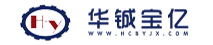
石油钻井废泥浆已被列入 危险废物名录,其对环境的危害极大,必须对其进行有效处理方可排放或资源利用。目前,国内对其处理的主要方法有:循环利用法、直接排放法、固液分离法、固化法等。其中的固液分离法因其具有适应性广、处理彻底、切合 节能减排政策等优点,是目前国内研究的热点。国内固液分离法所采用的核心分离设备主要是离心机、板框压滤机等传统设备,但这些设备分离废泥浆时,都需要将废泥浆加水稀释后才能进入设备,工作效率低。并且分离后的泥饼含水率大,呈粘稠状,仍然会污染环境,不能直接排放。结合我国西部某采油厂的废泥浆现状,尝试采用特种高压分离设备-模块化高压压干机,直接对废泥浆进行固液分离,分离后产生的滤液运至污水站处理后可回用,分离产生的泥饼达到 排放标准,实现了减量化、无害化,可直接填埋处理。
1 模块化废泥浆压干机较传统分离设备的优势
目前,国内用作废泥浆固液分离的设备主要是离心机、板框或隔膜厢式压滤机、带式机等。由于打井时产生的废泥浆不均匀,部分比较粘稠,以上设备的结构特点决定了粘稠废泥浆无法直接进入设备,必须对其进行加水稀释至流动态、均质处理,才能被输入设备进行固液分离处理。
模块化废泥浆压干机压滤核心模块独特的结构设计,可允许粘稠物料直接输入进行固液分离,省去了费时的稀释过程。模块化高压压干机采用高粘介质进料泵实现废泥浆直接进料,简化了设备,提高了工作效率。另外,离心机靠离心力进行固液分离,隔膜压滤机的压滤压力在0.7~1.2MPa,而模块化高压压干机的压滤压力高达3.00MPa,这使得分离出的固相物的含水率大大降低。
2 废泥浆现状及其固液分离工艺流程
此次高压固液分离尝试选在我国西部某采油厂的钻井现场进行。现场产生的大量废泥浆储存在经过防渗处理的泥浆池中,其状态为粘稠状、含固率高,并有分层现象。上层松软、钻井液添加剂占比量大、泥沙占比量小;下层与上层相反。泥浆池中包括多种作业的废弃物(液),现场实测其平均密度约为1.2t/m³,平均含水率约为40%。主要有:
(1)钻井液
含有重金属、油类、膨润土、碱和化合物等对人、畜和环境有害的物质,约占总废弃物的70%左右。根据当地地质构造废泥浆中的钻井液,钻井-开、二开时选用无固相、低固相聚合物水基钻井液体系。为了防止油井坍塌转用聚磺防塌钻井液。主要成分有:土粉、NaOH、NaCO3、KPAM、HV-CMC、堵漏剂(SDL、HD-Ⅱ、高效堵漏剂)等。此外,在射孔、压裂时还会用到粘土稳定剂(KC1)、羟丙基瓜尔胶、杀菌剂(OFB-1)等。
(2)废液
由各作业设备的清洗液、井液、污水等组成,有害物质主要是油类物质,也有少量的有机处理剂、重金属及碱类物质。
(3)钻屑
约占总废弃物的20%,污染物主要是钻井液。
本次作业场地的废泥浆,分层明显。为了提高处理效率,将上层液体直接抽至滤液罐,运至污水站另行处理。仅通过设备压滤下面的稠泥浆。
针对采油厂油井的分布情况,当区域内油井分布比较集中时,采取在区域内建设集中处理站,把区域内油井在钻井时产生的废泥浆运至集中处理站处理;当油井分散分布、距离较远时,每口油井产生的废泥浆单独进行处理,采用撬装式结构设计的分离设备,可方便转移至下一口油井。根据本设备应用地点现场的实际情况,采用1台撬装式高压分离设备对一口油井产生的废泥浆进行处理。
现场泥浆池中的废泥浆输送至搅拌装置中与絮凝剂混合、搅拌调理后,再输送至高压压干机压滤,产生的干泥饼外运填埋,产生的滤液运至污水站处理。废泥浆经本工艺进行固液分离处理后,其中的部分有害物质转移至滤液中,滤液运至污水站进行无害化处理,部分有害物质被固化在固相物(泥饼)中。通过本工艺处理后,固相物中各污染物指标应低于《危险废物填埋污染控制标准》(GB 18598-2001)的控制限值,以便对其进行填埋处理。
