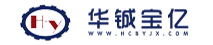
目前,我国大部分油田已进入高含水阶段。此前,油田采出液一般采用电脱水法处理,而电脱水器容易穿越电场,处理后的油水含量超标,不能满足逾期的处理要求。卧螺离心机更适合油泥资源化处理的工业化应用。但它的局限性是在三相分离中分离出的固相不够纯净,会混入较多的油相,分离效率也需要进一步提升。
朱桂华等对离心机内部物料进行三维模型的建立,结合Fluent软件选用RNG k-ε湍流模型与多重参考系模型,对流场内固、液两相进行模拟仿真,得到不同转速差下三相卧螺离心机流道的速度和压力云图,以及出砂口固相的干燥程度与转速差的关系曲线。郑胜飞等采用Fluent软件中的雷诺应力模型和离散相模型模拟离心机三维流场,得到流场内的压力和速度分布,颗粒沉降时间与理论计算结果相符合。
含油污泥是石油开采、提炼、加工、储存、运输等过程中产生的主要废物。它通常是一种由水、油、砂三相组成的高度稳定的乳状液,其中含有大量的碳氢化合物(PHCs)。如果不能将其回收处理,大量的含油污泥会污染地表。而且从污泥中回收原油也将具有很大的经济和环境效益。三相机械离心分离技术具有能耗低、污染小、操作简单等优点,适用于污泥资源化处理的工业应用。本文将采用计算流体力学(CFD)数值模拟以及实验验证的方法,对三相卧螺离心机在不同结构参数下的分离性能进行研究。
1 多相流和湍流模型
在流体力学软件Fluent中有3种多相流模型:VOF、Mixture及Euler模型。本文将采用Mixture模型。该模型适合离心机旋转系统中分散相不均匀分布的特点。
湍流模型选用RNG k-ε双方程湍流模型,其具有可解决高应变率和高流线弯曲率的优点,适合进行三维非定常不可压缩流场计算。
2 结果和数值模型
2.1 结构模型设计
根据三相分离的特点,建立了三相卧螺离心机的三维模型。
该模型有3个主要特点:
(1)挡油板在圆柱段靠近与锥段连接处,防止油相在螺旋输送器的推动下从出砂口流出。
(2)在圆柱段出口处设置一个类似连通器的结构,这使得油和水沿着它们各自的路径移动到单独的出口,并且控制出水口和出油口的径向高度,使得出水口与出油口的压力近似相等。
(3)在螺旋输送器圆柱段叶片上开孔,使挡油板挡住的油相可以通过开孔流回出油口,防止油相在挡油板处堆积,溢过挡油板,从出砂口流出。
这种三相卧螺离心机的新颖性和优点主要有:挡油板可以防止油滴继续向出砂口移动;螺旋输送器叶片上开孔的设计可以使油相尽可能地从出油口流出,提高分离效率。
2.2 数值模型构建
根据三相卧螺离心机的结构模型建立数值模型。
在对结果影响不大的前提下,移除了管道、法兰、肋板等结构,简化出油、出水、进料口结构,更多关注转鼓内部流场。
2.3 网格划分
使用ANSYS自带的meshing进行网格划分。螺旋输送器叶片外沿到内壁2mm的筒状部分,由六面体结构网格sweep划分,其余部分由四面体非结构网格划分。整个网格形式采用六面体结构网格和四面体非结构网格的混合网格形式。离心机模型单元数为1050474。网格质量检查显示平均网格质量为0.83,网格划分质量良好,满足计算要求。
2.4 计算条件
2.4.1 边界条件使用
使用Fluent2019 R3计算其内部流场。在转鼓和螺旋之间设置interface面,转鼓和螺旋轴壁面剪切条件为无滑移条件,壁面为滑动壁面。
入口定义为速度入口,3个出口定义为压力出口(表压为零)。
2.4.2 数值设定
油、水、砂三相都视为不可压缩流体,采用多重参考系模型计算流体区域的运动。由于流体处于湍流状态,将RNG k-ε方程作为湍流模型,采用标准壁面函数法进行近壁处理,计算使用分离的隐式和SIMPLE方法,采用瞬态法计算,时间步长设置为0.03s,直到结果稳定。
2.5 出水口和出油口位置的确定
在离心机的设计中,存在一个关键的问题,即出油口和出水口位置的确定。在排液过程中,如果油、水两相压力差较大,排液会出现明显的先后顺序,这样会使油、水两相从同一出口排出,严重影响分离效率。因此需要对出油口和出水口的压力进行计算,从而确定两者位置关系。
通过螺旋输送器叶片开孔位置、出油口距中心轴半径以及大量模拟,可知油相的稳定厚度约为15mm,平衡线保持在145mm处。出油口距中心轴半径为134mm,出油口半径为4mm。为了出油口能稳定出油并保证其回收效率,需要利用这些已知条件,通过排液压力来确定出水口的位置。
