尺寸φ108H7,并对带轮及差速器法兰等部位进行同轴度、跳动度等相关形位公差检查,满足各项尺寸配合要求。
②更换两端螺旋轴瓦,要求与螺旋轴径配合间隙在0.04-0.08之间。
③对转鼓主轴承轴径及螺旋推力轴承轴径进行喷涂加工,满足尺寸配合要求。
4 建议及结论
漂粉精LW450*730卧式螺旋卸料沉降离心机故障分析及维修处理措施是在平时工作中结合相关专业知识总结整理而成的。由于漂粉精物料含有碳酸钙颗粒,又含有强氧化作用的次氯酸钙,所以该物料在高速分离过程中对设备既产生高强度的磨损,又具有强腐蚀性。所以在漂粉精生产中,该离心机上述故障现象较具典型性,通过状态监测及时诊断设备运行状态,以离心机的实际状况为依据、根据生产需要制定出预知性维修计划的维修体制。预知性维修要求:不断地测知表征设备实际状态的参数;对测得参数进行分析、判断,做出是否发生故障以及故障类型、故障程度的评价;推测离心机状态的发展趋势,估算出较佳的维修时机。预知性维修实现了需要停车时才停车;需要更换零部件时才更换;需要维修什么项目才维修什么项目,既不让设备带病超期使用,也不要过度维修。积极开展主动维修,预知维修,改进提高检维修技术,有效延长设备完好使用时间,降低维修费用。不断完善LW450*730-Ⅰ离心机的维修方式,为漂粉精装置平稳连续生产奠定基础。