3 高压压干机设备介绍及实施过程
高压压干机的基本工作原理是:采用高压机械压榨的方法对废泥浆进行固液分离,其系统主要设备包括:主机、液压系统、气控系统、输送系统、药剂系统、动力系统、控制系统、调理系统。为了便于在采油区运输,设备采用撬装式结构,分为主机工作站、动力站、辅助站三大单元。其中主机工作站的压滤单元采用模块化设计,本机采用10个压滤单元。根据设备的设计产量要求,单元数量可相应增减。
3.1 废泥浆的输送方案
如前所述,废泥浆含固率高、粘度大且没有流动性,将其直接从泥浆池中可靠又经济的输送到设备中,有很大难度。考虑如下三种方案:
(1)采用长臂挖掘机
现场泥浆池一般长20~60m,深3m,对于分散布置的多个泥浆池,经现场应用,此种方案是可行的。但对于因场地限制、多个集中布置的泥浆池,由于泥浆池间没有通道,挖掘机无法通过而挖不到内侧泥浆池。同时,此方案需要专人操作1台挖掘机,其成本过高,大大超过了运营成本的承受能力。
(2)采用大吸力软管泵
现场试用了1台11kW的大吸力软管泵。试用时发现,软管吸口相对稀的泥浆及流态粘稠泥浆能够被吸上,但稀泥被吸走后,吸口很快被更粘稠的泥浆堵住而无法吸上,需要移动吸口或者向吸口喷水稀释才能吸上,同时需要不断移动软管泵及其吸管,操作极为不便,并且效率很低。
(3)采用大流量搅拌式砂浆泵及高压水泵
现场尝试采用1台7.5kW的大流量搅拌式砂浆泵,将其固定在浮筒上,泵体置于泥浆池中。工作时,采用高压水泵将砂浆泵吸口的泥浆冲散。搅拌式砂浆泵的搅拌叶片将冲下的泥块搅散。搅匀后直接输送至设备的储罐中,泥浆在储罐中沉淀后,上层液体可供高压水泵使用。下层的粘稠泥浆直接输送至主机中进行固液分离。砂浆泵固定在浮筒上,可在泥浆池内方便移动。此种方法相对经济、方便。但因为需要加水冲散泥浆,效率较差。目前还没有找到能够直接输送如此高含固率泥浆的设备。
经比较,本次尝试采用第三种方案。
3.2 废泥浆的调理及压滤过程
经过实验测试,废泥浆的脱水需要加入1%~2%的铁盐类絮凝剂絮凝,以提高脱水效果。
本设备的调理过程如下:
进入泥浆储罐中的废泥浆,通过泥浆罐下部的高粘介质螺杆泵,定量输送到搅拌输送机中,同时絮凝剂由计量泵定量输送到搅拌输送机,与废泥浆一起混合搅拌,直接输送至主机料仓。物料在搅拌输送机的一端进料混合,另一端连续出料。搅拌输送机的长度、物料的输送速度、输送量及调理效果等各参赛,通过实验已经提前确定较佳值。
主机料仓容积1.2m³,当设备检查到料仓满后,前端调理系统自动停止向料仓加料,同时主机料仓下的高粘介质螺杆泵按照程序向主机供料,供料结束后,主机自动进入压滤程序。
主机进料时,当设备检查到主机料仓料位低于设定值时,调理系统自动开启,向主机料仓供料直到料仓料满停止。
经过5次现场压滤测试,确定各工艺参数设定,根据得出的工艺参数,设备的处理能力计算如下:
(1)设备压滤周期约为30min。
(2)设备单次进料约0.8m³,则设备每小时处理废泥浆量约为1.6m³(约1.92t),按20h/d工作制计。则每天设备产量为:20×1.92=38.4t/d。现场动力站采用柴油发电机,根据现行实测,单个压滤周期(30min)整个设备消耗0号柴油约4L,则0号柴油消耗量为8L/h。
在主机压滤过程中,滤液经排水管道不断大量排出。现场滤液清澈、透明。压滤至20min时,泥饼压滤压力达到2.5MPa,此时滤液量很小,可排出泥饼。
经压滤后,废泥浆状态从粘流态变为块状,实测泥饼含水率约11.6%,远低于传统隔膜压滤机处理后的含水率。设备无故障连续稳定运行30天,本次尝试效果得到用户的肯定。
4 高压压干机实施效果分析
4.1 废泥浆处理产物-泥饼:重金属含量分析
