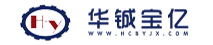
1 设备概况
呼伦贝尔金新化工有限公司浓盐水装置卧式螺旋卸料离心机(简称离心机)由意大利贝亚雷斯集团设计和生产,型号FP600 2RS/M,为环保装置重要的固液分离设备,其主要作用是将机械搅拌澄清池底沉淀的污泥进行固液分离(污泥主要成分是石灰乳等)。基本流程为:螺杆泵吸入机械搅拌澄清池底部的污泥,并加压至0.3MPa,输送至离心机,经离心机高速离心、卸料,实现固液相分离。离心机出泥口设计专用的刮泥装置,及时将固相物料清理,设备设计参数见下表:
项目 | 参数 |
运行容量/(m³/h) | 14 |
工作温度/℃ | 25 |
进口固体浓度/% | 4 |
离心机出口固体浓度/% | 25 |
聚合物(助凝剂)加药浓度/(μg/mL) | 76 |
固体回收率/% | 95 |
离心机设计容量/(m³/h) | 14 |
离心力/N | 32340 |
转鼓电机功率/kW | 15 |
螺旋电机功率/kW | 4.4 |
转鼓额定转速/(r/min) | 4000 |
出渣口固相含水率/% | 70~80 |
齿轮比 | 1:160 |
外形尺寸/mm | 3000×1050×1400 |
设备在启动前开启转鼓冲洗水,运行至额定转速后切换物料投入运行,轴承无冷却方案,轴承运行时正常温度在60~70℃,工况运行转速4000r/min。
2 存在的问题
2015年2月-2018年5月,随着工艺系统需要处理的泥量增多,设备运行周期变长,启停次数频繁,设备故障率逐渐增加,设备连续运行不到1个月就要被迫停机进行检修,主要问题表现为:
(1)离心机整体振动值偏高(22~32mm/s)。
(2)主轴承温度较高(85~95℃),润滑脂变质。
(3)物料堵塞在转鼓与螺旋之间,盘车卡涩,设备运行跳车。
(4)差速器故障。
(5)电机故障频繁。
2015年至2018年5月(共计41个月)停车检修52余次。设备代表性损坏情况:由于设备振动值较大,故障停车,解体大修,检查各轴承,并更换转鼓及螺旋液相端轴承和固相端轴承。
离心机本体轴承共计4个,分别为转鼓液相端轴承、螺旋液相端轴承、转鼓固相端轴承、螺旋固相端轴承,多次解体后发现除螺旋液相端轴承外,其他3个轴承及轴承轴径处损坏严重。
行星齿轮减速器故障导致停车5次,主要原因为:
(1)差转速低故障跳车。
(2)螺旋扭矩高故障跳车。
解体检查发现差速器损坏。液力耦合器故障1次,故障原因为转鼓转速低。
综上所述,离心机故障率较高,已经严重影响浓盐水脱泥系统长周期稳定运行,加重了浓盐水脱泥前、后系统的负荷,给整个浓盐水系统带来了极大的隐患。
3 原因分析及处理
离心机故障停车问题主要表现在:
(1)堵机导致转鼓轴承与螺旋轴承的转速差为零,设备不能正常使用。
(2)离心机轴承使用不当,引起轴承温度偏高(85~95℃),导致轴承损坏及振动。
以下从这2方面出发,分析导致故障频发的原因及处理措施。
3.1 堵机问题的原因及处理措施
导致卧式沉降离心机堵机常见的原因有:
(1)离心机本体设计缺陷,主要参考值为分离因数。
(2)离心机进料量不稳定,离心机处理不及时,物料堆积。
(3)转鼓轴承与螺旋轴承之间磨损严重,间隙过大导致物料积在转鼓壁上不能排出。
(4)差转速设定数值不正确等。
3.1.1 校核分离因数Fr
分离因数是离心机分离能力的主要指标,分离因数越大,物料所受的离心力越大,分离效果越好。分离因数与离心机的转鼓半径成正比,与转鼓速度的平方也成正比,因高转鼓转速比大半径对分离因数的影响要大得多。因此首先要对分离因数进行计算校核。
分离因数计算公式:Fr=rw²/g,w=2πn/60
式中:
Fr:分离因数,N;
