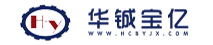
1 背景
石油炼制企业所产生的油泥和浮渣,处理难度大,成本高,尤其是新的环保法颁布后,危险废物非法处理将获刑,目前油泥浮渣处理是困扰炼油企业的重要环保问题,目前长岭分公司一污含油油泥的处理主要为两种方式。
(1)通过延迟焦化装置回炼,利用焦炭塔生焦后大吹气和小给水之间的间隙,时间约为1小时,把油泥注入到焦炭塔内利用余热回炼。
(2)送往热电作业部CFB锅炉掺烧,此方式消化油泥、浮渣量较大,每天可以达到20~30吨。但掺烧时,油泥易堵塞喷嘴,故障率较高,且油泥含水率较高,会造成能耗的增加。因此,靠CFB锅炉掺烧完全消化油泥也难以做到。
基于此,当前急需一种高效的油泥浮渣脱水工艺和处置方式,从而确保水务作业部的正常运行,达到油泥浮渣减量化、无害化、资源化处理的目的。
2 当前国内炼厂油泥浮渣脱水的主要处理方式
石化炼厂污水处理中产生的油泥(包括浮渣、底泥、生化油泥)属于有毒物质,国外学者对油泥中水的形态和分布做了大量的研究工作,其可将油泥中的水分为:间隙水(约占水体积的70%)、表面吸附水、毛细水、结合水(约占10%)。对油泥脱水的处理,迄今为止国内未掌握经济合理的处理手段,因此找出一条适合我国国情的、经济技术可行的油泥脱水技术迫在眉睫。当前主要采用的方法:调质-重力沉降浓缩工艺、调质-机械脱水工艺、调质-超声波辐射脱水、热萃取脱水等。
(1)油泥浮渣改性-重力沉降浓缩工艺
油泥脱水过程实际上是油泥的悬浮粒子群和水的相对运动,其中浓缩、化学调质、脱水是含油油泥处理必不可少的环节。高含水量的含油油泥不能直接进行机械脱水操作,先必须进行调质,即通过一定手段调整固体粒子群的性状和排列状态,使之适合不同脱水条件的预处理操作;然后才能实现泥、水分离。目前国内较多炼厂,如胜炼、长岭石化、中原油田等对油泥调质改性后,再“多次”重力沉降脱水,但由于油泥中的油成分主要为胶质、沥青质、石蜡等,通过重力沉降速度慢,短时间内难以达到较好的效果,处理后油泥含水率大于85%。
(2)机械脱水工艺
机械脱水主要技术有真空过滤、加压过滤、滚压过滤和离心过滤,其原理是在过滤介质两面产生压差,使固体颗粒被截留而水分通过。目前国内主要使用三相卧螺离心机对油泥进行脱水,如镇海炼化、洛阳石化、上海石化、济南炼油厂等,但脱水效果均不理想,主要表现:脱后油泥含水率仍75%~85%之间,脱水后水相中悬浮物含量高,离心机运行维护成本高。此外,通过离心设备对油泥脱水,还须注意离心机的离心因数、油泥停留时间的平衡和调节等,条件较苛刻。
(3)超声波辐射脱水
超声对有机物的降解主要基于超声空化和空化自由基原理:当一定强度的超声作用于油泥体系时,将产生大量的空化泡,这些气泡会随着声波变化而改变大小并瞬间破灭,产生空化现象,形成瞬间热电,产生高温、高压。而且超声还能起强化传质及絮凝等传递作用,其振动能量可不断被油泥絮体吸收转化为热能,起到一定的降粘作用,此方法目前 实验室研究。
(4)热萃取脱水
溶剂萃取法基于相似相溶原理:利用萃取剂把有机物从油泥中抽取出来,通过蒸馏把萃取剂从混合物中分离出来循环使用,剩余的废油得到回收利用。萃取剂包括有机溶剂和超临界溶剂。目前,萃取法处理含油油泥还在试验开发阶段,其关键是要开发出性能价格比高的萃取剂,目前还没有实际应用于炼厂含油油泥处理案例。
3 污水处理场油泥浮渣处理实践效果
针对长岭分公司二污晒泥场油泥,油泥脱水设备安装后,从2016年9月底开始进行油泥脱水工作。
该套油泥脱水设备进泥量约5~6t/h,脱出液出水澄清,通过追踪监测分析,在晒泥场油泥脱水期间,脱出液水量约5t/h,通过分析COD稳定在400~1180mg/L之间,油含量<50mg/L;经潜水泵输送至污水系统处理,没有对后续生化系统产生不良影响,二污污水外排或回用均能达到相应指标。长岭分公司二污晒泥场油泥脱水试验至2016年10月中旬,晒泥场及边沟约500t油泥处理完成。2016年11月初,利用此设备进行了二污中和池底部油泥的处理,在15天的时间内完成了约300m³的油泥脱水并干化处理。
4 结论
通过采用油泥浮渣脱水机处理过后的浮渣、油泥能够大幅的减量,脱出液中油水分离效果好,污水直接进入生化系统处理不会造成系统冲击,污油能够直接进入污油回炼系统之中。后期通过污泥干化装置的处理,油泥浮渣能够有效的变成无粘性粉末,进入热电作业部CFB装置掺烧,达到无害化处理。脱出液沉降少量时间可实现油、水分离,出水油含量低,可进入含盐污水隔油池,对系统影响小;脱出的油可进入污油系统,从而实现油泥的资源化利用。