废泥浆经高压压干机压滤后,大部分有害物质进入滤液,小部分有害物质被固化在泥饼中。对泥饼中的重金属按照GB 5086.2的方法进行检测,具体如下:
泥饼含水率11.6%,取一定量泥饼在105℃条件下烘至恒重。取100g烘干泥饼,加入1L浸取剂,在室温震荡8h、静置16h后,用0.45μm的滤膜过滤上清液,用ICP仪器分析溶液中的重金属溶出,浸取剂分别用pH=5、pH=7的去离子水(用盐水调节pH值)。泥饼中的重金属检测结果显示:浸出液中重金属含量均低于 标准GB 5085.3-2007、GB 18918-2001的限值,符合填埋要求。
4.2 设备运营成本分析
以下根据当前市场价格核算,具体实施时按照实际价格为准。
(1)能源消耗成本
根据标题3.2中测得的数据:设备产量为1.92t/h,设备消耗0号柴油约8L/h,则处理每吨废泥浆柴油消耗量为4.2L。柴油按市场价5.43元/L,则每吨废泥浆能耗成本为22.8元/t。
(2)药剂消耗成本
加药量为9.6kg,单次进料约0.8m³,泥浆浓度1.2kg/m³,则每吨废泥浆加药量为9.6/(0.8×1.2)=10kg。按药剂市场价900元/t计算,则废泥浆处理的药剂成本为9元/t。
(3)设备维护成本
根据设备结构及其维护情况,按3元/t折算。
根据以上分析,则处理每吨废泥浆成本为22.8+9+3=34.8元。
以上核算是设备的消耗成本,不含滤液的无害化处理成本及人工成本。此部分的成本与采用隔膜压滤机的成本相当。
4.3 废泥浆的减量化分析
本设备工作时,因废泥浆不需要加水稀释,可直接输入到设备中进行固液分离处理,因此其工作效率较高;所添加药剂为液体药剂,废泥浆处理后只减量不增量。本次处理的废泥浆平均含水率约40%,处理后泥饼含水率11.6%,则废泥浆减量:(100-60)/(1-0.116)/100=32.2%。即减量约1/3,这与传统添加固化剂固化工艺会导致很大增量相比有明显优势。
4.4 设备占地面积及处理量分析
设备主机采用立式结构设计,同样过滤面积情况下较传统卧式隔膜压滤机占地面积小,本机主机占地面积仅为2m×3m;辅助设备中除不需要加水稀释装置外,其它与传统隔膜压滤系统的辅机相同,因此较传统压滤设备占地面积小。
本设备的优势在于,特别适合对粘稠态的物料进行固液分离。现场循环钻井液经现场固控系统处理后产生的废泥浆,再经本设备初步筛分、沉淀分离后,大部分液相现场回用。本设备仅处理剩余高含固量的粘稠废泥浆,与传统隔膜压滤机相比,简化了工艺,提高了处理效率。
现场每口井废泥浆总产量约80~150m³,经初步筛分、沉淀分离后,剩余平均含水率40%左右的废泥浆约50~80m³。按本设备38t/d的处理量,仅需2~3天即可处理完毕。
5 结论
(1)通过本设备在现场30天的连续无故障运行测试,设备运行稳定,可以确定经特别设计的压滤主机直接处理高含固率的废泥浆是可行的。废泥浆不加水稀释,与传统隔膜压滤机相比,提高了处理效率。
(2)废泥浆经本设备分离后,大部分的有害物质转移到液相中,其固相(泥饼)中的重金属含量很小。对泥饼中的重金属按照GB 5086.2的方法进行检测,浸出液中重金属含量均低于 标准GB 5085.3-2007、GB 18918-2001的限值,符合填埋要求。
(3)本设备进行废泥浆固液分离时,仅加入液相的絮凝药剂,处理后有较大减量,减量约1/3。
(4)本压滤主机原理为机械压榨,泥饼压力可达30kg/cm2,远高于传统隔膜压滤机16kg/cm2的压力,处理后的泥饼含水率仅为11.6%。
(5)在同样过滤面积的情况下,本压滤主机因采用立式结构,较传统卧式隔膜压滤机占地面积小。
(6)处理废泥浆时,本设备的运转消耗成本与隔膜压滤机相当。
综上所述,本模块化高压压干机处理高含固率的废泥浆比隔膜压滤机等传统设备有较大优势。