r:离心机转鼓半径,m;
w:转鼓的角速度,r/s;
g:重力加速度,取9.8m/s²;
n:转鼓的转速,取4000r/min。
将参数带入计算公式,通过核算得出Fr=3200N。
常速离心机分离因数Fr小于3500N,适用于含较大颗粒或颗粒中等或纤维状固体悬液分离,常速离心机转速较低,转载容量较大,转鼓直径较大。根据计算,浓盐水离心机分离因数为3200N,属于常速离心机,根据分离因数校核,该离心机本体符合设计要求。
3.1.2 物料
物料主要成分为石灰乳,由螺杆泵(流量14m³/h、压力0.3MPa)直接进入离心机,从现场螺旋、转鼓扭矩波动上可以直接判断为物料不均匀导致,是导致离心机跳车的主要因素之一。
3.1.3 转鼓与螺旋间隙
根据现场实测,螺旋与转鼓间隙小于1mm,符合设计要求,这里排除螺旋与转鼓之间间隙问题。
3.1.4 差转速调节
由于现场机械搅拌澄清池出泥含固量不稳定,供泥泵出泥直接进入离心机,瞬间造成离心机转鼓与螺旋扭矩值波动,并且频繁波动,不能根据差转速调节曲线进行及时调节,因此会造成超扭矩跳车。
处理措施是在进入离心机前增加调理槽,将供泥泵出泥预 行搅拌后溢流进入离心机,解决物料堆积造成超扭矩跳车问题。
3.2 轴承频繁损坏原因分析及处理措施
轴承损坏是导致设备振动高跳车的主要原因。因此分析轴承损坏原因,并提出解决对策,进而降低设备检修频次。
检修中分析已经损坏的轴承发现:
(1)轴承缺润滑脂。
(2)轴承保支架损坏。
(3)轴承滚珠磨损。
(4)轴承内圈磨损。
(5)轴承轴径处磨损。
(6)轴承内进入介质。
3.2.1 轴承润滑脂分析
离心机随机润滑脂使用情况:
项目 | 转鼓轴承 | 螺旋轴承 |
油号 | 克鲁博UH1 14-31 | 克鲁博UH1 64-1302 |
频次/数量 | 200h/30g | 200h/30g |
由于损坏轴承只有转鼓轴承和螺旋轴承,因此只考虑转鼓轴承与螺旋轴承使用条件,而实际转鼓轴承及螺旋轴承添加润滑脂均为克鲁博UH1 64-1302,并且每运转200h补一次脂,根据贝亚雷斯厂家提供油脂使用说明,克鲁博UH1 64-1302为防水低温润滑脂,克鲁博UH1 14-31为高温润滑脂,克鲁博UH1 64-1302不能代替克鲁博UH1 14-31油脂加注至转鼓轴承内,因此转鼓轴承的油脂使用错误是导致轴承损坏的原因之一。
处理措施:正确使用润滑油脂,并严格控制加注油脂频次和数量。
3.2.2 螺旋固相端轴承损坏原因分析及排查
根据螺旋固相端轴承损坏情况判断为介质进入轴承内部导致轴承损坏,螺旋固相端轴承型号NKI85/26,实际运行相对转速5~35r/min,主要密封形式为双骨架油封密封。根据现场每次的堵机情况看,介质会进入螺旋固相端轴承内部,造成此处轴承损坏,因此必须杜绝堵机情况发生。
3.2.3 转鼓液相端轴承损坏原因分析及排查
转鼓液相端轴承深沟球轴承主要承受径向载荷,同时也承受轴向载荷。当其仅承受径向载荷时,接触角为零。当深沟球轴承具有较大径向游隙时,具有角接触轴承的性能,可承受较大轴向载荷,深沟球轴承摩擦系数很小,极限转速也很高。现场排除轴承质量问题、油脂问题、冷却系统问题的前提下,分析轴承损坏主要有以下原因。
3.2.3.1 检修安装不当导致
在确保正确操作和规范检修前提下,对轴承的安装游隙、预留热膨胀余量、内外圈的配合性质等进行检查。
3.2.3.2 轴承安装数据检查
大修时对检修数据进行分析,测量数据见下表:
测量点 | 定位端 | 自由端 |
轴颈直径 | 75.01 | 75.01 |
轴承内孔 | 75.00 | 75.00 |
轴承座内孔 | 160.01 | 159.97 |
轴承外径 | 160.00 | 160.00 |