在运行过程中,如果出水口压力大于出油口压力,则会导致排水速度大于排油速度,使油相厚度增加,使出水口压力下降;反之,如果出水口压力小于出油口压力,则会导致排水速度小于排油速度,使油相厚度减小,出水口压力上升。在一定范围内,可以实现排液压力平衡的负反馈调节,保证排液稳定。
3 模拟结果和讨论
3.1 离心机改进前油相体积分数分布分析
离心机改进前未设导油孔,油相回收率十分有限,而且在连续工作时,会出现油相在挡油板处过度堆积的问题。
随着设备的运行,油相在螺旋输送器的推动下于挡油板处堆积,然后溢出,使油相从出砂口推出,导致油相回收率下降,固相含油率上升,影响分离效率。
3.2 离心机改进后油相体积分数分布分析
模拟结果表明,在螺旋输送器的推动下,油相很难从离心机内壁面与螺旋输送器叶片外端的缝隙中流向出油口。因此,通过在螺旋输送器叶片上开设导油孔,使油能够顺畅地从出油口流出,避免油相在挡油板处堆积,影响分离效率。
同时,通过分析发现,物料在进入转鼓时,会带有径向的速度。当进料位置距离挡油板过近时,会在螺旋输送器的推动下,直接越过挡油板,导致油相回收率下降以及出砂口含油率增加,影响分离效率。
因此,通过大量的计算机模拟,不断优化,做出以下改进:螺旋输送器上增加了周向24个导油孔,并且将进料位置向大端法兰移700mm。
改进后变化明显,在长时间运行稳定后,油相依然没有溢出挡油板,油相堆积得到了很好的解决,这种改进方法能够提高油相回收率。
模拟结果表明,运行稳定时油、水、砂三相分层明显,出油口处几乎没有其他相,油相回收率得到很大的提高。
3.3 结构改进前后数据对比
分离效率主要由各个出口处油和砂的体积分数来反映。为了便于计算,用油相回收率和固相回收率来分别评价油和砂的分离效率。
油相回收率为出油口出油量占入口进油量的百分比。固相回收率为出砂口出砂量占入口进砂量的百分比。
在模拟过程中,监测各个出口的流量以及各组分体积分数,根据监测结果计算分离效率。
计算结果表明,增加导油孔,出水口含油率从10.2%下降到5.3%,出油口含油率也大幅度提升,油相回收率从59.4%提高到83.0%,固相回收率基本没有变化。结构改进后极大地提高了油相回收率,改进效果显著。
4 实验验证
根据三相卧螺离心机结构及特点,画出整套零件图和装配图,然后依据图纸到加工厂生产制造设备,搭建实验平台。
实验步骤如下:
(1)准备工作。实验用的原料为自来水、原油和石英砂,按照体积比7:2:1的比例进行配制,对物料边加热边搅拌,确保物料进入三相卧螺离心机前充分混合。
(2)空载运行以及热水预热。关闭进料阀和螺杆泵,开启离心机主副变频器,逐渐加速使离心机转鼓和螺旋达到较高转速。然后将螺杆泵通入热水罐,启动螺杆泵,再逐渐调节转鼓转速,观察各个进出口的流量变化。
(3)测试离心机的分离效率。关闭螺杆泵,让转鼓内的水自然排尽,然后将进料搅拌桶、螺杆泵、卧螺离心机三者相连,开启螺杆泵,开始进料。调节主副变频器逐渐使转鼓加速,使其处于恒定转速,保持进料物料特性和其他操作参数不变,对离心机进料、出油、出水及出砂进行采样并测量。
(4)测试改进的离心机的分离效率并记录数据。更换螺旋输送器,重复上述操作。
对实验分离出来的样品进行采样编号,之后采取焚烧法确定各组分含量。测量方法如下:首先,取一个清洁干燥恒重后的坩埚,称重,加入待测样品约10g,再次称重,然后将坩埚和样品以期放入电热恒温鼓风干燥箱烘干至恒重,称重;将干燥后的样品进行充分焚烧,称重。根据以上操作记录下的数据,可以计算出各个组分的含量。
实验结果表明,改进后的离心机确实能够显著提升出油口含油率以及油相回收率,与模拟结果相符。但实验中发现出油口含砂率与模拟相比差别较大,且含量很高,导致固相回收率不高。
通过观察样品发现,出油口的固相颗粒相比于出砂口的固相颗粒普遍偏小,且密度较小。总结原因,实验使用的石英砂粒径和球形度不够均匀,且存放时间过长混入了大量灰尘,这些固相形成浮渣从出油口排出。
5 结论
(1)通过水力平衡计算,控制油、水两相在出口位置的压力相等,从而确定出水口的位置。在一定范围内,可以实现排液压力平衡的负反馈调节,保证排液稳定。
(2)数值模拟中发现,传统的三相卧螺离心机在螺旋输送器的作用下,会将部分油相推向出砂口,影响分离效率。增加导油孔的设计可以使油相轴向流动,大大地减少了油相在挡油板处的堆积,对提升分离效率有积极作用。
(3)实验中油相回收率大幅度提升,能够证明导油孔在提升分离效率的实际作用。但在实验中也发现,浮渣对分离效率影响极大,在以后的实验中要选择更加纯净、大小均匀的固相颗粒,而且要避免露天堆放混入灰尘。