检修过程中定位端轴承各装配数据符合装配要求,自由端根据现场实测轴承座内孔直径偏小,轴承外圈与轴承座内孔装配为过盈配合。
3.2.3.3 自由端膨胀间隙检查
滚动轴承周向固定和径向游隙大小是通过轴承与轴承座配合达到的。径向游隙不仅仅关系到轴承的运转精度,同时影响其寿命。轴承游隙直接影响到轴承载荷分布、振动、噪声、磨损、温度和机械运转精度等技术性能。轴承的额定载荷是随着游隙的大小而变化,轴承样本中的额定负荷就是轴承在工作游隙为零时的推荐值。过盈配合的轴承应该通过计算选择合理的径向游隙。
在呼伦贝尔地区的环境条件下,由于冬季温差较大,轴膨胀量约0.5mm,此伸缩量足以使支持轴承损坏。在设计中自由端轴承外圈选择过渡配合,以便使转鼓轴承在热胀冷缩时可以相对于轴承座外圈进行有限滑动,避免轴承受到因热胀冷缩产生的轴向力作用。
基于以上计算及实际检修测量数据,两端轴承内圈在过盈量不足的情况下,热态下失去过盈量,造成轴承失稳并且离心机自由端为过盈配合,且盈量(0.03mm)较大,不能满足轴向膨胀窜动,造成定位端轴承轴向力过大,长时间运转促使轴承振动、温度升高、保持架损坏等情况的发生。因此,造成轴承内径与轴过盈量不足的主要原因是离心机经常更换轴承,在检修时使用砂纸抛光轴径处导致轴径过盈量不足。由于缺少0.005轴径,不便于修复,故采取降低转速,降低轴温等措施解决目前设备出现的故障问题。
处理措施:原设计转鼓电机为工频电机,转鼓电机通过液力耦合器输出,通过三角带传动至转鼓,实现转鼓的高速离心。原设计螺旋电机为变频滑环电机,螺旋电机通过同步齿带传动至差速器(二级行星齿减速机),差速器通过花键轴将转速传动至螺旋,实现螺旋的卸料。
保留原转鼓电机和螺旋电机,原转鼓电机由工频改为变频控制,转鼓转速根据工况要求来调整电机转速,控制系统采用双电机双变频全自动控制,转鼓电机根据物料特性调节不同离心机工作转速(降低离心机转速控制轴承温度,保障轴承过盈量以及自由端轴承膨胀量)。
转鼓转速及差转速均可无级调节,差转速根据输渣负载变化,差转速根据输渣负载变化,差转速自动反馈调节,推料功率自动补偿,使固渣在离心机内不仅受离心压力,而且在前端螺旋叶片间作双向挤压以保证固渣的恒定干度,使离心机不易发生堵料,保证在任意工况下均能安全可靠连续稳定运行,同时全自动控制,保证了额定工况下使其效率处于高点。整个机组的开、停设有手动和自动控制,PLC程序自动控制,下位与上位机进行通讯连接,通过通讯总线与DCS(远程I/O柜)实现双向通讯,实现远程操作与控制。
4 结束语
综上所述,可以得出以下结论:
(1)进料不均匀。引起离心机频繁跳车主要的原因是物料进料不均匀,离心机不能对突然变化的物料浓度进行及时调整,操作人员不能远程监控及操作离心机的运行,只能由现场巡检人员通过手动控制阀门控制进料量,并通过现场操作面板调节差转速。
(2)润滑脂使用不当。轴承温度高,油脂缺乏频繁,轴承油脂变色且频繁损坏,造成以上原因为误将螺旋润滑脂注入支撑轴承处,将低温耐水润滑脂使用至高温场合,导致润滑脂因高温流出轴承,满足不了两端支持轴承使用条件。
(3)轴承装配问题。高速旋转的轴承温升较高,面对突发的各种工况其受力变化较大,在受力多变的情况下,如果轴承装配间隙轻微的发生了变化,就会严重影响其使用寿命。虽然可以解决轴承装配问题,但解决不了多变的工况。因此,从工艺流程、操作流程入手,应对多变的工况,改善轴承的运行环境,才能降低轴承的损坏频率,保障设备长周期运行。
通过对故障原因进行全方位分析,以控制工艺流程,增加调理槽、改进操作流程,增加双变频并引入DCS等措施应对多变的工况。技术改进后离心机转鼓轴承温度从85~95℃降到50℃,振值从20mm/s降至7mm/s,保障了设备稳定长周期的运行。